What is the difference between aluminum extrusion and aluminum die casting?
Date: 2025-02-25 Categories: Blog Views: 120
As a deep-rootedaluminumAs an engineer in the molding field for over 20 years, I am often askedaluminum extrusionCore differences with aluminum die casting. This article will combine high pressure/low pressure/Gravitational castingHands-on experience with systematic comparisons from material science and process principles to business decisions.
What is aluminum extrusion?
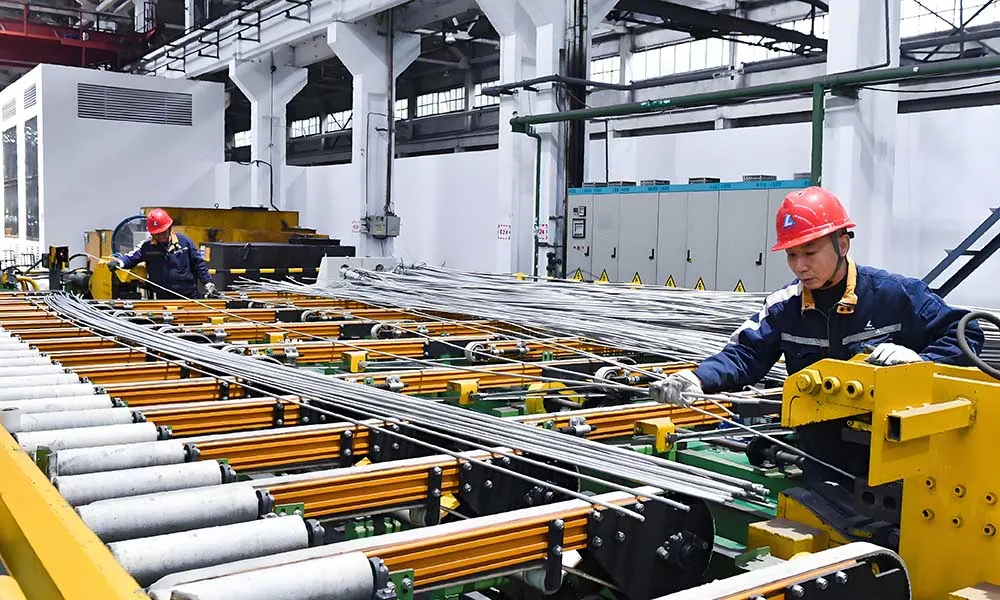
Aluminum extrusion is a solid-state process of extruding through a die and is part of theSolid State Plastic Molding, commonly used in the production of assembly line aluminum profiles, heat dissipation aluminum parts, and so on. At its core, aluminum rods heated to a plastic state (400-500°C) are fed into an extruder and forced through a die with a specific cross-sectional shape to form a continuous profile, which can be used to manufacture long-sized products such as door and window frames, guide rails and other products (longitudinal lengths of up to 10 meters or more).
Advantages of aluminum extrusion
Aluminum extrusion products have lightweight, corrosion-resistant characteristics, low tooling investment costs (about 30,000-200,000 yuan), the surface of the anodic oxidation treatment of the oxide film thickness of up to 0.012mm, presenting a bright texture, and no need for plating to meet the basic corrosion requirements. Can produce ultra-long one-piece molding structure, such as photovoltaic bracket rail (length of 12 meters, wind pressure > 3.5kPa).
Disadvantages of aluminum extrusion
The process is prone to warping and deformation, black lines, bumps and other surface defects, unoxidized aluminum still exists in the risk of rust, longitudinal strength is only 60%-70% of iron products. anodic oxidation layer of abrasion resistance is weaker than the electroplating process, and the overall cost of iron products than the high 3-4 times, for example, the building curtain wall profiles processing fee of about 25 yuan / kg, while the galvanized steel is only 8 yuan / kg.
What is aluminum die casting?
