Casting vs. machining: how do we choose?
Date: 2025-03-19 Categories: Blog Views: 578
As a core member of Ningbo Hexin casting technology team, I am in high pressure casting,Low-pressure casting,Gravitational casting I have been working in the field of casting and aluminum materials for more than 20 years, and have led the process development of hundreds of industrial-scale projects. Whenever customers ask the question of "how to choose between casting and machining", my answer is always: "There is no absolute advantage or disadvantage, only the most suitable combination of technologies for the scene." The following from the technical principles, practical experience and industry trends in three dimensions, in-depth analysis of the core differences between the two and the logic of choice.
What is casting?
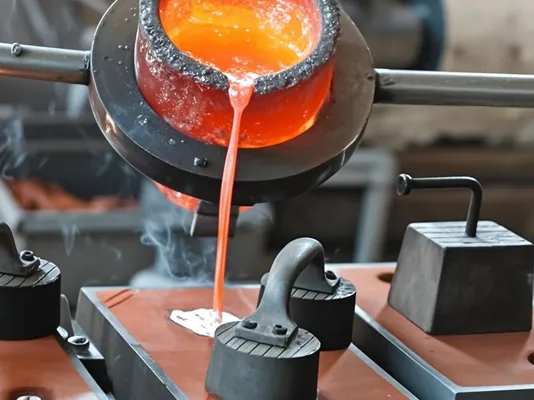
Casting is melting metal, manufacturing casting, and molten metal poured into the casting, solidification to obtain a certain shape and performance of the casting molding method. Casting and other parts forming process, compared with low production costs, process flexibility, almost independent of the size and shape of the part structure of the complexity of the limitations and so on.
As an important driver of human civilization, the history of casting technology can be traced back to ancient Europe in 4000 B.C. Gold castings unearthed at the Varna site in Bulgaria revealed the early beginnings of metal casting. During the same period, Mesopotamian craftsmen had already used copper alloy casting tools, and the Chinese bronze rituals of the Xia and Shang Dynasties showed the wisdom of the Oriental casting method by dividing the casting method, and broke through the iron casting technology a thousand years earlier than Europe. Technological exchanges across civilizations drove the iteration of crafts: Egyptian lost-wax methods shaped exquisite statues, China's Song Dynasty "Tian Gong Kai Wu" systematically documented clay casting, and the Islamic world integrated casting into the manufacture of precision instruments.
The industrial revolution in the 18th century became a turning point in the history of casting, coke ironmaking method and the combination of steam-powered die-casting machine, so that the cast iron parts to achieve large-scale production, support for railroads, textile machinery, and other industrial system construction. Modern casting more towards the field of high technology, the 20th century aluminum and magnesium alloy die casting boost the development of the aviation industry, 3D printing sand technology to break the limitations of the traditional process. Now the global casting annual output of more than 100 million tons, covering automotive, energy, medical and other key areas. China as one of the birthplace of casting, now with a global output of 40% above the industry leader, and through the green intelligent casting technology continues to lead the innovation. This 8,000-year-old technology is reshaping the foundation of modern manufacturing with the concept of digitalization and sustainability.
How does casting work?
Casting is an industrial technique whereby molten metal is injected into a specific mold cavity and left to cool and solidify to obtain a predetermined shape. The core process is divided into five main stages: firstly, a separable mold is designed according to the structure of the part; traditional sand casting uses quartz sand and binder to make a cavity with a pouring system, while investment casting uses ceramic shells or wax molds; then the raw metal is melted to liquid state in a high-temperature furnace.aluminum The metal needs to be heated to over 700°C, or 1400-1500°C for cast iron, and alloying elements are added to adjust properties. The pouring stage requires precise control of metal flow rate and temperature to avoid porosity or cold segregation defects, and modern vacuum die casting technology enhances mold integrity through negative pressure environments.
