تقنية الصب بالقالب: عملية تصنيع رئيسية لتحويل الرؤى إلى واقع ملموس
التاريخ:2024-12-24 الفئات:التدوين الآراء:1051
في التصنيع الحديث، تعتبر عملية الصب بالقالب وسيلة هامة لتصنيع الأجزاء المعدنية الدقيقة. إنها قادرة على إنتاج أجزاء معدنية معقدة الشكل عن طريق حقن المعدن المنصهر في قوالب دقيقة تحت ضغط عالٍ، وتستخدم على نطاق واسع في صناعة السيارات والإلكترونيات وغيرها من المجالات، مما يدعم التطور التكنولوجي للعديد من الصناعات الرائدة. ستقدم هذه الورقة تحليلاً متعمقاً للعمليات الأساسية واختيار المواد وتطبيقات عملية الصب بالقالب، وكيف تحقق هذه العملية الابتكار والتميز في التصنيع.
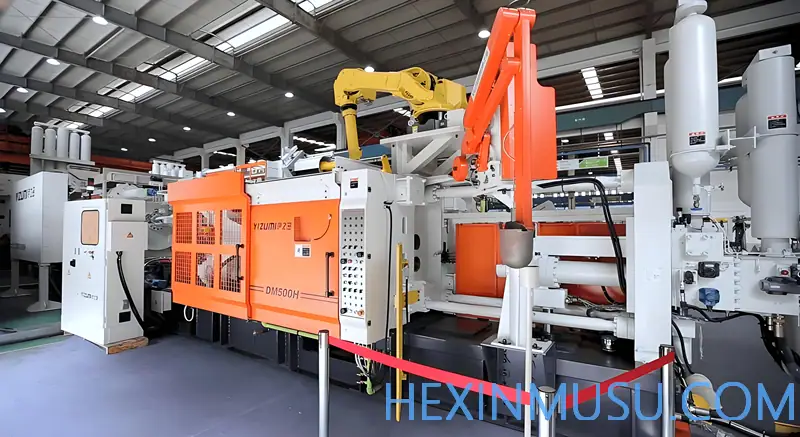
ما هو الصب بالقالب؟
الصب بالقالب هو طريقة فعالة ودقيقة لصب المعادن تستخدم قوالب قابلة لإعادة الاستخدام لإنتاج أجزاء معدنية معقدة الشكل. وعلى عكس عمليات الصب التقليدية، فإن الصب بالقالب يحقن المعدن المنصهر في القالب تحت ضغط عالٍ وهو مناسب بشكل خاص للإنتاج بكميات كبيرة، مما يوفر دقة عالية وقابلية للتكرار وتشطيبات سطحية ممتازة.
وقد استُخدمت عملية الصب بالقالب في البداية في صناعة الطباعة، ولكن سرعان ما توسعت إمكانية استخدامها على نطاق واسع لتشمل عدداً من المجالات، بما في ذلك صناعات السيارات والفضاء والإلكترونيات. واليوم، تستخدم عملية الصب بالقالب بشكل أساسي المعادن الخفيفة مثل الألومنيوم والزنك والمغنيسيوم لتلبية احتياجات التصنيع لمجموعة واسعة من المنتجات، بدءًا من المكونات الصغيرة والمعقدة إلى قطع السيارات المهمة. وتتمثل الميزة الأساسية لصب القوالب في قدرتها على إنشاء أجزاء ذات تفاوتات ضيقة للغاية وتقليل الحاجة إلى التصنيع الآلي اللاحق، مما يجعلها تقنية لا غنى عنها في التصنيع الحديث.
