Die casting costing: how to calculate the price of die castings
Date: 2025-02-03 Categories: Blog Views: 893
In the manufacturing industry, die casting process is widely used in the production of all kinds of parts and components with its high precision and high production efficiency. However, the costing of die casting is often an important part of the enterprise for price setting and cost control. Correct understanding of the cost of die casting components, not only help to set reasonable prices, but also help enterprises optimize the production process, improve profits. In this paper, we will analyze the cost of die casting, provide detailed costing methods, and discuss how to optimize the cost to reduce the overall cost of die casting.
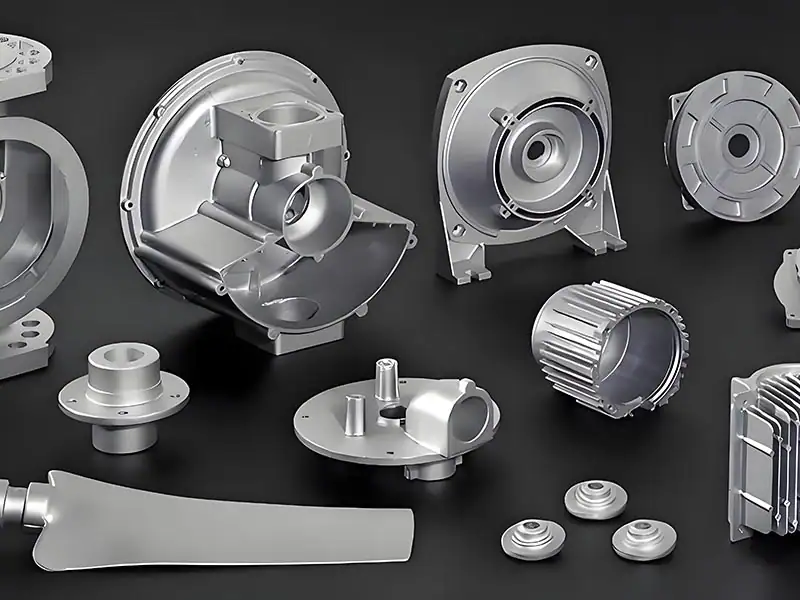
Is die casting costly?
The cost of die casting is indeed not low, which is the main reason why many companies hesitate to choose this process. Although die casting excels in precision, efficiency and complex parts manufacturing, its high cost, especially in small-scale production, often discourages enterprises. Therefore, Ningbo Hexin suggests that enterprises adopt die casting process when conducting large-scale production in order to amortize the cost. The following are a few key factors that affect the cost of die casting:
Three-dimensional metric modeling of die casting costs (in ADC12)aluminum(Shells as an example)
1. Dynamic control of material costs
- Base formula: C_m=(W_p×ρ×P_m×(1+15% loss))/yield rate
- Measured values of key variables:
- Material volatility: peak-to-valley ADC12 aluminum price difference of $4,200/ton in 2023 (see Figure 1)
- Thin-wall optimization: wall thickness of a motor end cap was reduced from 3.5mm to 2.8mm, and the material cost of a single piece decreased by 19%.
- Back material control: 30% back material added when the mechanical properties of 12% decline, need to balance the process window
2. Full-cycle mold cost management
Mould Type | Initial cost ($ million) | Lifetime (die times) | Individual assessment (dollars) |
---|---|---|---|
Single cavity H13 | 48 | 80,000 | 0.60 |
Four-cavity SKD61 | 126 | 150,000 | 0.21 |
Data source: Ningbo Hexin 2022 Mold Database |
3. Deconstruction of manufacturing cost elements
- Cost structure of a 2800T die casting unit:
- Equipment depreciation: $23/hour (depreciated linearly over 5 years)
- Energy cost: 18kW-h/module x $1.2 = $21.6
- Labor cost: 0.38 person/shift x $45/hour = $17.1
- Consumption of auxiliary materials: spraying agent 2.3 yuan / mold times
Six cost reduction engineering technology paths
Path 1: DFM Synchronized Engineering Optimization
- Case: A 5G base station filter housing
- Original program: 8 thick large sections (maximum wall thickness 8 mm)
- Optimized solution: topology optimization + follow-the-water path, weight reduction 23%
- Result: Reduction of material cost per piece by 16.5%, shortening of press-shooting cycle time by 18%.
