Die-casting aluminum alloy ADC12 products shot blasting skinning reason analysis and solution recommendation
Date: 2025-04-07 Categories: Blog Views: 550
This paper systematically analyzes the die castingaluminumThe material properties of ADC12 are correlated with the blasting process, and a multi-dimensional solution is proposed for the frequent blasting skinning problem in the industry. The article firstly clarifies the direct influence of ADC12 chemical composition on material properties, revealing the intrinsic correlation between fluctuations in the content of silicon, copper, magnesium and other elements and the fluidity, strength and corrosion resistance of the alloy. Based on the principle of shot peening process, the article analyzes the quantitative role of core variables such as shot parameters and ejection speed on the surface treatment effect, and points out that there is a common shortcoming in the current industry that only focuses on adhesion but ignores the standardization of surface quality. Through mold flow analysis, process parameter optimization and experimental verification, innovatively build a whole chain improvement system from material source control to mold design and equipment maintenance, combined with the case of motor shells to prove the effectiveness of the optimization of the exhaust channel, the adjustment of energy storage pressure and other key measures. The research not only provides quantifiable technical path for ADC12 shot blasting quality improvement, but also looks forward to the new direction of process optimization based on big data AI technology, which is of practical guidance significance for promoting cost reduction and efficiency in die casting industry.
Material properties of the die-cast aluminum alloy ADC12
1. Chemical composition
Major elements and their roles
ADC12 mainly contains silicon (Si), copper (Cu), magnesium (Mg), manganese (Mn), iron (Fe), zinc (Zn), aluminum (Al). Among them:
Silicon: the content is allowed to be 9.5~11.5%, if it is lower than 9.5%, there will be poor alloy fluidity and incomplete filling of the product, if it is more than 11.5%, it will be easy to have excessive segregation or to form lamellar crystals with ferro-aluminum, which will destabilize the alloy organization and make the product loose;
Copper: The content is allowed to be 1.5~3.5%, if it is lower than 1.5%, there will be a decrease in the strength and hardness of the product, if it is higher than 3.5%, there will be a decrease in the corrosion resistance;
Magnesium: the content is 0.1~0.3%, if the magnesium content is lower than 0.1%, there will be a decrease in the strength and hardness of the product, if higher than 0.3%, it will lead to defects such as thermal cracking of the product during die-casting;
Manganese: the content of 0.2 ~ 0.5%, if lower than 0.2%, there will be alloy grain coarseness, tensile strength and yield strength at the same time reduce, if higher than 0.5%, there will be alloy hard brittleness increase, difficult to process, easy to brittle fracture;
Iron: content in 0.6 ~ 1.2%, if lower than 0.6%, easy to stick mold, the formation of product strain deformation, if higher than 1.2%, there will be alloy due to hard and brittle crack; (iron and silicon at the same time ultra-high, prone to the formation of lamellar silicon-iron-aluminum crystals, resulting in inter-crystalline corrosion, the decline in alloy strength)
Zinc: content ≤ 1.2%, so zinc can be absent from the ADC12 alloy (difficult to remove when refining other alloys), and if present, must be less than 1.2%.
In addition, the matching ratio of refurnace material is also very critical, if the refurnace material is too much, it will cause the product crystallization grain coarseness, and the strength and hardness of the product will be reduced.
In summary, the chemical composition (percentage content) of the alloy basically determines its mechanical properties and also governs the appearance and internal crystalline organization of the product.
2、Physical Properties
ADC12 aluminum alloyDensity approximately 2.7 g/cm³(math.) genusMelting point 580~620°C; It is important to note that the values of these physical properties can vary depending on factors such as specific compositional differences and production processes.
ADC12'scoefficient of thermal expansionRelatively large, this characteristic is somewhat related to the blasting process.
3、Mechanical properties
The mechanical property indexes of ADC12 aluminum alloy are usually as follows:
Tensile Strength: about 228~296MPa;
Yield strength: about 140~170MPa;
Brinell hardness: about 70~95HB.
Elongation: 1~3%
Specific performance indicators may also vary depending on factors such as compositional differences and production processes.
