Low-pressure casting machine operation specification
Date: 2025-02-26 Categories: Blog Views: 3712
In today's era of rapid manufacturing growth, theLow-pressure castingTechnology has become one of the core processes in the production of high-end metal parts. The excellent performance of the equipment can not be separated from standardized operation and fine management. This operation specification is based onImprovement of yield rate and production safetyCombining years of practical experience with the latest process standards, this guide systematically organizes the operating points of the whole chain from daily start-up, production process to equipment maintenance. Whether you are new to this equipment or a technician wishing to optimize the production process, this guide provides you with a clear and practical reference basis.
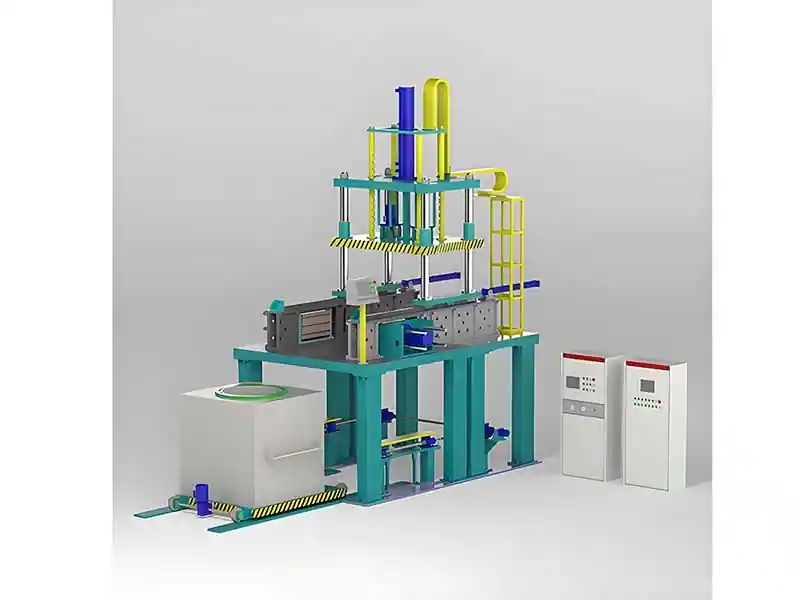
Daily startup and production
- security protection::
- Wear coveralls, safety shoes, gloves and safety glasses.
- Checking and Setting::
- Check the main control for alarms and replace the thermocouple if there is a thermocouple failure alarm.
- Check the temperature display on the main control cabinet (it should be 950°C when idle), and the two thermocouple temperatures show no more than 10°C difference.
- Set the operating and safety regulator temperatures to the operating temperature.
- Molten metal inspection in the furnace::
- Check the molten metal in the furnace, the height of the liquid level should be about 20mm from the top of the slag to the furnace cover, add copper ingots when the liquid level is low (do not add more than 20KG each time).
- Ascending Tube Inspection and Preparation::
- Check that the lift tube is not cracked, that it is clean and well coated, and that it is completely dry and preheated on the furnace.
- Remove the ascending tube cap.
- Remove the slag from the ascending tube position or push it around.
- Place a graphite coated asbestos washer in the ascending tube position.
- Install the lift tube and tighten.
- Heating and Startup::
- Turn on the gas, light the heating ring and turn on the compressed air.
- Heat the ascending tube to an orange color.
- Turn on the hydraulic and graphite tank pumps at the main control cabinet.
- Inspect the mold, clean and preheat the mold if necessary.
- Mold dipped graphite.
- Check the temperature of the mold, the temperature should be 110℃-120℃ during production.
- Inspection during heating::
- Remove the thermocouple and clean it with a steel brush.
- Graphite concentration was checked with a centrifuge.
- Check casting parameters.
- Observe the basement and check the water lines, screws and exhaust lines to make sure everything is in order.
- Prepare for production::
- When the lift tube and mold reach the desired temperature, clean the lift tube.
- Retighten the ascending tube slowly.
- After doing the above preparations can start production, pouring the first mold without pressure test pouring, pouring should be especially careful, once found problems immediately stop.
