Aluminum Alloy Extrusion: Principles, Process Optimization and Outlook for Future Applications
Date: 2024-12-04 Categories: Blog Views: 2123
Classification of Aluminum Alloy
Classification of cooked aluminum
(a) Classification by alloying elements
1. x x x indicates that the purity of 99.0% or more pure aluminum aluminum parts, panels 85/KG
2. x x x indicates aluminum-copper alloy
3. x x x indicates aluminum-manganese alloys
4. x x x indicates aluminum-silicon alloys
5. x x x indicates aluminum-magnesium alloy (imported from Switzerland)
6. x x x indicates aluminum-magnesium-silicon alloy T5 6063 6061
7. x x x indicates aluminum-zinc-magnesium alloy
8. x x x indicates alloys of systems other than those mentioned above
9. x x x indicates alternate classification numbers
(b) Classification by reinforcement mechanism
1. Strain hardeningaluminum: 1 x x x, 3 x x x, 4 x x x, 5 x x x
2. Heat treatable reinforced aluminum alloy: 2××××, 6××××, 7××××
Classification of cast aluminum alloys
Al (Al content minimum 99.0% or more) | 1 ××-× |
Al-Cu alloys | 2 ××-× |
Al-Si alloys containing Cu and Mg or Mg | 3 ××-× |
Al-Si alloys | 3 ××-× |
Al-Mg alloy | 4 ××-× |
Unused systems | 5 ××-× |
Al-Zn alloy | 7 ××-× |
Al-Su alloy | 8 ××-× |
Aluminum Extrusion (Pulled Aluminum) Introduction:
A. Processing Principles:
Aluminum ingots softened at high temperatures inaluminum extrusionUnder the strong extrusion of the machine, it flows through the aluminum extrusion mold and forms the aluminum profile products with the required shape.
B. Aluminum Extrusion Uses and Examples:
Building materials, aerospace industry, people's livelihood industry, precision electronics, optical parts, automobile, information industry, etc.
Examples: Aluminum doors and windows, curtain wall building materials
Installation of fall prevention devices on pylons and structures
Heatsinks and exterior parts for electronic components
Aluminum Ladder
Park and courtyard seating and railings
Advertising signs and signboards
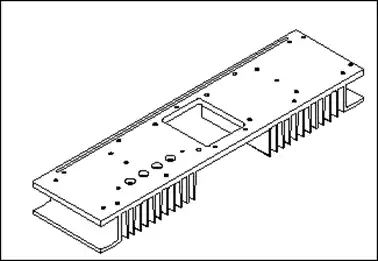
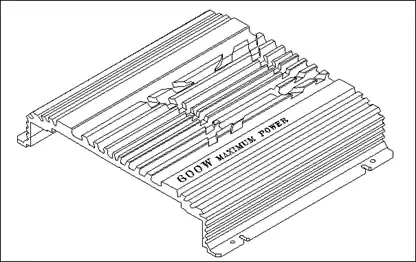
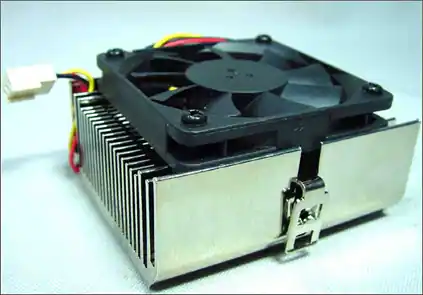
Case I.
Heat sinks for automobiles, electronic components, computer CPUs, etc.