عملية الصب بالقالب
يمكن تقسيم عملية إنتاج الصب بالقالب إلى عدة خطوات رئيسية:
- تحضير القالب
القوالب هي أساس عملية صب القوالب، وتشمل الأنواع الشائعة من القوالب القوالب ذات التجويف الواحد، والقوالب متعددة التجاويف والقوالب المركبة. يجب أن يأخذ تصميم القالب في الاعتبار مدى تعقيد الجزء وحجم الإنتاج، ويجب تنظيف القالب وتسخينه قبل الاستخدام لتجنب التشققات والعيوب الحرارية. - عملية الحقن
أثناء عملية الحقن، يتم صهر المعدن المنصهر وحقنه في القالب في أنظمة مختلفة. في حالة نظام الحجرة الساخنة، يتم الصهر داخل ماكينة الصب، بينما يقوم نظام الحجرة الباردة بصب المعدن المنصهر في الحجرة الباردة حيث يتم حقنه في القالب بالضغط. - التبريد والتصلب
يتم تبريد المعدن المنصهر وتجميده في قالب لتشكيل الجزء النهائي. تتطلب عملية التبريد ضغطًا مضبوطًا لمنع حدوث عيوب في الجزء بسبب الانكماش. - قذف (من طائرة)
بمجرد أن يتصلب المعدن بالكامل، يتم فتح القالب ويقوم قاذف الماكينة بدفع الجزء للخارج. - التشذيب والمعالجة اللاحقة
ولضمان جودة الجزء، يجب إزالة المواد الزائدة والنتوءات. وإذا لزم الأمر، يمكن تحسين دقة الجزء بشكل أكبر من خلال طرق ما بعد المعالجة مثل الطحن.
أنواع قوالب الصب بالقالب
واعتمادًا على عملية الصهر والحقن، يمكن تقسيم عملية الصب بالقالب إلى نوعين رئيسيين: الصب بالقالب بالغرفة الساخنة والصب بالقالب بالغرفة الباردة:
- صب القوالب بالقالب بالخلية الساخنة (علم المعادن)
مناسب للمعادن ذات درجة الانصهار المنخفضة مثل الزنك وبعض المعادنالألومنيوم. تستخدم هذه العملية مكبساً هوائياً لحقن المعدن في القالب من خلال خزان معدني منصهر متصل بماكينة صب القوالب. وهي عملية فعّالة وسريعة ومناسبة لإنتاج كميات كبيرة من الأجزاء الصغيرة، وتستخدم عادةً في إنتاج الإلكترونيات الاستهلاكية. - الصب بالقالب بالغرفة الباردة (علم المعادن)
تستخدم للمعادن ذات درجة الانصهار العالية مثل سبائك الألومنيوم والنحاس. في عملية الصب بالقالب بالغرفة الباردة، يتم صب المعدن المنصهر أولاً في غرفة باردة ثم يتم حقنه في القالب من خلال مكبس. هذه العملية مناسبة للأجزاء التي تتطلب قوة عالية ومقاومة للحرارة وتستخدم على نطاق واسع في تطبيقات السيارات والفضاء.
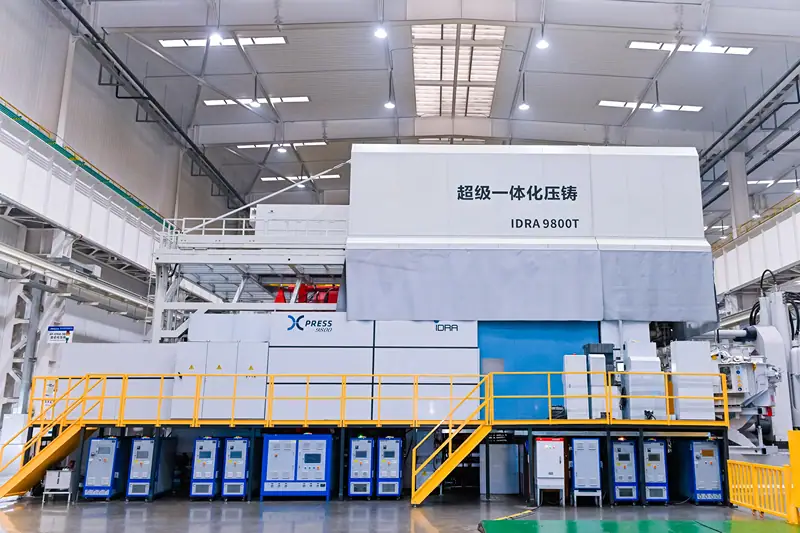
متغيرات وابتكارات الصب بالقالب
مع استمرار تطور التكنولوجيا، شهدت عملية الصب بالقالب مجموعة متنوعة من المتغيرات والابتكارات لتلبية الاحتياجات الصناعية المختلفة. على سبيل المثال
- صب القوالب بالجاذبية:: يتم حقن المعدن المنصهر في القالب باستخدام الجاذبية، مما يجعلها مناسبة لإنتاج كميات كبيرة من المسبوكات الدقيقة.
