Aluminum alloy gravity casting common defects and preventive measures
Date: 2025-01-21 Categories: Blog Views: 1794
Gravitational casting Is in the casting process, the first solidified metal liquid due to thermal expansion and contraction volume contraction, need to rely on the upper part of the metal liquid gravity to supplement, complete the effect of shrinkage. Gravity casting solidification for the order of solidification, is the whole part in the solidification of the solidification in accordance with a certain order of successive solidification, relatively backward solidification position can be complementary shrinkage of the relatively forward solidification position, so that the final casting defects are concentrated in the last cooling parts (risers, gates position), to get qualified production castings. Gravity casting aluminum Sequence of solidification of wheel castings:
Rim - Spoke - Center hub (beveled) - Diverter cone - Sprue (riser)
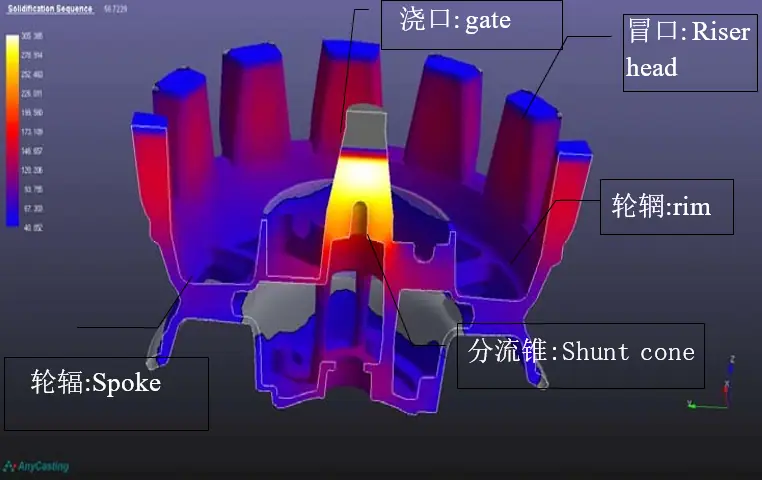
Casting process design parameters include machining allowances, process allowances (risers and other complementary shrinkage location), metal shrinkage (shrinkage coefficient) and pulling mold slope, cooling system (to ensure that the casting of the sequential solidification) and so on.
When the solidification sequence of the casting or process design parameters do not meet the product requirements, casting defects will arise, aluminum alloy castings common casting defects and preventive measures are:
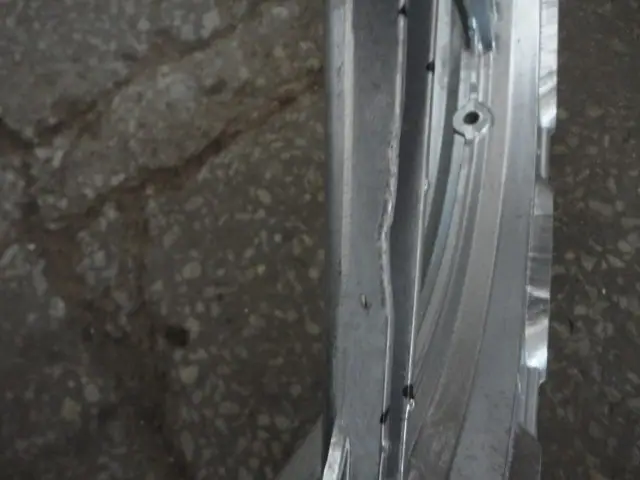
1. undercast
Characteristics: In the casting molding process, some parts of the filling is incomplete.
Causes of formation:
a. Aluminum liquid fluidity is not strong, high gas content in the liquid, more oxide skin;
b. Poor casting system, the inner gate cross-section is too small;
c. Poor mold exhaust conditions, poor exhaust, too much paint, mold temperature is too high resulting in high air pressure in the cavity and can not be discharged smoothly.
Preventive measures: 1, improve the liquid aluminum fluidity, especially refining and slagging, and appropriately increase the mold temperature or casting temperature (increase the casting speed, adjust the wall thickness margin, open the auxiliary bar channel); 2, increase the cross-section area of the inner gate; 3, improve the exhaust conditions, according to the adverse phenomena combined with the actual situation of the mold, increase the overflow groove and the exhaust line, the deep concave cavity to add the exhaust plugs, re-spraying the paint, so that the paint is thin and uniform, and wait for the mold to dry and close the production. And wait for the paint to dry before mold production.
2. crackles
Characteristics: the blank is damaged or broken, open into a long thin lines, irregular status quo, there are two kinds of penetration and non-penetration, under the action of the external force is the trend of development, cold, hot cracks, but the difference: cold cracks at the metal is not oxidized, hot cracks at the metal is oxidized.
