Mold flow CAE (fluid simulation technology) casting applications
Date: 2025-02-11 Categories: Blog Views: 3484
Nowadays, with the development of computer software, artificial intelligence, simulation and analysis software accuracy and credibility, the application of mold flow analysis software in the foundry industry is more and more common. cae simulation technology is widely used in the development of casting molds and product production. Numerical computation theory and GPU parallel technology breakthroughs, the modern casting process has entered the era of digital simulation and physical experimentation dual-wheel drive. This paper is based on the author's work in the high-pressure/low-pressure/ Gravitational casting With 23 years of engineering experience in the field, combining with typical process cases, it deeply analyzes the key points of the application of mold flow CAE technology in actual production.
Principles of casting simulation technology and engineering boundary conditions
The casting process is essentially a non-stationary heat and mass transfer process of molten metal under complex constraints, and its numerical simulation requires the establishment of a three-dimensional coupled model containing the Navier-Stokes equations, energy conservation equations, and solidification phase transition equations. It should be especially emphasized that the following key parameters must be paid attention to in engineering practice:
Interface heat transfer coefficient: measured data and software default value deviation up to 40%, need to use the heat flow probe for on-site calibration
Melt rheology: Die casting aluminum Significantly non-Newtonian fluid characteristics in the high-speed filling stage
Solidification shrinkage compensation: dynamic iterative calculations in conjunction with alloy thermophysical property databases are required
Casting simulation CAE mainstream software
Mold flow CAE technology is a fluid simulation technology based on computer technology, which uses mathematical models and algorithms to simulate and analyze fluid flow. In the field of casting, mold flow CAE technology can simulate the charging and solidification process of metallic fluids in the mold, including the flow rate, pressure distribution, temperature field changes, etc., to help engineers better understand and control the casting process.
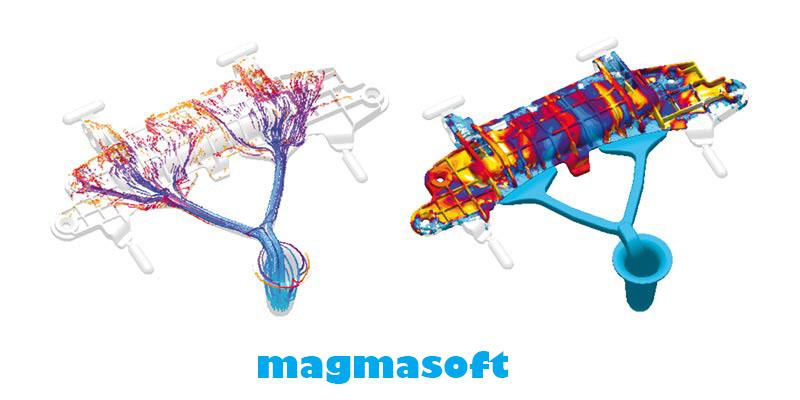
Magmasoft
MAGMASOFT software is a cae simulation software opened by a German company specializing in the foundry industry. The software can be the right cast (pour metal into a mold) Comprehensive simulation and analysis of mold filling, solidification, cooling, heat treatment, stress and strain. The simulation technology of the software makes the complex casting process digital, visualization, easier to be observed and understood by the foundry. At the same time, the calculation speed is faster, almost a working day. There is no problem with thin-walled parts (FLOW3D headache for thin-walled products), the software heat shrinkage results are accurate, but the software flow is not as good as flow3d and procast.
Typical applications: automotive steering knuckles Low-pressure casting process optimization
Advantage: Unique "dual-grid" technology effectively balances computational efficiency (3 million grids in 8 hours)
Limitations: deviations in flow prediction for complex casting systems need to be corrected manually
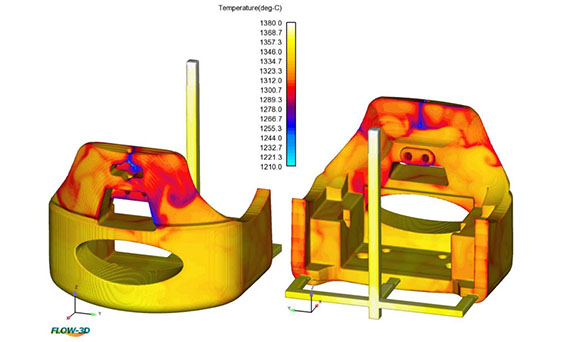
Flow3d
FLOW3D was developed in the United States and is widely used. It is a general-purpose software widely used in aerospace industry, metal casting, coatings, consumer products, micro inkjet heads, marine transportation, microelectromechanical systems, hydrodynamics, etc. FLOW3D has been used in die casting with very high accuracy, with reasonable parameter settings, and the flow accuracy can reach more than 90%. FLOW3D employs a very important fluid dynamics method, such as improved stability and unique free surface tracking (VOF) technology, which makes the results more realistic and more like the die-casting process. FLOW3D is easy to operate, with few interfaces and procedures, which is a good feature. The only disadvantage is that the calculation time will be longer, usually one day to three days. If the product is very large (500mm*400mm*300mm), the calculation will take nearly four days. And the requirement for mesh processing is also higher. Compared with the Korean software anycasting, everyone feels that the flow embodiment is more similar. But the accuracy of details is much higher than anycasting.