- صب القوالب بالضغط:: تعبئة المعدن بالضغط المنخفض أو المرتفع، وهي مناسبة لإنتاج الأجزاء ذات المتطلبات العالية الدقة، مثل أجزاء السيارات والفضاء.
- الصب بالقالب المفرغ من الهواء:: تحسين جودة السطح ودقة الأبعاد من خلال تهيئة بيئة تفريغ تقلل من احتباس الهواء ومناسبة للمنتجات عالية الجودة.
- الصب بالقالب بالبثق:: يمكنها تحسين الخواص الميكانيكية ودقة الأجزاء وتستخدم عادة في قطع غيار السيارات.
- صب القوالب شبه الصلبة:: إنتاج أجزاء ذات أشكال هندسية معقدة بدقة وقوة أعلى عن طريق درجات حرارة صب محددة.
مقارنة بين مزايا وعيوب الصب بالقالب
إن مزايا الصب بالقالب المعدني، وهي عملية تصنيع تستخدم على نطاق واسع في الإنتاج الصناعي، جعلتها مهمة في الإنتاج الضخم. ومع ذلك، فإن لها أيضًا بعض القيود التي قد تؤثر على استخدامها في سيناريوهات تطبيق معينة. فيما يلي تحليل المزايا والعيوب الرئيسية لعملية الصب بالقالب وأسبابها:
مزايا الصب بالقالب
- دقة أبعاد ممتازة
الصب بالقالب المعدني قادر على إنتاج أجزاء ذات دقة أبعاد عالية، وهو مناسب بشكل خاص للتطبيقات التي تتطلب تفاوتات ضيقة. وتعتمد الدقة على تصميم القالب وعملية التصنيع، ويمكن تحقيق دقة أبعاد أعلى خاصةً عندما يتم تصنيع القوالب باستخدام ماكينات CNC عالية الدقة، مثل ماكينات CNC ذات 5 محاور. بالإضافة إلى ذلك، يساعد استخدام متغيرات العملية مثل الصب بالقالب منخفض الضغط (LPDC) والصب بالقالب بالجاذبية على ملء القوالب بدقة، وبالتالي زيادة دقة الجزء. - هندسة معقدة
يتميز الصب بالقالب بقدرته على إنتاج أجزاء ذات أشكال هندسية معقدة، بما في ذلك المسبوكات والجدران الرقيقة وغيرها من التصميمات. وقد مكّنت هذه الميزة عملية الصب بالقالب من إنتاج أجزاء ذات هياكل معقدة ومجموعة واسعة من الوظائف في مجالات مثل الفضاء والسيارات والإلكترونيات الاستهلاكية. وبهذه الطريقة، يمكن للمصممين دمج المزيد من الوظائف في جزء واحد، مما يقلل من الحاجة إلى التجميع اللاحق. - إنتاج بكميات كبيرة للتسليم السريع
الصب بالقالب هو عملية إنتاج بكميات كبيرة مناسبة لتصنيع كميات كبيرة من الأجزاء. في عملية الصب بالضغط العالي، يكون الإنتاج أسرع بسبب الضغوط العالية المستخدمة، مما يقلل من تكلفة الإنتاج لكل وحدة من الأجزاء. وفي حالة القوالب المركبة على وجه الخصوص، يمكن تصنيع أجزاء متعددة في وقت واحد، مما يزيد من الإنتاجية وفعالية التكلفة لكل جزء. - تشطيب سطح أملس
نظرًا للضغط العالي الذي يتم حقنه في المعدن أثناء عملية الصب بالقالب، فإن الأجزاء المعدنية المصبوبة عادةً ما يكون سطحها أملس، خاصةً فيالصب بالضغط المنخفضوصب الجاذبيةوعمليات أخرى. لا تعمل هذه المعالجة السطحية عالية الجودة على تحسين مظهر الجزء فحسب، بل تقلل أيضًا من مقدار الجهد المطلوب للمعالجة السطحية اللاحقة. - عمر طويل للعفن
قالب الصب بالقالبوعادةً ما تكون مصنوعة من الفولاذ عالي الجودة مع مقاومة ممتازة لدرجات الحرارة والضغوط العالية. يمكّن هذا الفولاذ المتين القوالب من تحمل الاستخدام لفترات طويلة وعمر خدمة طويل، مما يقلل من تكرار استبدال القوالب وتكاليف الصيانة للإنتاج طويل الأجل.
