High Pressure Die Casting Principle Advantages and Disadvantages, Applications and Services
Date: 2024-12-13 Categories: Blog Views: 4361
What is high pressure die casting?
Principle of High Pressure Casting:High Pressure Die Casting(HPDC) refers to a casting process for the production of metal products, the principle of the process is to melt the metal solution at high temperatures through the hopper will be melted metal liquid poured into the die casting machine injection pipeline, in the piston or plunger in the hydraulic pressure or pressurized gas push forward. Make the melted metal liquid filleddie casting moldCavity, molding and solidification under the action of pressure and obtain castings, followed by die casting machine under the action of the cylinder to open the high-pressure die casting mold, aluminum die casting parts out, this process is called high-pressure die casting. As shown in the following diagram of the die casting machine production moving picture.
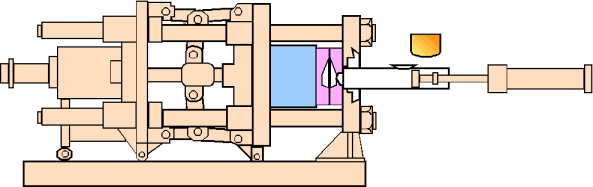
High pressure die casting process characteristics
- oppressive: the metal liquid is under pressure to fill the cavity, and in the higher pressure crystallization solidification, common pressure for 15-100Mpa. part of even able to reach 200Mpa. so the high pressure die casting pressure range is relatively large.
- high speed: The liquid metal fills the cavity at high speeds, usually between 10 and 50 m/s, and in some cases more than 80 m/s (the linear velocity introduced into the cavity through the inner gate - the inner gate speed), so that the filling time of the liquid metal is extremely short (about 0.01-0.2 seconds) and the cavity can be filled.
- highly accurate: Due to high speed and high pressure, the molds can only use high strength thermoforming mold steel, high precision molds, high precision products, smooth product surface.
oppressiveDie castingPros and Cons:
oppressiveDie castingPros.
1, castings of high dimensional accuracy; surface finish is good, generally equivalent to 5 ~ 8 level.
2、Higher strength and hardness, strength is generally higher than sand casting 25~30%.
3, dimensional stability, good interchangeability, can die casting thin-walled complex castings.
4, machine productivity is high, such as domestic J Ⅲ 3 horizontal cold air die casting machine average eight hours can die casting 600 ~ 700 times, small hot chamber die casting machine average every eight hours can die casting 3,000 ~ 7,000 times
5, die-casting long life, a die-casting type, die-casting bell alloy, life up to hundreds of thousands of times, or even millions of times; easy to realize mechanization and automation.
6, die casting size precision high, the table flood clean and other advantages. Generally no longer be machined and used directly, or processing is very small, so both improve the utilization of metal, but also reduces a large number of processing equipment and man-hours.
oppressiveDie castingDisadvantages.
1, die-casting due to the liquid metal filling cavity speed is high, the flow state is not stable, so the use of general die-casting method, the casting inside easy to produce porosity, elongation is not good, can not be heat treatment.
2, on the inner concave and convex complex castings die casting difficulties. High pressure die casting defects are more.
3, not suitable for small batch production, the reason is the high cost of manufacturing die-casting type, die-casting production efficiency, small batch production is not economic.
4. High cost of equipment and molds.
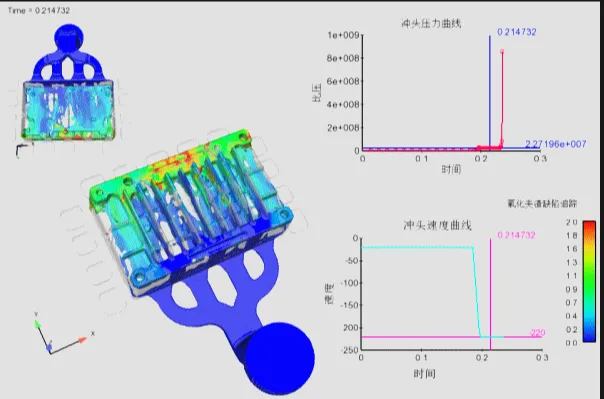
What metals can be die cast?
