数控机床加工余量的确定
发布时间:2025-01-17 分类:新闻 浏览量:1429
CNC加工余量确认
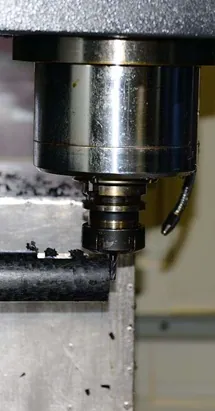
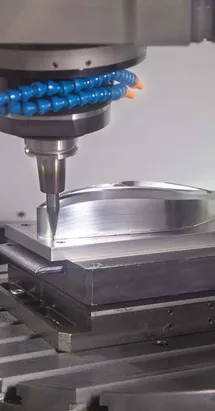
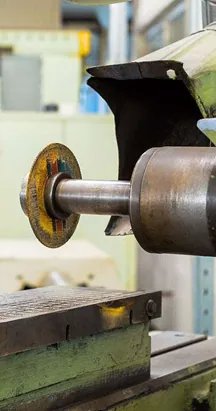
什么是CNC加工余量?
1.指加工所需要产品预留的加工厚度,去除预留厚度后能够得到符合要求的工件尺寸、形状和位置精度。
2.加工余量的大小直接影响到加工效率和加工质量,因此合理确定加工余量是数控机床加工中的重要环节。
CNC加工余量的影响因素:
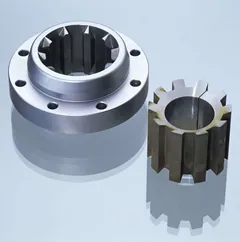
工件材料
工件材料的硬度、强度、韧性等物理性能对加工余量的大小有较大影响。
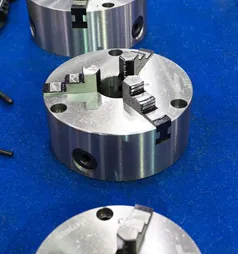
刀具性能
刀具的锋利程度、耐磨性、刚性等性能会影响加工余量的确定。
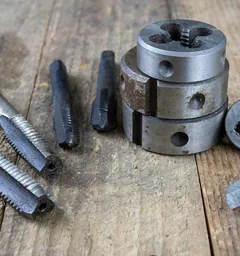
机床精度
机床的定位精度、重复定位精度、传动系统稳定性等都会影响加工余量的确定。
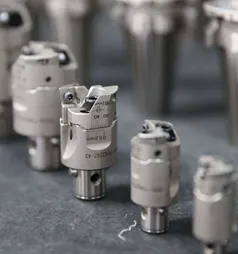
加工工艺
不同的加工工艺(如粗加工、半精加工、精加工)对加工余量的需求不同。
CNC加工余量的确定方法:
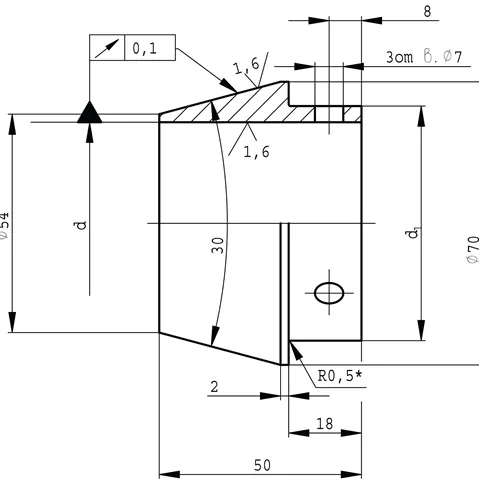
根据经验确定
根据实际加工经验,结合相似案例,确定加工余量的大小。
试验法
通过试验切削的方式,观察切削力、切削温度等参数变化,确定合理的加工余量。
分析法
通过建立数学模型或仿真模型,分析工件材料、刀具、机床等因素对加工余量的影响,从而确定合理的加工余量。
数控机床加工余量的计算
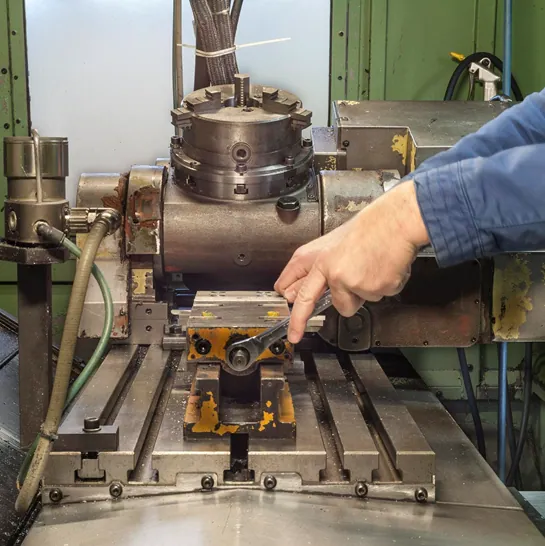
切削深度
根据工件材料和加工要求,确定切削深度,从而计算出加工余量。
切削速度
不同的切削速度会影响切削力的大小,进而影响加工余量的确定。
进给速度