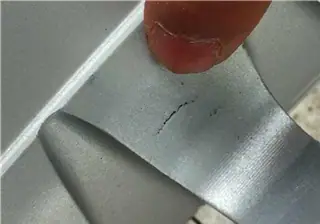
Causes of formation:
a. The casting structure is not reasonable, the contraction is hindered, casting round angle is small;
b. The ejector unit is deflected and unevenly loaded;
c. The mold temperature is too high or too low, and the mold opening process is seriously strained and cracked;
d. Harmful elements in the alloy exceed the standard, and the elongation rate decreases;
e. Poor venting;
Preventive measures: 1, improve the casting structure, reduce the mold wall thickness difference, increase the crack part of the rounded corner or arc radius; 2, correct the mold ejection system and the upper and lower mold clamping pins, bushings, to ensure that the ejection of the smooth; 3, adjust the mold temperature to the normal temperature to eliminate the inverted pull mold and unevenness of the phenomenon, and appropriately increase the mold pickup mold inclination; 4, control of the composition of the liquid aluminum, especially the composition of the hazardous elements; 5, repair the mold exhaust system to ensure that this part of the mold exhaust smooth. 5, repair the mold exhaust system to ensure that the part of the mold exhaust smooth.
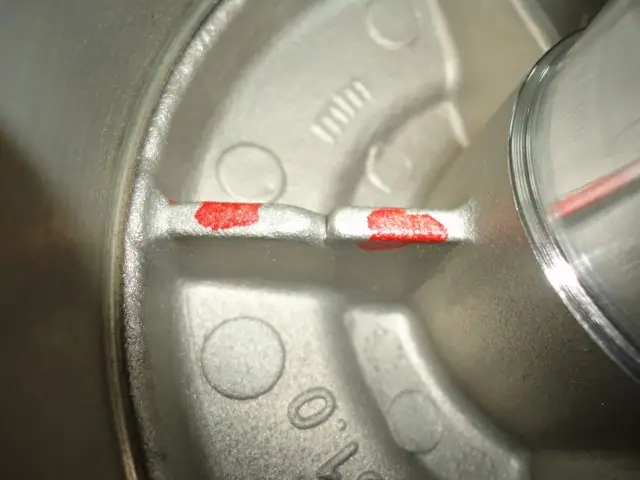
3. cold storage
Characteristics: Traces at the butt or lap of the fluid flow, with rounded edges of their intersections, and a tendency to continue to develop under the action of an external force.
Causes of formation:
a. Poor fluidity of aluminum liquid;
b. Liquid split strand filling fusion is poor or the process is too long to connect;
c. Liquid (mold) temperature is too low or insufficient exhaust;
Preventive measures: 1, appropriate increase in liquid aluminum temperature and mold temperature, check and adjust the liquid aluminum alloy composition; 2, reasonable arrangement of the overflow channel, increase the flow channel, shorten the process, so that the liquid aluminum filled with sufficient; 3, increase the casting speed or increase the temperature of the mold, improve the mold exhaust system.
4. (of beverages) sparkling
Characteristics: Under the skin of the casting, gas bubbles formed by the expansion of the aggregated gas.
Causes of formation:
a. The mold temperature is too high, and the temperature of the aluminum liquid is too high;
b. The filling speed is too fast, and the metal liquid is involved in the gas during the filling process.
c. The paint is gassed, sprayed too much, not volatilized before casting, and the gas is wrapped in the surface layer of the casting;
d. Poor venting;
e. Insufficient time to leave the mold, open the mold too early.
Preventive measures: 1, amend the mold cooling process, cooling the mold temperature to the normal working temperature; amend the melting process to ensure that the liquid aluminum temperature is normal; 2, slow down the filling speed, to avoid vortex package gas (can be controlled by the density of the screen, thickness, etc.); 3, the selection of a small amount of gas to the coating, spraying a thin and uniform layer of paint, thoroughly dry and evaporate after the mold; 4, to amend the time to stay in the mold, to ensure that the solidification of the full.
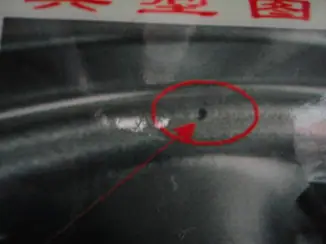
5. Air holes (gas and slag holes)
Characteristics: Regularly shaped holes with smooth surfaces formed by gases involved in the interior of the casting.
Causes of formation:
a. Aluminum liquid into the cavity, the positive impact, resulting in vortex; b. Charging speed is too fast, resulting in stagnant flow;
c. Poor exhaust; d. Mold cavity location is too deep; e. Too much paint, not completely dry and evaporate before filling;
f. Aluminum liquid refining is poor, not complete slagging;
h. There are debris in the cavity, and the filter does not meet the requirements or is improperly placed; i. The machining allowance is too large.