Routine operations during production
- Clean out the liter tube every 30 minutes if necessary.
- Use a steel brush to clean the inner cavities and sprue of the mold if necessary.
- expense or outlaysandblastThe mold is cleaned by a machine (the cleaning interval is about 30 molds, and the number of times of cleaning is increased in case the mold is very dirty).
- Inspect castings for defects as constantly as possible.
- The temperature of graphite water should be controlled at 30-60℃, and the height of graphite water should be 10-15mm higher than the back of the immersed mold.
Daily closure
- Setting Temperature & Cleanup::
- Set the operating and safety regulator temperature to 950°C.
- Clean the mold and close the pouring valve.
- Close and Remove::
- Turn off compressed air and gas to the lift tube heating ring.
- Loosen the lift tube and remove and de-gasket.
- Elevate the liquid tube cap.
- Loosen the filler tube.
- Furnace metal and lid handling::
- Strip the slag from the molten metal, retaining about 20mm as insulation.
- Add copper ingots to improve the liquid level, slightly below the normal level (20mm from the furnace cover) can be, pay attention to each time to add the best not to exceed 20Kg.
- Clean around the furnace cover charge tube and install the charge tube.
- Clearance and closure::
- Clean the thermocouple with a steel brush.
- Remove unused items from the oven lid.
- Shut off the hydraulic pump and the graphite cell pump.
- Clean up around the machine.
- Turn off the air supply and vacuum cleaner.
Key operations and parameters to maintain casting yields
Do daily polishing experiments to confirm the material.
Effective cleanup::
Effective mold cleaning (including sandblaster cleaning, brushing or scraping with steel brushes, etc.).
Effective liter tube cleaning.
Charging and handling::
Effective spiking.
Continuous uninterrupted operation.
Temperature and altitude::
Correct mold temperature (120°C).
Suitable graphite water height (10~15mm above the immersion mold).
Graphite water concentration and cleanliness::
Suitable graphite water concentration (12-20% depending on the size of the mold).
Clean graphite water (no grit, oil, etc.) is typically filtered once a week and the graphite is replaced every 600 hours.
Temperature and metal specifications::
Suitable graphite water temperature (30°C-60°C).
Correct metal fluid temperature (995°C - 1010°C).
Correct metal specification.
Other key parameters::
B is added without hard spots (if grain treatment is not done in the copper ingot) to improve fluidity and to obtain a good grain structure, reduce shrinkage and cracks.
Fe and Sn shall be less than 0.21 TP3T (Fe, Sn shall both be less than 0.21 TP3T).
Al content of 0.61 TP3T minimum.
The distance from the metal slag to the bottom of the lid is 20-40 mm.
Observe that the casting height and riser height become smaller, and increase the pressure when appropriate.
Frequently Asked Questions (FAQ)
How should the mold temperature be set under the new 2025 standard? What are the differences from the old version?
- New National Standard Requirements: Mold temperature should be strictly controlled at110℃-120℃(Older versions allow ±15°C fluctuation), with AI temperature control module for real-time calibration.
- Exception handling: If the temperature is out of tolerance, check the thermocouple contact points as a matter of priority and clean up graphite residue on the mold surface (the temperature control failure on the 80% originated here).
What is the temperature at which an ascending tube is heated to "orange"? How can I avoid cracking?
- If the heating does not change color for more than 5 minutes, check whether the gas pressure is ≥0.2MPa.
- Anti-Cracking Essentials::
- Before daily use withSteel brush cleaning of oxidized layer
- Mandatory replacement when coating wear rate >30%
How can I reduce my monthly gas consumption costs?
Measured data for 2025 suggests that savings could be realized by adopting the following scenarios23% Energy consumption::
- preheating phase: Pre-heating of copper ingots with waste heat recovery unit (reduction of gas consumption by 15%)
- production stage: Enable Dynamic Pressure Mode (refer to Chapter 6, "Energy Savings Parameter Package")
- decommissioning stage: Liquid level is lowered to a distance of40mm(retains 20mm more insulation than the old standard)