Low Pressure Die Casting Principles and Applications
Date: 2025-01-07 Categories: Blog Views: 4427
What is low pressure die casting?
Aluminum low pressure die casting (LPDC) is to make liquid metal under pressure to complete the filling cavity and solidification process two get castings of a casting method. Because there is a certain pressure but much lower than High Pressure Die Casting The pressure (the highest pressure is only 1% for high-pressure die casting), low-pressure die casting pressure range in (20 ~ 60kPa), because of its role in the pressure is small and slow, but also be able to manufacture a more complex internal hollow products (hollow part of the need for the sand core and then subsequently remove it so called low-pressure sand casting), the principle of its role is more close to the aluminum casting, and therefore also known as the aluminum low-pressure casting.
Low pressure die casting processThe molten aluminum liquid enters the cavity smoothly through the mold gate along the rising liquid pipe (the pipe in the middle of the crucible) under the action of gas pressure in the impermeable crucible, keeps the gas pressure on the liquid surface of the crucible, maintains the pressure for a certain period of time, and so on, and the products in the cavity of the low-pressure mold solidify, and then lifts the gas pressure on the liquid surface of the crucible, and the unsolidified metal in the rising liquid pipe flows back to the crucible through the crucible, and the liquid flows back to the crucible through the crucible. The liquid flows back to the crucible, and then the product is solidified in the low-pressure mold cavity by Low-pressure casting The machine opens the mold to take out the low-pressure aluminum casting. Since the casting direction of low-pressure casting is inverse Gravitational casting Also known as anti-gravity low pressure casting.
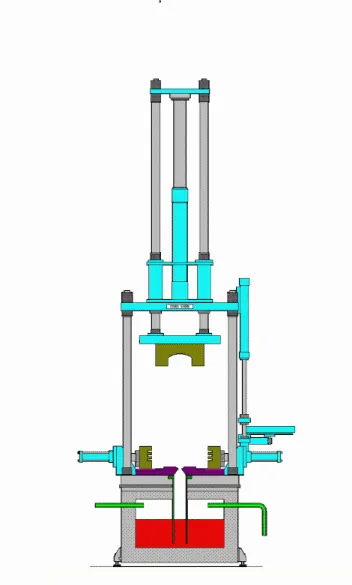
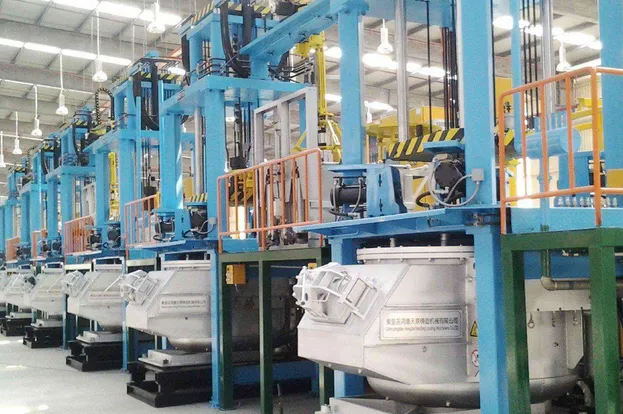
History of Low Pressure Casting
At the beginning of the twentieth century, there were already countries that started to study the low-pressure casting process one after another, and E.H. Lake of the United Kingdom was the first one to register a report about the aluminum Low-pressure casting patent company, the French first in the aluminum alloy casting production promotion and use.
After the outbreak of the Second World War, aviation military industry and other manufacturing industries have further development, should be widely used in the low-pressure casting process for high-demand aircraft engine system aluminum alloy parts, mass production of aluminum alloy castings, North America the use of low-pressure aluminum alloy casting technology is widely used in automotive parts, motor shell and other castings manufacturing. In this way, the low pressure casting process quickly spread to the field of general machinery, textile machinery, instruments and commercial products.
China began to study low-pressure casting from the 1950s, but the development has been relatively slow. With the development of the automobile industry, and the adoption of a large number of new technologies, at the end of the last century and the beginning of this century, low-pressure casting in China has been the rapid development of domestic low-pressure casting machine function and performance, and the use of the stability and reliability of the machine has been close to or reached the international advanced level, is used in a large number of automobile wheel hubs, automobile cylinder heads and other castings production.
Low pressure die casting mold material selection
Low pressure die casting mold is also known as low pressure permanent mold, the use of metal cavity manufacturing molds, can be used to turn the sand mold (ductile iron), mold steel mold (p20, #45, H13 and other heat-resistant mold steel), production. Different molds have different mold life, ordinary sand mold life is about 2000-5000 mold, modulation of #45 life can be done 5000-10000 + mold, ordinary have done a vacuum heat treatment of h13 can reach 30000 mold life. The better ones can even reach 50,000 molds or even 100,000 molds.
