Die casting and sand casting: how to correctly select the most suitable casting process for you
Date: 2025-01-13 Categories: Blog Views: 2133
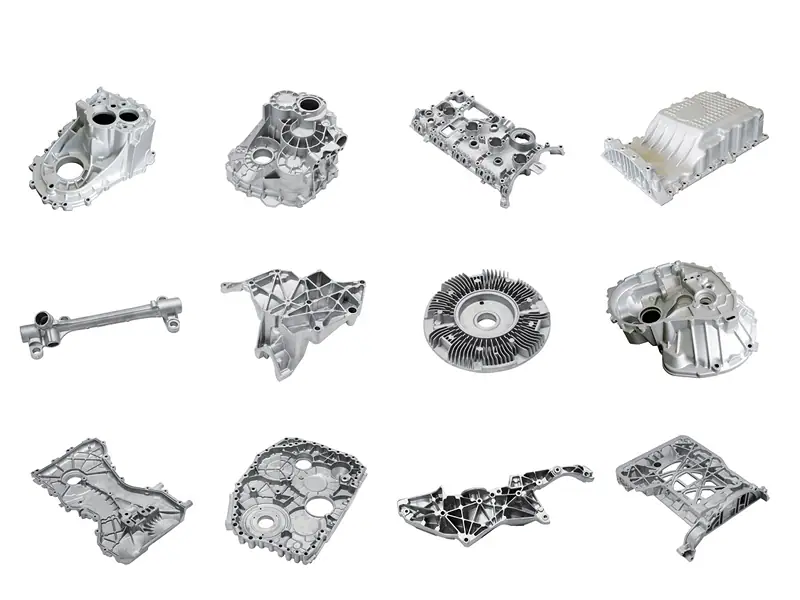
In manufacturing, casting is one of the key technologies used to produce components. Whether for automobiles, appliances, or industrial machinery, the casting process provides a robust and reliable solution. Die casting and sand casting are the two most common casting methods, and they differ significantly in many ways. Choosing the right casting process will have a direct impact on product cost, accuracy, productivity and material suitability. In this article, we will introduce each of these two casting processes and help you make the best choice for your project.
Die casting and sand casting: process introduction
1. What is die casting?
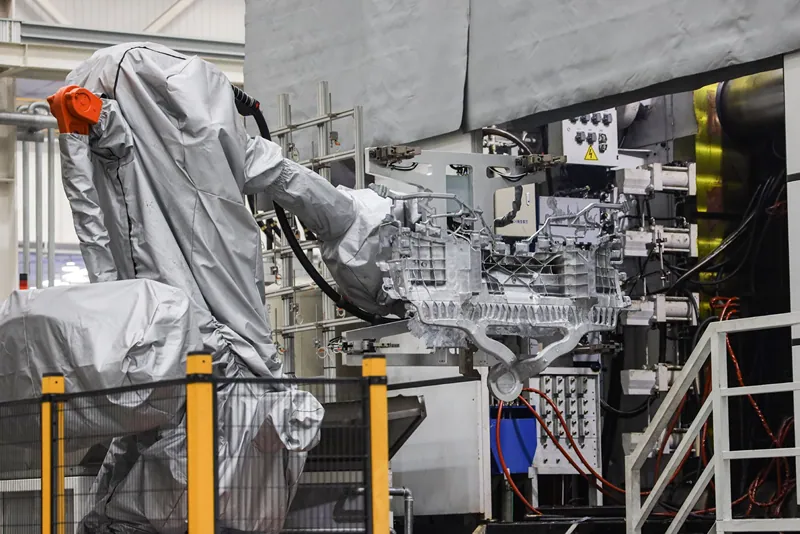
Die casting is a casting process in which molten metal is injected into the cavity of a precision mold through high pressure. It is commonly used in the casting of aluminum, zinc, copper, magnesium and other alloys, and is especially suitable for mass production of parts with complex shapes and high precision requirements. The metal is pressed into the mold through high pressure, and high precision parts can be obtained after cooling.
Key features of the die casting process:
- highly accurate: Capable of producing castings with precise dimensions and smooth surfaces, suitable for the production of complex shaped parts.
- high productivity: Due to the ability of the die casting process to fill molds quickly, production is very fast and suitable for high volume production.
- Good surface quality: The casting surface is flat and smooth, reducing the need for post-treatment.