Path 2: Mold Intelligent Design System
- Economic efficiency model for multi-cavity molds:
Q_Critical = (C_Multi-Cavity - C_Single Cavity)/(S_Single Piece - S_Multi-Cavity)
Four-cavity molds are economical when order quantity > 52,000 pieces
Path 3: Fine tuning of process parameters
- Pressure injection velocity versus porosity curve (Fig. 2):
- Optimal window: defect rate <2% at 3.8-4.2m/s
- For every 0.5m/s increase in speed, the mold wear rate increases by 37%
Path 4: Intelligent Production System
- Comparison of implementation effects:
| Metrics | Traditional Lines | Smart Lines
|--------------|----------|----------|
| oee | 68% | 89% |
| Unsatisfactory Product Rate | 4.2% | 1.8% |
| unit energy consumption | 3.6kW-h/kg | 2.9kW-h/kg |
Path 5: Precise Matching of Surface Finishes
- Cost gradient analysis:
- Native oxidation: $6-8/piece
- Micro-arc oxidization: $22-25/piece
- PTFE Coating: $35-40/piece
Note: Calculated by 300mm x 200mm surface area
Path 6: Collaborative supply chain innovation
- Aluminum liquid direct supply model for cost reduction:
- Traditional model: Aluminum ingot purchase + smelting Cost = raw material price + 1200 RMB/tonne
- Direct supply mode: liquid aluminum delivery Cost = raw material price +480 RMB/tonne
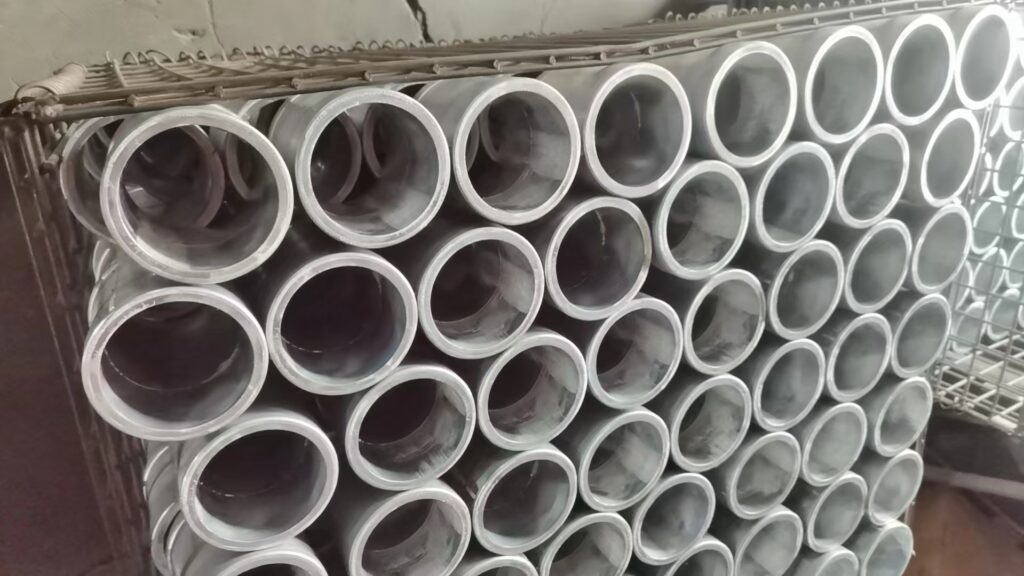
Third, die-casting process cost optimization strategy
1. Optimization of process parameters
- Injection speed and pressure matching:
- A new energy vehicle motor housing project showed that the pressure injection speed was increased from 3.2m/s to 3.8m/s, while the pressure injection pressure was adjusted from 850bar to 920bar, and the porosity was reduced from 2.8% to 1.2%.
- Optimization of benefits: $11.5 reduction in single-piece scrap losses
- Mold temperature control:
- Adopting zoned temperature control technology, the temperature difference of the mold is reduced from ±25℃ to ±8℃.
- Results: Mold life increased by 30%, single-piece cost-sharing reduced by $0.18
2. Intelligent upgrading
- Real-time monitoring system:
- The fluctuation of pressure injection curve is controlled within ±1.5%.
- Defect warning accuracy of 92%
- Benefit: Reduction of downtime losses by approximately $230,000/year
3. Lean production management
Human error rate is reduced by 67% breaks. In addition, proper storage conditions prevent damage to the mold during nonuse.
Quick Mold Exchange (SMED) implementation:
Mold changeover time compressed from 45 minutes to 18 minutes
Annual capacity increase of 15%
Standardized operations:
Operational standardization rate increased to 95%
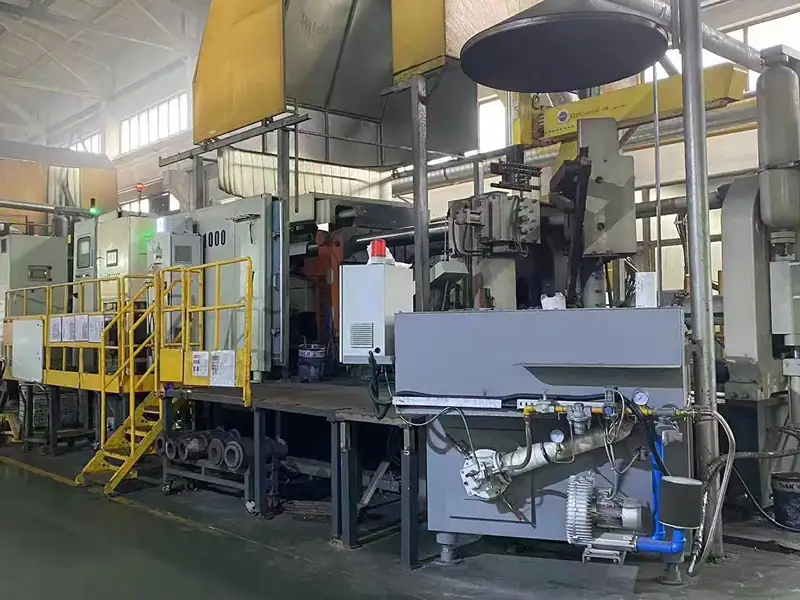
Frequently Asked Questions
Q1: How to evaluate the economy of die casting process?
