Plastic spraying process and its characteristics
Date: 2025-03-10 Categories: Blog Views: 131
Process Principle of Plastic Spraying
Electrostatic powder coating technology realizes high efficiency coating through high voltage electrostatic adsorption. The core process is: compressed air will be powder coating conveyed to the electrostatic spray gun, the muzzle of the high-voltage generator produces 80-100kV static field triggered corona discharge, so that the atomized powder charged; charged particles in the electric field under the action of directional adsorption on the surface of the grounded workpiece, along with the thickening of the coating to form a charge buildup, the uniformity of the film through the homogeneous static repulsive autonomy control; and ultimately by the high-temperature curing of the formation of a dense film to complete the whole process of industrialized application from powder adsorption to coating formation. Powder adsorption to the coating molding of the whole process of industrialized applications.
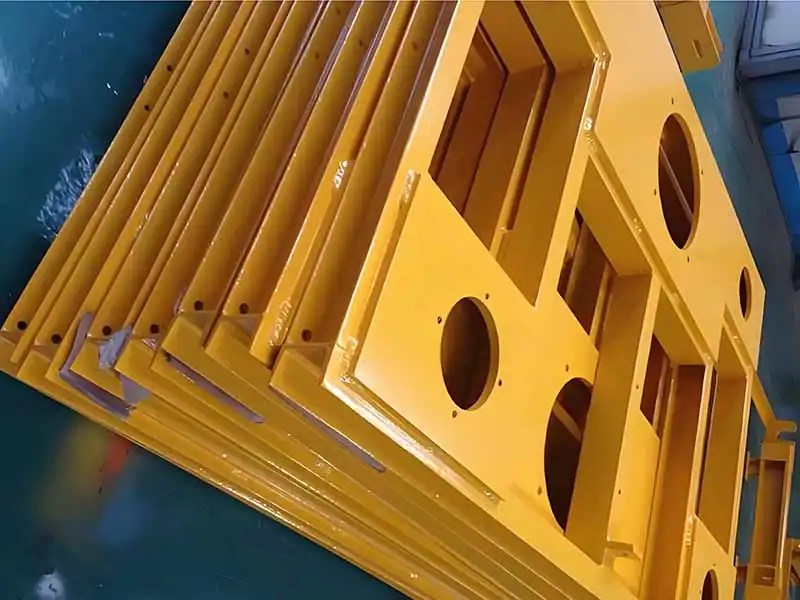
workflow
Process name | Purpose of the process task and detailed steps | Related equipment | Related materials |
---|---|---|---|
1. Pre-processing | goal: Removes contaminants from the surface of the workpiece and forms a phosphate layer that prevents rust and enhances adhesion. step by step: ① Degreasing: Acid degreaser (sulfuric acid/hydrochloric acid) to remove grease. ② Rust removal: pickling or mechanical grinding to eliminate oxidized layer ③ Phosphating: Generation of a gray crystalline phosphate film (2-4 g/m²) ④ Passivation: Enclosing the pores of phosphating film to improve corrosion resistance | Quadruple concrete treatment tanks (degreasing tanks/ pickling tanks/ phosphating tanks/ passivation tanks) | Sulfuric acid, hydrochloric acid, soda ash (Na₂CO₃) Acid degreaser, phosphate solution (zinc system), passivation solution (chromate) |
2. Electrostatic spraying | goal: Realization of uniform adsorption and efficient recovery of powder coatings step by step: ① Electrostatic generation: spray gun loaded with 60-100kV negative high voltage ② Powder atomization: compressed air (0.4-0.6MPa) disperses the powder. ③ Electric field adsorption: Directional deposition of charged powder on the surface of the workpiece. ④ Recycling treatment: cyclone + cartridge secondary recycling (95% utilization rate) | Multi-station electrostatic spraying machine Powder Recycling Spray Booth Air compressor + three-stage oil and water filter | Epoxy polyester powder (particle size 15-45μm) High-gloss, matte, textured, and other specialty powders. |
3. High-temperature curing | goal: Completion of powder melt leveling and cross-linking curing reaction step by step: ① Rising Temperature Stage: 10℃/min to 185 ② Constant temperature curing: 185±5°C for 15 minutes. ③ Cooling stage: natural cooling to below 50°C ④ Quality inspection: hardness/adhesion/appearance inspection | Gas-fired radiant curing oven (with intelligent temperature control system) Hot air circulator temperature recorder | Natural gas/electricity (heating energy) (Note: the curing process consumes no additional material) |
4. Decorative treatment | goal: Realization of special appearance effects (wood grain/pattern/high gloss, etc.) step by step: ① Gloss Finish: Clear powder/UV coating to enhance the luster. ② Thermal transfer: Reproduction of texture by transfer film (150-200°C) ③ Water transfer: impregnation of activated film to form 3D patterns ④ Partial finishing: Hand-painted special effect coatings |
Working Principle