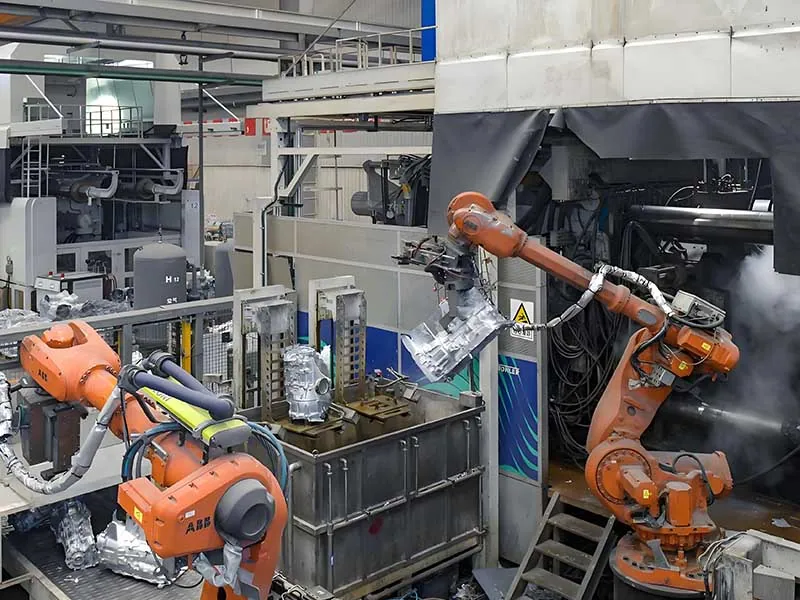
Aluminum die casting belongs toLiquid High Pressure CastingThe 680-720°C molten ADC12 alloy will be used to50-120MPaPressure injection into the steel mold, in 20-60 seconds to complete the full process of filling - solidification - demolding. Its essence is the non-equilibrium solidification process of metal under super-rapid cooling (>100℃/s). It is suitable for the production of complex thin-walled parts such as automobile parts and 3C housings, and the cycle time of a single piece can be shortened to less than 30 seconds.
Advantages of Aluminum Die Casting
The high hardness of the die casting (A380 alloy has a tensile strength of 320MPa) allows for one-piece molding of complex features such as threaded holes and reinforcement bars, eliminating the need for subsequent cutting processes. Zinc-aluminum alloy hybrid die casting can also enhance wear resistance, such as automotive transmission housing can be reduced by 60% assembly parts through this process.
Disadvantages of Aluminum Die Casting
Mold development costs are high (about 200,000-2 million yuan), and the difficulty of modifying the design errors, you need to rely on 10,000-piece orders to share the cost. For example, a new energy vehicle door lock shell die-casting mold offer of 850,000 yuan, while the injection mold only needs 150,000 yuan.
Core Differences Comparison Table
comparison dimension | aluminum extrusion | aluminum die casting |
---|---|---|
Molding Principle | Solid-state plastic deformation | Liquid High Pressure Casting |
Minimum wall thickness | ≥1.0mm | 0.5mm |
Mold cost (typical) | ¥50,000 (construction profiles) | ¥800,000 (automobile parts) |
production-ready batch | 500-50,000 pieces | >10,000 pieces |
surface treatment | Anodized (cost +15%) | Powder coating (cost +20%) |
Frequently Asked Questions (FAQ)
1. When must I choose aluminum extrusion?
- Requirement ScenariosLong-size structural parts (>5 meters), anodized parts, and small to medium-sized custom orders.
- typical case: High-speed railroad car keel (tensile strength >310MPa), outdoor billboard frame (weather-resistant life of 10 years +).
2. Why is die casting better for automotive parts?
- technology adaptability: 30% weight reduction in unibody molding (370 fewer parts in Tesla's rear chassis die casting), with mass production beats of 90 seconds per piece.
- cost threshold: When the order quantity > 50,000 pieces, die-casting unit cost is 40% lower than extrusion (Source: China Society of Automotive Engineering).
3. What is the essential difference between the surface treatment of the two processes?
- aluminum extrusion: Dependent on anodizing to form a dense aluminum oxide layer (film thickness 0.01-0.03mm), but wear resistance is only equivalent to 1/3 of hard anodizing.
- aluminum die casting: Due to surface porosity defects, electrophoretic coating (film thickness 20-30μm) or nano-ceramic coating (cost increase of 25%) is mostly used.
4. How to solve the problem of porosity in die castings?
- Process upgrades: Adopting vacuum die-casting technology (vacuum degree ≤ 50mbar), the porosity is reduced from 5% to 0.5%.
- Material optimizationHigh purity aluminum ingot (Fe content <0.15%) is used in conjunction with rare earth densifiers to enhance melt fluidity.
5. What are the future trends in technology convergence?
- Extrusion-die casting composite process: Extrusion is used to create the main bearing structure, and then complex features are die-cast locally (Toyota's new battery tray costs 18% less).
- Semi-solid molding: Aluminum paste is formed in the solid-liquid coexistence state, combining the strength of extruded parts (tensile 380 MPa) with the complexity of die castings.