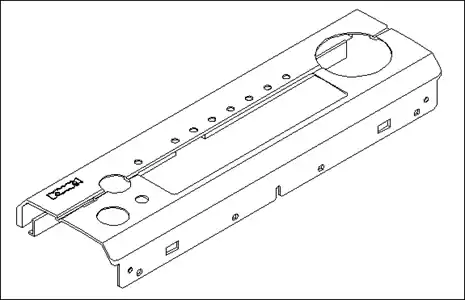
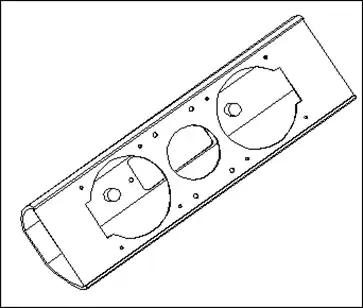
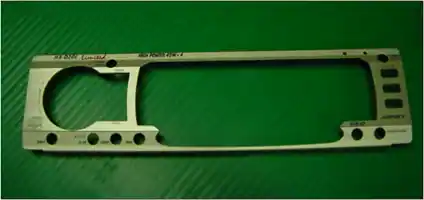
Case II.
Audio speaker tubes, DVD amplifier shells and other appearance products, now gradually applied to MP4, MP3, cell phone shells and other small electronic products shell above.
Aluminum extrusion type commonly used materials
6063 Aluminum Extrusion: (One of the AL-Mg-Si workout alloys)
Chemical composition (%)
Silicon (Si) | Iron (Fe) | Copper (Cu) | Manganese (Mn) | Magnesium (Mg) | Chromium (Cr) | Zinc (Zn) | Titanium (Ti) | Other elements | Aluminum (Al) | |
various | Total | |||||||||
0.20.1¯ | 0.35¯ | 0.1¯ | 0.1¯ | 0.60.45 | -0.9¯ | 0.1¯ | 0.1¯ | 0.05¯ | 0.15¯ | balances |
T5 Heat Treatment.
Refers to the extruded material by the high temperature extrusion process after cooling, by the cold working process and by artificial age hardening treatment.
Melting treatment 520°C aging 205°C about 2 hours
6063-T5 Extruded Mechanical Properties.
Tensile strength Kg/mm2 | Yield strength Kg/mm2 | Elongation % |
15 or more | 11+ | 8 or more |
The above standards are based on Chinese national standards CN82068 and 2257.
Manufacturing process of aluminum extrusion profiles:
Compounding→Melting & Casting→Composition Analysis→Extrusion Molding→Process Inspection→Straightening→Sawing→Process Inspection→Ageing Treatment→Finished Product Inspection→Packaging & Warehousing→Shipping
Aluminum Extrusion Die Introduction
Extrusion molds are divided into flat molds, bridge molds and hollow molds.
Steel used for molds
1.SKD-61 Japan high frequency 2.Hitachi DAC
3.Sweden ASSB 4.Sweden QRO-90
Design of the feed opening.
The feed opening of the die is determined by the size of the ingot cylinder, for example.
1500T machine, using Φ6" spindle-Φ140mm
2350T machine, using Φ8" spindle-Φ190mm, Φ9"-Φ210mm.
In order to prevent the surface of the ingot from penetrating into the inlet, the inlet is usually at least 1.5 mm thicker than the ingot container on each side.
10~15mm smaller.
Shrink Size.
Increase the mold size by 1% according to the actual size of the extruded mold.
Design Brief
A. Betting Ratio.
Hollow mold-profile section area: ingot cylinder section area = (40-60):1
Solid molds are in the 80-100 range and extrusion is good.