عيوب الصب بالقالب
- للمعادن غير الحديدية فقط
يتم تطبيق عملية الصب بالقالب بشكل أساسي على المعادن غير الحديدية مثل الألومنيوم والزنك والمغنيسيوم. هذه المعادن لها درجات انصهار معتدلة ويمكن حقنها بسهولة في القوالب تحت ضغط عالٍ. ومع ذلك، بالنسبة للمعادن الحديدية ذات درجات انصهار أعلى، مثل الصلب والحديد، فإن الصب بالقالب غير مناسب. وتتطلب معادن مثل الصلب والحديد معدات خاصة وعمليات أكثر تعقيدًا لصبها، مما يجعل نطاق استخدامات الصب بالقالب محدودًا إلى حد ما. - تكلفة العفن العالية
تكون قوالب الصب بالقالب أكثر تكلفة في التصنيع، خاصة عند استخدامالتصنيع الآلي بالتحكم العدديعندما يتعلق الأمر بصناعة القوالب، فإن العملية معقدة ومكلفة. وعند تصنيع الأجزاء المعقدة على وجه الخصوص، فإن استخدام القوالب الفولاذية عالية الجودة سيؤدي إلى زيادة التكاليف. وعلى الرغم من أن عملية الصب بالقالب مناسبة للإنتاج بكميات كبيرة، إلا أن تكلفة الأدوات يمكن أن تكون عاملاً مقيداً للدفعات الصغيرة أو الأجزاء المعقدة. - الحساسية للعيوب
قد تظهر أجزاء الصب بالقالب في عملية الإنتاج مسامية وانكماش ومسامية وعيوب أخرى، خاصة في الصب بالضغط العالي، هذه العيوب أكثر شيوعًا. على سبيل المثال، قد يؤدي احتباس الهواء أثناء عملية الصب إلى تكوين مسام على سطح الجزء، وقد تشكل هذه المسام فقاعات هواء أثناء المعالجة الحرارية، مما يؤثر على جودة الجزء. قد تكون هناك حاجة إلى خطوات تشطيب سطحية إضافية لمعالجة هذه العيوب، مما يزيد من تكاليف الإنتاج. - غير مناسب للإنتاج على نطاق صغير
على الرغم من أن عملية الصب بالقالب مناسبة للإنتاج على نطاق واسع، إلا أنها تنطوي على استثمار أولي مرتفع، خاصة من حيث التكاليف الثابتة مثل تصنيع القوالب وإعداد المعدات. ونتيجة لذلك، عادةً ما تكون عملية الصب بالقالب غير مناسبة للإنتاج على نطاق صغير أو إنتاج جزء لمرة واحدة. بالنسبة للإنتاج على نطاق صغير، قد تكون العمليات الأخرى (مثل القولبة بالحقن أو التصنيع باستخدام الحاسب الآلي) أكثر ملاءمة ويمكن أن تقلل من التكاليف ومهل الإنتاج.
مواد هيرشي المعدنية في الصب بالقالب
عادةً ما تكون المواد المعدنية المستخدمة في عملية الصب بالقالب عبارة عن سبائك غير حديدية مثل الألومنيوم والمغنيسيوم والزنك. تتميز هذه السبائك بخصائص أداء مختلفة ومناسبة لمتطلبات التطبيقات المختلفة. يقدم الجدول التالي مقارنة تفصيلية لسبائك الصب بالقالب الشائعة، مع سرد تركيباتها الرئيسية ونقاط انصهارها وخصائصها وتطبيقاتها النموذجية.
