高品质零件
HEXIN有15年制造经验,可提供精密压铸,并在各个阶段进行全面的质量检查:生产前、生产中、首件检验和交付前。
快速产品交期
HEXIN 的中国压铸制造商网络确保高效快速生产。我们的能力包括支持复杂定制项目的先进自动化设施。
压铸专家
作为定制压铸解决方案的专家,我们可提高产品耐用性并降低成本。我们先进的技术和机械可确保每个部件都具有高品质、功能性和美观性。
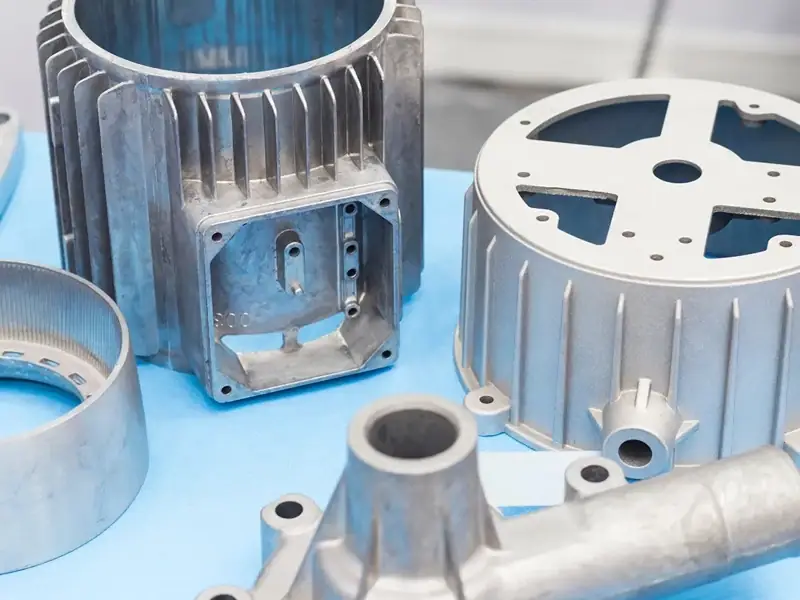
什么是压铸
压铸是通过模具成型金属零件的工艺,主要分为高压铸造(高压快速成型,适合复杂精密件与薄壁结构)、低压铸造(低压缓速填充,专攻高力学性能与中空部件)和重力铸造(自然重力浇注,适配大型简单零件)。贺鑫模塑基于精密压铸设备与定制化工艺,针对新能源汽车、电子散热器等领域需求,提供从模具设计到后处理的全流程服务,兼顾部件的高精度、高致密性及表面光洁度,助力客户优化生产效率与产品性能,实现从原型开发到批量制造的无缝衔接。
在贺鑫,我们的专家团队会仔细审查每个压铸项目,以确保我们的方法符合您的特定要求。我们优先优化生产流程,确保每个部件都符合高标准的耐用性和美观性。通过专注于先进的铸造技术并利用精密压铸机,我们可以帮助您在功能和外观方面实现卓越的效果,最终提高产品的整体价值。
压铸的应用领域压铸是一种高精度、高效率的金属铸造工艺,因其能够制造尺寸精确、质量稳定的部件,广泛应用于多个行业。以下是压铸工艺的主要应用领域:
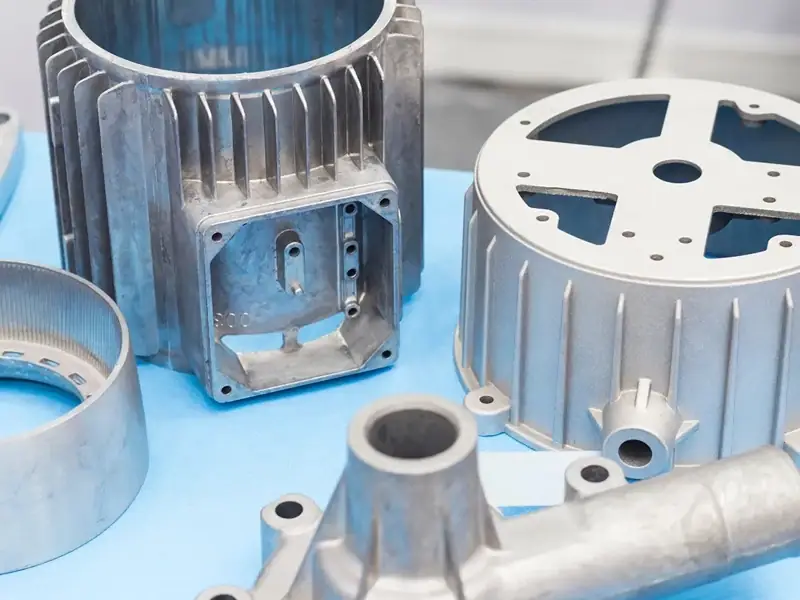