Advantages and disadvantages of low pressure die casting
Advantages of low-pressure casting
- 1, low pressure die casting aluminum liquid flow speed is slow, less debris involved, by changing the pressure speed, melt soup by laminar flow filling.
- 2, the use of bottom injection type filling, metal liquid filling stable, no splash phenomenon, can avoid the involvement of gas and mold wall and core erosion, the adoption of improved casting pass rate.
- 3, the aluminum alloy products produced by the low-pressure die-casting machine manufacturers crystallize under pressure, the low-pressure die-casting products have dense organization, clear outline, smooth surface, high mechanical properties, which is particularly advantageous for the casting of large thin-walled parts.
- 4, can change the pressure speed of low pressure casting process, melt soup by laminar flow filling.
- 5, low-pressure aluminum casting materials are widely used.
Disadvantages of low pressure die casting
- 1, low production efficiency, more gravity die casting, high pressure die casting compared. High-pressure die casting > gravity die casting > low-pressure die casting
- 2. Long casting cycle, poor productivity. In order to maintain directional solidification and molten soup mobility, the mold temperature is high and the solidification speed is slow.
- 3, close to the gate low pressure die casting aluminum organization is coarse, the mechanical properties of the lower surface is not high, need a comprehensive and close management (temperature, pressure, etc.).
- 4. High mold cost.Low pressure casting mold For metal mold life non sand casting One-time casting, known as "low-pressure permanent mold casting."
- 5, equipment costs are high. Low-pressure casting machine prices relative to the gravity casting machine, sand casting is not a small investment.
Low pressure cast aluminum material selection
Low pressure casting is mainly used in the field of non-ferrous alloy casting, common aluminum alloy, magnesium alloy and other light alloy castings. One of the most widely used aluminum alloy, usually we speak of low pressure die casting refers to aluminum alloy low pressure casting. Common aluminum alloy materials are.
- aluminum-silicon alloy: Aluminum-silicon alloy containing silicon about 11%, plus a small amount of copper, iron, nickel enhancement degree, commonly used in low-pressure casting.
- aluminum-copper alloy: A relatively hard aluminum alloy, aluminum-copper alloy containing copper 3%, is the earliest cast aluminum. High mechanical properties at room temperature and high temperature, easy casting, good cutting, excellent heat resistance.
- Aluminum-magnesium alloy:High strength, high hardness and good heat resistance make it superior for manufacturing high quality parts. Its excellent weldability and corrosion resistance make it suitable for manufacturing parts that require high color and surface quality.
- Aluminum-magnesium-silicon alloy:With high strength, high stiffness, excellent heat resistance and mechanical properties, it is an ideal material for manufacturing high-quality parts and industrial equipment. It is widely used in low-pressure casting, and A380 and A356 aluminum alloys are especially common in low-pressure casting.
Scope of Application
The application range of low pressure casting is quite wide, especially suitable for areas with high requirements for casting quality. Especially in China, where the manufacturing industry is developed, in order to provide customers with more cheap and easy to use aluminum alloy castings, OEM, ODM, batch customized aluminum alloy products. Aluminum low pressure foundries apply it to:

Try HeXin now!
- automobile industryIn the automotive industry, low-pressure casting of wheel hubs, cylinder blocks, cylinder heads, pistons and gearbox housings are required to withstand high temperatures and high pressures, and low-pressure casting ensures that the parts are dense and have good performance.
- aerospace: The castings are resistant to extreme environments and low-pressure die casting of high-precision aluminum alloys and magnesium alloys for engine components and airframe structures.
- machinery manufacturingThe company produces a wide range of complex mechanical parts and components, such as gears, bearing housings, pump bodies, and so on.
- electrical and electronic equipment: Production of components such as radiators and motor housings.
Frequently Asked Questions (FAQs)
What is the difference between aluminum low pressure die casting and high pressure die casting?
Aluminum low pressure die casting is a slow casting method, and high pressure die casting is a high-speed high pressure casting method, although it is a form of pressure casting, but high pressure die casting products are more brittle, low pressure casting product performance closer to gravity casting (low pressure die casting is also known as anti-gravity casting) can also be heat treatment, aluminum should be more extensive. High pressure die casting production efficiency is high, the speed is fast, low pressure casting efficiency is relatively low and slow.
Is low pressure die casting suitable for mass production?
Suitable, although the low pressure die casting efficiency is relatively low but also can reach (24 hours 200-300 mold), much higher than sand casting, high degree of automation, high use of aluminum, high product stability.
Compared with gravity casting low-pressure casting product qualification rate is higher?
Yes, although it is called low-pressure die casting, its flow rate is slow and the pressure is small, which is closer to gravity casting, but its degree of automation is high, and the pressure (20~60kPa) is lower than die casting but greater than gravity, so the product production is more stable.