The solidification process determines the internal quality of the casting, engineers through the cooling system design to regulate the direction of grain growth, large castings such as marine diesel engine cylinder block often use sequential solidification technology to eliminate shrinkage holes. After the mold needs to be cleaned, cutting sprue and other processing, CNC machine tools for precision machining of key parts, aerospace parts also need X-ray flaw detection of internal defects. Contemporary casting has been integrated with digital innovation, 3D printing sand technology can be complex oil channel direct molding, simulation software can predict the trajectory of the metal flow in advance, and green casting through the old sand regeneration system will be the utilization rate of waste up to 95%, highlighting the depth of the integration of intelligent manufacturing and sustainable development.
Advantages of casting
For complex parts: Mold design allows for the forming of metal parts with hollow structures, curved surfaces or irregular contours, solving geometric complexities that are difficult to achieve with other processes.
Wide material compatibility: A wide range of metals and alloys can be processed, including recycled scrap or low purity raw materials, simply by ensuring that the melting temperature matches the heat resistance of the mold.
Scale cost advantage: After a one-time investment in the mold, a large number of identical castings can be produced repeatedly, and the cost per piece decreases significantly with the increase in batch size.
Highly adaptable in size: Sand casting supports the manufacture of large components, while technologies such as die casting are suitable for the molding of small and medium-sized precision parts.
Multi-material integration capabilities: Direct casting of composite structural parts (e.g. reinforced bushings) by pre-positioning metallic or non-metallic inserts in the mold.
Disadvantages of casting
Risk of internal defects: Fluctuations in process parameters or material problems can easily lead to defects such as porosity, shrinkage, cold segregation, etc. Strict quality control is required.
High manpower dependency: The traditional casting process involves multiple manual operations such as mold preparation, pouring, cleaning, etc., with a low degree of automation.
environmental burden: Smelting metal releases harmful gases and dust, and improper disposal of waste sand and slag may pollute the environment, so it needs to be equipped with environmental protection facilities.
What is machining?
machining(Machining) is a core technology for precision molding of metals, plastics and other materials through physical cutting, and is widely used in key aspects of modern manufacturing. The process utilizes equipment such as lathes, milling machines, CNC machine tools, etc., with drills, cutting tools or grinding wheels, to remove material allowance with millimeter or even micron-level precision, and transform the blank into a part that meets the design requirements. In automotive manufacturing, the crankshaft hole of the engine block needs to be turned and bored through multiple processes to ensure concentricity; the aerospace field relies on five-axis CNC machine tools to cut out the complex surfaces of the titanium alloy frame, and the tolerance can be controlled within ±0.005mm. Compared with casting or 3D printing, machining can achieve a higher surface finish, precision grinding can make the bearing raceway to achieve Ra0.1μm mirror effect, while processing hardened steel and other super-hard materials. However, traditional cutting will produce 30% material loss, in recent years, green processing technology through the micro-lubrication and high-speed cutting will enhance the efficiency of 40%, while the intelligent CNC system can automatically optimize the tool path, reduce energy consumption and costs. From miniature bone nails for medical devices to spindles for wind turbines, machining continues to support the demand for industrialized production of high-end equipment and precision devices with the precise characteristics of "subtractive manufacturing".
Advantages of Machining
high accuracy: Micron-level precision control can be achieved through multi-axis CNC technology, which is particularly suitable for complex parts with stringent dimensional requirements, such as turbine blades and medical implants.
Rapid response to small batch requirements: No need for complex mold development, directly processed from design files, significantly shortening the cycle time for prototyping and small-scale production.
Stable Repeatability: Relying on CNC programs and standardized tool paths to ensure consistent part dimensions and surface quality in mass production.
automated production: The CNC system automates the entire process, reduces manual intervention, reduces operating errors and improves the efficiency of continuous operation of the equipment.
Wide range of material adaptabilityCompatible with metals, engineering plastics, ceramics and composites to meet the diverse needs of different industries for material properties.