高压压铸优缺点高压压铸工艺在制造金属零件时,具有多项独特的优势,使其成为汽车、消费电子、家电行业中复杂精密部件的首选技术:
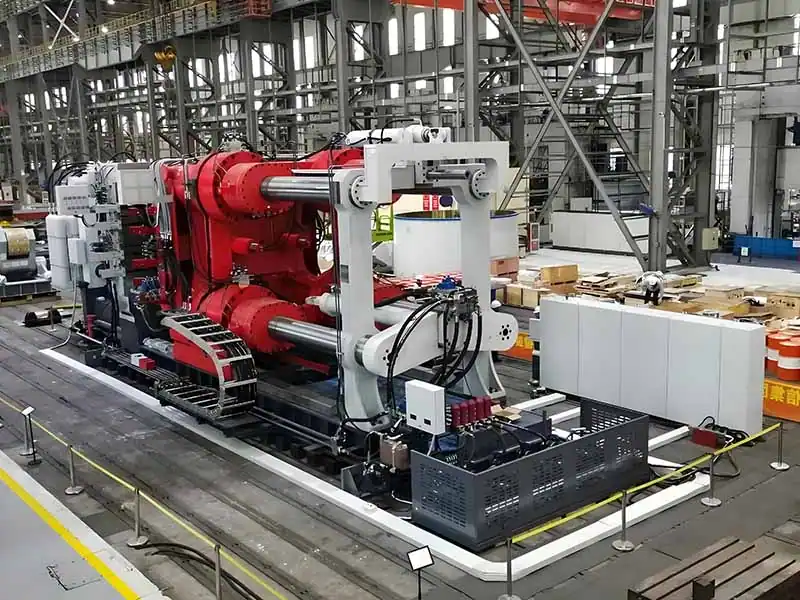
低压压铸的优缺点低压压铸工艺在制造金属零件时,具有多项独特的优势,使其成为汽车、航空航天、工业设备领域高力学性能部件的首选技术:
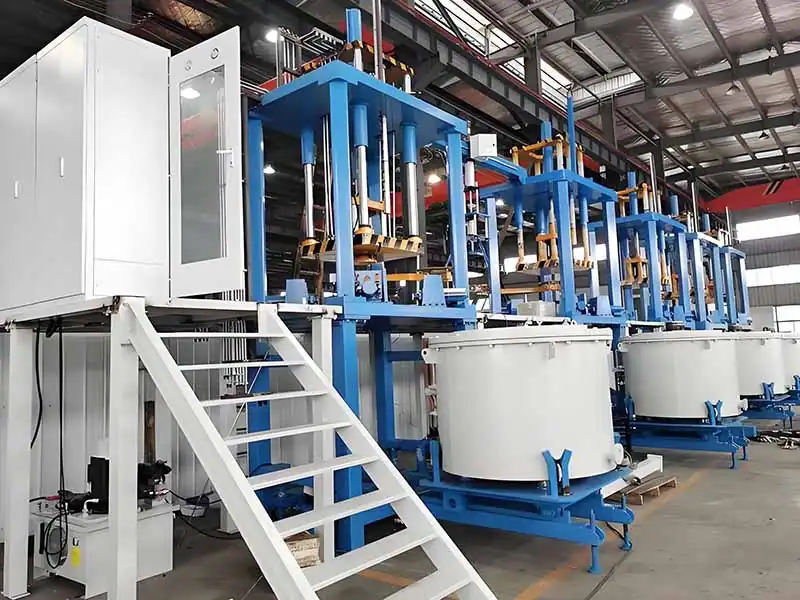
重力压铸优缺点重力压铸工艺在制造金属零件时,具有多项独特的优势,使其成为重型机械、农业设备、建筑行业中大型厚壁零件的首选技术:
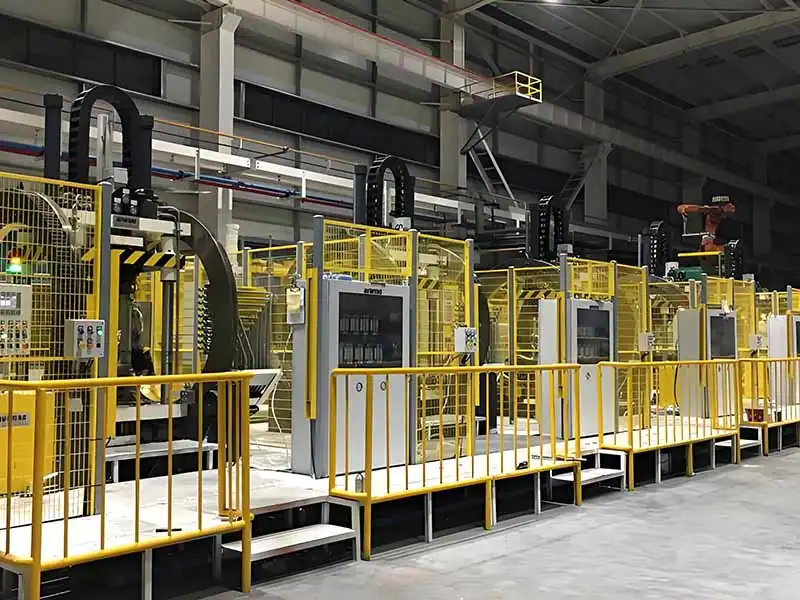
什么是压铸工艺?
压铸是一种将熔融金属(如铝、锌、镁合金)通过高压注入精密模具中的铸造工艺。该工艺能够生产形状复杂、尺寸精确的零件,广泛应用于汽车、电子、家电等行业。通过高压注入,熔融金属填充模具,经过冷却后形成零件,具有良好的表面质量和高强度。
压铸的生产效率如何?
压铸工艺的生产效率较高,适合大批量生产。模具一旦制作完成,可以进行大量零件的高效生产。由于高压注射熔融金属填充模具,零件在短时间内即可成型,缩短了生产周期,特别适合需求量大的行业,如汽车和电子行业。
压铸过程中可能出现哪些缺陷?
压铸过程中可能会出现以下缺陷:
- 气孔:由于气体未能排出或冷却不均而形成的空洞。
- 冷隔:由于金属未能完全流动并接合形成的裂缝或薄弱区域。
- 裂纹:由于模具设计不当、冷却不均或金属应力过大导致的裂纹。
- 表面缺陷:如划痕、气泡等,可能影响零件的外观质量。
压铸件是否可以进行后期加工?
