Rapid Tooling: An Innovative Solution to Accelerate Product Development and Manufacturing
Date: 2025-02-14 Categories: Blog Views: 1527
In this era of rapid technological change, the manufacturing industry is undergoing a profound transformation from "scale first" to "agile and efficient". Rapid Tooling (Rapid) Preface: China mold manufacturing dilemma and breakthroughs
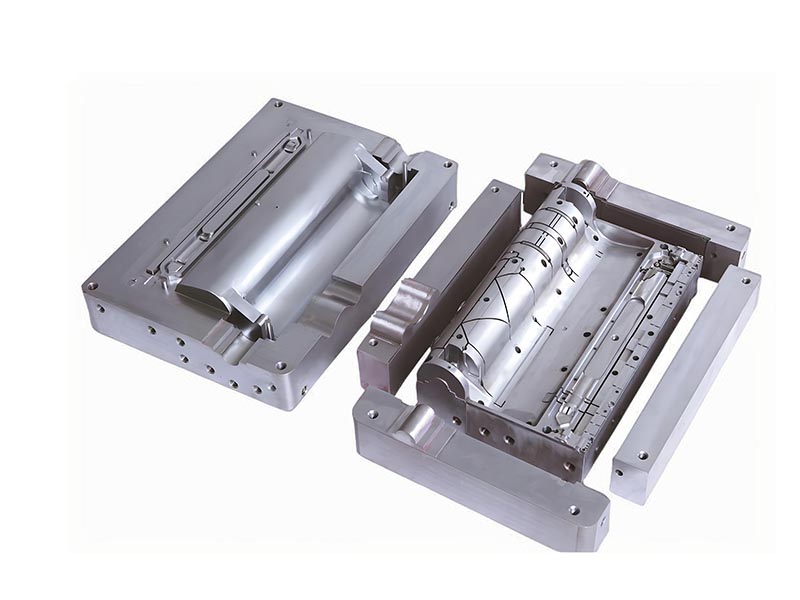
As an engineer who has been deeply engaged in the foundry industry for 23 years, I (He Xin) have witnessed the metamorphosis of China from a major importer of molds to independent innovation. In Ningbo this mold industry gathering place, we have experienced the traditional steel mold development cycle is long, the pain of trial and error cost is high, but also experienced the revolutionary breakthroughs brought by rapid mold technology. This paper will combine high pressure casting, Low-pressure casting and other practical application scenarios, revealing the role of rapid tooling in the aluminum Critical technical logic in component manufacturing.
1, the essence of rapid mold: not a compromise, but a precise match
1.1 Three major pain points of traditional molds
- time cost: A high pressure casting mold can take up to 8-12 weeks to develop.
- financial pressure: Automotive engine case molds cost more than 2 million yuan
- Trial and error risk: Gravitational casting One structural modification to the mold adds $150,000 to the cost
1.2 Technical orientation of the rapid tooling
This is achieved through the triple innovation of materials science, processing technology, and simulation technology:
- Cycle Compression 70%: Minimum 7 working days from design to mold testing
- Cost Reduction 50%-80%: Aluminum mold costs can be controlled at $80,000 to $150,000
- Precise matching of trial production quantitiesSupports pilot plant requirements from 500 to 30,000 pcs.
2、Four major casting process of rapid mold solutions
2.1 High Pressure Casting (HPDC) Scenario
High-pressure casting is the process of pressing molten aluminum alloy soup of 680-720°C into the mold cavity at a speed of 10-50m/s under a clamping force of 1600-2000T, the core challenge of which is that the mold needs to withstand extreme thermo-mechanical loads. The innovation in this scenario is reflected in the double optimization of material and structure: QRO90 hot-working steel is used to replace the traditional H13 steel, and its molybdenum-vanadium alloy composition increases the thermal fatigue resistance by 40%, which, together with the nitriding treatment on the surface (with a layer depth of 0.2-0.3mm), can prolong the life of the mold to more than 30,000 die times. Structural design of the modular insert system, for vulnerable areas (such as gates, ejector pin position) for local reinforcement, a company in Ningbo, the production of new energy motor end cover, through the rapid replacement of inserts to shorten the mold maintenance time from 8 hours to 1.5 hours. In terms of economy, the cost per piece is reduced from ¥18.6 to ¥7.3 for traditional molds, and the development cycle is compressed to 12 days, which is especially suitable for automotive structural parts projects with an annual output of less than 50,000 pieces.
