Aluminum die casting mold design full analysis: from process to optimization of the practical guide
Date: 2025-02-15 Categories: Blog Views: 870
As a senior engineer of Ningbo Hexin, who has been deeply engaged in the casting industry for more than 20 years, I am well aware of the aluminum die casting mold The core position in the manufacturing industry. Whether it is automotive parts, 3C electronic products, or aerospace components, aluminum die casting process of high efficiency and precision are inseparable from the mold design of the subtle support. This article will combine practical experience, system analysis of aluminum die casting mold design points, technology trends and optimization strategy, for industry colleagues to provide a practical guide.
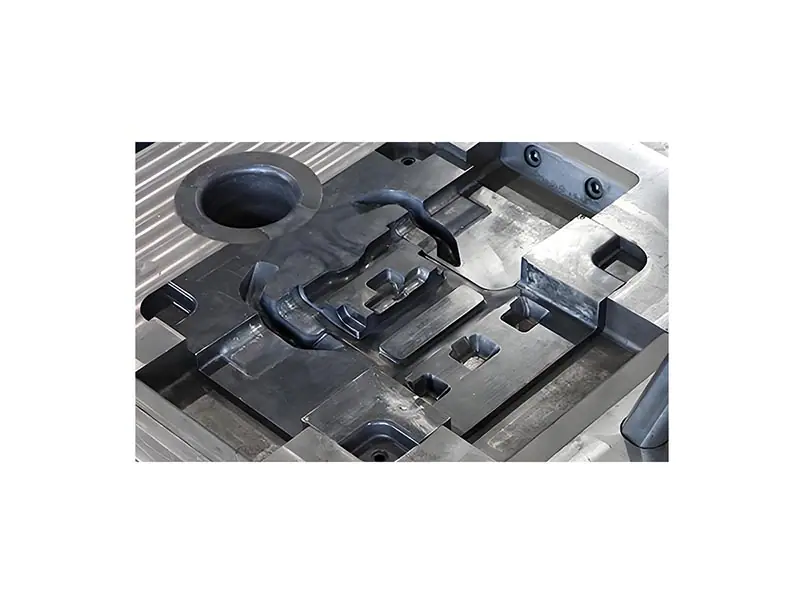
The core value of an aluminum die casting die: why it is the key to process success or failure
Die casting mold is not only the metal molding "template", but also production efficiency and product qualitydetermining factorThe importance of this is threefold. Its importance is reflected in three areas:
- Accurate precision
The cavity design of the mold directly determines the dimensional tolerance (usually ±0.1mm) and surface finish (Ra 1.6~3.2μm) of the casting. For example, in automotive engine block die casting, mold cooling system design if not reasonable, will lead to uneven local contraction, triggering porosity or deformation. - High production efficiency
A set of optimized multi-cavity mold can increase the production efficiency by more than 300%. Taking a new energy vehicle motor shell project as an example, after adopting a 4-cavity mold, the hourly output jumped from 15 pieces to 60 pieces, while the yield was stable at over 98%. - Cost Advantage
Mold life has a direct impact on the cost per part. By using H13 hot-working steel to make molds, through the surface TD treatment (thermal diffusion method), the life of the molds can be increased from 100,000 to 500,000 molds, which significantly reduces the cost of apportionment.
Five major types of aluminum die casting mold and selection strategy
Mould Type | Applicable Scenarios | cost cycle | Technical characteristics |
---|---|---|---|
Prototype Mold | Small lot validation (<500 pieces) | Low cost/2-3 weeks | 3D Printing +machiningcomposite process |
Rapid Tooling | Pilot production (500-5000 pieces) | Medium cost/4-6 weeks | Laser cladding additive manufacturing |
Unit molds | Multi-species and small batch | modular design | Quick change cavity inserts |
Production molds | High volume (>100,000 pieces) | High cost/8-12 weeks | Multi-slider structure + point cooling system |
Trimming Mold | Deburring and runner separation | necessary for | Hydraulic servo drive + precision guidance |
Suggestions for selection:
- High Pressure Die Casting(HPDC)Priority is given to production molds with vacuum systems to reduce air holes;
- Thin-walled complex parts(e.g. cell phone center frames) Rapid tooling is recommended, combined with localized squeeze casting techniques;
- Multi-variety flexible productionUnit molds can be used to reduce changeover time to less than 30 minutes.
