Understanding CNC Machining: What You Need to Know
Date: 2025-02-01 Categories: Blog Views: 719
Computerized numerical control (CNC) is a manufacturing and processing technology that computesmachiningSoftware pre-written programs, in the CNC system through the computer control of the machine tool trajectory, machining speed and other parameters, control machinery and tools according to the command like a robot to carry out a series of complex mechanical movements, the workpiece accurately carried out by the processing, revolutionized the manufacturing industry. The global CNC machine tools market is expected to grow significantly, valued at more than $128 billion by 2028.The rapid growth of CNC surfaces the shift in manufacturing towards digitalization and precision.
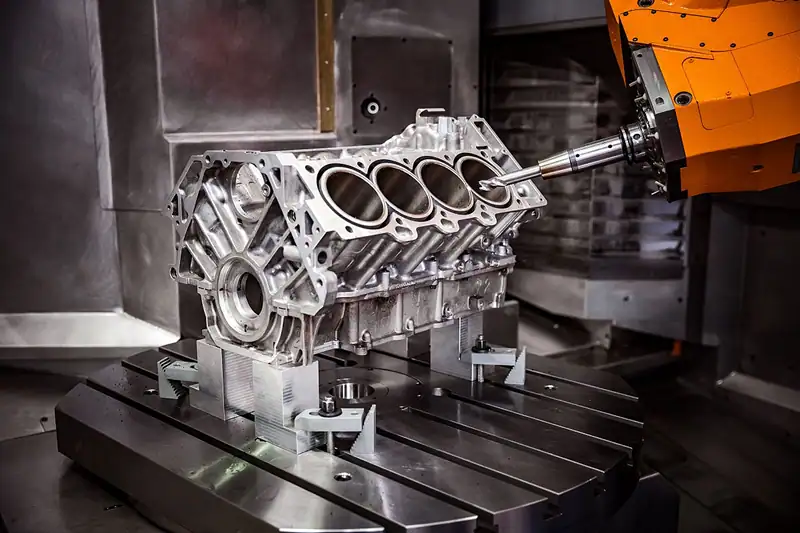
What is CNC?
Definitions and basic concepts
CNC machining, i.e. computerizednumerical control machining, is a manufacturing technology that precisely cuts and shapes materials through computer-controlled machine tools. You can think of it as an automated method of machining that is capable of performing complex mechanical movements according to a pre-written program. CNC machines control functions such as tool feed rates, spindle speeds, tool changers, and coolants through coded commands to efficiently accomplish complex designs that would be difficult to achieve manually.CNC machining not only ensures mass-produced quality, it also ensures extreme precision.
Historical development and evolution
The origins of CNC technology can be traced back to the 1940's. In 1949, MIT undertook a key research project for the U.S. Air Force that laid the foundation for the development of CNC technology. This innovation marked a major change in manufacturing, bringing unprecedented precision and efficiency.
By 1972, CNC machining technology was widely used worldwide. With the introduction of CAD (Computer Aided Design) and CAM (Computer Aided Manufacturing) software, CNC systems realized great advances. These technologies made complex designs possible and simplified the production process. Today, CNC machining has become one of the core technologies of modern manufacturing.
Today's CNC machines, such as VMCs (vertical machining centers), have revolutionized manufacturing. They offer unrivaled precision, efficiency and versatility. The capabilities of CNC machining have been further enhanced with advances in artificial intelligence and software technology, making them even more efficient and economical. Today, CNC machines are widely used in a variety of industries, including aerospace and medical devices, to produce a wide range of high-precision components.
The combination of CNC, CAD and CAM software has pushed manufacturing to the forefront of technology, leading to better working conditions, greater precision, less waste and more efficient production processes. As technology continues to evolve, CNC machining will continue to shape the future of manufacturing, bringing even more innovative applications and improvements.
How does CNC machining work?
Understanding how CNC machining works is crucial for those involved in manufacturing or design. This process achieves amazing precision by translating digital designs into physical objects. Here are the key steps in CNC machining.
CNC Process Overview
CNC machining begins with a digital design. Designers use specialized CAD software to create 3D models, and computers subsequently translate these designs into a series of instructions. These instructions guide the CNC machine to perform cutting, forming or milling operations. The entire process is highly automated, ensuring high precision and repeatability. This method is particularly suited to the production of complex parts.
Key stages of CNC machining
To fully understand CNC machining, it is important to understand its key stages:
- CAD software design
First, the designer creates a detailed 3D model of the part using CAD software.CAD software provides the flexibility to design complex shapes and structures and allows for adjustments to be made during the design phase. - Converting designs to CNC code
Once the design is complete, it is converted to CNC code (usually G-code). These codes are the "language" of the CNC machine and contain detailed information about tool movement, speed, cutting position, etc. The accuracy of the codes directly affects the quality of the final product. The accuracy of the code has a direct impact on the quality of the final product. - Machine setup and operation
After the code is ready, the operator needs to set up the machine, including fixing the material and configuring the machine parameters. After ensuring that all settings are correct, the machine will automatically perform machining tasks according to the CNC code. - Quality control and organization
After machining, strict quality control is carried out. Operators check the dimensions and surface quality of the parts to ensure that they meet the design requirements. If necessary, post-treatment processes such as polishing and painting are also carried out to enhance the appearance and performance of the parts.
