Die casting technology: a key manufacturing process for turning visions into reality
Date: 2024-12-24 Categories: Blog Views: 1833
In modern manufacturing, the die-casting process is regarded as an important means of manufacturing precision metal parts. It injects molten metal into precision molds at high pressure, enabling the production of complex shaped metal parts, which are widely used in automotive, electronics and other fields, supporting the technological development of several leading industries. This paper will provide an in-depth analysis of the core processes, material selection and applications of the die casting process, and how this process can achieve innovation and excellence in manufacturing.
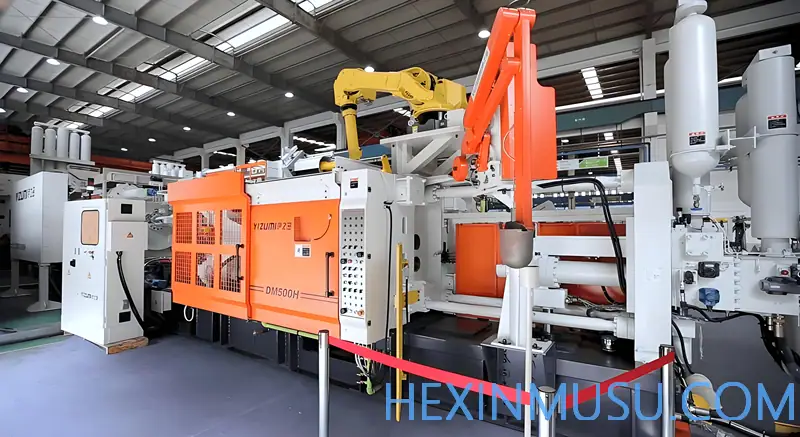
What is die casting?
Die casting is an efficient and precise method of metal casting that utilizes reusable molds to produce complex shaped metal parts. Unlike traditional casting processes, die casting injects molten metal into the mold under high pressure, making it particularly suited to high-volume production and providing high precision, repeatability, and excellent surface finish.
The die casting process was initially used in the printing industry, but its potential for widespread use soon expanded to a number of fields, including the automotive, aerospace and electronics industries. Today, die casting uses primarily lightweight metals such as aluminum, zinc and magnesium to meet the manufacturing needs of a wide range of products, from small, complex components to critical automotive parts. The core advantage of die casting is its ability to create parts with extremely tight tolerances and reduced need for subsequent machining, making it an indispensable technology in modern manufacturing.
Die Casting Process
The production process of die casting can be divided into several key steps:
- Mold Preparation
Molds are the foundation of the die casting process, and common types of molds include single cavity molds, multi-cavity molds, and combination molds. Mold design needs to consider the complexity of the part and the scale of production, the mold needs to be cleaned and preheated before use to avoid cracks and thermal defects. - injection process
During the injection process, molten metal is melted and injected into the mold in different systems. In the case of the hot chamber system, the melting takes place inside the casting machine, while the cold chamber system pours the molten metal into the cold chamber where it is injected into the mold by pressure. - Cooling and solidification
The molten metal is cooled and solidified in a mold to form the final part. The cooling process requires controlled pressure to prevent defects in the part due to shrinkage. - eject (from a plane)
Once the metal is fully solidified, the mold is opened and the machine ejector pushes the part out. - Trimming and post-processing
To ensure the quality of the part, excess material and burrs need to be removed. If necessary, the accuracy of the part can be further improved by post-processing methods such as grinding.
Types of Die Casting
Depending on the melting and injection process, the die casting process can be divided into two main types: hot chamber die casting and cold chamber die casting:
- hot cell die casting (metallurgy)
Suitable for low melting point metals such as zinc and certainaluminum. The process uses a pneumatic plunger to inject metal into the mold through a molten metal reservoir attached to the die casting machine. It is efficient, fast and suitable for high volume production of small parts, commonly used in the production of consumer electronics. - cold room die casting (metallurgy)
Used for high melting point metals such as aluminum and copper alloys. In cold chamber die casting, molten metal is first poured into a cold chamber and then injected into the mold through a plunger. This process is suitable for parts requiring high strength and heat resistance and is widely used in automotive and aerospace applications.
