Zinc die casting and aluminum die casting core technology comparison
Date: 2025-02-19 Categories: Blog Views: 633
In the modern manufacturing industry under the wave of vigorous development, die-casting technology with its high efficiency, high precision characteristics, in the automobile, electronics, aerospace and many other fields widely used. Zinc die casting and aluminum die casting as the two main stream of die casting process, like two bright pearls in the manufacturing industry, each exudes a unique light, has different advantages and applicable scene. For engineers, in product design and production, accurate selection of die casting technology is crucial, which is directly related to the product performance is excellent, cost control is reasonable, production efficiency can meet expectations. This article will be in-depth analysis of zinc die casting and aluminum die casting technology, from the material characteristics, process parameters, cost composition and other dimensions of the comparison, for engineers to provide a comprehensive, detailed selection decision-making reference.
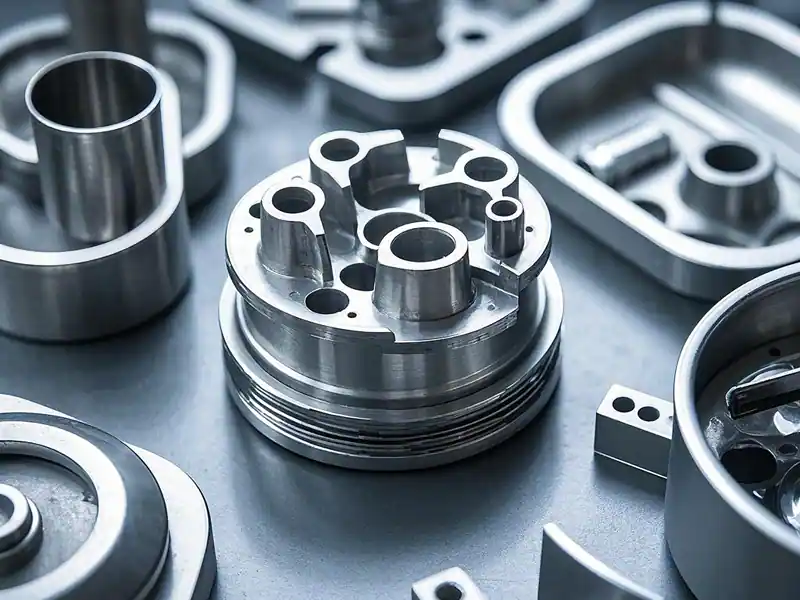
Technical Principles
(i) Principle of zinc die casting
The zinc alloy is heated to liquid state, using high pressure to quickly inject it into the cavity of the precision mold, and quickly cooled and solidified under high pressure to obtain zinc alloy die castings. Due to the relatively low melting point of zinc alloy, it is easier to realize liquid flow and fill the mold in the die casting process.
(ii) Aluminum Die Casting Principles
aluminumAfter heating and melting into a liquid state, through the die casting machine to apply high pressure, so that its high-speed filling of the mold cavity, and under pressure cooling crystallization, the formation of the desired aluminum alloy die casting. Aluminum alloy due to its own characteristics, in die casting need to pay attention to control the temperature and pressure parameters to ensure the quality of castings.
Core Parameter Comparison Table
comparison dimension | zinc die casting | aluminum die casting |
---|---|---|
Density (g/cm³) | 6.6-7.1 | 2.6-2.8 |
Melting point (℃) | 380-420 | 580-660 |
Tensile strength (MPa) | 220-420 | 160-310 |
Thermal conductivity (W/m-K) | 110-130 | 90-150 |
Mold life (die times) | 1,000,000+ | 100,000-200,000 |
Surface roughness Ra(μm) | 0.4-0.8 | 0.8-1.6 |
unit cost | high | relatively low |
Minimum wall thickness (mm) | 0.5 | 1.0 |
Cycle time (s) | 5-15 | 15-30 |
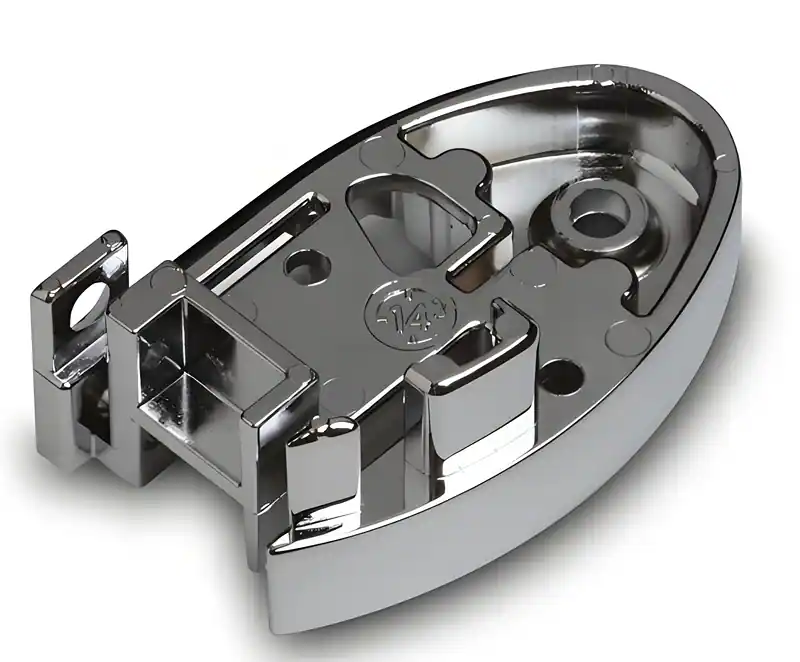
Analysis of key technology differences
1. Comparison of physical properties
- Zinc Alloy Advantage
The density is close to carbon steel (7.1g/cm³), and the impact strength is 2.5 times that of aluminum alloy. The fatigue life of an automobile steering knuckle was improved by 40% after adopting ZA-8 alloy. - Aluminum Alloy Advantage
With a specific strength of 120-150, it is irreplaceable in lightweight scenarios such as new energy battery trays.