Overview of the Shot Peening Process
1、The principle of shot blasting
The working mechanism of shot blasting equipment
The working mechanism of shot blasting consists of the following main parts:
Shot Storage and Transportation Systems: Shots are usually stored in specific hoppers and transported to the blast machine by means of a conveyor (e.g. screw conveyor);
Shot blasting machine: this is the core component of the shot blasting equipment, shot blasting machine inside the high-speed rotation of the impeller, the impeller has a number of blades, when the impeller rotates at high speed, the blades will drive the projectile accelerated and ejected at high speed;
Workpiece Conveyor System: Used to convey the workpieces to be treated to the blasting area and send them out after the treatment is completed, the commonly used conveyor methods are crawler, hook, roller conveyor and so on;
Dust removal system: in the blasting process will produce a large amount of dust and impurities, dust removal system through the fan generates negative pressure, the dust will be sucked into the dust collector for filtration and purification, in order to ensure that the working environment is clean and in line with environmental requirements.
Shot blasting is a surface treatment technology, the principle is mainly the use of high-speed rotation of the impeller will projectile (usually steel shot, steel wire cut shot, etc.) to the surface of the workpiece to be processed at a very high speed; in the process of shot blasting, the projectile has a large kinetic energy impact on the surface of the workpiece to produce a strong impact and scraping effect, this impact can remove the surface of the workpiece oxide, rust, dirt and other adhesions, and at the same time in the surface of the workpiece At the same time in the surface of the workpiece to produce compressive stress, so that the surface is strengthened. Improve fatigue strength and resistance to stress corrosion; specifically, the impeller in the shot blasting equipment in the motor drive high-speed rotation, the projectile is accelerated by the impeller thrown in a specific direction, when the projectile impact on the surface of the workpiece will cause the surface of the workpiece material to produce plastic deformation and fall off, so as to achieve the effect of cleaning and strengthening.
The effect of shot blasting depends on the material of the projectile, shape, size, speed, blast angle, as well as shot blasting time and many other factors, different workpieces and processing needs to choose the appropriate parameters of the shot blasting process, in order to achieve the desired quality and efficiency of treatment.
2, shot blasting process parameters
Shot blasting pellet material and size: for ADC12 aluminum alloy shot blasting pellet material commonly used 304 stainless steel cast steel shot or steel wire cut shot; the diameter of the pellet is 0.2 ~ 0.6 mm;
Blasting speed: The blasting speed used for ADC12 aluminum alloy is usually 50~70 m/s;
Shot blasting angle: usually 30~75 degrees;
Shot blasting time: according to the size, shape and surface condition of the workpiece, generally 5~15 minutes;
Shot flow: according to the shot blasting equipment and workpiece, usually in the range of 90~280 kg / min;
Setting principle: in actual production, through testing and quality inspection to determine the most suitable for the workpiece being shot blasting process parameters, in order to obtain the desired surface treatment effect and avoid peeling, wrinkling and other issues, to obtain the ideal surface treatment effect with the smallest parameters is the highest pursuit of shot blasting parameter settings, but also one of the ways to maximize the benefits.
3, shot blasting process in die-casting aluminum alloy ADC12 products in the application of the current situation
Common practices in the industry
The purpose of workpiece shot blasting is only to increase the adhesion of baking paint or plastic spraying requirements, the use of coarse shot blasting pellets, shot blasting time is shorter, shot blasting skinned workpiece using rework grinding treatment, no fine investigation of the causes of problems such as shot blasting skinned, as well as the development of improvement programs;
Strict requirements on the surface quality of the workpiece after shot blasting, such as color difference (the standard is silver-white), skinning (not off the irregular pieces suspended in the surface of the product), wrinkles (shot blasting surface wrinkles), deformation and other defects in the reception of the lower limit standardization; so that the die-casting process of all the products caused by pores, loosening, cold segregation, flow marks (stagnation) and other defects in the analysis of the causes, and the development of measures to improve the wheelblasting machine, some of the features of upgrading and continuous optimization. Some of the functions of the shot blasting machine for upgrading, continuous optimization, the pursuit of shot blasting surface quality to achieve the goal of 0 defects.