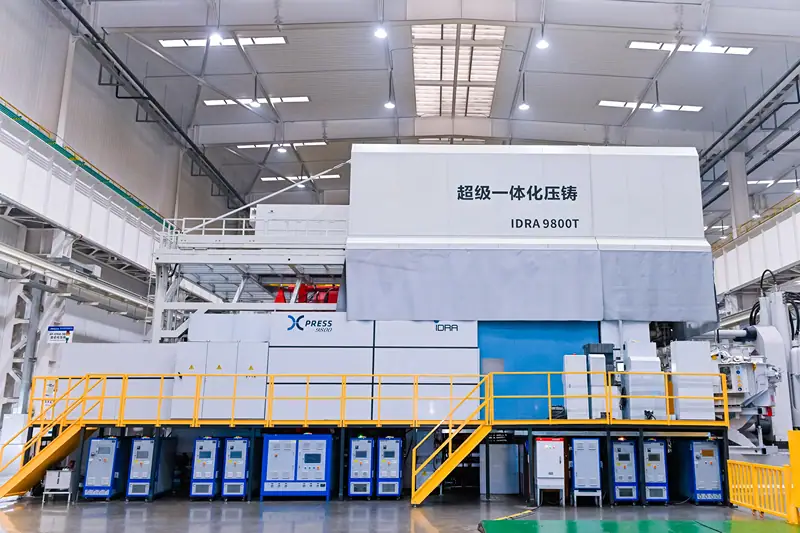
Die casting variants and innovations
As technology continues to evolve, the die casting process has seen a variety of variants and innovations to meet different industrial needs. For example:
- gravity die casting: Molten metal is injected into the mold using gravity, making it suitable for the production of high-volume precision castings.
- pressure die casting: Filled with metal by low or high pressure, it is suitable for the production of parts that require high precision, such as automotive and aerospace parts.
- vacuum die casting: Improve surface quality and dimensional accuracy by creating a vacuum environment that reduces air retention and is suitable for high-end products.
- extrusion die casting: It can improve the mechanical properties and precision of the parts and is commonly used in automotive parts.
- Semi-solid die casting: Produces parts with complex geometries with higher precision and strength through specific casting temperatures.
Comparison of advantages and disadvantages of die casting
The advantages of metal die casting, a manufacturing process widely used in industrial production, have made it an important part of high-volume production. However, it also has some limitations that may affect its use in certain application scenarios. The following is an analysis of the main advantages and disadvantages of die casting and the reasons for them:
Advantages of Die Casting
- Excellent dimensional accuracy
Metal die casting is capable of producing parts with high dimensional accuracy, especially for applications requiring tight tolerances. Accuracy depends on the mold design and manufacturing process, and higher dimensional accuracy can be achieved especially when the molds are manufactured using high-precision CNC machines, such as 5-axis CNC machines. In addition, the use of process variants such as low pressure die casting (LPDC) and gravity die casting helps to fill the molds accurately, thus increasing the accuracy of the parts. - Complex geometry
Die casting is capable of producing parts with complex geometries, including castings, thin walls, and other designs. This characteristic has enabled die casting to produce parts with complex structures and a wide range of functions in fields such as aerospace, automotive and consumer electronics. In this way, designers can integrate more functionality into a single part, reducing the need for subsequent assembly. - High-volume production for fast delivery
Die casting is a high-volume production process suitable for making large quantities of parts. In high-pressure casting, production is faster due to the high pressure used, which reduces the production cost per part. Especially in the case of using a combination of molds, multiple parts can be manufactured at the same time, increasing productivity and cost-effectiveness per part. - Smooth surface finish
Due to the high pressure injected into the metal during the die casting process, cast metal parts usually have a smooth surface finish, especially in theLow-pressure casting,Gravitational castingand other processes. This high-quality surface treatment not only improves the appearance of the part, but also reduces the amount of effort required for subsequent surface treatments. - Long mold life
die casting moldThey are usually made of high quality steel with excellent resistance to high temperatures and pressures. These tough steels allow the molds to withstand prolonged use and have a long service life, reducing the frequency of mold replacements and maintenance costs for long-term production.
