The application of automotive aluminum die casting lightweight technology path and practice exploration
Date: 2025-03-04 Categories: Blog Views: 94
Author: Senior Engineer, Ningbo Hersin Molding Co., Ltd (20 years experience in casting industry)
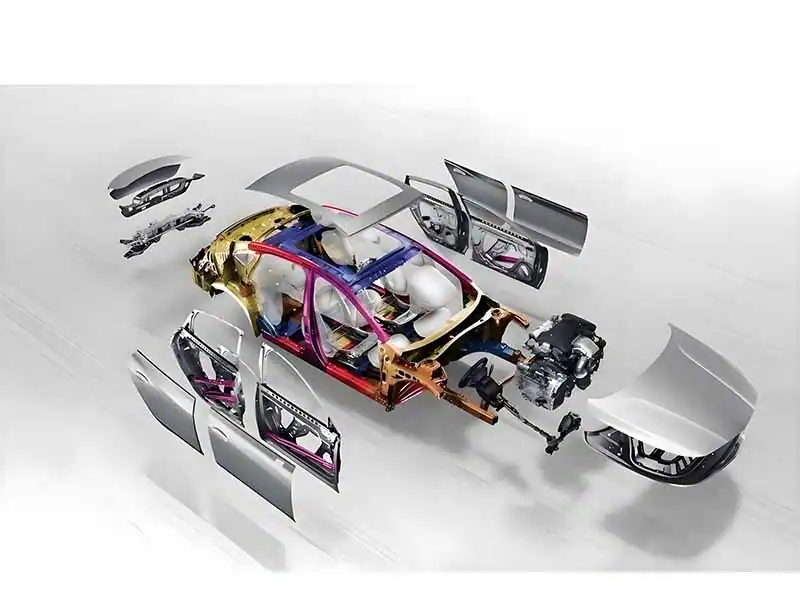
1. Strategic value of aluminum alloy materials
With the deepening of global carbon emission reduction policies, the automotive industry is undergoing a structural transformation from "steel-based" to "multi-material synergy". aluminum The material, by virtue of itsLow density propertiestogether withRecyclable AdvantageAluminum alloy die casting has become the core breakthrough in realizing the light weight of the whole vehicle. In the architecture of new energy models, aluminum alloy die casting has penetrated into the body frame, three electric systems, chassis structure and other key areas, forming a lightweight solution covering the whole body.
Current industrial practice shows that the use of modular die-casting technology can significantly reduce the number of parts and assembly complexity. Typical cases show that through the structural integration and process innovation, a model of body-in-white successfully realized material weight reduction and production line efficiency synchronization. This technology path not only responds to the demand for energy saving and emission reduction, but also creates significant economic benefits for car manufacturers.
2, aluminum die casting technology system
2.1 Comparison of mainstream processes
Process Type | Technical Advantages | Typical Application Scenarios |
---|---|---|
High Pressure Die Casting | High-precision thin-wall molding | Motor housings/gearbox components |
Low-pressure casting | Low porosity and high densification | Suspension system/wheel assembly |
Gravitational casting | Near-net-shape forming of thick-walled parts | Chassis components/steering knuckles |
pass (a bill or inspection etc)Vacuum Assisted Technologytogether withIntelligent temperature control system for moldsModern die casting processes have broken through traditional wall thickness limitations to enable more complex lightweight structural designs25.
2.2 Direction of technological innovation
- Integral molding: Consolidate multiple parts into a single component, reducing joining processes and material redundancy.
- Composite Process Development: Integrate casting and forging technology to improve the mechanical properties of key components.
- Digital Simulation: Optimize casting system design and reduce process development costs through CAE simulation.
3、Industry application practice
3.1 Structural innovations in the bodywork
All-aluminum body technology throughTopology optimization designtogether withHigh Toughness Alloys ApplicationsIn addition, the weight of the body-in-white has been significantly reduced under the premise of ensuring collision safety. Typical models have realized the proportion of aluminum die-casting parts in the car body is more than half, which significantly improves the range and handling performance.
3.2 Upgrading of the triboelectric system
Key components such as the drive motor housing are made ofThin-wall die casting solutionsThe new product is designed to meet the needs of sealing and protection while breaking through traditional weight limitations and helping to improve energy efficiency.
4. Challenges of industry chain synergistic development
technological bottleneck | Innovative Solutions | Synergies |
---|---|---|
Oversized member deformation control | Development of a multi-dimensional compensation mold system | Improved stability of dimensional accuracy |
Material recycling rate | Construction of an integrated spectral sorting and smelting device | Reducing carbon emission targets |
process stability | Deployment of online monitoring and machine learning systems | Realize real-time defect alerts |
Leading industry players are passingIntelligent Die Casting IslandThe construction has raised the precision of process parameter control to a new order of magnitude. After the introduction of a full-process MES system at a production base, the fluctuation of key quality indicators narrowed significantly.
5. Future direction of technological evolution
- Ultra-large die-casting equipment: Promote the popularization of modular production of front pods/rear sumps.
- digital twin: Build virtual debugging platform to shorten new product development cycle.
- Low Carbon Preparation Systems: Improving the recycled aluminum supply chain to achieve green manufacturing.
Current technological breakthroughs have extended toMaterial-Process-Equipment Co-InnovationAt the level of a new die-casting production line, a new type of energy recovery system, successfully reduced the unit energy consumption to the industry's advanced level.
concluding remarks
Automotive aluminum die casting lightweight has developed from local substitution to systematic engineering solutions. As a casting enterprise with the ability to serve the whole industry chain, we will continue to plowingMaterial modification.process integrationtogether withintelligent manufacturingfield, providing technical support for the green transformation of the global automotive industry.