CNC machining 20 years of combat: the teacher hand in hand to teach you to play the CNC machine tools
Date: 2024-12-26 Categories: Blog Views: 1954
I am Ningbo He Xin dry more than 20 years old CNC, from the apprentice to touch the iron chips to take the apprentice to adjust the five-axis, the hand of the parts less than hundreds of thousands of pieces. Today, I will nag with you!numerical control machiningThose doorways are guaranteed to make you listen to them for less!
What's so great about CNC machines?
In the early years, when we were doing manual milling, it was hard to make 10 pieces a day. Now with five-axis linkage, complex surface of the aviation blade can be 50 pieces a day! Precision is from millimeter-level dry to hair-thin (± 0.01mm), the last time for German customers to do precision bushings, three coordinates test report out, foreigners thumbs up.
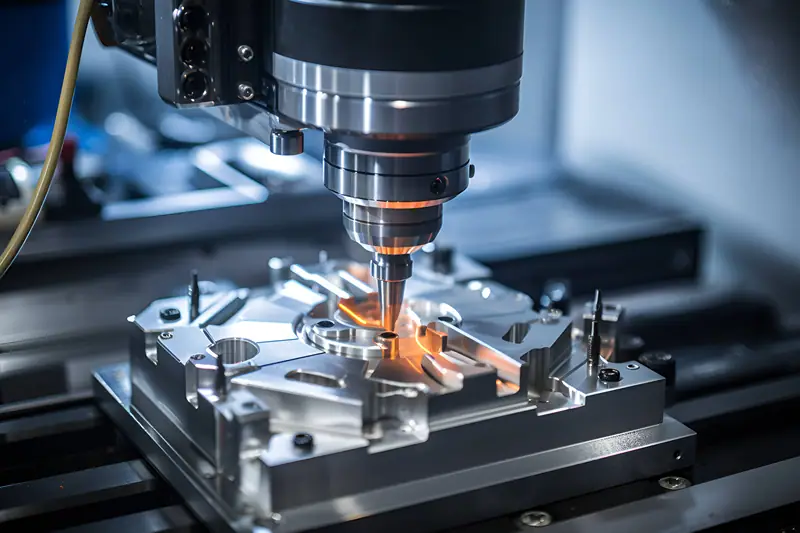
What's in the belly of a machine tool?
- design session
CAD drawings now young people play smooth, but masters have to keep an eye on: last year, a new design turbine blade runner forget to leave the retreat groove, almost 200,000 of the tool dry scrap! - the knack of programming
G-code looks like a book of days? Remember these three life-saving phrases:
- Slow roughing speed (800 rpm) Deep draft (2mm)
- Fast finishing speed (3000 rpm) Shallow draft (0.2mm)
- Curved surfaces must be opened for patching
- on-the-spot processing
Last month I took a rush order for a shaped heat sink, the material was a tough titanium alloy. I adjusted the cutting fluid concentration to 12% and used ceramic coated inserts to harden the tool life from 50 pieces to 120 pieces.
Master's unique tips
headache | folksy solution | serious program |
---|---|---|
Deformation of thin-walled parts | Padded kraft paper shock-absorbing | Segmented machining + thermal stress simulation |
deep hole drilling deviation | Make the center hole before changing the drill | Gun Drill + High Pressure Internal Cooling |
Poor surface finish | Hand throwing with sandpaper | Ball end cutter + helical milling |
Material selection mnemonic:
- For wear resistance: choose D2 mold steel
- To be lightweight: 6061aluminum
- To strength: 17-4PH stainless steel
- To save money: 45# steel tempering
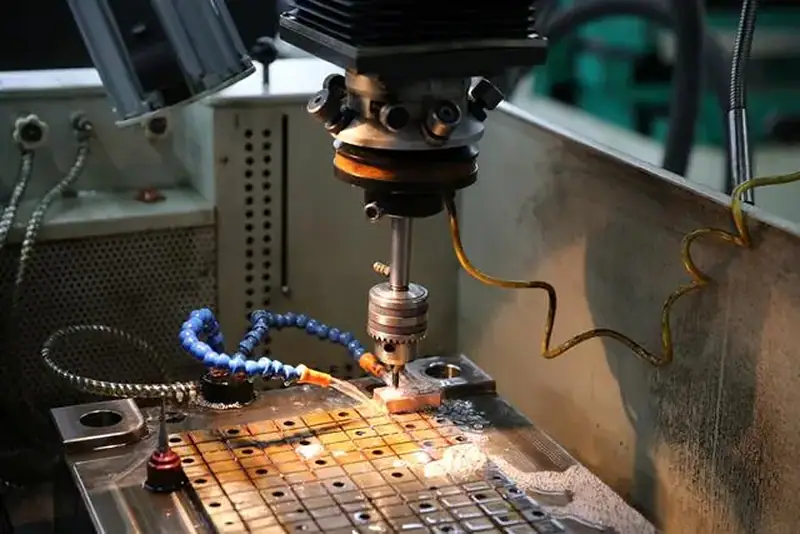
The potholes we've stepped in over the years
- Don't be greedy, you'll suffer big losses.: A time to buy cheap tungsten carbide cutter, the results of machining 316 stainless steel chipped, scratched the machine guide, the repair cost enough to buy three sets of genuine tools!
- Neglecting machine tool maintenanceOne time, I didn't change the guide oil for three months to meet a deadline, which resulted in the Y-axis backlash exceeding 0.03mm, and reworked the whole batch of 2000 pieces of shells.
- blindly chasing new products: Followed the trend to buy a smart tool setting instrument, the results of the workshop dust often false alarms, not as reliable as the teacher's plug ruler.
Advice from a veteran industry driver
- There are three things you don't do when you get an order.:
- Tolerances exceeding machine accuracy will not be made
- No material without a test report
- Don't do it if you're in a hurry to get your first batch
- Equipment Selection Guide:
- Small factories buy Taiwan machines (cost-effective)
- Middle factory with German-Japanese machine (stable accuracy)
- The rich go straight for the Swiss (heirloom level)
- Apprentice training tips:
A good seedling should keep an eye on these three:- Looking at drawings can reveal design flaws
- Listening to the sound of the machine tool to know the tool wear
- Touch the iron chips to determine whether the cutting parameters are reasonable
Teacher's private tools
- Three treasures of the workshop:
- Reddan powder (check flatness)
- Diamond pens (dressing wheels)
- Purple copper hammer (precision assembly)
- The baby in the cell phone.:
- Cutting Parameter Calculation APP
- Tool life management applet
- Machine Tool Fault Codes
The things you always ask me.
Q:What should I do about the old sticky knife in stainless steel processing?
A: Remember these three things - 300 RPM down, 5 degrees more front angle, and double the concentration of cutting fluid!
Q: Is 5-axis programming difficult to learn?
A: There are two more hurdles than 3-axis: tool axis control and collision check. It is recommended to simulate with VERICUT first, don't practice with real machine tools!
Q: Can domestic CNC systems be used?
A: wide number and Kainty now do not bad, regular processing is completely enough. But do precision mold or have to match the Fanuc system.
concluding remarks
CNC this line of work, three points rely on equipment, seven points rely on craftsmanship. Remember our teacher's words: work not in time, the machine white shaking; parameters adjusted fine, money counting hard. Ningbo Hexin's door is always open for you, with drawings to ensure that you go with a smile!