High pressure casting Die casting machine tonnage selection
Date: 2024-08-03 Categories: Blog Views: 2132
These days a customer asked me how to choose the right die-casting tonnage is not die-casting tonnage is the bigger the better, so write this article slightly explaineddie casting moldSelection of tonnage. Picture High pressure casting is a kind of pressure casting, in the case of high speed and high pressure liquid through the pressure chamber, by the die casting machine hammer into the mold internal molding, die casting machine tonnage the greater the pressure is mainly reflected in the clamping force, and die casting hammer. So how to judge the die casting products need the size of the tonnage?
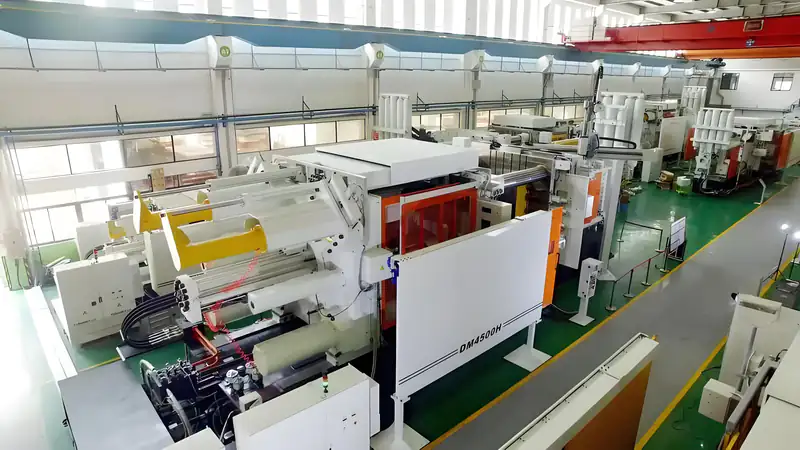
How to CalculateHigh Pressure Die CastingTonnage, here we consider four main aspects.
1, Calibration of die casting products clamping force
What is clamping force?
Clamping force refers to, high pressure die casting products in the casting process, the molten metal liquid with high pressure into the mold cavity will produce a force to support the mold, this time the high pressure die casting machine exerted to the mold locking force, to prevent the die casting machine because of the force is not enough and open, this force is called clamping force.
Clamping force formula.
Clamping force = K × (Ff + Ffa)
Among them, K for the safety factor, generally take 1 ~ 1.3, wall thin complex parts take large value; Ff for the die casting counterpressure, and the die casting machine injection ratio pressure and projection area; Ffa for the transverse core pulling when the action of the slider purification tight surface of the normal counterpressure.
Alternatively, clamping force = actual projected area of the part × specific pressure × safety factor K/1000 + number of side cores N × projected surface area of the side cores × tan(angle of the miter wedge) × specific pressure
This formula takes into account the effect of side core withdrawal on clamping force and introduces parameters such as specific pressure and safety factor.
2, Calibration fullness
What is fullness?
Fullness refers to the aluminum high pressure die casting die in the production of aluminum high pressure die casting, the volume of metal liquid in the pressure chamber accounted for the proportion of the volume of the pressure chamber. In the case of the size of the press is unchanged high pressure die casting the larger, the higher the degree of filling.
Influence of fullness on high pressure die casting.
Too full.
- Mould damage: Excessive filling may cause the mold to be overstressed, resulting in damage to the mold and increased production costs.
- Liquid metal overflow: Too much filling may also lead to the liquid metal overflow mold in the die casting process, resulting in material waste and environmental pollution.
- Unstable casting quality: Excessive filling degree may lead to casting quality instability, such as increased casting dimensional deviation and uneven internal organization.
Filling level too low
- Casting surface defects: Underfilling will lead to defects such as porosity, inclusions, cracks and other defects on the surface of the casting, reducing the surface quality of the casting, thus affecting the appearance and service life of the casting.