Case validation: a spacecraft titanium alloy casting coil gas defect prediction accuracy of 93%
Advantage of VOF algorithm: free surface tracking error <0.2mm for thin-walled parts
Calculated cost: a new energy vehicle motor casing (620 × 480 × 320mm) full process simulation took 98 hours
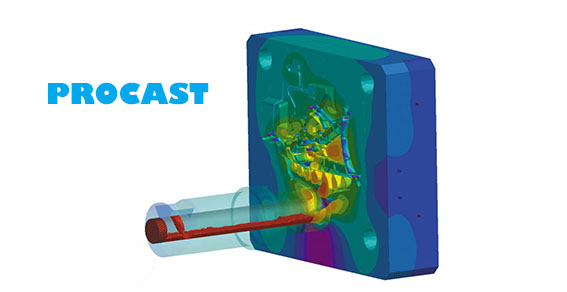
Procast
American Procast Software UES (UNIVERSALENERGY SYSTEM) company developed casting process simulation software. There are a lot of modules and it is fast, but the meshing is a bit anti-human, the parameters are more comprehensive, and it requires a lot of people to input. Compared to other CAE casting simulation and analysis software, driving a manual transmission is more automatic. In terms of flow and heat shrinkage, the software simulation results are relatively accurate, parameter settings in line with the reality can be achieved when the accuracy of 90% or more. Even higher.
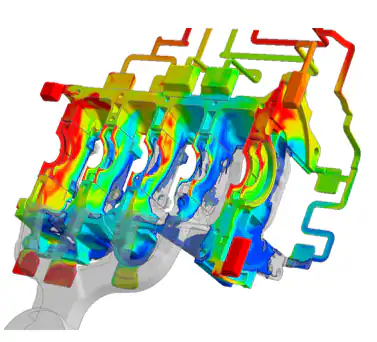
Anycasting
Anycasting is a new generation of advanced casting simulation software system based on Windows operating platform, specially developed for various casting process simulation system. After years of iterative upgrading, the software has a powerful Real Flow solver and three-dimensional processing technology can simulate a variety of casting processes, including die casting, low-pressure casting, sand casting, etc., to provide users with efficient, accurate and realistic casting simulation analysis results.
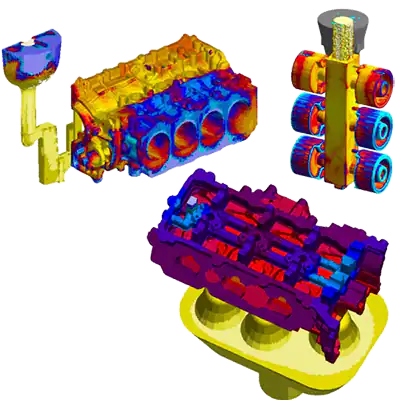
Huaji CAE
Huacasting CAE is an integrated software system, located in Huazhong University of Science and Technology, after more than 30 years of research and development, continuously improved and perfected in long-term production practice. Taking the numerical simulation technology of casting charging and solidification process as the core, it carries out process analysis and quality prediction for the molding process of casting, and assists the craftsmen to complete the process optimization of casting. The software simulates the charging and solidification process of castings on the computer, and predicts the defects that may occur in the casting process, such as air roll, slag entrapment, sand flushing, insufficient pouring, cold segregation, shrinkage, shrinkage and loosening.
Localization Advantage: Sand casting process kit covers 90% domestic foundry enterprise demand
Measured data: correlation between shrinkage prediction and industrial CT test results R²=0.87
Update: GPU Acceleration Module Increases Computing Efficiency by 400%
Typical engineering application scenarios and value quantification
Casting system optimization
In a high-pressure casting project of an engine block, it was found through Flow3D simulation that there was a problem of metal-liquid collision in the traditional fan gate. After optimized to a stepped pouring system:
Reduced roll gas defect rate from 121 TP3T to 2.31 TP3T
Mold Life Extension 30%
Solidification process control
Solidification simulation of railroad castings by adjusting the cold iron layout using Magmasoft:
Process yield increased from 68% to 82%
Radiation detection pass rate increased by 18 percentage points
Micro-organizational forecasting
Successful prediction of grain size distribution of an aluminum alloy wheel based on the secondary development module of Procast:
Error between measured and predicted values < 1.5 levels
Heat treatment process optimization saves energy 22%
Technology Development Frontiers and Engineering Recommendations
Multi-physical field coupling: the current urgent need to break through the real-time coupling algorithm of flow field-stress field-microstructure
Digital Twin Application: It is recommended that companies establish a closed-loop validation system of process parameters-simulation results-inspection data
Domestic software breakthrough: China casting CAE in the field of sand casting has reached the international advanced level, it is recommended to give priority to consider