السبائك | الأنواع الفرعية الشائعة | القاعدة | نقطة الانصهار (درجة مئوية) | الخصائص الرئيسية | التطبيق النموذجي |
---|---|---|---|---|---|
الألومنيوم | A380، A360، A390، A390، A413، ADC12 | الألومنيوم (Al)، النحاس (Cu)، السيليكون (Si)، المغنيسيوم (Mg) | 577 - 660 | خفيفة الوزن، ومقاومة للتآكل، وقوة عالية، وقابلية تشغيل جيدة، وفعالية من حيث التكلفة. | السيارات (مكونات المحرك، والعجلات، والهيكل)، والفضاء (المكونات الهيكلية، والمباني)، والإلكترونيات (المباني، والهيكل) |
سبائك المغنيسيوم | AZ91D, AM60B, AS41B, AZ91D, AM60B, AS41B | المغنيسيوم (Mg)، الألومنيوم (Al)، الزنك (Zn) | 632 - 650 | خفيف للغاية وقابلية صب جيدة للاستخدامات الحساسة للوزن وقابلية صب ممتازة. | الفضاء الجوي (هيكل الهيكل والأجزاء الداخلية)، والسيارات (المكونات خفيفة الوزن)، والإلكترونيات (الأجهزة المحمولة باليد، وأغطية الهواتف المحمولة) |
سبيكة الزنك | سبائك الزنك #2، #3، #5، #5، #7، ZA8، ZA27 | الزنك (Zn)، الألومنيوم (Al)، النحاس (Cu)، المغنيسيوم (Mg) | 381 - 419 | قابلية صب ممتازة ونقطة انصهار منخفضة ومناسبة للتصميمات المعقدة وفعالة من حيث التكلفة. | الإلكترونيات (الموصلات، العلب)، والأجهزة (الأقفال، والأزرار)، ولعب الأطفال وقطع غيار السيارات (قطع الديكور، والتروس) |
سبيكة نحاس | نحاس (مثل C85700)، برونز (مثل C93200) | النحاس (النحاس)، الزنك (الزنك) (النحاس الأصفر)؛ النحاس (النحاس)، القصدير (القصدير) (البرونز) | 900 - 1083 | قوة عالية، وموصلية ممتازة ومقاومة ممتازة للتآكل، ومتينة. | الأنابيب (أنابيب المياه المقاومة للتآكل، وأنابيب الغاز)، والموصلات الكهربائية (أطراف التوصيلات، والتلامس الكهربائي)، والمكونات البحرية (مكونات مقاومة للتآكل)، والمحامل |
سبيكة القصدير | - | القصدير (Sn) (90%)، والنحاس (Cu) (2.5%)، والرصاص (Pb) (7.5%)، والأنتيمون (Sb) | 170 - 230 | نقطة انصهار منخفضة، وسيولة جيدة، ومقاومة للتآكل، وسهولة الصب. | أدوات الزينة (المجوهرات والمشغولات اليدوية) والتماثيل والهدايا التذكارية |
سبيكة رصاص | - | الرصاص (Pb)، القصدير (Sn) | 183 - 327 | نقطة انصهار منخفضة، ناعمة، مقاومة جيدة للتآكل، مناسبة للوقاية من الإشعاع. | التدريع الإشعاعي (المعدات الطبية، المنشآت النووية)، البطاريات (يتم استبدالها تدريجياً) |
سبيكة أساسها القصدير | - | القصدير (Sn)، النحاس (Cu)، الأنتيمون (Sb) | 232 | نقطة انصهار منخفضة، وخصائص صب جيدة، ومقاومة جيدة للتآكل. | المكونات الإلكترونية (مواد اللحام، والأجزاء الإلكترونية)، والمجوهرات، والتطبيقات الخاصة (الأجزاء الصغيرة، والمجوهرات الفاخرة) |
مقارنة الصب بالقالب مع عمليات التصنيع الأخرى
غالبًا ما يتم الخلط بين عملية الصب بالقالب وعمليات التصنيع الأخرى (مثل القولبة بالحقن، والتشكيل، والختم، وما إلى ذلك)، خاصةً بالنسبة لأولئك الجدد في مجال التصنيع. وعلى الرغم من أوجه التشابه بينهما، فإن لكل عملية فوائدها الفريدة ومجالات تطبيقها. فيما يلي مقارنة بين عملية الصب بالقالب والعمليات الشائعة مثل القولبة بالحقن والتشكيل للمساعدة في فهم الاختلافات وسيناريوهات التطبيق:
