Heat Treatment of Aluminum and Aluminum Alloys - Solutions
Date: 2024-08-30 Categories: Blog Views: 2004
Ningbo Hersin in on aluminum andaluminumWhen carrying out heat treatment, it is vital to recognize the current problems faced and why it is important to keep a tight rein on process fluctuations and equipment deviations. In order to provide assistance to colleagues in the heat treatment field, Ningbo Hersin has summarized and categorized the most commonly encountered process problems and put forward a number of targeted suggestions for solving them. Next, these topics will be discussed in more depth.
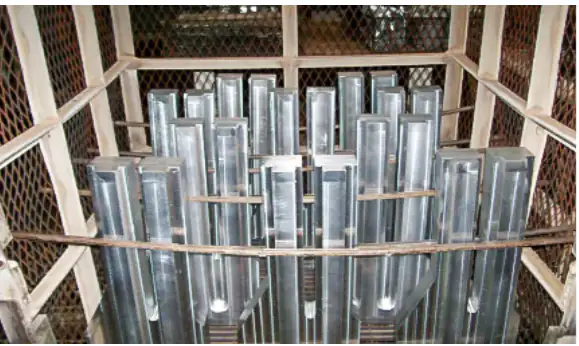
Heat Treatment Related Issues
For heat treatment of aluminum, the most reported problems include:
1) Wrong placement of parts
Incorrect Placement - At higher temperatures during solid solution the product is less rigid and is easily deformed by gravity. Correct placement (Figure 1) can avoid these problems.
seek1. Correct parts placement
2) Heating up/warming up too fast-This can cause thermal distortion and should be prevented. Correct placement of the parts will help to heat them evenly.
3) Higher than expected residual stress levels--Heat treatments not only change mechanical properties, but also directly affect residual stress levels.
The following are some possible causes: a large difference in cooling rates between the surface and the interior during quenching (including when the casting is cooled after solidification); an inappropriate rate of temperature rise; temperature changes occurring in intermediate steps; and so on.
Residual stresses are related to factors such as (large) differences in cooling rates, cross-section thickness of the part, sudden changes in cross-section dimensions, and strength of the material. It must be remembered that the stresses induced by quenching are much greater than those induced by other processes, including casting.
4) Fluctuation in time/temperature/quenching parameters--They will lead to deviations in mechanical and/or physical properties between parts and between batches.
Causes include too long a part transfer time, improper hardening (too slow), overheating, underheating, or changes in time-temperature parameters during the precipitation hardening process. For example, larger particles (precipitates) are precipitated in the case of too much time and too high a temperature.
5) Excessive heating--This is when incipient or eutectic melting tends to occur. As an example, solid solution heat treatments are performed at temperatures close to the melting point of many aluminum alloys (especially the 2xxx series, which is often only a few degrees below their melting point). Appropriate temperatures are required to promote the dissolution of solid alloying elements.
6) Insufficient heating--This results in a loss of mechanical properties due to insufficient supersaturation. If the aging temperature is too low and/or the aging time is too short, the formation of the solute-atom aggregation zone (GP-zone) is not easily achieved, resulting in low strength after aging.
7) Insufficient quenching causes deformation--The problem/difficulty in this area is the movement of the part into the quenchant, especially when manual quenching must be employed.
The part must enter the quenchant smoothly. In heat treaters' jargon, avoid "slapping" the part against the quenchant. Uniform heat transfer throughout the part prevents cooling differences and strain differences.
Changes in heat transfer in the horizontal direction are usually more unfavorable than changes in the vertical direction. It is important to keep the quenchant at the proper temperature, to control its warming, to ensure that it flows uniformly, to select the most suitable quenchant (e.g., air, water, or polymer), and so on.
For example, the cooling rate of the polymer can be adjusted for a specific application by varying the concentration, temperature and intensity of stirring to ensure uniform heat transfer and quenching rate during the boiling phase of the nucleus. Maintenance of the quenchant is also important. For parts with complex shapes, such as forgings, castings, impact extrusions and parts made with thin plates, lower quench rates can be used to improve deformation behavior.
8) Surface peeling/high temperature oxidation--We discuss this issue in detail in "High Temperature Oxidation - A Case Study".
9) Excessive statute of limitations--This may cause a loss of mechanical properties. If the aging temperature is too high and/or the aging time is too long, the critical nucleus size of the precipitated phase in the supersaturated solid solution increases, resulting in a lower strength index after aging.
10) Inadequate statute of limitations--This may also cause loss of mechanical properties.
11) Improper natural limitation--The length of natural aging varies from about 5 days for alloys in the 2xxx series to about 30 days for other alloys. 6xxx and 7xxx series are less stable at room temperature, and changes in mechanical properties can persist for many years.
There are some alloys for which natural aging is inhibited or delayed for several days after cryogenic treatment at or below -18°C (-1˚F).
It is common practice that forming, straightening and stamping have been completed before the material properties are changed by aging. For example, cryogenic treatment is a measure often taken by 2014-T4 rivets to maintain good riveting properties.
12) Improper artificial limitation--Artificial aging (also known as precipitation heat treatment) is a longer, lower temperature process. Temperature control is critical and temperature uniformity of ±6˚C (±10˚F) must be strictly guaranteed. The optimum target for temperature uniformity should be ±4˚C (±7˚F).
13) Insufficient holding time- - The consequence is that the desired mechanical properties are not achieved. Too short a time leads to insufficient supersaturation, while too long a time tends to deform the part.
14) Poor temperature uniformity--This can result in mechanical properties not being achieved or even altered. Typical requirements for process temperature uniformity are ±6˚C (±10˚F), while most aerospace applications expect ±3˚C (±5˚F).
15) Improper cold working after solid solution treatment--This is usually due to a lack of understanding of the reaction of the alloy being treated. For example, cold working of a 2xxx series alloy in the quenched state will significantly increase the extent to which it reacts to subsequent precipitation treatments.
(16) Insufficient cooling rate during annealing of solution heat-treated products-The maximum cooling rate must be maintained at 20˚C (40˚F) per hour until the temperature is reduced to 290˚C (555˚F). Cooling rates below this temperature are less important.
Casting related issues
Incidentally, it should be mentioned that there are many defects in aluminum ingots in factory condition that affect subsequent heat treatment and mechanical properties, including:
1) Holes/center sparsity-Causes insufficient shrinkage, hydrogen segregation or surface oxidation (often due to air bubbles)
2) Inclusions--Casting impurities in the form of carbides, borides, oxides, etc. (due to grain refiners or air bubbles)
3) Macro or micro bias--Solute components and high hardness intermetallic compound particles and second phase particles are not evenly distributed. Proper homogenization helps to solve this problem.
4) Deformation/shrinkage--Cause of cooling-induced stress/strain
5) Thermal tearing--Mainly due to shrinkage problems
6) Rolling (thin and thick plates) or ductile (extrusions, bars and sheets) problems involved in obtaining higher mechanical properties. However, secondary heat treatment should be avoided if higher levels of performance are required.
concluding remarks
The solution to most aluminum heat treatment related problems is:
Understand what can go wrong; determine appropriate practices and steps; maintain consistency (and reproducibility) in performing those steps; monitor the process in real time whenever possible; and keep records of heat-treating furnace operations and time-temperature profiles to confirm that the intended operation is actually being performed.
Finally, ensure that appropriate test methods are used to confirm that the components meet the requirements and function reliably in actual use.
Heat treaters have known about these requirements before, but they are more critical for heat treating aluminum and aluminum alloys than in other areas.