Disadvantages of machining
Limited internal structural processing: Complex internal features such as deep holes and cavities require multiple tool changes or customized tooling, making machining significantly more difficult and costly.
Size constrained by equipment: Due to the limitations of machine travel and spindle rigidity, it is difficult to realize overall precision machining of oversized or heavy workpieces.
Low resource utilization: The cutting process generates large amounts of metal shavings or dust and has a higher rate of raw material loss than additive manufacturing or near-net-shape processes.
Machining and casting: types and technologies
Processing type
mill: The use of rotary multi-flute tool cutting workpiece along the multi-axis direction, suitable for machining flat, curved surfaces and complex three-dimensional structure, widely used in mold cavities, shaped parts manufacturing.
turn: Highly efficient molding of rotary parts (e.g., shafts, discs and sleeves) through the combination of workpiece rotation and linear feed of the cutting tool, which can complete the machining of external rounds, internal holes and threads.
drilling: A spiral drill bit is used to rotate and penetrate the material to form a round hole, supporting through-hole, blind hole and step hole processing, often used for batch production of positioning holes for parts assembly.
hardened: Micro cutting of workpiece surface with high speed rotating grinding wheel to enhance dimensional accuracy and finish, suitable for tool edge sharpening and high-precision bearing raceway machining.
boring: Expanding the inner diameter of the pre-drilled holes by single-edged boring tools, precisely controlling the coaxiality and cylindricity of the holes, mostly used for precision internal cavity machining of engine blocks, hydraulic valve bodies, etc.
broach: The use of broaches with multi-stage tooth shapes for one-time molding of keyways, splines, or shaped bores, with high efficiency and stable surface quality, is suitable for the mass production of gears and couplings.
wire erosion: Cutting of conductive materials by the principle of galvanic corrosion allows the processing of complex contours of super-hard metals, and is particularly suitable for precision punching dies and aerospace engine blade molding.
planing: Tool linear reciprocating motion cutting plane or groove, suitable for large machine tool guide rail, base plate plane machining, easy to operate but less efficient.
EDM: Using pulse discharge to corrode conductive materials, it can process micro holes, complex cavities and cemented carbide molds, breaking through the hardness limitations of traditional cutting.
Each process is applied according to the combination of tool characteristics, trajectory and material adaptability, and together they cover the needs of the entire industrial chain from roughing to ultra-finishing.
Casting type
sand casting: The use of silica sand, clay or resin binder to make a one-time or semi-permanent casting, the formation of cavities through the model embossing, suitable for cast iron, cast steel and other metals with high melting point of diversified production, commonly used in the engine block, valves and other structural components manufacturing.
Die casting: Molten metal is pressed into a high-strength steel mold at high speed and quickly cooled and formed, specializing in the mass production of precision thin-walled parts made of non-ferrous metals such as aluminum, zinc, magnesium, etc., which are widely used in automotive parts, electronic housings and other products with high requirements for surface finishes.
investment castingThe wax mold is used to replace the solid model, wrapped with multi-layer refractory coating to form a ceramic shell, and injected into the metal liquid after melting away the wax mold, which can replicate the complex and fine structure of turbine blades, artwork, etc., and is especially suitable for small-lot customization of high-temperature alloy parts in the field of aviation and aerospace.
centrifugal casting: By using centrifugal force to make the liquid metal uniformly adhere to the inner wall of the rotary mold, we can form seamless tubes, hubs, and other rotationally symmetrical parts, combining both material densification and productivity, and are mostly used in the production of pipes and bearing rings.
Low-pressure casting: The liquid metal is smoothly injected into the closed mold through pneumatic pressure, reducing turbulence and oxidation, and forming hollow parts with high density requirements, such as aluminum wheel hubs and cylinder heads, with the advantages of both process stability and material utilization.
vanishing mold casting (TCM)Foam model is used to replace the traditional mold, the model is vaporized and filled with liquid metal during pouring, and can be integrated to form castings with complex inner cavities, which is suitable for single-piece or small batch production of mining machinery, pump and valve housings, and so on.
continuous casting (metallurgy): Liquid metal is continuously solidified and drawn through a water-cooled crystallizer to directly produce bars, plates or profiles, dramatically improving the molding efficiency of steel, copper alloys and other materials, and becoming a core process for large-scale production in the metallurgical industry.