2. Differences in process systems
- Melting Method
Zinc alloy using hot chamber die casting (furnace integration), energy consumption compared to aluminum cold chamber process is reduced by 35%. measured data show that the zinc die casting unit energy saving up to 42%. - Mold Economy
Zinc die casting mold life over a million times, a door lock mold continuous use for 5 years without repair. Aluminum alloy mold usually 100,000 times after the need for TD treatment repair.
3. Surface treatment characteristics
- zinc die casting
The cast surface reaches Ra0.4, and the pass rate of direct plating is more than 98%. A 3C product spindle eliminates the grinding process, and the yield rate is increased by 12%. - Aluminum die castings
Surface defects need to be treated by micro-arc oxidation, and the cost of adding anodizing to an automotive part increased by 181 TP3T.
Typical Application Scenarios
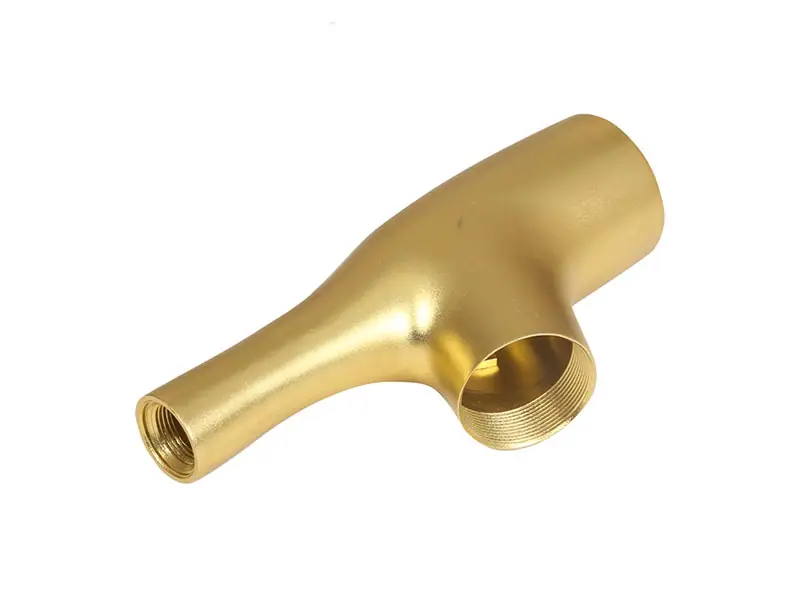
Zinc die casting preferred field:
- Ultra-thin structural components: USB-C port housing (0.5mm wall thickness)
- Highly corrosive environments: Marine hardware (passed 2000h salt spray test)
- High frequency production: 500,000+ annual production of bathroom fittings
- Electromagnetic shielding: 5G Base Station Filter Housing
Aluminum die casting applicable scenarios:
- Lightweight just need: Electric vehicle electric drive housing (weight reduction 40%)
- High-temperature service parts: Engine mounts (temperature resistant 150°C+)
- Complex heat sinks: LED lampholder heat sink tooth structure
- Conductive Functional Parts: Photovoltaic inverter housing
Cost-benefit analysis (200,000 pieces per year)
cost item | Zinc Die Casting Program | Aluminum Die Casting Solutions |
---|---|---|
Mold Investment | ¥800,000 | ¥1.2 million |
Material cost per unit | ¥6.2 | ¥4.8 |
Reprocessing costs | ¥0.5 | ¥1.2 |
Total annual cost | ¥1.34 million | ¥1.44 million |
ROI cycle | 9 months | 13 months |
Selection Decision Flowchart
graph TD
A[Requirement analysis] --> B{Wall thickness ≤0.8mm?}
B -->|Yes| C[Selection of zinc die-cast]
B -->|No| D{Operating temperature ≥120℃?}
D -->|Yes| E[Select Aluminum Die Casting]
D -->|No| F{Annual output ≥300,000 pieces?}
F -->|Yes| C
F -->|No| E
Clarification of technical misconceptions
Q: Is zinc alloy fully corrosion resistant?
A: It is indeed superior to aluminum in pH 4-10 environments, but titanium alloy is recommended for strong acid environments (pH<3)
Q: Can aluminum alloy be made into ultra-thin parts?
A: The new AlSi10MnMg formulation can achieve 0.8mm wall thickness, but the mold cost increases 35%