Low pressure die casting molds
Date: 2025-02-25 Categories: Blog Views: 1972
Low-pressure casting It is a casting method in which molten metal is injected into the mold cavity by gas pressure. Compared with high-pressure casting, low-pressure casting can improve the surface quality of castings, reduce porosity, and is suitable for casting more complex shapes. In the process of low-pressure casting, the composition and design of the mold is critical, which directly affects the quality of the castings, production efficiency and the service life of the mold. This paper will discuss Low pressure casting mold The main components of the casting and their influence on the quality of the casting.
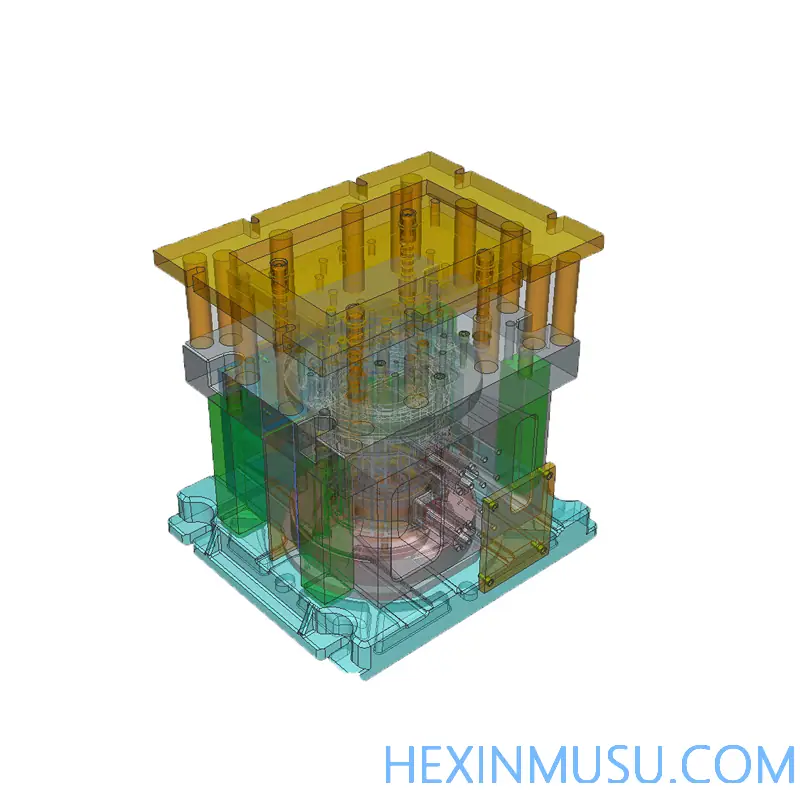
The main components of low pressure casting mold
Low-pressure casting mold by the six core components of the synergistic effect: mold cavity as the core of the molding, the use of H13 hot work mold steel precision machining, to ensure ± 0.15mm dimensional tolerance and Ra ≤ 0.8μm surface finish; injection port through the 60 ° tapered tangent design to achieve laminar flow filling, the flow rate is controlled in the 0.8-1.2m / s in order to avoid the volume of gas; exhaust system integration of the parting surface of the micro-gap ( 0.05-0.08mm), vacuum groove and porous ceramic plugs to reduce the porosity defect rate of more than 80%; cooling system built-in profiling with the shape of the waterway, 8-12mm from the mold surface arrangement, combined with the flow control valve to make the mold temperature gradient <15 ℃; mold frame using QT600 ductile iron box structure, elastic deformation <0.02mm/1000kN; sealing system through the The sealing system combines high-temperature fluorine rubber ring and metal hard seal, the leakage rate is <0.5Pa-m³/s, which guarantees the stable operation of 150,000 mold times.
Key Considerations for Low Pressure Casting Mold Design
The mold design needs to balance the material performance, structural mechanics and maintenance cost. Priority is given to H13 steel (hardness HRC48-52) or SKD61 (surface TD treatment) to cope with aluminum washout and thermal stress; MAGMAsoft is used to carry out multi-field coupling simulation of filling-solidification to ensure that the temperature difference between metal fronts is 1.5; modular design is used to realize rapid replacement of inserts, and combined with the strain gauges to monitor the expansion of fatigue cracks in the mold in real time. The cooling water circuit layout needs to be optimized by ANSYS thermodynamics, so that the temperature difference of local hot spots can be controlled within ±3℃; at the same time, the hydraulic jacking bar system (density of 1/100cm²) and zero positioning interface are preset, which can shorten the maintenance downtime to 12 minutes.