Problems and challenges
High-quality qualified ADC12 aluminum alloy shot blasting parts are high-quality qualified die-casting billet after the completion of the processing of shot blasting equipment, if the shot blasting parts appear skinning and other problems, the end of the reverse analysis of the reasons: shot blasting equipment is intact? → Is the use of shot blasting particles appropriate? → Is the set blasting time, speed, flow rate appropriate? →Is the die-casting blank grinding in accordance with the requirements? → Does the die-casting blank have appearance defects (cold segregation, flow marks, spots, pores, cracks, etc.)? →Die casting production, die casting machine and peripheral equipment is intact? → Are the process parameters (ejection pressure, ejection speed, pouring temperature, coating concentration and spraying amount, etc.) optimal? →die casting moldDoes the pouring system, cooling system, ejector mechanism, cavity finish, mold release slope, hardness of cavity parts, rounded corners of cavities, etc.) meet the requirements? → Is the movable mechanism of the die-casting mold running stably and reliably? → Is the process parameter of melting process (mixing of return material, melting temperature, refining temperature, refining agent dosage ratio, nitrogen setting pressure and flow rate, etc.) optimal? →Is the chemical element of ADC12 in accordance with the requirements?
In the actual production, it may be analyzed that there is a problem in one link, but when solving its problem, it must be considered comprehensively whether it will bring other problems, so it needs team communication and collaboration, and it needs multi-faceted argumentation and multiple experimental verification.
03.
Analysis of the causes of shot peening of die-casting aluminum alloy ADC12 products
1. Source-ADC12 material factors
Silicon (Si) content ≥ 11.5%: Iron (Fe) ≥ 1.2%, resulting in excess chemical synthesis, as well as lamellar organization, loose surface organization, in the impact of shot blasting and scraping, skinning phenomenon will occur;
Magnesium (Mg) ≥ 0.3%: manganese (Mn) ≥ 0.5%, zinc (Zn) ≥ 1.2%; produce hard brittle surfaces or cracked surfaces, in the impact of shot blasting, it will be seriously peeled off lack of material;
Copper (Cu) ≤ 1.5%: The surface strength and hardness of the product is insufficient, under the impact of shot blasting and scraping, concave deformation and skinning or wrinkling will occur;
Ratio of furnace return material ≥ 50%: melting slag removal and degassing are very difficult, physical properties and mechanical properties will be reduced, die casting products are difficult to achieve a good surface (porosity and impurities present in the product fill end surface), shot blasting is easy to skin.
2, die-casting mold design factors
Mold straight pouring channel cross-section and cross channel cross-section ratio is not appropriate, the total cross-section of the cross channel is larger than the cross-section of the straight pouring channel, in the cross channel at the negative pressure volume of gas, gas into the mold cavity to increase the load of the exhaust channel, the gas is easy to remain in the product, the formation of air holes, the distribution of air holes to the shallow surface of the product, the shot blasting will be skinned or blistering;
Multi-strand branch sprue filling, sprue spacing is too large, two strands of sprue in the middle of the formation of reflux trapped gas; two or more strands of sprue filling direction hedge, the formation of turbulence, the product surface will have air holes (commonly known as stagnant tumors), by the impact of shot blasting force, it will be skinned;
Mould design circulating cooling waterway, reached the end of the sprue filling, resulting in the mold temperature is always in a low state, the product shallow surface appears cold segregation, flow marks, pitting and other loose conditions, the impact of the shot blasting force, it will be a serious skinning;
Mold design of the exhaust channel can not meet the exhaust demand (exhaust speed greater than 350 m / s), the location of the overflow channel is not at the end of the filling or defective position, resulting in exhaust and slag exhaust is not smooth and trapped air, the product filling the end of the location of the shallow surface layer of air holes, shot blasting force impact, skinning;
Mold cross sprue and inner gate cross-section is too small, the filling pressure is blocked, increasing the pressure transfer difficulties, the product is loose - the strength and hardness is not up to the requirements of the impact of blasting force, it will be skinned or deformed.
3, die-casting machine and peripheral equipment factors
Die casting machine type plate parallelism and flatness (≤ 0.5) error is large, the clamping is not solid, resulting in the parting surface run aluminum water, casting pressure depletion, product strength and hardness decline, the impact of shot blasting force, product skinning
Eccentricity between the ejection center of the ejection mechanism and the center of the ejection hole of the fixed model plate, resulting in stagnation of the ejection punch, pressure depletion, loss of product strength and hardness, impact of shot blasting force, and skinning of the product;
Excessive clearance between the punch and the melt cup, backrun aluminum water during compression injection, resulting in punch stagnation, pressure depletion, product strength and hardness decline, impact of shot blasting force, product peeling.