- 1.Zinc alloy die-casting :Zinc alloy has the advantages of better mobility, strength and so on, the appearance of the product die-casting out of the better, the surface of the less rolled up polished plating has a better appearance, commonly used in the production of appearance of the manufacturing of parts, common Zamak 2, Zamak 5, etc., more different alloy composition, zinc alloys have different mechanical properties.
- 2.aluminumDie casting :Aluminum is the most common alloying element for die casting metals, and its alloys are made by adding iron. Aluminum. Silicon. Copper and other elements to change the mechanical properties of the material, fluidity, commonly used in the manufacture of complex precision parts, aluminum high-pressure die casting widely used in the automotive industry, mechanical equipment, with light weight, dimensional stability, corrosion resistance, thermal conductivity and other advantages, common high-pressure die casting aluminum alloy a360, a380, adc12 and so on.
- 3. Magnesium alloy die casting :Magnesium alloys are not only lighter than aluminum, they are also easier to work with, making them ideal for objects that require additional machining or surface finishing after casting. Die cast magnesium alloys are easier to cast and are usually hot die cast. Widely used in powertrain components, mechanical parts and automotive parts. Common ones are AZ91D, AM60.
- 4. Copper alloy die casting :Copper alloy can also be cast by die-casting, but because of its high melting point, usually lower life, but because of this metal property of copper, some products have to use copper alloy manufacturing, so the use of die-casting process greatly reduces the production cost.
- 5.Other metal die-casting :In addition to the above metals, lead alloys, tin alloys, etc. are also commonly used in die casting.
The current problems of die casting?
1. Because the alloy liquid pressed into the mold is generally in the non-vacuum conditions of rapid cooling and solidification, such as improper casting, castings are prone to porosity, water lines and other defects.
2. Die castings produced by ordinary methods cannot be heat-treated and welded at high temperatures.
3. At present, die-casting certain concave parts, high melting point alloy castings are still difficult.
4. Die-casting equipment price is high, mold manufacturing needs a certain period, so it is not suitable for single piece or small batch production. Only in mass production, there are good economic benefits.
How is the high pressure die casting production process?
- 1. Selection of materials:Choose the metal material that meets the customer's product requirements.
- 2. Melting and pouring:The selected alloy material is melted in a crucible and introduced into the mold through a hopper.
- 3. Die-casting molding: Under pressure, the melted alloy liquid is filled into the mold cavity.