B. Relationship between profile flesh thickness and alloying
Alloy Type | Extruded outer recruiting circle diameter | Minimum meat thickness required for extrusion |
6063 | 0~75mm | 0.85mm |
75~100mm | 1.15mm | |
100~150mm | 1.60mm | |
150~200mm | 2.00mm | |
200~250mm | 2.50mm | |
6061 | 0~75mm | 1.30mm |
75~100mm | 1.60mm | |
100~150mm | 2.00mm | |
150~200mm | 3.00mm | |
200~250mm | 4.80mm |
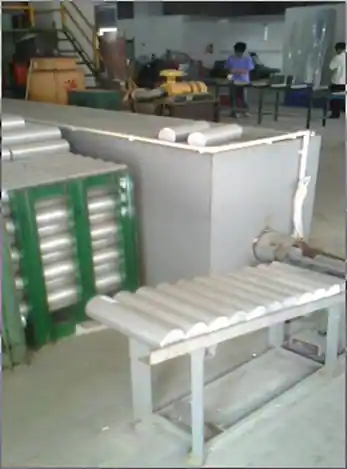
Raw materials (aluminum ingots) and heating of aluminum ingots
(Material temperature 480+/-20 degrees)
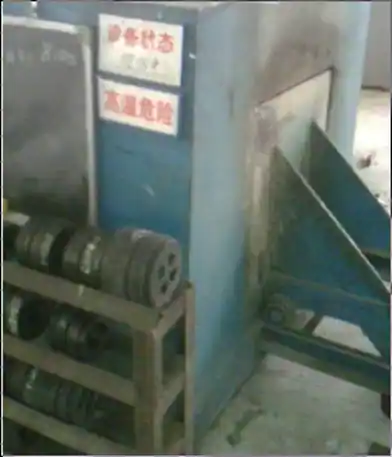
Extrusion mold and mold heating
(Mold temperature 470+/-10 degrees, hold for 2-4 hours)
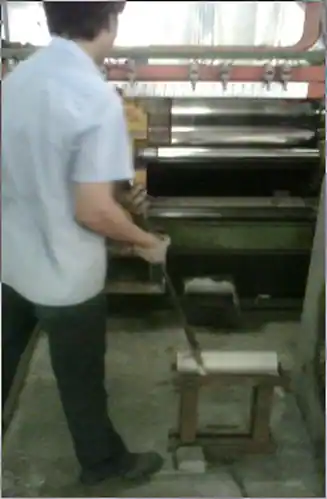
feed
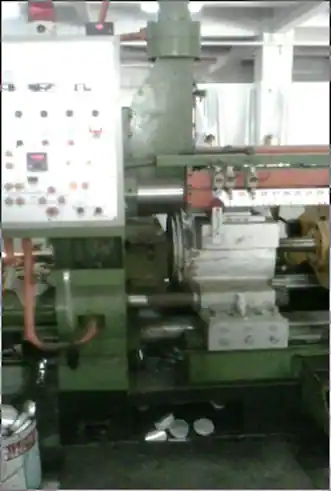
squeezes
(Machine must be warmed up to 380+/-10 degrees)
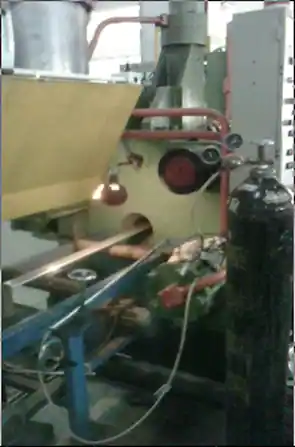
exposed to strong winds
(Temperature controlled below 300 degrees)
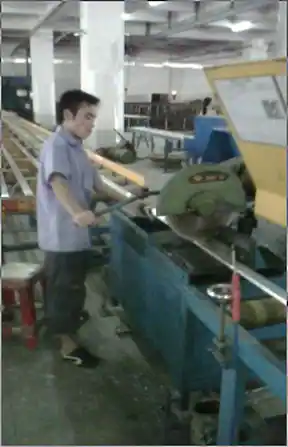
cut
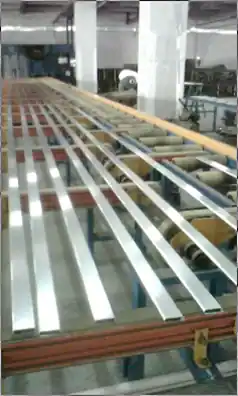
after cutting
Aluminum Extrusion Die Introduction
Extrusion molds are divided into flat molds, bridge molds and hollow molds.
