The definitive guide to centrifugal casting technology: Principles/Processes/Industrial Applications Analysis
Date: 2025-02-23 Categories: Blog Views: 2097
What is centrifugal casting?
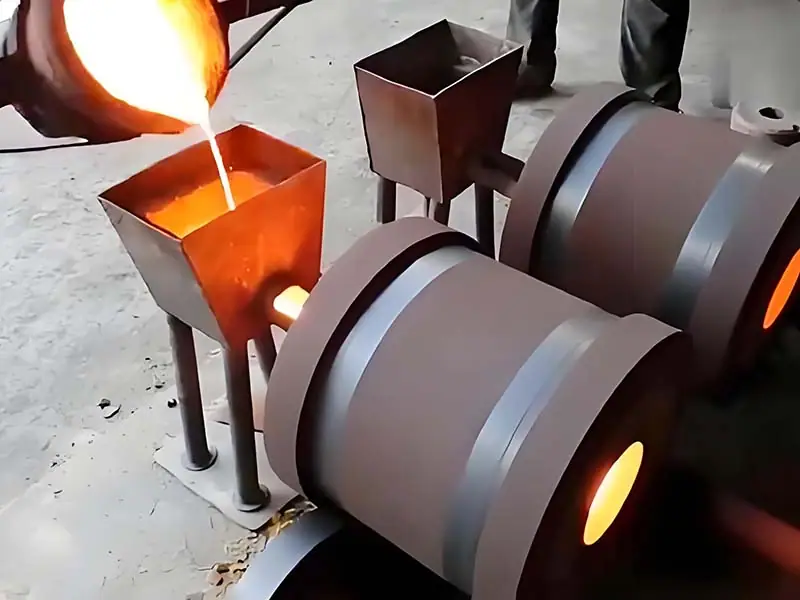
Centrifugal casting is a liquid forming process in which liquid metal is poured into a rotating mold through the centrifugal force generated by the rotating mold (up to 150 times the force of gravity) and rotated at high speeds (usually 250 to 1500 r/min) so that it fills the casting and solidifies under the action of centrifugal force to form a casting. This process is particularly suitable for the manufacture of marine engine cylinder liner, aerospace high temperature parts and other harsh working conditions products - more measured data show that centrifugal casting aluminum The tensile strength of the parts is more than 25% higher than that of traditional sand casting.
How centrifugal casting works
The centrifugal casting process begins with the injection of liquid metal into a rotating, high-temperature mold. Depending on the specific requirements of the design, the mold can be rotated vertically or horizontally.
During this process, centrifugal force distributes the liquid metal evenly within the mold at a pressure close to several times the force of gravity. This applied pressure ensures that the casting is free from cracks, as well as micro and macro defects. This is very similar to the conventional die casting process, which also applies pressure to minimize overall defects in the product.
As the mold fills, the denser liquid metal is pushed against the inner wall of the rotating mold. In addition, the dense metal solidifies directionally from the outer radial center, while the less dense materials and impurities float to the outer diameter.
Once solidification is complete, the entire part is removed from the mold and then machined to remove any impurities left around the edges of the part. The end result is a high quality material with no internal voids or bubbles.
Here are the simple steps of the basic centrifugal casting process once the mold is prepared:
- The first step, as in any casting process, is to heat the metal above its melting point.
- The second step is to rotate the mold in preparation for pouring. Typically, the rotation speed is between 300 and 3000 rpm, although the actual speed depends on the project.
- Next comes the pouring step. This process is relatively simple and requires no special preparation, but extra care is needed because the pouring takes place while the mold is rotating.
- Once the casting is complete, the next step begins automatically. The rotation not only helps the cooling process, but also generates enough pressure in the mold to ensure that no defects associated with the casting process occur.
- After cooling, the next step is similar to any other casting process. Simply remove the mold from the rotating device and remove the material from the casting.
- Finally, the final product is finished. Centrifugal rotation pushes impurities in the material to the edges, and removal of these impurities by machining results in a product of the desired quality.
Two types of centrifugal casting machines
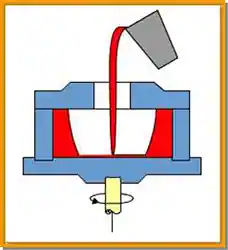
Vertical centrifugal casting

Horizontal centrifugal casting
Vertical centrifugal casting
It is mainly used for the production of circular castings with a height less than the diameter, and sometimes special-shaped castings can be poured with this centrifugal casting machine.Due to the stable installation of the vertical casting machine, not only metal molds can be used, but also non-metal molds such as sand molds and investment shells can be used.