Technical difficulties:
- The mold needs to withstand 1600T clamping force
- Aluminum alloy melt soup temperature up to 700 ℃
- Requirements for die life >50,000 cycles
Rapid Tooling Solutions:
- Material upgrades: Replacement of conventional H13 steel with QRO90 hot work steel
- Structural optimization: Core design with inserts for localized reinforcement of critical areas
- real time data5G base station heat sink housing produced by a company in Ningbo, with a mold life of 32,000 die cycles
2.2 Low Pressure Casting (LPDC) Scenarios
Low-pressure casting injects aluminum liquid smoothly into the mold cavity through 0.5-0.8MPa air pressure, which is especially suitable for the production of thin-walled parts requiring high densities. The breakthroughs of fast mold in this field focus on temperature control and pouring system optimization: the developed multi-zone mold temperature control system (±2℃ accuracy) with gradient cooling channel design, the yield of new energy battery tray produced by an enterprise in Ningbo has been increased from 81% to 95%. the pouring system designed by topology optimization technology has shortened the filling time from 9.2 seconds to 6.8 seconds, and increased the utilization rate of the metal by 12%. The quick mold solution adopts pre-hardened steel P20 + local copper alloy inserts, which reduces the mold cost to 45% of the traditional solution. It is especially suitable for the pilot testing of aerospace hydraulic housings and other complex structural parts, with a typical project delivery cycle of 15-20 days, supporting small batch production of 3,000-8,000 pieces.
technological breakthrough:
- Development of special mold temperature control system (±2℃ accuracy)
- Gradient cooling channel design
- case (law)A new energy vehicle motor housing project, product yield increased from 78% to 93%.
2.3 Gravity casting scenario
Gravity casting relies on the self-weight filling of metal liquid and is commonly used in the production of large and complex parts. Rapid mold in this field to achieve three major innovations: First, 3D printing sand mold and metal mold composite technology, through the SLS process to produce sand core (precision CT8 level) combined with the steel outer mold, so that the engine cylinder block trial period from 45 days to 12 days; Second, the heat balance control system, embedded in the mold key areas of the copper alloy inlays (thermal conductivity 380W/m-K), so that a marine diesel engine cylinder head of the The temperature gradient was reduced by 40%; Third, intelligent exhaust design, using porous metal vent plugs instead of traditional exhaust slots, which reduced the casting porosity defect rate from 15% to below 3%. Economic data show that the rapid mold program to reduce the average number of trial mold 2.3 times, a single trial mold cost savings ¥ 12-18,000 yuan, especially suitable for single-piece weight of more than 50kg of large construction machinery parts development.
Innovative practices:
- 3D printing sand mold combined with metal mold technology
- Localized inlay of copper alloy to improve thermal balance
- economic benefit: Reduce the number of mold trials by 40%, shorten the cycle time of pouring system optimization by 65%
3、Five core technologies of rapid mold
3.1 Material selection matrix
application scenario | recommendation material | Hardness (HRC) | Thermal conductivity (W/m-K) | cost index |
---|---|---|---|---|
high-pressure casting | H11+ Surface Nitriding | 48-52 | 24.3 | ★★★★ |
Small batch aluminum alloy | 7075 Aircraft Aluminum | 35-40 | 130 | ★★★ |
High Precision Structural Parts | S7 tool steel | 54-56 | 29.4 | ★★★★☆ |
3.2 Comparison of surface treatment processes
- micro-arc oxidation: Formation of 10-30μm ceramic layer, temperature resistance >800°C
- DLC coating: Reduced coefficient of friction to 0.1, increasing mold life by 3 times
- real-life exampleA turbocharger shell mold by the composite coating treatment, mold life exceeded 80,000 times
3.3 Lifetime prediction model
Based on Moldflow simulation data with field monitoring:
L=K× (σappliedσUTS)m×Nthermal
Among them:
- K: Material constants (0.8-1.2 for aluminum alloys)
- m: Fatigue index (6.5 for steel molds, 4.2 for aluminum molds)
- Examples of applications: Prediction error within ±8%
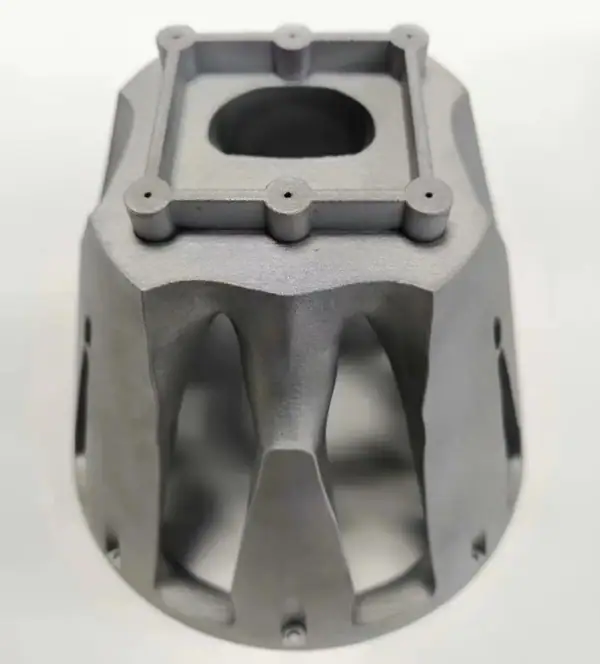
