喷塑工艺流程及其特点
发布时间:2025-03-10 分类:新闻 浏览量:132
喷塑的工艺原理
静电粉末喷涂技术通过高压静电吸附实现高效涂装。其核心流程为:压缩空气将粉末涂料输送至静电喷枪,枪口高压发生器产生80-100kV静电场引发电晕放电,使雾化粉末带电;带电粒子在电场力作用下定向吸附于接地工件表面,随涂层增厚形成电荷堆积,通过同性静电斥力自主调控膜厚均匀性;最终经高温固化形成致密涂膜,完成从粉末吸附到涂层成型的全流程工业化应用。
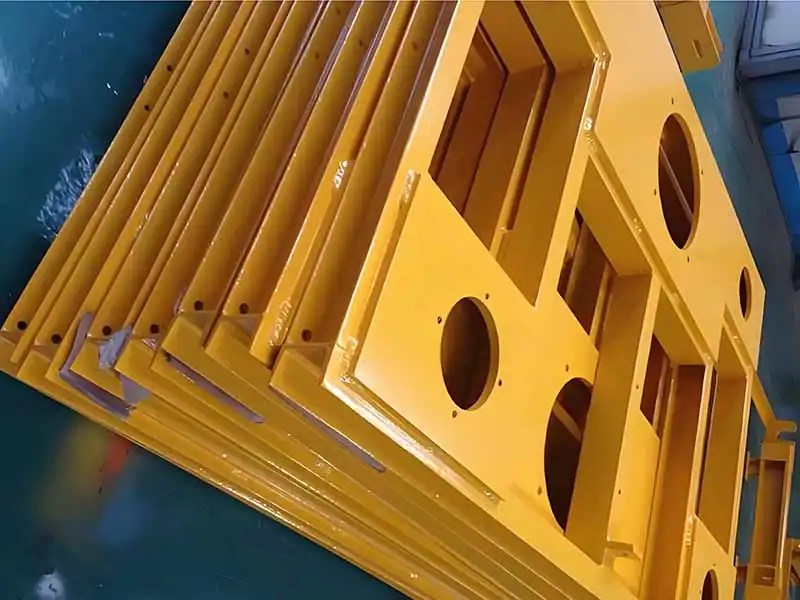
工作流程
工艺名称 | 工艺流程目的任务及详细步骤 | 相关设备 | 相关材料 |
---|---|---|---|
1. 预处理 | 目的: 清除工件表面污染物,形成防锈且增强附着力的磷化层 详细步骤: ① 除油:酸性除油剂(硫酸/盐酸)去除油脂 ② 除锈:酸洗或机械打磨消除氧化层 ③ 磷化:生成灰色磷酸盐结晶膜(2-4g/m²) ④ 钝化:封闭磷化膜孔隙提升耐蚀性 | 四联体混凝土处理槽(除油槽/酸洗槽/磷化槽/钝化槽) | 硫酸、盐酸、纯碱(Na₂CO₃) 酸性除油剂、磷化液(锌系)、钝化液(铬酸盐) |
2. 静电喷涂 | 目的: 实现粉末涂料均匀吸附与高效回收 详细步骤: ① 静电发生:喷枪加载60-100kV负高压 ② 粉末雾化:压缩空气(0.4-0.6MPa)分散粉末 ③ 电场吸附:带电粉末定向沉积工件表面 ④ 回收处理:旋风+滤芯二级回收(95%利用率) | 多工位静电喷塑机 粉末回收喷房 空气压缩机+三级油水过滤器 | 环氧聚酯粉末(粒径15-45μm) 高光/哑光/纹理等专用塑粉 |
3. 高温固化 | 目的: 完成粉末熔融流平与交联固化反应 详细步骤: ① 升温阶段:10℃/min升至185℃ ② 恒温固化:185±5℃保持15分钟 ③ 冷却阶段:自然降温至50℃以下 ④ 质量检测:硬度/附着力/外观检验 | 燃气辐射式固化炉(配智能温控系统) 热风循环装置 温度记录仪 | 天然气/电能(加热能源) (注:固化过程不消耗额外材料) |
4. 装饰处理 | 目的: 实现特殊外观效果(木纹/花纹/高光等) 详细步骤: ① 罩光处理:喷涂透明粉末/UV涂料增强光泽 ② 热转印:通过转印膜(150-200℃)复制纹理 ③ 水转印:浸渍活化膜形成3D图案 ④ 局部精修:手工补喷特殊效果涂料 |
工作原理
- 工作时静电喷涂的喷枪或喷、喷杯部分接负极,工件接正极并接地, 在高压静电发生器的高电压作用下,喷枪(或喷盘、喷杯)的端部与工件之间就形成一个静电常涂料微粒所受到的电场力与静电场的电压主和涂料微粒的带电量成正比,而与喷枪和工件间的距离成反比,当电压足够高时,喷枪端部附近区域形成空气电离区,空气激烈地离子化和发热,使喷枪端部锐边或极针周围形成一个暗红色的晕圈,在黑暗中能明显看见,这时空气产生强烈的电晕放电。
- 涂料中的成膜物即树脂和颜料等大多数是由高分子有机化合物组成,多成为导电的电介质,溶剂形涂料除成膜物外还有有机溶剂、助溶剂、固化剂、静电稀释剂、及其他各类添加剂等物质。这类溶剂性物质除了苯、二甲苯、溶剂汽油等,大多是极性物质,电阻率较低,有一定的导电能力,它们能提高涂料的带电性能。
- 电介质的分子结构可分为极性分子和非极性分子二种。极性分子组成的电介质在受外加电场作用时,显示出电性;非极性分子组成的电介质在外加电场作用下,显示电极性,从而对外来的导性电荷产生亲合力,使电介质在外加电场中其外表面能局部带电。
- 涂料经喷嘴雾化后喷出,被雾化的涂料微粒通过枪口的极针或喷盘、喷杯的边缘时因接触而带电,当经过电晕放电所产生的气体电离区时,将再一次增加其表面电荷密度。这些带负电荷的涂料微粒的静电场作用下,向导极性的工件表面运动,并被沉积在工件表面上形成均匀的涂膜。
喷塑优点
- 环保性优:无溶剂挥发,粉末回收利用率>95%,符合RoHS环保标准。
- 性能突出:涂层硬度达2H-3H,耐盐雾>500h,附着力达0级(百格法)。
- 效率显著:单次成膜60-120μm,固化仅15-20分钟,自动化喷涂效率提升40%。
- 装饰性强:可定制木纹/金属/3D纹理,光泽度覆盖哑光至镜面。
喷塑缺点
- 厚度受限:超薄(<40μm)或超厚(>200μm)涂层工艺稳定性差。
- 改色困难:换色需彻底清洁设备,小批量多色订单成本增加30%-50%。
- 基材限制:仅适用于耐温>180℃的金属件,塑料/木材需特殊处理。
- 能耗较高:固化炉能耗占工艺总耗电65%,燃气加热碳排放较传统喷漆高20%。