Each casting technology is matched and applied according to mold characteristics, metal fluidity and production needs, forming a full range of manufacturing capabilities from art castings to industrial components.
The main difference between machining and casting
Tooling Features
Machining relies on milling cutters, drills, turning tools and other cutting tools to mold parts directly, while casting needs to build the molding space through the model making, mold preparation and other pre-processes, the tool chain covers the whole process from the wax mold carving to the sand preparation.
Precision control
Machining through the CNC system to achieve micron-level accuracy, especially good at high surface finish and complex geometric details; casting parts by the mold accuracy, metal shrinkage and other factors, need to use precision die casting or melt mold process to improve the consistency of the size.
Material compatibility
Casting materials are limited by the melting point and fluidity, sand casting suitable for cast iron, cast steel and other high melting point metals, die casting focus on aluminum, zinc and other low melting point alloys; machining can handle metal, engineering plastics, ceramics and other diversified materials, hardness range is wider.
design complexity
Machining is good at molding sharp edges, thin-walled structures and precision holes and grooves, but there are processing blind spots for deep cavities, internal curves and other closed structures; casting can be molded as a single piece with internal cavities, curved streamlined complex parts (such as engine blocks), but the details of the sharpness is low.
Production scale adaptation
Casting has a cost advantage in mass production, molds can be quickly copied after a one-time investment; machining without molds, through the program can be adjusted to respond to the demand for small quantities or single-piece customization, strong flexibility.
Part Performance
Machined parts due to the absence of solidification defects, mechanical properties more uniform; casting parts through directional solidification, heat treatment and other processes to optimize the grain structure, can be close to the strength of the raw material, but there may be microscopic pores or inclusions.
Prototyping Efficiency
Machining is based on direct cutting from CAD models, with prototypes completed within hours; casting prototypes need to go through mold development and metal pouring, with longer lead times, but investment casting can speed up the process by 3D printing wax molds.
Integrated cost structure
Casting high cost of pre-mold, suitable for scale dilution of the cost of a single piece; machining without mold costs, material loss and labor costs with the batch of linear increase, more suitable for small and medium-sized or high value-added products.
The two types of processes complement each other in manufacturing: casting solves the batch forming of complex components, and machining realizes the final correction of precision features, together supporting the complete manufacturing chain from blank to finished product.
Where is casting and machining used?
Industry Classification | Casting Typical Applications | Typical applications for machining |
---|---|---|
automobile manufacturing | Engine block, transmission housing, wheel hubs, suspension mounts | Transmission gears, piston rings, crankshaft journals, brake calipers |
aerospace | Turbine casings, engine blades, landing gear structural components | Titanium frames, fuel nozzles, flight control precision parts |
medical equipment | Medical bed frame bases, imaging equipment housings | Artificial joints, surgical instruments, micro-implants (e.g. bone nails) |
Energy and Power | Wind turbine hatch, nuclear reactor pressure vessel | Turbine blade tongue and groove, hydraulic spools, transmission connections |
Industrial equipment | Valve housings, pump bodies, heavy machinery bases | High-precision bearings, screws, mold inserts, automated robotic arms |
electronic communications | 5G Base Station Heat Sink, Aluminum Alloy Shell (Die Casting) | RF connectors, chip heatsinks, micro sensor housings |
rapid transit | Train brake disk blanks, rail fasteners | Wheelset machining, bogie precision bushings, signaling system parts |
Shipbuilding | Propeller castings, marine diesel engine cylinder liner | Propulsion shaft system, servo precision gears, hydraulic line fittings |
consumer goods | Cast iron pots and pans, door lock bodies, bathroom hardware | Smart home appliance gears, precision hinges, metal bezels for electronic products |
Construction & Infrastructure | Municipal manhole covers, steel structure connection nodes, bridge bearings | Building formwork fasteners, elevator guide rails, seismic support fittings |
Process Adaptation Logic:
- cast (pour metal into a mold)place particular emphasis onComplex one-piece moldingFor example, engine blocks with internal cavities, thin-walled die-cast electronic housings, and high-pressure-resistant valves;
- machiningspotlightPrecision Functional Components: e.g., high speed bearing raceways, micron-sized medical implants, precision runners for aviation fuel, etc.