Die casting around the vacuum machine-vacuum valve clogging, vacuum failure, the product trapped gas, the product surface appears cold segregation, flow marks, pitting and other loose conditions, the impact of the shot blasting force, it will be serious skinning;
Point cooler failure, cooling water pressure is insufficient, the flow is insufficient, resulting in overheating of the mold heat concentration parts, the product should be part of the heat contraction and oxide skin layer, the impact of shot blasting force, the product skinning.
4、Die-casting process setup factors
Insulation furnace temperature setting is low (≤ 640 ° C), easy to precipitation of silicon, easy to fill the aluminum liquid liquid mobility is reduced, easy to fill the product is not full, the product shallow surface layer of the cold segregation, flow traces, pockmarks and other loose conditions, by the impact of shot blasting, will be a serious skinning;
The casting pressure and filling speed are set low, the product strength and hardness decreases, the blast force impacts, and the product peels;
Filling high-speed start point location is not set properly: 1. High-speed start point location before the melting cup of air will be involved in the cavity, the exhaust channel exhaust load increases, the gas is difficult to exhaust, filling the end will produce air holes, shallow surface of the product air holes by the impact of shot blasting, peeling; 2. High-speed start point location after the slow speed of the liquid aluminum into the cavity, it will be quickly cooled, the product will be the formation of interlayer (cold septum), loose, the impact of shot blasting force, the product peeling; 3. High-speed start point location after the aluminum liquid into the cavity, it will rapidly cool, products will form interlayer (cold septum), loose, shot blasting force impact. Product skinning;
Spraying time is set too long, resulting in low mold temperature (185~230°C) or heat imbalance, the product will appear cold segregation, flow marks, pockmarks and other loose conditions, by the impact of shot blasting force, it will be serious skinning;
High-pressure point cold set water time (standard for the end of the pressure injection delay 3 ~ 8 seconds) is too long, resulting in mold local temperature (185 ~ 230 ° C) is low or heat imbalance, the product will appear cold segregation, flow marks, pockmarks and other loose conditions, by the impact of shot blasting force, will be serious peeling;
Vacuum machine vacuum start time and end time is not set properly, resulting in vacuum failure, cavity trapped gas, the product shallow surface layer of air holes by the impact of shot blasting force, will be serious skinning;
5, die casting blank grinding factor
Flying edges of die casting blanks and multiple materials are not cleaned and polished, and the residual flying skin after blasting - skinning;
Die casting blanks sanding excessively, the blank surface of the dense layer sanding off, shot blasting force impact, will be skinned.
6, shot blasting particle size factors
The diameter of the purchased blasting pellets is inconsistent and larger than the process setup diameter size, resulting in an increase in blasting force, which impacts the product to peel;
7, shot blasting process parameter setting factors
Setting the blasting speed too high, the impact force increases, resulting in product skinning;
Set the shot blasting time is too long, continuous impact scraping, resulting in product dense layer peeling, product skinning;
Set the shot blasting projectile flow is too large, the impact of scraping increased, resulting in product dense layer peeling, product skinning.
8. Environmental factors
The blasting environment is not ventilated and the temperature is high, resulting in softening of the product surface and peeling of the blast.
Recommended solution for shot peening of die-cast aluminum alloy ADC12 products
1. Material improvement measures
The chemical composition of the purchased raw material ADC12 is taken as close as possible to the permissible intermediate value;
Reclaimed material is graded and upgraded to secondary reclaimed material, which is used in conjunction with new material, and the percentage of reclaimed material is reduced.
2, die-casting mold casting row and cooling system optimization measures
Through the mold flow analysis, find the sprue filling dead corner, negative pressure air turbulence, the end of the intersection and other bad filling mode, optimize the sprue filling mode, reduce the dead corner reflux, reduce the negative pressure air volume, increase the overflow exhaust settings;
Through the mold flow analysis, find the oxidation slag parts, thermal nodes, add the mold point cooling device (mechanism), so that the mold heat balance to improve.