- Adoption of the "break-even point analysis":
Q_critical = (mold cost + equipment share)/(unit selling price - unit variable cost)
Example: Q_critical = 12,500 pieces for a shell program, i.e., economic for order quantities > 12,500 pieces.
Q2: How to reduce cost for small quantity order?
- Recommended Programs:
- Adopt universal mold frame + insert design, reduce mold cost 40%
- Material utilization increased by 25% by selecting semi-solid forming process
- Case: a medical device shell (500 pieces) successful cost reduction 31%
Q3:How to extend the service life of the mold?
- Key Technologies:
- Surface treatment: TD treatment can improve mold life by 2-3 times
- Maintenance strategy: plasma cleaning every 5,000 mold cycles
- Measured data: An H13 mold life increased from 80,000 to 150,000 die cycles.
Q4:How to choose the optimal tonnage of die casting machine?
- Calculation formula:
P_Die Casting Machine = (A_Projection x P_Ratio Pressure)/1000
Among them:- A_Projection: Projected area of the part (cm²)
- P_specific pressure: aluminum alloy recommended 550-850bar
- Factor of safety: 1.2-1.5
Q5: How to reduce the cost of surface treatment?
Grading Strategy: Application Scenario Recommended Process Cost Range ($/piece) Common Appearance Partssandblast+Anodizing8-12Wear-resistant corrosion-resistant partsMicro-arc oxidation18-25Highly decorative requirementsElectrophoresis+spraying30-45
HERSHIN: Your Die Casting Partner
Despite the high cost of die casting, through reasonable optimization and choosing professional partners, companies can still control costs while ensuring quality. As an experienced die casting service provider, Ningbo Hersin is committed to providing customers with efficient and economical solutions.
With a team of professional engineers, we are able to provide customized mold design and manufacturing services according to customers' needs. In addition, we offer a wide range of material choices and surface treatment solutions to ensure that your products achieve the best balance between quality and cost.
As an ISO 9001:2015 certified company, we have advanced production facilities and strict quality control system. By choosing Ningbo Hexin, you can not only enjoy cost discounts of up to 30%, but also get fast delivery lead time. Simply upload your design files to our online platform and get a quote and manufacturability analysis (DfM) within 12 hours.
Faqs
Q1: Is die casting suitable for small lot production?
Die casting is more suitable for mass production because of its higher initial cost (e.g., mold manufacturing). For small-scale production, it is recommended to consider other processes such asmachiningOr 3D printing.
Q2: How to choose the right mold material?
The selection of mold material should be based on production scale, part complexity and material properties. For high volume production, it is recommended to choose high strength and wear resistant materials to extend mold life.
Q3: How much can automated production reduce costs?
Automated production can significantly reduce labor costs while improving productivity and product consistency. The exact cost savings depend on the scale of production and the degree of automation.
Q4: Is surface treatment necessary?
Surface treatment can enhance the appearance and durability of products, but not all parts need it. Companies should choose the right surface treatment according to the actual needs of the product to avoid unnecessary costs.
Cost Decision Support System Development Practices
Ningbo Hexin has developed an intelligent quotation platform based on the ISO 9001 system to realize:
- 24 hours quick response: upload 3D model → get DFM report + cost breakdown table
- Dynamic database support:
- Access to Shanghai Nonferrous Real-time Metal Quotes
- Integration of 2800+ sets of mold historical cost data
- Cost prediction accuracy: ±5% (validation sample N=137)
Process Selection in the Perspective of Engineering Economics
Order size (pieces) | Recommended Processes | Cost advantage range |
---|---|---|
<500 | CNC machining | Low 28%-45% |
500-3000 | Semi-solid casting | Low 12%-25% |
>3000 | High Pressure Die Casting | cost-optimized |
concluding remarks
Die casting cost control is a systematic project throughout the product life cycle. Ningbo Hexin through the original "cost three-dimensional map" analysis method, has successfully helped 37 enterprises to realize an average of 22.6% comprehensive cost reduction.