Preventive measures: 1, the use of conducive to the discharge of gas in the cavity of the infusion shape, to avoid the aluminum liquid first closed on the parting surface of the overflow system; 2, reduce the liquid aluminum filling speed (increase the density of the screen and other ways); 3, in the cavity of the last filling part of the overflow groove and the exhaust channel, and to avoid being closed by the liquid aluminum; 4, the deep cavity installation of exhaust plugs and the use of the mosaic structure to increase the exhaust; 5, with the wind gun to clean the cavity, and to re Spray paint, to ensure that the amount of paint thin and uniform; 6, liquid metal in addition to gas, immediately stripping slag, pouring, do not stay too long, in order to prevent re-absorption of gas, in addition, the alloy containing aluminum as far as possible without the supply of furnace melting; 7, to meet the needs of the case, reasonable adjustment of the product processing allowance.
6. Shrinkage
Characteristics: Irregularly shaped holes with rough surfaces caused by insufficient internal compensation during condensation of castings.
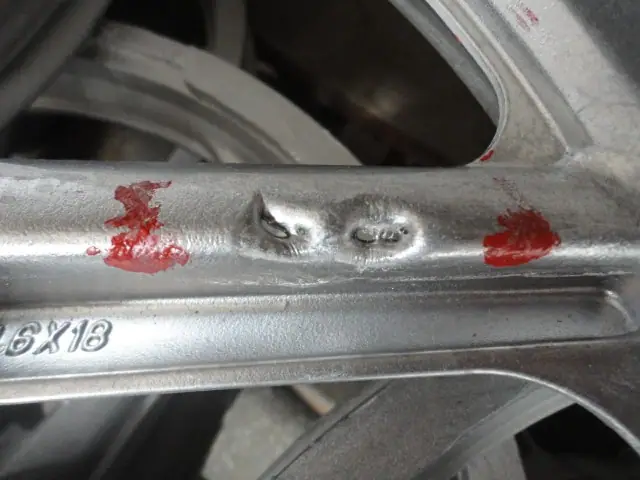
Causes of formation:
a. Aluminum liquid temperature is too high;
b. Uneven wall thickness of the casting structure, resulting in hot joints;
c. Smaller inner gate;
d. High local temperature of the mold.
Preventive measures: 1, in the case of meeting the pouring requirements, reduce the temperature of the liquid aluminum; 2, improve the casting structure, eliminate metal accumulation parts, slow transition; if you can not change the casting structure, the local impact of shrinkage of the "cold joints" parts, can be behind the perimeter of the drilling and milling slots, and then filled with adiabatic materials to increase the thermal resistance, can be adjusted Reasonable temperature field; 3, the local hot knot should be taken to forced cooling (can be used locally inlaid copper and other ways), in order to adjust a reasonable shrinkage temperature gradient; 4, increase the dark risers, in order to facilitate the pressure to better transfer; 5, adjust the thickness of the mold coating to control the local temperature of the mold.
7. decorative design
Characteristics: the casting surface is smooth streaks, visible to the naked eye, but not felt with the hand, the color is different from the normal basic metal grain, slightly rubbed with sandpaper that is not.
Causes of formation:
a. Charging too fast;
b. Too much and uneven amount of paint;
Preventive measures: 1. Reduce the filling speed; 2. Thin and uniform dosage of paint, following the principle of thin center and thick edge;
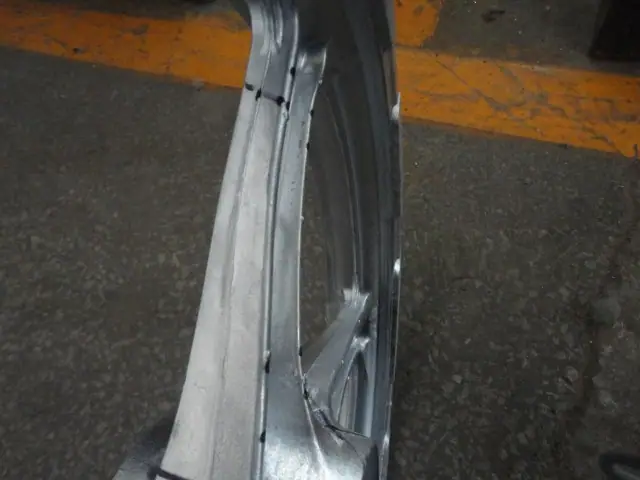
8.deformity
Characteristics: the casting geometry does not match the design requirements of the overall deformation.
Causes of formation:
a. Poor casting design, causing uneven shrinkage;
b. Open the mold too early, the casting is not rigid enough;
c, the mold pick mold tilt is too small, mold release difficulties;
d. Take and place the casting, improper operation;
e. The casting cools too quickly, causing deformation.