The six golden rules of aluminum die casting mold design
- Fractal Line Optimization
The parting line should avoid critical functional surfaces. For example, a 5G base station radiator uses curved surface parting so that burrs are produced on non-contact surfaces, reducing post-processing costs. - Hydrodynamic design of flow channel systems
adoptionTapered cross sprue(Inlet 8mm → Outlet 4mm), together with the 30° inner gate angle, can realize the smooth filling of aluminum liquid and avoid the oxidation slagging caused by turbulent flow. - Heat balance control of cooling systems
The core part is embedded with beryllium copper inserts (thermal conductivity 210 W/mK), which can realize gradient temperature control with the mold thermostat (250℃ in the gate area→180℃ at the end) and shorten the cooling time by 20%. - Scientific calculation of demolding slope
Depending on the alloy shrinkage (about 0.6% for ADC12) and surface requirements, the outer wall slope is taken as 1°~1.5° and increased to 2°~3° for deep cavity parts. For example, the deep cavity structure of a UAV shell uses a 3° slope, and the ejection resistance is reduced by 40%. - Precise layout of exhaust and overflow tanks
A stepped overflow tank (depth 0.3mm→0.8mm) is set in the final filling area, and with the vacuum valve (vacuum ≤50mbar), the porosity can be controlled below 0.5%. - Advanced selection of mold materials
- Conventional parts: H13 steel (hardness 48-52 HRC)
- High wear resistance requirements: DIEVAR steel (with cobalt and molybdenum additions)
- Corrosion-resistant scenes: STAVAX ESR (mirror-polished to Ra 0.05μm)
Cutting-edge technology in the industry: Digitalization and Intelligent Empowerment Mould Upgrade
- AI simulation-driven design iterations
Through AnyCasting/MAGMA software, the whole process simulation of filling-solidification-stress can be completed within 48 hours, and the risk of shrinkage can be predicted in advance. A gearbox shell project optimized the gate position through simulation, reducing the number of mold trials by 3 times. - 3D Printed Conformal Cooling Waterways
The use of Selective Laser Melting (SLM) technology to manufacture shaped waterways has enabled the mold temperature difference to be controlled within ±5°C, significantly reducing thermal joints. After the application of a LED lampshade mold, the cycle time was shortened by 18%. - Internet of Things (IoT) Mold Monitoring System
Temperature/pressure sensors are implanted at critical locations in the mold to monitor the cavity surface condition in real time. When abnormal fluctuation of clamping force (>5%) is detected, a warning is automatically triggered to avoid batch defects.
Practical case: a new energy vehicle battery tray mold optimization
challenge:
- Product size 1200×800mm, average wall thickness 2.5mm, airtightness ≤ 0.5Pa-m³/s required
- Initial yield is only 65%, the main defects are cold segregation and deformation.
prescription:
- Balanced filling path with tangential feeding of double gates
- Mold core implanted with 12 sets of pulsed cooling tubes for dynamic temperature control
- Ejector system uses nitrogen gas springs to equalize the release force.
results-based:
- Yield improved to 92%
- Reduction of production tempo from 180s to 140s
- Mold life exceeds 300,000 die cycles
Frequently Asked Questions (FAQ)
Q1:How to evaluate the technical strength of mold suppliers?
- Key metrics: Cpk value of past cases (≥1.33), CAE analysis capability, completeness of trial mold report.
Q2:How to choose the surface coating for mold?
- Conventional: CrN coating (hardness 2200 HV)
- Highly wear-resistant: AlCrN (temperature resistant to 900°C)
- Mold release enhancement: DLC diamond-like coating
Q3: Best practices for mold maintenance?
- Daily: Check thimble lubrication (use high temperature grease NLGI grade 2)
- Every 5,000 molds: EDM repairs minor cracking
- Every 50,000 molds: Integral tempering treatment (550℃×2h)
concluding remarks
Aluminum die casting mold design is a combination of science and art, both require rigorous engineering calculations, but also rely on a wealth of practical experience. With the deep penetration of digital technology, mold industry is ushering in the "intelligent design - precision manufacturing - predictive maintenance" of the new paradigm. As a practitioner, the only way to take the lead in the triangle game of cost, efficiency and quality is to continue to embrace innovation.
For customized mold solutions or technical advice. Welcome to contact Ningbo Hersin Casting Team - With 20 years of experience, we empower your products with ultimate precision and performance.