Disadvantages of die casting
- For non-ferrous metals only
The die casting process is mainly applied to non-ferrous metals such as aluminum, zinc and magnesium. These metals have moderate melting points and are easy to inject into molds under high pressure. However, for ferrous metals with higher melting points, such as steel and iron, die casting is not suitable. Metals such as steel and iron require special equipment and more complex processes to cast, which makes the application of die casting somewhat limited. - High mold cost
Die casting molds are more expensive to manufacture, especially when using thenumerical control machiningWhen it comes to making molds, the process is complex and costly. Especially when manufacturing complex parts, the use of high-quality steel molds will further drive up costs. While the die casting process is suitable for high volume production, the cost of the molds can be a limiting factor for small quantities or complex parts. - Sensitivity to defects
Die casting parts in the production process may appear porosity, shrinkage, porosity and other defects, especially in high-pressure casting, these defects are more common. For example, air retention during the casting process may lead to the creation of pores on the surface of the part, and these pores may form air bubbles during heat treatment, affecting the quality of the part. Additional surface finishing steps may be required to address these defects, increasing production costs. - Not suitable for small-scale production
Although die casting is suitable for mass production, its initial investment is high, especially the fixed costs of mold manufacturing and equipment setup. As a result, the die casting process is usually not suitable for small-scale production or one-off part production. For small-scale production, other processes (such as injection molding or CNC machining) may be more appropriate and can reduce costs and production lead times.
Hershey's Metal Materials in Die Casting
The metal materials used in the die casting process are usually non-ferrous alloys such as aluminum, magnesium and zinc. These alloys have different performance characteristics and are suitable for different application requirements. The following table provides a detailed comparison of common die casting alloys, listing their main compositions, melting points, properties, and typical applications.
alloys | Common subtypes | base | Melting point (°C) | Main characteristics | typical application |
---|---|---|---|---|---|
aluminum | a380, a360, a390, a413, adc12 | Aluminum (Al), Copper (Cu), Silicon (Si), Magnesium (Mg) | 577 - 660 | Light weight, corrosion resistant, high strength, good workability and cost effective. | Automotive (engine components, wheels, chassis), aerospace (structural components, housings), electronics (housings, bodies) |
magnesium alloy | az91d, am60b, as41b | Magnesium (Mg), Aluminum (Al), Zinc (Zn) | 632 - 650 | Extremely lightweight, good castability for weight-sensitive applications, excellent castability. | Aerospace (body structure, interior parts), automotive (lightweight components), electronics (handheld devices, cell phone housings) |
zinc alloy | Zinc alloy #2, #3, #5, #7, ZA8, ZA27 | Zinc (Zn), Aluminum (Al), Copper (Cu), Magnesium (Mg) | 381 - 419 | Excellent castability, low melting point, suitable for complex designs and cost effective. | Electronics (connectors, housings), hardware (locks, buttons), toys and automotive parts (decorative parts, gears) |
copper alloy | Brass (e.g. C85700), bronze (e.g. C93200) | Copper (Cu), Zinc (Zn) (Brass); Copper (Cu), Tin (Sn) (Bronze) | 900 - 1083 | High strength, excellent conductivity and corrosion resistance, durable. | Piping (corrosion-resistant water pipes, gas pipes), electrical connectors (terminals, electrical contacts), marine components (corrosion-resistant components), bearings |
tin alloy | - | Tin (Sn) (90%), Copper (Cu) (2.5%), Lead (Pb) (7.5%), Antimony (Sb) | 170 - 230 | Low melting point, good fluidity, corrosion resistance, easy casting. | Decorative items (jewelry, handicrafts), figurines, souvenirs |
lead alloy | - | Lead (Pb), Tin (Sn) | 183 - 327 | Low melting point, soft, good corrosion resistance, suitable for radiation shielding. | Radiation shielding (medical equipment, nuclear facilities), batteries (gradually being replaced) |
tin-based alloy | - | Tin (Sn), Copper (Cu), Antimony (Sb) | 232 | Low melting point, good casting properties, good corrosion resistance. | Electronic components (soldering materials, electronic parts), jewelry, special applications (small parts, fine jewelry) |