3, die-casting machines and peripheral equipment inspection and maintenance
System pressure of the die casting machine;
Clamping force of die casting machine - four Goring columns with balanced force;
Accuracy of the pressure, speed, and punch running position of the die casting machine's ejection system;
Air compressor, vacuum machine, high pressure spot cooler, holding furnace, spraying machine, etc.
4、Optimization of die-casting process parameters
Holding oven temperature setting 660°C±10°C
Die casting high-speed start point in the theoretical high-speed start point on the basis of 60 ~ 100mm in advance, test die casting production blanks sent to the shot blasting sample verification, to determine the optimal location;
Casting pressure according to the average wall thickness of the product recommended value to take the upper limit (1 ~ 3mm - casting pressure 45 ~ 60MPa; 3 ~ 6mm - casting pressure 60 ~ 80MPa; 6-10mm - casting pressure 80 ~ 110MPa).
5、Die-casting blanks cleaning and polishing essentials standard upgrade
Die casting blank cleaning and polishing standardization, must be polished and cleaned up after the sample parts to take to the shot blasting verification, no flying edge peeling, polished and cleaned up the standard sample parts can be sealed, released, and strictly according to the sample parts for polishing and cleaning up die casting blanks.
6, shot blasting machine spot check maintenance
The blast machine must meet the settings for each process parameter;
The data displayed on the blast machine's monitor must be accurate.
7、Selection of shot blasting pellets and new and old collocation
Shot blasting pellets must be screened with a special sieve, larger than the process requirements of the diameter of the pellets screened out by the pellet supplier needs to be reground before use, and need to be re-screened; the proportion of new pellets added not more than 60%.
8, the curing of the parameters of the blasting process
Shot blasting process parameters need to be first according to the relatively low blasting speed and shot blasting projectile flow, shot blasting time as short as possible, after the test shot verification, to confirm that the product meets the quality of the shot blasting (no skinning, no color difference) in order to solidify the process parameters.
9、Temperature control of the blasting environment
The blasting environment must be kept dry and ventilated, and the temperature controlled within 30°C.
Experimental validation cases
ADC12 Die Casting - Motor Shell Blank Shot Peeling Problem List
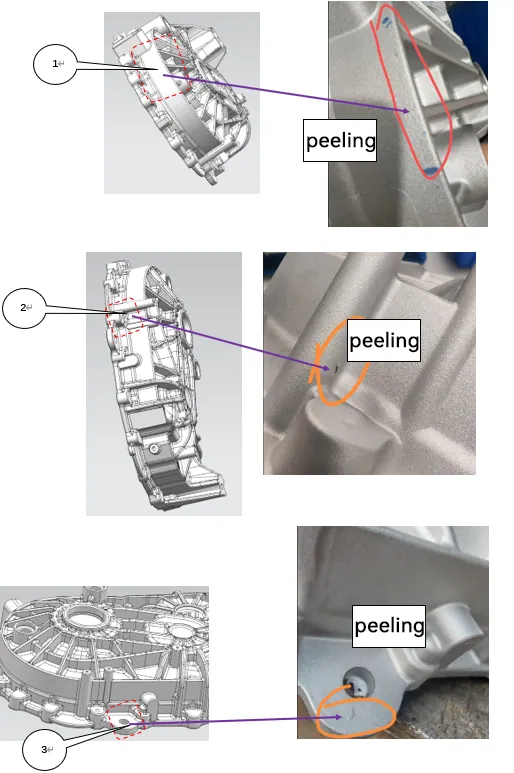
1、The cause analysis of each skinned part
Skinning position ① ② ③ are filling end, exhaust gas is not smooth and filling pressure is small is the main reason, followed by aluminum pouring temperature is low; position ② shows that the shot blasting time is too long, the surface of the phenomenon of wrinkles, in essence, the strength and hardness of the product is uneven and low (die casting billet in the vicinity of skinning cold segregation and flow marks).
2、Development of improvement measures for each skinned area
(1) Unclog the exhaust channel and deepen the exhaust channel by 0.05mm.
(2) Optimization of die-casting process parameters ~ two fast accumulator to add nitrogen (from 11.5MPa increased to 12MPa), energy storage pressure increased (from 13.5MPa increased to 14.5MPa); holding furnace temperature setting increased (from 645 ° C to 660 ° C);
(3) Optimization of shot blasting process parameters to shorten the blasting time (from 6 minutes to 5 minutes for single side blasting on exposed hangings).