- Work electrostatic spraying gun or spray, spray cup partially connected to the negative pole, the workpiece is connected to the positive pole and grounded, in the high-voltage electrostatic generator under the action of high voltage, the end of the gun (or spray pan, spray cup) and the workpiece between the formation of an electrostatic constant paint particles are subject to the electric force and the static field voltage and the amount of charged particles of the paint is directly proportional to the gun and the workpiece distance is inversely proportional to the gun when the voltage is high enough to form an air ionization zone in the area near the end of the gun. When the voltage is high enough, the area near the end of the spray gun forms an air ionization zone, the air is intensely ionized and heated, so that the sharp edge of the end of the spray gun or around the pole needle to form a dark red halo, which can be clearly seen in the dark, when the air produces a strong corona discharge.
- Coatings in the film-forming materials, namely, resins and pigments, etc. Most of them are composed of polymer organic compounds, more than a conductive dielectric, solvent-based coatings in addition to film-forming materials, there are organic solvents, co-solvents, curing agents, electrostatic diluents, and other types of additives and other substances. Such solvent substances in addition to benzene, xylene, solvent gasoline, etc., most of them are polar substances, low resistivity, a certain degree of conductivity, they can improve the charged properties of the coating.
- The molecular structure of the dielectric can be divided into polar molecules and non-polar molecules. Polar molecules composed of dielectrics in the applied electric field, showing the electrical properties; non-polar molecules composed of dielectrics in the applied electric field, showing the electrode, so that the external conductive charge to produce the affinity, so that the dielectric in the applied electric field in the external surface can be locally charged.
- The paint is atomized by the nozzle and then sprayed out, the atomized paint particles are charged due to contact when they pass through the pole needle of the gun or the edge of the spray disk and spray cup, and when they pass through the gas ionization zone produced by the corona discharge, they will increase their surface charge density once again. These negatively charged paint particles under the action of the electrostatic field, to the conductivity of the workpiece surface movement, and be deposited on the surface of the workpiece to form a uniform coating film.
Advantages of Plastic Spraying
- Environmentally friendlyNo solvent volatilization, powder recycling rate >95%, in line with RoHS environmental standards.
- outstanding performance: Coating hardness up to 2H-3H, salt spray resistance > 500h, adhesion up to grade 0 (Hundred grams method).
- Significant efficiency: 60-120μm film formation in a single pass, curing in only 15-20 minutes, automated spraying efficiency increase of 40%.
- Decorative: Customizable wood/metallic/3D textures with gloss levels covering matte to mirror.
Disadvantages of spray molding
- Thickness limitation: Poor process stability for ultra-thin (200μm) coatings.
- Difficulty in changing colors: Changing colors requires thorough cleaning of equipment, increasing costs for small, multi-color orders 30%-50%.
- Substrate Limitations: Only for metal parts with temperature resistance >180°C. Plastic/wood requires special treatment.
- Higher energy consumption: Curing oven energy consumption accounted for 65% of total process power consumption, gas heating carbon emissions are 20% higher than traditional spray painting.