进给速度的大小会影响切削面的粗糙度,从而影响加工余量的确定。
基于工件材料的加工余量计算
材料硬度
硬度较高的材料可能需要更大的加工余量。
材料韧性
韧性较大的材料在加工时容易产生热量和切削力,因此需要较大的加工余量。
材料热处理状态
热处理状态不同的材料,其硬度和韧性会有所不同,从而影响加工余量的确定。
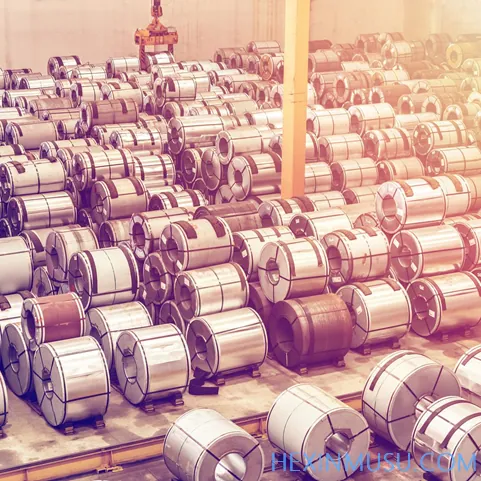
基于刀具磨损的加工余量计算
刀具磨损程度
磨损程度较大的刀具会影响切削面的粗糙度,从而影响加工余量的确定。
刀具寿命
刀具寿命较短时,需要较大的加工余量以避免刀具破损。
刀具类型
不同类型的刀具具有不同的切削性能,因此需要根据刀具类型确定合适的加工余量。
优化目标与约束条件
优化目标
在满足加工精度和表面质量的前提下,最小化加工余量,提高加工效率。
约束条件
加工过程中的切削力、切削热、刀具磨损等因素需在可承受范围内,同时确保加工过程的稳定性和可靠性。
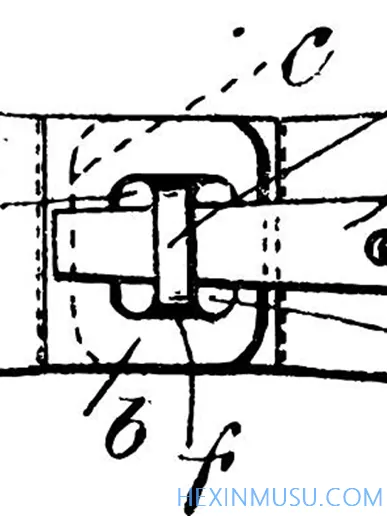
优化算法的选择与应用
遗传算法
通过模拟生物进化过程中的遗传机制,实现全局搜索最优解。适用于多变量、非线性、离散型优化问题。
粒子群算法
模拟鸟群、鱼群等生物群体的觅食行为,通过个体间的信息共享和协作,寻找全局最优解。适用于连续型优化问题。
模拟退火算法
借鉴固体退火原理,通过随机搜索和概率接受劣解,避免陷入局部最优解。适用于多约束、非线性优化问题。
加工余量优化实例分析
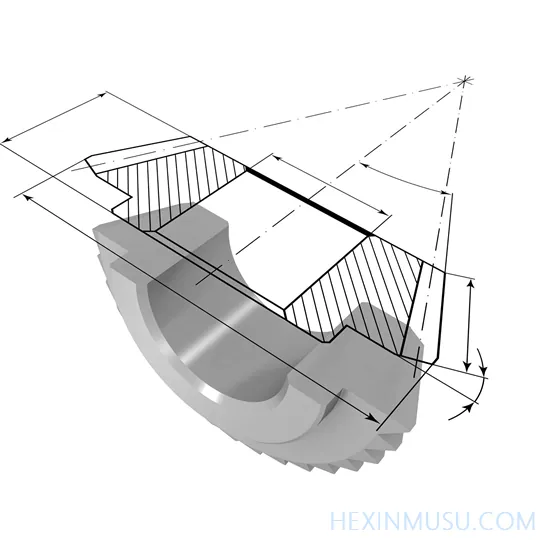
实例一
针对某复杂曲面零件的加工余量优化,采用遗传算法对加工参数进行优化,实现了加工余量的显著降低,提高了加工效率。
实例二
针对某航空发动机叶片的加工余量优化,采用粒子群算法对切削路径进行规划,在保证加工精度的前提下,有效减少了加工余量,降低了刀具磨损。
实例三
针对某模具型腔的加工余量优化,采用模拟退火算法对切削参数进行优化,实现了加工余量的最小化,提高了加工质量和效率。
数控机床加工余量的控制
实时采集数据
通过传感器和监测设备,实时采集数控机床的加工数据,如切削力、切削温度、刀具磨损等.