Preventive measures: 1, improve the casting structure, so that the wall thickness is uniform; 2, to determine the best time to open the mold, increase the rigidity of the casting; 3, to increase the casting pick mold slope; 4, take and put the casting, it should be light to take light to put; 5, after the mold is opened, the casting should be placed in the air to cool slowly.
9. Shrinkage
Characteristics: Shrinkage of aluminum alloy castings generally occurs near the inner sprue, the thick part of the riser root, the rim wall, the thick and thin transfer parts of the spokes, and the thin-walled parts with large planes. The fracture is gray when the casting billet is not treated, and the fracture is gray and light yellow or gray-black after heat treatment, and it is cloudy on the X-ray film when X-ray projection is made, and the serious ones are silk net shape.machiningThe parts show small and scattered pinholes after machining. Shrinkage in castings can be detected by X-ray, fracture and other inspection methods.
Causes of formation:
a. Poor riser shrinkage; b. Too much gas in the furnace material; c. Too high a temperature near the inner sprue; d. Too much moisture in the sand mold, and the sand core is not dried;
e. Improper spraying of mold coatings; f. Improper filling time of castings in the casting process; h. Too high temperature of aluminum liquid and too fast pouring speed.
Preventive measures:
1、Supplement the aluminum liquid from the riser part and improve the gate design; 2、The slagging and degassing treatment of aluminum liquid should be sufficient and thorough; 3、Spokes shrinking part set cooling system or put cooling ring block (such as the mold inlaid with copper, etc.), etc. to reduce the temperature of the mold near the inner sprue; 4、Control the moisture of sand to ensure that the sand core is baked and dry; 5、Choose the right paint, formulate the corresponding paint mixing irrationality, change the coating spraying Choose the right coating, make the appropriate coating blending irrational, change the coating spraying method (the closer the gate the thinner the coating), and provide professional training to the relevant personnel; 6, change the casting in the casting filling time, adjust the process parameters; 7, real-time monitoring of the liquid aluminum temperature, control the pouring speed (increase the screen or change the shape of the screen and other ways).
10. Mis-molding:
Characteristics: One part of the casting is misaligned with the other part at the parting surface, and a relative offset occurs.
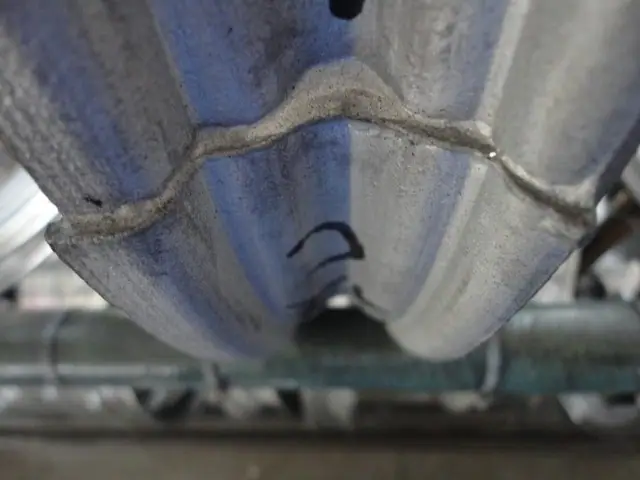
Causes of formation:
a, mold insert displacement (such as four slider did not close the mold in place);
b. Wear of mold guiding parts (wear of mold closing pins and sleeves);
c. Poor precision of mold manufacturing and assembly.
Preventive measures: 1, adjust the block, to be tightened; 2, the replacement of guiding parts; 3, correct the mold to eliminate errors.
Choosing the right gravity die casting service provider
Gravity casting is a simple and efficient metal casting process, but it still requires some knowledge and experience. Higher precision and quality can be achieved through specialized gravity casting techniques. Therefore, it is wiser to choose a professional service provider like Ningbo Hersin to outsource your casting needs.
At Ningbo Hexin, our team of engineers have many years of experience in gravity casting and are able to advise you on the most suitable casting process for your project. As an ISO 9001:2015 certified company, we are equipped with state-of-the-art casting equipment to ensure the production of high-quality parts. By uploading design files through our online platform, you will receive an accurate quote and technical analysis within 12 hours, helping you complete your project more efficiently.
Frequently Asked Questions and Answers
Causes of porosity defects?
Poor venting, poor refining of the aluminum liquid, or too fast pouring speed caused.
Aluminum alloy castings appear the cause of the pattern?
Patterns are generally caused by charging the mold too fast or spraying the paint unevenly.
Reasons for cracks in aluminum castings?
Cracks are usually caused by irrational design of the casting structure, improper mold temperature or excessive harmful elements in the aluminum liquid.
How to avoid undercasting in aluminum gravity casting?
Improve the fluidity of the aluminum liquid (increase the temperature of the aluminum water, add specific elements), increase the cross-section of the inner gate and improve the exhaust conditions of the mold (increase the scheduling plugs)