3. Implementation measures team tasks
(1) Mold repair group repair mold exhaust plate, exhaust depth deepening 0.05mm
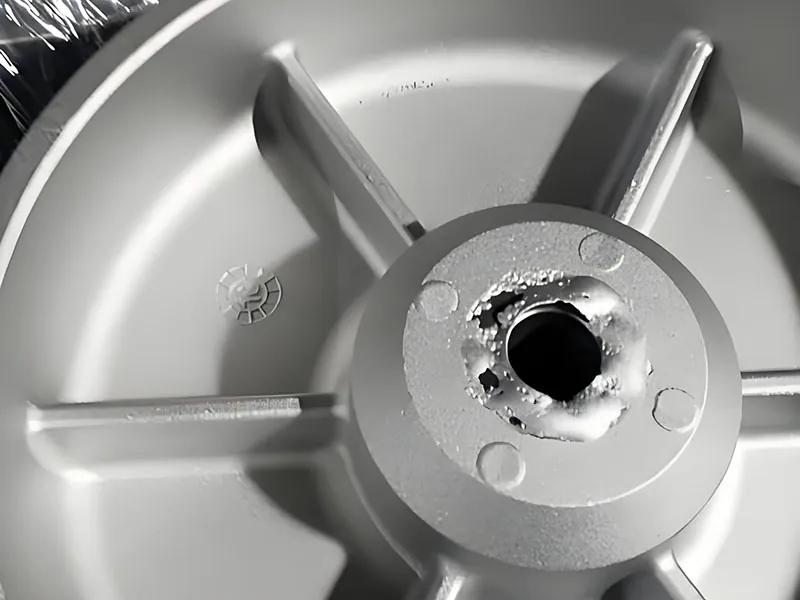
(2) die-casting process group according to the improvement measures to reset the parameters of the second fast storage pressure of 14.5MPa, the holding furnace temperature is set to 660°C.
(3) The die casting process team reset the blast time to 5 minutes.
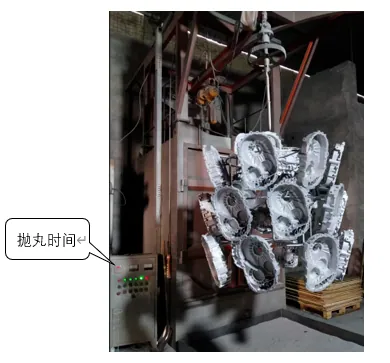
4. Implementation and testing of measures
After the implementation of the improvement measures, it was verified by shot blasting and judged to be qualified by the quality department testing, as shown in the figure below:
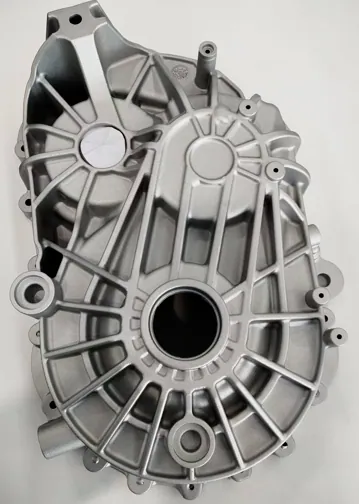
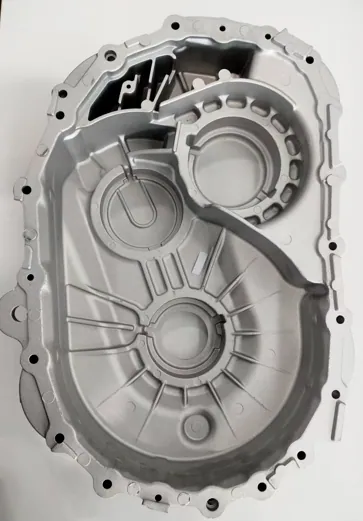
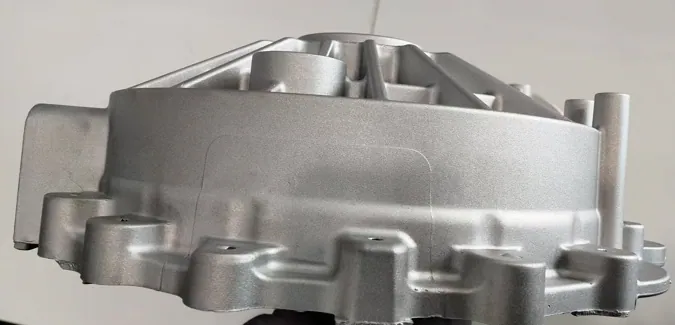
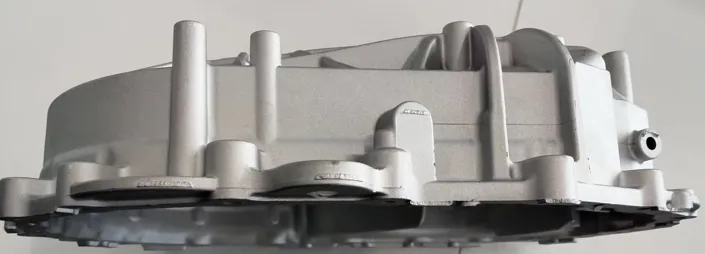
Summarize improvement results
Using the elimination method to find the exact cause of shot peening, and then formulate corresponding measures to solve the problem of ADC12 alloy product peening at a small experimental cost, this result is the pursuit of the die casting industry, but also the goal.
Conclusion and outlook
1. Conclusions of the study
Through the analysis of the chemical composition, physical properties, mechanical properties of aluminum alloy ADC12 material, through the analysis of the die casting process, summed up to ensure that the strength and hardness of ADC12 aluminum alloy products necessary conditions, through the understanding of the shot blasting pellets, through the analysis of the shot blasting process, summed up the shot blasting process on the product with impact and scraping force, the comprehensive analysis for: if ADC12 Aluminum alloy strength and hardness does not meet the standards, shot blasting easy to skin; if the shot blasting particles, shot blasting projectile flow, shot blasting time is too long, ADC12 alloy products by shot blasting is also easy to skin, so the need for a balance between the two.
As mentioned in the above case, the strength and hardness of the product were not up to standard, and the strength and hardness were improved through improvement, and the time of shot blasting was too long, and the time of shot blasting was shortened through improvement, and finally we got the qualified products of shot blasting for ADC12 alloy.