数据分析与处理
对采集到的实时数据进行处理和分析,以评估加工过程的稳定性和预测余量变化。
异常检测与报警
通过实时监控系统,及时发现加工过程中的异常情况,如刀具磨损过度、切削力异常等,并发出报警提示。
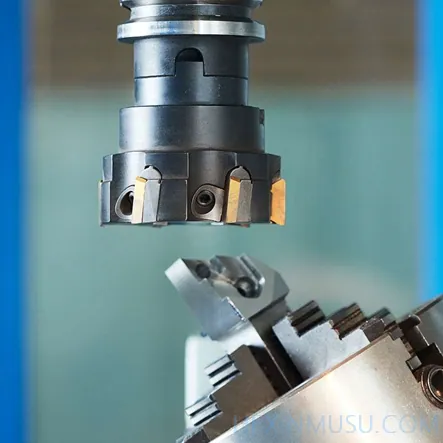
CNC加工余量不足时的预警系统
- 余量阈值设定 :根据加工要求和工艺参数,设定合理的余量阈值,当余量低于该阈值时触发预警。
- 预警方式 :通过声光电等多种方式,及时向操作人员发出预警信号,提醒操作人员关注并采取相应措施。
- 预警记录与处理 :对预警信息进行记录和整理,以便后续分析和处理,同时采取相应措施调整加工参数或更换刀具。
余量控制系统的设计与实现
系统架构设计
根据数控机床加工余量的控制需求,设计合理的系统架构,包括硬件和软件部分。
数据处理算法
研究和开发适用于实时监控和预警系统的数据处理算法,以提高数据处理速度和准确性。
系统集成与调试
将各个模块集成到系统中,并进行调试和优化,以确保系统的稳定性和可靠性。
余量确定技术的发展趋势
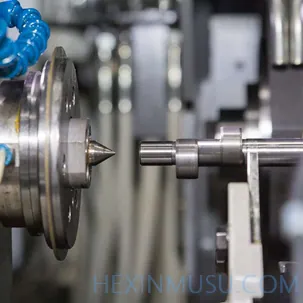
智能化
利用人工智能和机器学习技术,实现加工余量的自动识别和预测提高加工精度和效率。
精细化
实现加工余量的精确控制,满足通过高精度测量和数据处理技术,:高精度加工需求。
集成化
将余量确定技术与工艺规划、加工仿真等集成,实现加工过程的全面优化。
余量优化技术的创新方向
工艺创新
研究新的加工工艺和方法,降低加工余量,提高加工效率。
材料创新
开发新型材料,降低材料对加工余量的影响,提高加工质量。
算法创新
研究新的算法和技术,优化加工余量的计算和控制,提高加工精度。
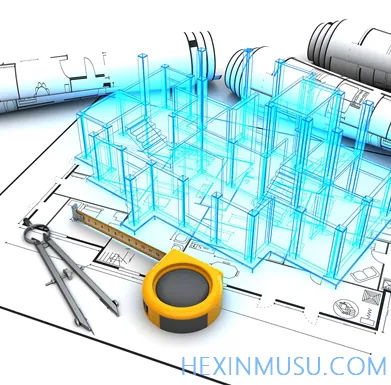