الفرق بين الصب بالقالب والقولبة بالحقن
إن الصب بالقالب والقولبة بالحقن هما عمليتا قولبة شائعتان، وكلاهما يستخدمان مبدأ الحقن وهما مناسبتان لتصنيع الأجزاء ذات التفاصيل المعقدة والتشطيب السطحي الممتاز. ومع ذلك، تختلف المواد والعمليات المستخدمة فيهما. وفيما يلي الاختلافات الرئيسية بين العمليتين:
التباين | صب القوالب | القولبة بالحقن |
---|---|---|
سير العمل | حقن المعدن المنصهر تحت الضغط في قوالب الصلب المصممة مسبقًا | حقن البلاستيك المصهور تحت الضغط في قوالب مصممة مسبقًا من الصلب أو الألومنيوم |
الماكينات | السبائك المعدنية غير الحديدية (مثل الألومنيوم والزنك والمغنيسيوم) | اللدائن الحرارية أو اللدائن الحرارية |
مواد القوالب | الصلب (الكيمياء) | فولاذ أو ألومنيوم |
التهدئة | وقت تهدئة أطول | فترة تهدئة أقصر |
سرعة الإنتاج | بطيئة نسبيًا | قريبًا نسبيًا |
تكلفة المعالجة | ارتفاع تكاليف القوالب (باستخدام قوالب الصلب) | انخفاض تكاليف الأدوات (باستخدام أدوات الألومنيوم) |
تكلفة المكوّن | أعلى (بسبب طول وقت الإنتاج) | أقل (وقت إنتاج أسرع) |
الفرق بين الصب بالقالب والتشكيل
الفرق الرئيسي بين التشكيل والصب بالقالب هو طريقة التشكيل. تتضمن عملية التشكيل تشكيل المعدن في حالة صلبة من خلال تطبيق قوى الضغط، بينما تتضمن عملية الصب بالقالب حقن المعدن المنصهر في قالب مصمم مسبقًا. وتختلف العمليتان أيضًا من حيث المواد القابلة للتطبيق وسرعة الإنتاج وأداء الأجزاء:
التباين | حدادة (معدن) | صب القوالب |
---|---|---|
سير العمل | تشكيل المعدن المسخن عن طريق تطبيق قوة ضاغطة | حقن المعدن المنصهر في قالب تحت الضغط |
الماكينات | للمعادن الحديدية وغير الحديدية مثل الصلب والألومنيوم | بالنسبة للمعادن غير الحديدية مثل الألومنيوم والزنك والمغنيسيوم |
مواد التشكيل | لا حاجة للقوالب، ولكن استخدام القوالب لتحسين الشكل | يجب استخدام القوالب |
سرعة الإنتاج | أبطأ | قريبًا نسبيًا |
التحكم في التحمل | تحمّل متوسط | تحكم عالي الدقة في التحمل |
خصائص الجزء الأخير | تحسين الخواص الميكانيكية | تعتمد الخواص الميكانيكية على مادة الصب |
الفرق بين الصب بالقالب والختم
الختم هو عملية تشكيل الصفائح المعدنية بواسطة مكبس وهو مناسب للإنتاج الضخم للأجزاء رقيقة الجدران. وبالمقارنة مع الصب بالقالب، فإن عملية الختم لها مواد وعمليات تشكيل مختلفة، خاصة من حيث تعقيد الأجزاء القابلة للتطبيق والإنتاجية:
التباين | صب القوالب | لكمة |
---|---|---|
سير العمل | حقن المعدن المنصهر في قالب للتشكيل | تشكيل الأجزاء عن طريق ختم الصفائح المعدنية باستخدام قالب. |
الماكينات | السبائك المعدنية غير الحديدية بشكل رئيسي (مثل الألومنيوم والزنك) | مناسبة لجميع أنواع الصفائح المعدنية (مثل الصلب والألومنيوم) |