是的,压铸件通常需要进行一定的后期加工,以进一步提高尺寸精度和表面质量。常见的后期加工工艺包括:
- 机加工:如铣削、车削等,用于调整零件尺寸,去除毛刺或不规则表面。
- 表面处理:如喷砂、抛光、阳极氧化等,用于提高零件的外观质量和耐腐蚀性能。
- 热处理:通过退火、淬火等方式,提高零件的硬度和强度,满足特定的工作要求。
压铸的公差是多少?
压铸工艺的公差通常在±0.1mm至±0.5mm之间,具体公差范围取决于零件的尺寸和形状。通过精密的模具设计和严格的工艺控制,压铸件可以达到较高的尺寸精度,适用于需要较高公差要求的行业应用。
压铸模具的交付周期通常多长?
压铸模具的交付周期通常为4到8周,具体取决于模具的复杂程度、材料的选择以及制造厂的生产能力。如果模具设计复杂或需要进行多次调整,交付时间可能会延长。
压铸设计需要注意哪些方面?
压铸设计需要考虑以下要点:
- 壁厚均匀性:零件的壁厚要均匀,避免出现冷隔或变形。
- 合理排气设计:设计排气孔来排出空气和气体,避免产生气孔缺陷。
- 冷却系统设计:模具内部要有合适的冷却通道,以确保金属熔液均匀冷却,减少内应力和变形。
- 流道和浇口设计:合理设计流道和浇口系统,保证金属的顺利流入模具,避免产生缺陷。
压铸中为什么会出现气孔,如何避免?
气孔是由气体或空气在熔融金属中未能完全排出而形成的。常见原因包括排气设计不良、金属注入速度过快、冷却不均等。避免气孔的措施有:
- 改善排气设计:确保模具设计有足够的排气孔。
- 控制注入速度:避免过高的注入压力和速度导致气体困 trapped。
- 优化铸造温度:确保金属熔液温度适宜,避免过冷或过热。