Comparison of die casting with other manufacturing processes
Die casting is often confused with other manufacturing processes (e.g., injection molding, forging, stamping, etc.), especially for those new to manufacturing. Despite their similarities, each process has its own unique benefits and areas of application. Below is a comparison of die casting with common processes such as injection molding and forging to help understand the differences and application scenarios:
Difference between die casting and injection molding
Die casting and injection molding are two popular molding processes that use the principle of injection and are suitable for creating parts with intricate details and excellent surface finishes. However, their applicable materials and processes differ. The following are the main differences between the two:
discrepancy | Die casting | injection molding |
---|---|---|
workflows | Injection of molten metal under pressure into pre-designed steel molds | Injection of molten plastic under pressure into pre-designed steel or aluminum molds |
makings | Non-ferrous metal alloys (e.g. aluminum, zinc, magnesium) | Thermoplastics or thermosets |
Mold Materials | steel (chemistry) | Steel or Aluminum |
cooldown | Longer cooldown time | Shorter cooldown |
production speed | relatively slow | relatively soon |
processing cost | Higher mold costs (using steel molds) | Lower tooling costs (using aluminum tooling) |
component cost | Higher (due to longer production time) | Lower (faster production time) |
Difference between die casting and forging
The main difference between forging and die casting is the way they are molded. Forging involves molding metal in a solid state by applying compressive force, while die casting involves injecting molten metal into a pre-designed mold. The two processes also differ in terms of applicable materials, production speed and part performance:
discrepancy | forge (metal) | Die casting |
---|---|---|
workflows | Forming of heated metal by applying compressive force | Injection of molten metal into a mold under pressure |
makings | For ferrous and non-ferrous metals, such as steel, aluminum | For non-ferrous metals such as aluminum, zinc, magnesium |
Molding materials | Does not require a mold, but uses a mold to optimize the shape | Must use molds |
production speed | slower | relatively soon |
tolerance control | Medium tolerance | High precision tolerance control |
Final Part Properties | Improvement of mechanical properties | Mechanical properties depend on the casting material |
Difference between die casting and stamping
Stamping is a process of forming metal sheets by means of a press, and is suitable for the mass production of thin-walled parts. Compared to die casting, stamping has different molding materials and processes, especially in terms of the complexity of the applicable parts and productivity:
discrepancy | Die casting | punch |
---|---|---|
workflows | Injecting molten metal into a mold to form a shape | Forming parts by stamping metal sheets using a die. |
makings | Mainly non-ferrous metal alloys (e.g. aluminum, zinc) | Suitable for various metal sheets (e.g. steel, aluminum) |
Mold Materials | steel (chemistry) | steel (chemistry) |
Part Shape | For complex shaped parts | For thin-walled parts and simple shapes |
production speed | slower | relatively soon |
accurate | highly accurate | Lower precision |
Difference between die casting and 3D printing
3D printing is an additive manufacturing-based process that creates parts by stacking materials layer by layer. 3D printing offers greater flexibility and faster prototyping capabilities than die casting, but differs in production speed and part performance:
discrepancy | Die casting | 3D printing |
---|---|---|
workflows | Injecting molten metal into a mold to form a shape | Layer-by-layer printing of materials based on digital models |
makings | Non-ferrous metal alloys (e.g. aluminum, zinc) | Thermoplastics, metal powders, etc. |
Mold Materials | steel (chemistry) | No molds required |
production speed | slower | relatively soon |
accurate | highly accurate | Moderate precision |
appliance | Mass production of complex parts | Rapid prototyping, low volume production |
Common die casting materials and selection
Aluminum, zinc, magnesium and other alloys are common die-casting materials, they each have unique properties, suitable for different application scenarios. The following are the characteristics of several common alloys:
- aluminum: Lightweight, corrosion-resistant, and easy to process, it is widely used in automotive, aerospace, and electronics applications.