Horizontal centrifugal casting
Mainly used for the production of sleeve and tube castings with length greater than diameter.
Three types of centrifugal casting
typology | Product Cases | Ningbo Hexin Craft Breakthrough |
---|---|---|
True Centrifugal Casting | Diesel engine cylinder liner (HT300) | Bimetallic composite casting technology |
Semi-centrifugal casting | High-speed rail brake disk (ADI material) | Graphite Cold Iron Excitation Cooling System |
centrifugation | Hydraulic valve body (ZL104) | Vacuum-assisted casting technology |
Characteristics of centrifugal casting
(1) The castings are crystallized under the action of centrifugal force, with dense organization, no defects such as shrinkage holes, shrinkage loosening, air holes, slag entrapment, etc., and good mechanical properties.
(2) When casting round hollow castings, the core and pouring system can be omitted, simplifying the process and saving metal.
(3) to facilitate the manufacture of bimetallic castings, such as steel bushings cast copper lining, the bonding surface is strong, wear-resistant, can save copper alloy.
(4) centrifugal casting rough inner surface, the size is not easy to control, need to increase the machining allowance to ensure the quality of castings, and is not suitable for the production of easy segregation of the alloy.
Advantages of centrifugal casting:
(1) When centrifugal casting is used to produce hollow rotating body castings, the core, pouring system and riser can be omitted.
(2) Due to the rotation of the liquid metal in the resulting centrifugal force, the density of the metal is pushed to the outer wall, while the density of the gas, slag to the free surface to move, the formation of directional solidification from the outside to the inside, so make up for the shrinkage of the conditions, the casting of dense organization, good mechanical properties.
(3) to facilitate the casting of "bimetallic" bushings and tiles, such as in the steel bushings cast a thin layer of copper bushings, can save the more expensive copper.
(4) Good filling capacity.
(5) Elimination and reduction of consumption in pouring systems and risers.
Disadvantages of centrifugal casting:
(1) The free surface inside the casting is rough, with large dimensional errors and poor quality.
(2) It is not suitable for alloys with large density deviation (such as lead bronze) and light alloys such as aluminum and magnesium.
Application centrifugal casting
Centrifugal casting is mainly used toMass production of pipe and tube castingsThe products can be used to produce a wide range of products, such as iron pipes, copper bushings, cylinder liners, bimetallic steel-backed copper bushings, heat-resistant steel rollers, seamless steel tube blanks, paper machine drying drums, etc., and can also be used forProduction of wheel castings, such as pump wheels and motor rotors.
Comparison of centrifugal casting and other casting processes
Casting method | sand casting | investment casting | metal molding | High Pressure Die Casting | Low-pressure casting | centrifugal casting |
Applicable metals | arbitrarily | Unrestricted, mainly cast steel | Unrestricted, mainly non-ferrous alloys | Aluminum, zinc, magnesium and other low melting point alloys | Predominantly non-ferrous alloys, also used in cast steel and cast iron | Mainly cast iron and cast steel |
Range of casting quality | unrestricted | Generally less than25kg | Mainly small and medium-sized castings | Generally less than10kgThe castings can also be used for medium-sized castings. | Mainly small and medium-sized castings | unrestricted |
production volume | unrestricted | Batch and mass production, as well as single piece and small batch production. | In batches, manufacture in bulk | In batches, manufacture in bulk | In batches, manufacture in bulk | In batches, manufacture in bulk |
Casting dimensional tolerances (mm) | 100±1.0 | 100±0.3 | 100±0.4 | 100±0.3 | 100±0.4 | |
Surface roughness of castings | roughness | Ra25~Ra3.2 | Ra25~Ra12.5 | Ra6.3~Ra1.6 | Ra25~Ra6.3 | Roughness of inner surface |
Casting grain organization | coarse grain | coarse grain | grain | Fine grain, many internal pores | grain | |
tolerance (i.e. allowed error) | oldest | Small or no processing | few | Small or no processing | comparatively small | Large machining allowances on internal surfaces |
Productivity (general level of mechanization) | Low, medium | Low, medium | Medium and high | supreme | center | Medium and high |
Minimum wall thickness of castings (mm) | 3.0 | in general0.7 | aluminum2~3 | 0.5~1.0 | general2.0 |
FAQFaqs
Q1: What is the maximum size of centrifugal casting parts that can be handled?
→ Diameter Φ2.5m × length 8m (single piece weight 20 tons)
Q2: How to solve the problem of centrifugal casting segregation?
→ Recommendation: AdoptionPulsed electromagnetic field + gradient coolingcomposite process
Q3: Is it economical to try out small batches?
→ <50 pieces recommended sand casting, mold costs account for too high