Advantages and applications of low pressure casting molds
Low-pressure casting molds in the automotive, aviation field to show unique advantages: through the 0.3mm machining allowance near-net molding technology, a new energy vehicle control arm to save 62%machiningCost; Vacuum-assisted casting makes the qualification rate of 1.2mm thin-walled parts reach 98%, and the weight reduction is 35% compared with the traditional process; Gradient temperature-control technology improvesaluminumGrain size to grade 7 (ASTM E112), wheel casting fatigue life increased by 3 times. In the field of aviation, Ti6Al4V titanium alloy hatch hinge mold to achieve tensile strength > 950MPa, directional solidification blade mold columnar crystal ratio of more than 80%. Compared with high-pressure casting, its single-piece material cost reduction of 29% ($85 vs. $120), mold life enhancement of 87.5% (150,000 die times vs. 80,000 die times).
Core features of low pressure casting molds
This technology combines cost-effectiveness and precision manufacturing: shorten the mold development cycle by 40% (digital twin only needs 2 trials), surface roughness up to Ra0.8μm (better than high pressure casting's 1.6μm); adapt to the 0.8-150mm wall thickness range, especially good at the complex internal cavity parts such as engine block; fully automated production through PLC integration with a production beat of ≤ 90 seconds per piece, saving 45% in labor costs; material utilization up to 95% (30% higher than sand casting); further reduce the carbon footprint with the application of recycled aluminum. Saving 45%; material utilization rate up to 95% (30% higher than sand casting), with the application of recycled aluminum to further reduce the carbon footprint.
Frequently Asked Questions (FAQ)
How to choose between H13 and SKD61 mold steel?
H13 steel (hardness HRC48-52) is suitable for high-temperature cycling conditions (such as engine block molds), and its thermal fatigue resistance is 30% higher than that of SKD61; while SKD61, with surface hardness up to HV1800 after vanadium infiltration by TD, is more suitable for ejector pins with high wear-resistant requirements, and can extend its life to more than 200,000 die times.
2. How to solve the problem of aluminum sticking to the mold?
The use of laser burring technology (surface roughness Sa 2.5μm) combined with amorphous carbon coating (friction coefficient 0.1), together with the release agent quantitative spraying (3-5g/m²), can reduce the rate of aluminum adhesion to below 0.1%. After the application of a gearbox housing mold, the cleaning time was shortened from 30 minutes/mold to 5 minutes.
3. How can the mold cooling system be optimized?
The use of 3D printing with the shape of the cooling water circuit, the distance from the mold surface is shortened to 5mm, with dynamic flow control (PID algorithm adjustment), can make the local mold temperature difference from ± 15 ℃ down to ± 3 ℃, the casting solidification time is reduced by 25%, the yield is increased by 12%.
4. What is the cost difference between low and high pressure casting molds?
Initial mold investment in low-pressure casting is 40% lower (about 500,000 yuan vs. 850,000 yuan), but single-piece material cost savings of 29% (85 yuan vs. 120 yuan). With an annual production capacity of 100,000 pieces, the total cost of the low-pressure process can be reduced by 2.1 million yuan.
5. How can mold life be extended?
Nitriding treatment (white bright layer thickness of 0.08-0.12mm) combined with stress annealing (300°C x 4 hours) every 50,000 die cycles can increase H13 steel mold life from 100,000 die cycles to 180,000 die cycles, with a reduction of 35% in comprehensive maintenance costs.
6. How to ensure the quality of thin-walled castings (<1.5mm)?
Adopting vacuum-assisted technology (cavity vacuum ≤ 50mbar) superimposed on extrusion and shrinkage (pressure 80-100MPa), it can realize stable production of aluminum alloy parts with a wall thickness of 1.2mm, with a porosity rate of <0.5% and an increase in strength of 20%.
7. What are the future technology trends?
Intelligent molds (embedded fiber optic sensors to monitor stress in real time) and self-healing coatings (microcapsules to release restorative agents) will be mass-produced in 2026, which are expected to reduce mold maintenance costs by another 40%. Semi-solid casting technology will bring down the wall thickness limit to 0.5mm, boosting new energy vehicles to reduce weight by more than 15%.
reach a verdict
The composition of low pressure casting mold directly determines the quality and productivity of castings. Through the reasonable design of the various components of the mold, including the mold cavity, injection port, exhaust system, cooling system, etc., can significantly improve the surface quality of castings, reduce defects, and extend the service life of the mold. With the development of technology, low-pressure casting mold materials and designs continue to innovate, and will play an important role in more areas in the future.