Steel used for molds
1.SKD-61 Japan high frequency 2.Hitachi DAC
3.Sweden ASSB 4.Sweden QRO-90
Design of the feed opening.
The feed opening of the die is determined by the size of the ingot cylinder, for example.
1500T machine, using Φ6" spindle-Φ140mm
2350T machine, using Φ8" spindle-Φ190mm, Φ9"-Φ210mm.
In order to prevent the surface of the ingot from penetrating into the inlet, the inlet is usually at least 1.5 mm thicker than the ingot container on each side.
10~15mm smaller.
Shrink Size.
Increase the mold size by 1% according to the actual size of the extruded mold.
Design Outline:
a. Betting ratio.
Hollow mold-profile section area: ingot cylinder section area = (40-60):1
Solid molds are in the 80-100 range and extrusion is good.
b. Relationship between profile flesh thickness and alloy.
Alloy Type | Extruded outer recruiting circle diameter | Minimum meat thickness required for extrusion |
6063 | 0~75mm | 0.85mm |
75~100mm | 1.15mm | |
100~150mm | 1.60mm | |
150~200mm | 2.00mm | |
200~250mm | 2.50mm | |
6061 | 0~75mm | 1.30mm |
75~100mm | 1.60mm | |
100~150mm | 2.00mm | |
150~200mm | 3.00mm | |
200~250mm | 4.80mm |
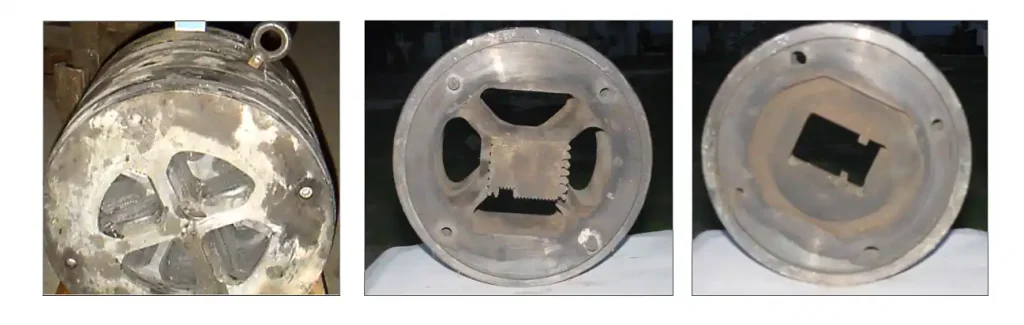
This picture is a picture of a die for a hollow aluminum extrusion.
Upper left is the whole set of mold, middle is the upper part of the mold, right is the lower part of the mold
Hardness of aluminum profiles
Aluminum profiles commonly used material is 6063-T5, hardness is adjusted and controlled by subsequent aging treatment (i.e., heat treatment: preheating for 3 hours, temperature up to 195 ± 10 ℃, insulation for 3 hours and then out of the air-cooled). According to the subsequent processing of the product, the hardness requirements are shown in the table below:
Type | hardness |
General Extrusion | WB11-13 |
Extruded shape requiring grooving and milling | WB11-13 |
Extruded shape where the hole diameter is close to the edge and the punched hole is prone to denting and deformation. | WB5-8 |
Extruded with countersunk holes, pull-out holes | WB8-10 |
Aluminum sheet to be bent and formed, extruded | WB5-8 |
Aluminum plate 1050/1100 | WB5-8 |
Aluminum extrusion material 6063-T5 | WB11-13 |
Aluminum extrusion material 6061-T6 | WB13-15 |
Aluminum Extruded Material Inspection Standards
Aluminum extrusion material inspection standards are shown in the table below. Aluminum extrusion profile for cell phone belongs to the tube category, and it is used to check the inner shape size and curvature with the specially made inner cavity jig, and the appearance surface is determined by test grinding and oxidation.