3D Printing Rapid Prototyping
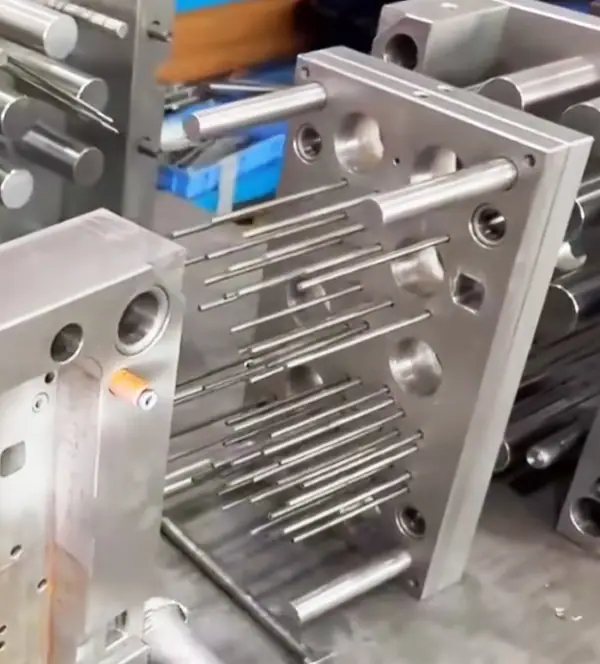
Rapid Tooling
4、The integration of 3D printing and rapid mold innovation
Followed by the shape of the cooling water channel is the core advantage of 3D printing molds: molds manufactured through SLM technology, the spacing between the cooling channel and the product contour can be controlled at 1.5-2mm (traditional drilling process ≥ 8mm), so that the injection cycle of a certain automotive grille shortened from 48 to 32 seconds, the deformation from 0.8mm down to 0.3mm.Gradient material printing technology can be achieved by the combination of the high hardness of HRC55 on the surface of the die core The combination of HRC35 high hardness on the surface of the mold core and HRC35 high toughness in the core, a drone bracket mold is treated in this way, and the impact resistance is improved by 60%. Economic analysis shows that for complex molds with more than 5 shaped waterways, the total cost of the 3D printing solution can be reduced by 42% compared with CNC, which is especially suitable for precision scenarios such as medical microfluidic chip molds. The current technical limitations lie in the maximum molding size (most devices ≤ 500mm) and post-processing requirements (key mating surfaces still require CNC finishing), but with the development of multi-laser technology, it is expected that the overall printing of meter-sized molds can be achieved in 2025.
4.1 Technological breakthrough points
- Conformal cooling channelsShorten injection cycle time by 23% and reduce deformation by 40%.
- Gradient material printing: Core surface hardness of HRC55, internal toughness of HRC35 maintained
- Case Data: A LED lampshade mold cooling efficiency improvement of 37%
4.2 Economic analysis
norm | Traditional CNC molds | 3D Printing Molds |
---|---|---|
development cycle | 18 days | 6 days |
Complex structural costs | 100% | 65% |
Modification costs | 30% | 8% |
5. Three practical recommendations for manufacturing enterprises
- Establishment of mold grading system:
- Class A molds (>100,000 molds): conventional steel molds
- Class B molds (10,000-50,000 molds): Fast steel molds
- Class C molds (<10,000 molds): 3D printing/aluminum molds
- Implementation of digital twins:
- Introduction of MAGMA simulation system at the mold design stage
- Installation of IoT sensors to monitor stress distribution during the production phase
- Building a rapid response mechanism:
- Stocking of standardized module banks (covering 80% common specifications)
- Establishment of regional collaborative networks (Ningbo has formed a 2-hour supply chain circle)
Conclusion: The next ten years of the mold industry
From the Ningbo mold cloud platform project we are implementing, rapid mold is being transformed to intelligent and service-oriented:
- Intelligent Quotation System: 5 minutes to generate a mold solution by entering parameters
- blockchain traceability: Full life cycle quality traceability
- Shared Mold Library: Reducing SME 30% Inventory Costs
Rapid ToolingFrequently Asked Questions (FAQ)
Q1: Can quick molds be used for mass production?
A: Scenario-based assessment is required:
- Aluminum alloy mold: Suitable for small batch <5000 pieces
- Pre-hardened steel molds: can support 30-50 thousand pieces
- It is recommended to incorporate a digital monitoring system to assess the mold condition in real time
Q2:How to control the dimensional accuracy of quick mold?
A: Recommended Programs:
- Machining stage: using 5-axis machine tools + in-line measurement (accuracy ±0.02mm)
- Mold trial phase: full inspection of critical dimensions using a Coordinate Measuring Machine (CMM)
- Mass production stage: sampling and testing every 500 molds
Q3:What are the innovative technologies for surface treatment of rapid tooling?
A: Three cutting-edge technologies:
- Laser cladding: repairing wear areas at a reduced cost of 40%
- Nanocomposite coating: coefficient of friction reduced to 0.08
- Plasma nitriding: surface hardness up to HV1200
Q4: What are the limitations of 3D printed molds?
A: Current major limitations:
Post-processing requirements: CNC finishing of critical mating surfaces is often required
Maximum size: Most devices are limited to 500 x 500 x 500mm
Material selection: currently the main support mold steel, aluminum alloy