CNC machining ensures high quality production through precise steps from design to quality control.
Types of CNC machines
In manufacturing, different types of CNC machine tools play an important role in material processing. Each type of machine tool has its unique features and is suitable for different application scenarios. Understanding these types of machine tools helps in choosing the most suitable equipment.
CNC Milling Machine
A CNC milling machine is a versatile tool used to cut and shape materials. It removes material from a workpiece by moving a rotary tool along multiple axes. CNC milling machines are suitable for tasks such as face milling, shoulder milling, and drilling, and are particularly good at creating complex parts with high precision. The aerospace and automotive industries use CNC milling machines extensively because of their ability to efficiently produce complex designs.
CNC lathe
CNC lathe is mainly used for turning operations. It is suitable for manufacturing symmetrical parts such as cylinders and cones by rotating the workpiece and shaping it using a fixed tool. CNC lathes offer higher accuracy and consistency compared to manual lathes. CNC lathes are commonly used in the medical device and electronics industries to produce high-precision parts.
CNC Plasma Cutting Machine
CNC plasma cutters are used to cut electrically conductive materials such as steel, aluminum and copper. It achieves precise cutting by melting and blowing away the material with a high velocity ionized gas (plasma). CNC plasma cutters are widely used in the automotive and metal fabrication industries due to their ability to perform complex cutting tasks quickly and accurately.
The main features of CNC plasma cutting machines:
- Precision cutting: Enables intricate designs and detailed cuts, reducing material waste.
- efficient production: Fast cutting speeds and shortened production lead times.
- versatility: Flexibility for a wide range of metal materials.
CNC Router
The CNC router is similar to a handheld router, but is controlled by a computer, enabling higher precision 3-D cutting. It is suitable for a wide range of materials such as wood, plastic and metal and is commonly used in the furniture manufacturing and signage industries. The CNC router is capable of producing intricate patterns, engravings and fine decorations.
Advantages of CNC machining
CNC machining offers significant advantages in modern manufacturing, making it the technology of choice for many industries. Below are the key benefits of CNC machining:
Precision and accuracy
CNC machining is known for its high precision and accuracy. With computer-controlled machine tools, parts can be produced to exacting design specifications, ensuring that every component meets requirements. This precision is especially important in industries such as aerospace and medical device manufacturing, where even small deviations can lead to serious consequences.
Efficiency and speed
The automation and efficiency of CNC machining allows it to dramatically reduce production time. CNC machines can run continuously without the need for human intervention, thus increasing productivity. In addition, CNC machines are able to perform multiple operations simultaneously, further increasing production speed. This enables manufacturers to deliver products faster and meet market demands.
Versatility and flexibility
CNC machining is extremely versatile and flexible. It is capable of handling a wide range of materials, including metals, plastics and composites, and is suitable for the production needs of different industries. For example, 5-axis milling machines are able to approach workpieces from multiple angles, reducing machining time and setup complexity. This flexibility makes CNC machining ideal for responding to diverse production needs.
By utilizing the precision, efficiency and versatility of CNC machining, manufacturers are able to significantly increase their production capabilities and stay ahead of the curve in a competitive market.
Frequently Asked Questions (FAQ)
1. What materials is CNC machining suitable for?
CNC machining can handle a wide range of materials, including metals (e.g., aluminum, steel, copper), plastics, composites, and more. The exact choice depends on the application scenario and performance requirements of the part.
2. How accurate can CNC machining be?
CNC machining is typically accurate to ±0.001 inches (about 0.025 mm), depending on the performance of the machine tool and the machining conditions.
3. Is CNC machining costly?
The initial investment is high, especially the cost of molds and equipment. However, CNC machining offers significant cost advantages in high-volume production because it reduces labor costs and material waste.
4. Is CNC machining suitable for small batch production?
While CNC machining is more cost-effective for high-volume production, it can also be used for low-volume production, especially if the part design is complex or requires high precision.
5. What is the difference between CNC machining and 3D printing?
CNC machining creates parts by cutting material, while 3D printing builds parts by stacking material layer by layer. cnc machining is better suited for high-precision and high-strength parts, while 3D printing is better suited for rapid prototyping and complex geometries.
6. How long does CNC machining take?
Machining time depends on the complexity of the part, the type of material and the performance of the machine tool. Simple parts may take only a few minutes, while complex parts may take hours or even longer.
7. Does CNC machining produce scrap?
Yes, CNC machining produces a certain amount of waste, especially during the cutting process. However, material waste can be minimized by optimizing the design and machining path.