مواد القوالب | الصلب (الكيمياء) | الصلب (الكيمياء) |
شكل الجزء | للأجزاء المعقدة الشكل | للأجزاء رقيقة الجدران والأشكال البسيطة |
سرعة الإنتاج | أبطأ | قريبًا نسبيًا |
دقيقة | عالية الدقة | دقة أقل |
الفرق بين الصب بالقالب والطباعة ثلاثية الأبعاد
الطباعة ثلاثية الأبعاد هي عملية قائمة على التصنيع الإضافي تقوم بإنشاء الأجزاء عن طريق تكديس المواد طبقة تلو الأخرى. وتوفر الطباعة ثلاثية الأبعاد مرونة أكبر وقدرات إنتاج نماذج أولية أسرع من صب القوالب، ولكنها تختلف في سرعة الإنتاج وأداء الأجزاء:
التباين | صب القوالب | الطباعة ثلاثية الأبعاد |
---|---|---|
سير العمل | حقن المعدن المنصهر في قالب للتشكيل | طباعة طبقة تلو الأخرى للمواد بناءً على النماذج الرقمية |
الماكينات | السبائك المعدنية غير الحديدية (مثل الألومنيوم والزنك) | اللدائن الحرارية، مساحيق المعادن، إلخ. |
مواد القوالب | الصلب (الكيمياء) | لا حاجة للقوالب |
سرعة الإنتاج | أبطأ | قريبًا نسبيًا |
دقيقة | عالية الدقة | دقة معتدلة |
الأجهزة | الإنتاج الضخم للأجزاء المعقدة | النماذج الأولية السريعة والإنتاج منخفض الحجم |
مواد الصب بالقالب الشائعة واختيارها
يُعد الألومنيوم والزنك والمغنيسيوم وسبائك المغنيسيوم وسبائك أخرى من المواد الشائعة في الصب، ولكل منها خصائص فريدة من نوعها، ومناسبة لسيناريوهات الاستخدام المختلفة. فيما يلي خصائص العديد من السبائك الشائعة:
- الألومنيوم:: خفيفة الوزن، ومقاومة للتآكل، وسهلة المعالجة، وتستخدم على نطاق واسع في صناعة السيارات والفضاء والإلكترونيات.
- سبائك المغنيسيوم:: خفيف الوزن للغاية للتطبيقات ذات الوزن الحرج مثل الفضاء والإلكترونيات الاستهلاكية.
- سبيكة الزنك:: درجة انصهار منخفضة، وقابلية صب ممتازة، وتستخدم عادة في المنتجات الإلكترونية والأجهزة وقطع غيار الألعاب.
- سبيكة نحاس:: قوة عالية وتوصيل كهربائي جيد للموصلات الكهربائية والمكونات البحرية.
تحسين التصميم والتصنيع
لا يعتمد تصميم الصب بالقالب على اختيار المواد فحسب، بل يحتاج أيضًا إلى مراعاة عوامل مثل هندسة الجزء، وزاوية السحب، ونصف قطر الشريحة، وما إلى ذلك، من أجل تحسين أداء الجزء، وقابلية التصنيع وفعالية التكلفة. على سبيل المثال، يمكن لزاوية السحب المناسبة أن تمنع بشكل فعال التصاق الأجزاء بالقالب وتقلل من خطر التلف؛ ويمكن أن يساعد نصف قطر الشريحة المعقول على توزيع الضغوط بالتساوي وتجنب تركيزات الضغط.
التوصل إلى حكم
لقد أصبحت تقنية الصب بالقالب تقنية لا غنى عنها في التصنيع الحديث، وذلك بفضل دقتها العالية وقدراتها الإنتاجية الكبيرة الحجم. سواءً كانت قطع غيار السيارات أو العلب الإلكترونية أو مكونات الطيران، فإن تقنية الصب بالقالب توفر أساسًا متينًا للابتكار والتميز في التصميم. ومع استمرار تقدم المواد والعمليات، ستستمر تقنية الصب بالقالب في تقديم حلول أكثر كفاءة وأعلى جودة لمجموعة متنوعة من الصناعات في المستقبل.