- magnesium alloy: Very lightweight for weight-critical applications such as aerospace and consumer electronics.
- zinc alloy: Low melting point, excellent castability, commonly used in electronic products, hardware and toy parts.
- copper alloy: High strength and good electrical conductivity for electrical connectors and marine components.
Design and Manufacturing Optimization
Die casting design is not only dependent on material selection, but also needs to consider factors such as part geometry, draft angle, fillet radius, etc., in order to improve part performance, manufacturability and cost-effectiveness. For example, a proper draft angle can effectively prevent parts from sticking to the mold and reduce the risk of damage; a reasonable fillet radius can help evenly distribute stresses and avoid stress concentrations.
reach a verdict
Die casting has become an indispensable technology in modern manufacturing due to its high precision and high volume production capabilities. Whether it's automotive parts, electronic housings, or aerospace components, die casting technology provides a solid foundation for innovation and design excellence. As materials and processes continue to advance, die casting will continue to bring more efficient, higher quality solutions to a wide range of industries in the future.
Die casting common problems and coping strategies
Why are die castings prone to porosity?
Pockets are usually caused by the metal not venting completely during the injection process, or by defective mold design (e.g., poor venting system). Strategies include optimizing the mold venting design, adjusting the injection speed and pressure, and using a more efficient venting system.
Why are defects likely to appear on the surface of die castings?
Surface imperfections such as bubbles, creases and scratches are mostly caused by uneven mold surfaces or uneven metal flow. To avoid such problems, the surface finish of the mold should be checked regularly to ensure that the injection temperature and flow rate are stable.
What is the problem with shrinkage holes in die castings?
Shrinkage hole is due to the casting cooling metal shrinkage failed to replenish the filler, often appear in large or complex shape die casting. Shrinkage holes can be effectively avoided by optimizing the mold design, improving the efficiency of the pouring system and adjusting the cooling rate.
Are die castings prone to cracking?
Cracking usually occurs when the metal flows unevenly or cools too quickly, and can be caused by excessive injection pressure or poor mold design. Cracking can be minimized by controlling injection speed, temperature and pressure, and by using high-strength materials.
What about dimensional instability of die castings?
Dimensional instability may be due to mold wear, unstable injection pressure or improper temperature control. Regular overhaul and maintenance of the mold to maintain stable injection conditions, as well as fine tuning of the temperature control system, can effectively solve the problem of dimensional instability.
How does mold wear affect die casting quality?
Wear of molds can lead to loss of product precision and even affect the appearance and performance of castings. In order to cope with the problem of die wear, the dies should be inspected and replaced regularly, wear-resistant materials should be used, and the design and process of the dies should be optimized.
Why are die castings prone to deformation?
Deformation is usually due to uneven cooling or poor mold design, especially when the casting is large or complex. The risk of distortion can be reduced by adjusting the cooling system and optimizing the mold design.
How can cold segregation be reduced?
Cold segregation is a delamination defect formed due to the failure of the metal to fully fuse when injected into the mold. To prevent cold segregation, it is necessary to optimize the injection speed and temperature to ensure smooth metal flow, and reasonably design the pouring system and runner.
Is post-processing of die castings necessary?
The post-processing requirements for die castings depend on the design requirements and surface quality criteria of the part. Some parts require additional machining such as grinding, drilling or deburring to meet tight tolerances and surface finishes.