Extrusion Manufacturers' Process Tolerance Capability Status
Dongfeng | Golden Bridge |
Thickness tolerance: 1.5-5 ±0.1 5-10 ±0.15 Above 10 ±0.2 Tolerance of external dimensions: Below 30 ±0.15 30-60 ±0.2 60-120 ±0.3 Above 120 ±0.4 Flatness: below 50 0.1 50-100 0.2 100-200 0.3 Angle: ±0.5° Extruded hole diameter tolerance: ±0.08 Extrusion hole min: ø1.3 Can open the maximum range of the extruder type: Within 200mm of external circle | Minimum thickness tolerance: ±0.1 Shape and position tolerance min: ±0.1 Overall dimensions: 0-6 ±0.15 6-30 ±0.2 30-120 ±0.3 120-315 ±0.4 Above 315 ±0.5 Flatness: Below 50 0.1 50-200 0.2 Above 200 0.25-0.3 Angle: ±0.5° Extruded hole diameter tolerance: ±0.08 Extrusion hole min: ø1.6 Can open the maximum range of the extruder type: Within 310mm diagonally |
Aluminum Extrusion Design Considerations
Extrusion molds are divided into flat molds, bridge molds and hollow molds.
. Tolerance should be set to fully consider the manufacturer's production capacity, because aluminum extrusion is molded under hot pressure, the product tolerance is relatively large compared to the rubber parts, hardware, see the above table.
. The thickness of the material should not be too thin, in principle, more than 0.8mm, less deformation, better extrusion condition, and mass production.
. Hollow tube material thickness difference should not be too large, generally not more than 4 times, otherwise the mold is more difficult to trim and extrusion.
. Formally open the mold, must provide detailed surface process results, because the surface treatment process affects the pre-extrusion mold clamping line determination, affecting the extrusion mold, hardware punching die mold size value (oil spraying will make the product aperture becomes smaller, the shape of the larger, narrower inner cavity, and oxidation is the opposite;sandblast(This can result in larger apertures, thinner bodies, or deformation of the product; the wire drawing process should consider the material to leave a margin)
. Extruded material can not do absolute sharp corners, the design of the sharp corners of the prismatic aluminum profiles will have about 0. 3 R angle, after subsequent polishing, oxidation, oil spraying and other processes, the R angle will reach about 0. 4.
. The proportion of hollow and solid parts of aluminum extrusion shall not be too large or offset too much, depending on the actual structure.
. Common hollow mold construction:
The hollow tube shown on the right can be as thin as 0.7, depending on the shape and size of the structure.
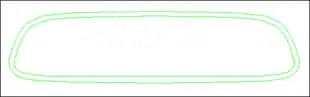
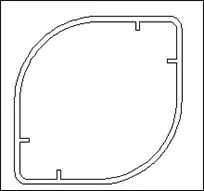
The hollow tube shown in the left picture, the width of the four bars is generally in a material thickness, not too wide, too wide will lead to the appearance of the surface of the concave marks and water lines, depending on the structure of the shape and dimensions
The hollow tube shown on the right is the common structure of the horn tube, and other accessories are fixed by tapping on the cylinder, but the size of the cylinder is relatively large, and it is not suitable for cell phone parts and MP3 and other small products.
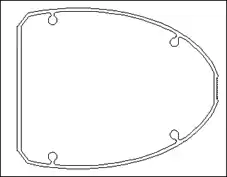
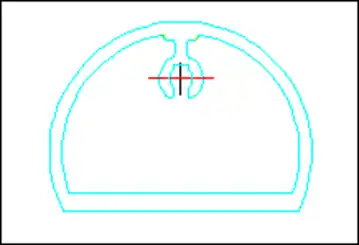
Left hollow tube, also belongs to the common structure of the horn tube, shaped holes can be inserted into a guide rail, guide other accessories
The hollow tube shown on the right is also a commonly used structure for flared tubes, and the round hole can be tapped directly or inserted into a riveted round steel post to fix or guide other fittings.