- 4. Cooling and demolding:The mold is lowered to a certain temperature by air/water cooling, the product is cooled and solidified, the mold is opened and the product is removed.
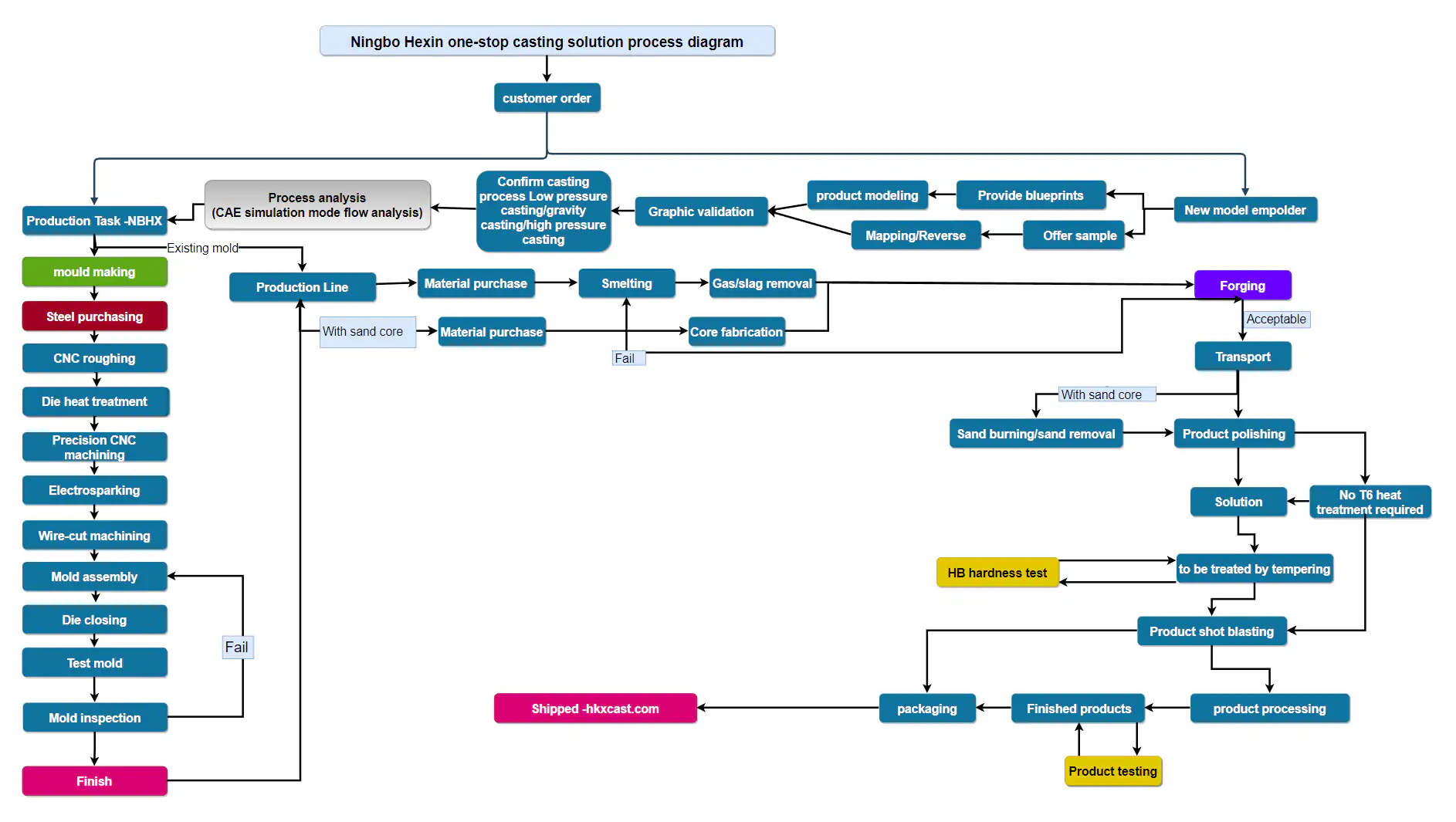
Types of Die Casting Equipment
According to the temperature state can be divided into cold chamber die casting machine and hot chamber die casting machine.
- Cold chamber die casting machine:Cold chamber die casting machine means that the chamber and the furnace are separate.
- Hot chamber die casting machine:Metal melting, holding and ejection units are integrated into the die casting machine.
According to the way of placing can be divided into horizontal die casting machine, vertical die casting machine and full vertical die casting machine.
- Horizontal cold chamber die casting machine:Die casting machines with horizontally placed chambers, produced by horizontal casting.
- Vertical cold chamber die casting machine: The chamber is placed vertically and the ejector head moves vertically, but the clamping device is still horizontally distributed.
- Full vertical cold chamber die casting machine: The press chamber is placed vertically, the ejection punch moves vertically, and the clamping device is also vertically distributed.
Application of high pressure die casting process
1. Automobile Industry
Die casting products in automobile manufacturing occupies an important position, widely used in the manufacture of various parts and components production including engine parts (such as cylinder block, cylinder head, crankcase, etc.), transmission system parts, chassis parts and so on. Aluminum alloy die casting accounted for the whole car casting 30% above.
2. Electronic product
Die casting products are commonly used in the manufacture of electronic product shells, such as cell phones, computers, flat-panel TVs and so on. These products have high requirements for the appearance quality, structural strength and heat dissipation performance of die castings.
3. Furniture
Die casting products are also widely used in furniture products, such as refrigerators, color TVs, washing machines, air conditioners and other products shell and parts. These products on the die casting of corrosion resistance and aesthetics have certain requirements.
4. Machinery and equipment
Die casting products play an important role in a variety of industrial equipment, such as machine tools, pumps and valves, pressure vessels and so on. These equipments have high requirements on the strength and precision of die castings.

Try HeXin now!
China Aluminum Die Casting Factory Contact.
Die casting dozens from now on has more than 200 years of history, China zhejiang ningbo he xin is a focus on aluminum alloy casting industry to provide OEM aluminum alloy products supplier. There are independent mold workshop, product production workshop, can provide customers with high-pressure die-casting molds, high-pressure aluminum die casting product solutions. We have decades of production experience to avoid the production defects of die casting.