2. Research shortcomings and prospects
Shortcomings of the research process: due to the small number of experiments, and difficult to detect the local strength of the product, so did not really find the strength and hardness of the product adapted to the shot blasting Peeling critical point (data), did not achieve the lowest cost achievement ADC12 alloy strength and hardness of the product and the shot blasting impact and scraping force of the balance.
Prospects for future research direction: with the development of big data AI technology, I believe that the same industry will ADC12 alloy shot peening problem solved more thoroughly, spend less cost and reap more benefits.
Faqs
- Q: What are the casting performance advantages of ADC12?
A: Excellent fluidity, easy to mold complex precision parts, and strong corrosion resistance, suitable for mass production. - Q: How can I avoid blasting peels?
A: Comprehensive control of material composition, mold exhaust design, die casting process parameters (e.g., temperature, pressure) and shot blasting parameters are required. - Q: How are the parameters of the blasting process set?
A: Shot material (such as stainless steel shot), speed (50~70 m/s), time (5~15 minutes) need to be adjusted according to the characteristics of the workpiece. - Q: What are the common defects after ADC12 blasting?
A: Peeling, wrinkling, deformation, etc., mostly caused by excessive material composition, poor mold design or improper blasting parameters. - Q: What are the directions for mold optimization?
A: Improve the sprue design by mold flow analysis, increase the exhaust channel and overflow channel to avoid air holes and cold segregation. - Q: How is the die casting process adjusted?
A: Increase the holding furnace temperature (660°C±10°C) to optimize casting pressure and filling speed to ensure a dense product. - Q: How are shot peening pellets selected?
A: Use stainless steel pellets with a diameter of 0.2~0.6mm, screen to remove oversized particles, and mix new and old pellets proportionally. - Q: What are the best practices for setting blasting parameters?
A: Initial parameters are set to low speed, short time and low shot flow, gradually adjusted until no skinning and surface quality is achieved.