- Internal defects in castings: The underfilling may also lead to defects such as porosity, inclusions, cold segregation, etc. These internal defects will reduce the mechanical properties of the casting, such as strength, toughness, etc., thus affecting the service life of the casting.
- Thermal balance of the mold is affected: For horizontal cold chamber die casting machine, insufficient filling also affects the thermal balance of the mold, which may lead to mold temperature fluctuations, which in turn affects the solidification and shrinkage of the castings and reduces the dimensional accuracy of the castings.
Fullness formula.
Aluminum high-pressure die casting suppliers are aware of the quality of the liquid metal in the chamber when it is fully filled.:
textDegree of filling = (mass of casting metal liquid / mass of metal liquid in the press chamber when it is completely filled mass of casting metal liquid) × 100%
Among them:
- The quality of the casting liquid metal (mj): The quality of the metal fluid actually injected into the pressure chamber.
- Mass of liquid metal when the chamber is completely filled (mym): The mass of metallic fluid in the fully filled state of a finger pressure chamber.
Equation 2 (calculations based on pressure chamber dimensions and density of the metallic fluid):
textFullness = (4Gm/πρmLD²)×100%
Among them:
- Gm: Mass of the casting metal liquid (g).
- ρm: Density of the metallic liquid (g/cm³).
- L: Pressure chamber length (mm)
- D: Pressure chamber diameter (mm)
This formula calculates the degree of filling from the dimensions of the pressure chamber and the density of the metal fluid, which is more direct and practical.
3, Calibrate mold dimensions
The casting for a simple mold layout, know its mold size . According to the mold dimensions to verify the selected die casting machine golin column distance is appropriate Finally determine the use of die casting machine tonnage So how to reasonably select the tonnage of the press it:.
- 1, the calculated clamping force must be less than the size of the nominal clamping force of the die casting machine
- 3, the calculated mold opening force and pushing force should be less than the selected die casting machine maximum opening force and pushing force,
- 2、Calculation of the pressure chamber capacity should be less than the nominal pressure chamber capacity of the die-casting machine
- 4, the total thickness of the mold should be greater than the minimum closing distance of the die casting machine
- 5, die casting maximum opening distance should be greater than the total thickness of the mold and the product height sum
- 6, the mold is installed in the die-casting machine template size and hole position should be compatible with the die-casting machine fixed plate size and hole position
- 7, mold external dimensions and out of the mold body of the maximum size of the external mechanism should not touch with the die casting machine tie rod, otherwise it will affect the normal operation of the die casting machine and the use of a. Determine the clamping force of die casting machine - - calculate the clamping force - - safety coefficient - - ejection pressure - - projected area The safety coefficient K and the complexity of castings as well as the die casting process and other factors, generally take 1-1.3 for thin-walled complex casting, because of the For thin-walled complex castings, due to the use of higher injection speed, injection pressure and mold temperature, so that the mold parting surface is subjected to a greater impact, so K should take a larger value, and vice versa take a smaller value.
4. Determine the injection volume of the machine
The shot volume is an important parameter of the die casting machine unit. It is the most permanent parameter when choosing a die casting machine, expressed in kilograms. Select a sufficient shot volume of die casting machine - should not choose the shot volume just equal to the weight of the die casting blank die casting machine. The usual choice is the weight of the die casting blank should account for the shot material volume of 25% --- 85% is appropriate. Three to determine the projection area of the parts projection area is an important parameter of die casting model selection, the projection area is not only the area of the parts, including the area of the garbage and the water outlet. Estimation of the area of the general clamping force divided by the die casting of the injection ratio pressure. For the existing beer parts, casting area calculation should be divided into small regular shape calculation.
- (1) Calculation of s for the area of a circle with a diameter of d: s = Лd2/4
- (2) Calculation of the area s of a square with side a: s = a2
- (3) Calculation of the area s of a rectangle of length a and width b: s = ab
- (4), the upper base is a, the lower base is b, the height h for the trapezoid area s calculation: s = (a b) h / 2