The two types of processes are often used in tandem - casting to provide near-net-shape blanks, and machining to finish critical areas, together realizing a high-performance end product.
Which should I choose? Machining or casting
When deciding whether to use machining or casting for a manufacturing project, you need to make a comprehensive evaluation based on design characteristics, production goals, and resource conditions. Below is an in-depth look at the key decision dimensions to help you accurately match your process to your needs.
1. Production scale and scalability
- Select CastingIf the project requires long-term, stable mass production (e.g., automotive parts, structural components for household appliances), the cost per piece of the casting process decreases significantly as production volume increases. The reusability of molds gives them a natural advantage in large-scale production, especially for the rapid reproduction of standardized products.
- Select MachiningFor small batch customization (e.g. prototyping, aerospace special parts) or products that require frequent design iterations, machining does not require expensive tooling inputs and can quickly respond to changes in orders, flexibly adapting to small and medium-sized batch production.
2. Structural complexity of parts
- Select CastingIf the part contains internal cavities, thin-walled structures, multi-directional flow paths and other complex geometric features (such as engine block, hydraulic valve body), casting can be molded through the mold cavity in one go, to avoid the time-consuming problems of machining multi-processes.
- Select Machining: If the design focuses on external precision contours, microvia arrays, or ultra-fine surfaces (e.g., optical device bases, medical implants), the cutting accuracy of machining enables millimeter-level control of complex surfaces and is particularly suited to deep carving of open structures.
3. Accuracy and consistency requirements
- Select Casting: The dimensional accuracy of cast parts usually depends on mold quality and process control, and is suitable for medium-precision scenarios (e.g., pipe connectors, decorative components). For high-precision mating surfaces, a hybrid process of "casting + local finishing" can be used to reduce costs.
- Select MachiningWhen parts need to meet micron-level tolerances or tight fit (e.g., precision gears, semiconductor device cavities), machining can consistently deliver highly consistent finished products thanks to digital programming and highly rigid equipment.
4. Material properties and compatibility
- Select Casting: For metals with good flowability such as aluminum alloys, zinc alloys and cast iron. For recycled materials (e.g. recycled aluminum ingots), the casting process melts and reshapes them efficiently, significantly improving resource utilization.
- Select Machining: Compatible with a wider range of material types including high hardness alloys (titanium alloys, hardened steels), non-metals (engineering plastics, ceramics) and composites. Particularly suitable for processing materials that are difficult to melt mold or are heat sensitive.
5. Material utilization and sustainability
- Select Casting: Near-net-shape technology minimizes material waste and is particularly suited to the processing of precious or scarce metals. The carbon intensity of recycled aluminum casting is only 1/3 that of new aluminum processing, which is in line with the green manufacturing trend.
- Select Machining: The chips and trimmings generated during the cutting process may account for a large proportion of the weight of the raw material, and a waste recycling system is required to reduce environmental costs.
6. Speed of production and lead times
- Select Casting: The mold development stage takes some time, but the efficiency is extremely high after mass production is launched, making it suitable for projects with long lead times and stable output.
- Select Machining: Short cycle time from drawing to finished product for urgent orders or fast iterative prototyping, especially benefiting from the agility of digital manufacturing.