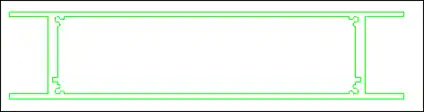
. Extruded hole design considerations
Take for example the labeling of the extruded holes in the figure on the right
A show: extrusion hole (riveting PIN or screws) of the minimum diameter of the hole diameter reference value of 1.3 (different manufacturers of different machine tonnage of the minimum value is not the same, depending on the shape of the structure), the hole tolerance band should be at least 0.15 range;
B at the show: must leave the wall thickness, wall thickness value is generally about 0.5, not too little, to prevent the screws or PIN hit down after the expansion, outward letting
C: Here add R angle R0.5 or so, good for extrusion mold life and material flow;
D: This size should be considered the feasibility of extrusion manufacturers, the tolerance can be taken as the upper limit, A for ø2.0, need to take 1.2-1.5mm, A for ø1.5, need to take 0.8-1.0mm.
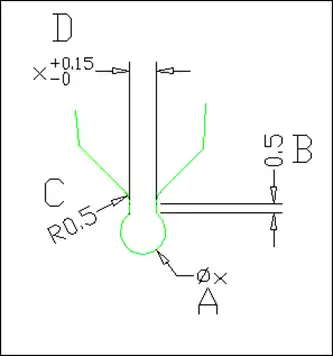
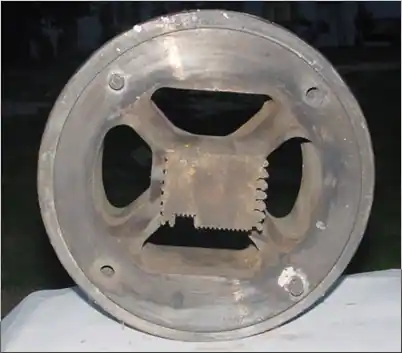
Mold inlet for hollow molds
. Closing line problem for aluminum extruded hollow molds:
As shown in the picture, the hollow mold structure of the product material is extruded from four or two (according to the size of the product) inlet, four strands of material in the mold inside the final fusion, but in the fusion of the four strands of material will produce a dark line, called the mold line. The material at the mold line is easy to produce bubbles, water lines, impurities and other bad appearance.
For the surface treatment of grinding, oxidation type of appearance hollow tube products (horn tube, MP3 shell, etc.), because of its appearance requirements, in the extrusion mold opening should be communicated to confirm the location of the clamping line and the important appearance of the protective surface and the general appearance of the surface, so that extrusion molding manufacturers will be arranged in the non-appearance of the surface of the molding line in the non-appearance of the appearance of the surface and the appearance of the surface of the secondary, as well as the Division grinding process using special processing techniques to minimize and eliminate the clamping line. The traces of the molding line are minimized and eliminated by our special processing techniques during the grinding process.
Aluminum extrusion surface treatment process
The post-processing process for aluminum extrusion is fully compatible with that for aluminum sheet metal parts.
Aluminum extruded built-in parts generally use degreasing and cleaning process; the appearance of the parts of the process are brushed, sandblasted, oxidized, high-gloss, silkscreen, laser, oil spraying, secondary oxidation and so on.
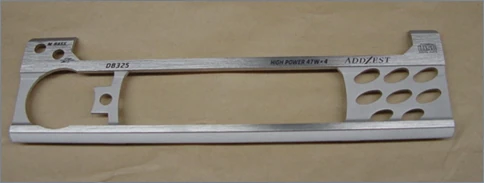
Drawing + sandblasting + oxidizing + silk-screening
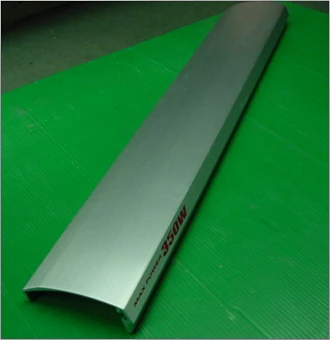