مشاكل الصب بالقالب الشائعة واستراتيجيات التعامل معها
لماذا تكون مصبوبات القوالب عرضة للمسامية؟
عادةً ما تكون الجيوب ناتجة عن عدم تنفيس المعدن بالكامل أثناء عملية الحقن، أو بسبب التصميم المعيب للقالب (مثل نظام تنفيس رديء). تشمل الاستراتيجيات تحسين تصميم تنفيس القالب، وضبط سرعة الحقن والضغط، واستخدام نظام تنفيس أكثر كفاءة.
لماذا من المحتمل أن تظهر العيوب على سطح مصبوبات القوالب؟
تنتج العيوب السطحية مثل الفقاعات والتجاعيد والخدوش في الغالب عن أسطح القالب غير المستوية أو التدفق المعدني غير المتساوي. ولتجنب مثل هذه المشاكل، يجب فحص سطح القالب بانتظام للتأكد من استقرار درجة حرارة الحقن ومعدل التدفق.
ما هي مشكلة ثقوب الانكماش في مصبوبات القوالب؟
يرجع سبب الانكماش إلى فشل انكماش معدن التبريد في الصب في تجديد الحشو، وغالبًا ما يظهر في الشكل الكبير أو المعقد لقالب الصب. يمكن تجنب الانكماش بفعالية من خلال تحسين تصميم القالب، وتحسين كفاءة نظام الصب وضبط معدل التبريد.
هل مصبوبات القوالب عرضة للتشقق؟
عادةً ما يحدث التشقق عندما يتدفق المعدن بشكل غير متساوٍ أو يبرد بسرعة كبيرة، ويمكن أن يحدث بسبب ضغط الحقن المفرط أو سوء تصميم القالب. يمكن الحد من التشقق عن طريق التحكم في سرعة الحقن ودرجة الحرارة والضغط، وباستخدام مواد عالية القوة.
ماذا عن عدم استقرار الأبعاد في مصبوبات القوالب؟
قد يرجع عدم ثبات الأبعاد إلى تآكل القالب أو ضغط الحقن غير المستقر أو التحكم غير السليم في درجة الحرارة. يمكن للإصلاحات والصيانة الدورية للقالب للحفاظ على ظروف حقن مستقرة، بالإضافة إلى الضبط الدقيق لنظام التحكم في درجة الحرارة، أن تحل مشكلة عدم استقرار الأبعاد بشكل فعال.
كيف يؤثر تآكل القالب على جودة الصب بالقالب؟
يمكن أن يؤدي تآكل القوالب وتلفها إلى فقدان دقة المنتج وحتى التأثير على مظهر وأداء المسبوكات. ولمكافحة تآكل القوالب، ينبغي فحص القوالب واستبدالها بانتظام، وينبغي استخدام مواد مقاومة للتآكل، كما ينبغي تحسين تصميم القوالب وعملية تصنيعها.
لماذا تكون مصبوبات القوالب عرضة للتشوه؟
عادةً ما يكون التشوه ناتجًا عن التبريد غير المتكافئ أو سوء تصميم القالب، خاصةً عندما يكون الصب كبيرًا أو معقدًا. يمكن تقليل خطر التشوه عن طريق ضبط نظام التبريد وتحسين تصميم القالب.
كيف يمكن الحد من الفصل البارد؟
الفصل على البارد هو عيب في التفكيك يتشكل بسبب فشل المعدن في الانصهار الكامل عند حقنه في القالب. ولمنع الفصل البارد، يجب تحسين سرعة الحقن ودرجة الحرارة لضمان التدفق السلس للمعدن، كما يجب تصميم نظام الصب والعدّادات بشكل مناسب.
هل المعالجة اللاحقة لمسبوكات القوالب ضرورية؟
وتعتمد متطلبات ما بعد المعالجة لمسبوكات القوالب على متطلبات التصميم ومعايير جودة السطح للجزء. وتتطلب بعض الأجزاء عمليات تصنيع إضافية مثل الطحن أو الحفر أو إزالة الأزيز لتلبية التفاوتات الصارمة والتشطيبات السطحية.