7. Comparison of cost structures
- Core cost items for casting: Mold design and manufacturing costs account for the majority of the initial investment, which is suitable for production volume cost dilution scenarios.
- Core cost items for machining: Equipment depreciation, tool wear and labor programming costs dominate, suitable for small batch, high value-added products.
8. Innovative practices in hybrid processes
For most industrial scenarios, a single process often cannot fulfill all needs.Recommended Strategies:
- Casting + Finishing: Utilizing casting to realize complex body structures and then CNC finishing of critical mating surfaces (e.g., automotive gearbox housings);
- Additive Manufacturing + Cutting: 3D printing of near-net-shape blanks to reduce machining allowances (e.g., aerospace shaped brackets).
Summary: Dynamic trade-offs and precise decision-making
- Preferred casting scenarios: High volume, complex internal cavity structures, material cost sensitive, green manufacturing oriented;
- Preferred machining scenarios: Small lot sizes, high-precision requirements, hard material machining, rapid delivery pressure;
- The golden combination of hybrid processes: Balancing efficiency and precision to achieve the optimal solution of cost and performance.
In Ningbo Hexin's practical experience, successful cases often originate from the dynamic evaluation of the above dimensions. It is recommended that enterprises establish a multi-departmental collaborative process review mechanism, and introduce third-party technical consulting when necessary, to ensure that the process selection of each project is scientific, economical and sustainable.
Faqs
Q1: How to choose casting or machining according to the production demand?
The choice of process needs to weigh the production volume, part complexity, material characteristics and precision requirements - casting is suitable for large quantities of complex structural parts (such as engine block), can be molded cavity but the accuracy is limited; machining to adapt to small quantities of high-precision needs (such as precision gears), can handle a variety of materials, but the efficiency with the complexity of the reduction.
Q2: Which process is more cost-effective?
Casting pre-mold cost is high but the cost of a single piece with the amount of decreasing, suitable for large-scale production (such as millions of pieces of electronic shell); machining without mold input, suitable for small and medium batch customization (such as aerospace parts), but the material loss pushed up the cost of emerging technologies, such as 3D printing sand is to break the traditional cost of the border.
Q3: How does material selection affect process decisions?
Casting is limited by the fluidity of the metal (e.g. aluminum die casting) and the melting point (e.g. cast iron).sand casting), while machining can cut super-hard alloys (e.g., titanium alloys) and engineering plastics, but it is prone to chipping on brittle materials (e.g., ceramics) and requires special tools and processes.
Q4: How do you handle highly complex parts?
Casting through the melt mold technology one-piece molding complex internal cavity (such as turbine blades), machining with five-axis CNC cutting precision surfaces (such as impellers), but the closed structure needs to be a combination of processes: casting blanks + machining finishing (such as cylinder boring), to achieve a balance between function and cost.
Q5: Which process is more environmentally friendly?
Casting faces high energy consumption melting and waste sand disposal challenges, requiring old sand regeneration systems; machining needs to deal with cutting fluid contamination and metal chip recycling, but green technology (dry cutting, micro-lubrication) gradually reduces the environmental impact, and both require closed-loop production optimization.
Q6: Is it necessary to combine two processes?
Synergistic applications become the norm: casting provides near-net-shape blanks (e.g., gear castings), machining completes high-precision features (e.g., tooth grinding); additive manufacturing + CNC finishing breaks through the traditional limitations to meet the ultra-complex needs of aerospace parts and so on.
Q7: Which one is faster to choose for prototyping?
Machining delivers metal/plastic prototypes in hours with the advantage of straight CAD cuts, while casting combined with 3D printed wax molds reduces the cycle time from weeks to days for functional prototypes that require verification of material properties or structural strength.
Core logicCasting heavy "molding efficiency", machining heavy "precision and control", selection needs to be around the cost, time, performance of the three dimensions, most of the scenarios need to be complementary to the two rather than alternative.