2. What is sand casting?
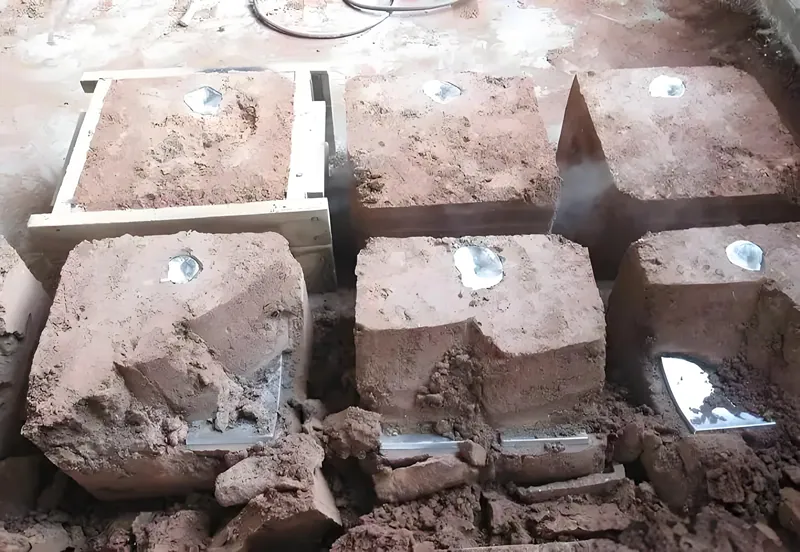
Sand casting is a traditional casting method that uses a sand mold as a mold to form castings by pouring molten metal. It is usually used for large size castings or for production needs that require less mold. Sand casting offers a high degree of flexibility and can be adapted to different shapes and materials.
The main features of the sand casting process:
- High mold flexibility: Sand casting molds can be made as quickly as needed for large size castings.
- Lower cost: Sand casting molds are simple and relatively inexpensive to make.
- adaptable: Capable of casting a wide range of metals, including cast iron, aluminum, copper, steel, etc., suitable for small batch or custom production.
The main difference between sand casting and die casting
Die casting and sand casting each have unique advantages and disadvantages and are applicable to different scenarios. We will help you understand the main differences between them through a few key dimensions of comparison.
1. production efficiency
- Die casting: Like fast workers on an assembly line, die casting is capable of producing large quantities of castings in a short period of time through a process of high pressure injection and rapid cooling. For high volume production, die casting is an extremely efficient option.
- sand casting: In contrast, sand casting has a longer production cycle. Sand molds need to be made before each casting, and each sand mold has a limited service life, so it is more suitable for small and medium-sized batch production.
parablesIf we compare the production efficiency to a racing car, die casting is like a very fast car, while sand casting is like a stable family car, the speed difference is obvious.
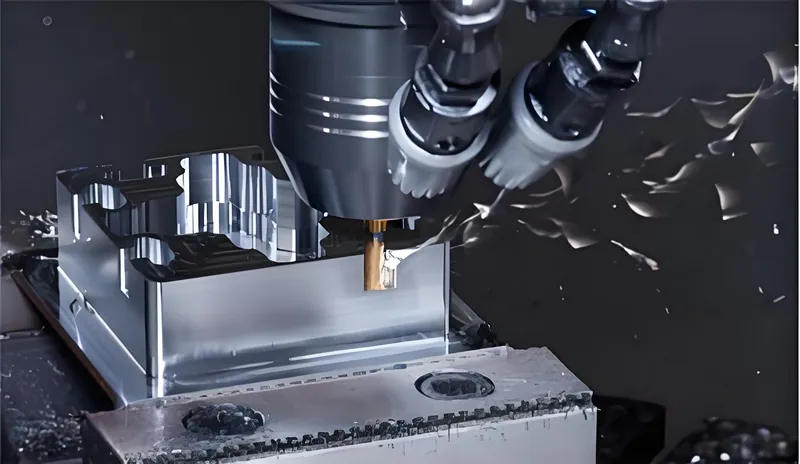
2. Casting accuracy
- Die casting: Die casting offers very high precision and consistency, producing parts with virtually burr-free, smooth surfaces. It is particularly suited to the manufacture of small precision parts with complex shapes, such as automotive engine components and electronic housings.
- sand casting: The precision of sand casting is relatively low, the surface of the casting is rough, and the dimensional error is large, which usually requires post-processing, such assandblastand trimming.
Die casting is like carving a fine work of art, requiring every detail to be perfect; while sand casting is more like carving a stone sculpture with a rough cutter, where the shape is roughly right but the surface details may need to be trimmed.
3. Adaptation of casting materials
- Die casting: It is suitable for casting light alloys such as aluminum, zinc, magnesium, etc. and is particularly effective for casting non-ferrous metals. It is not suitable for metals with higher melting points such as steel, as the high temperatures and pressures required are beyond the working range of the equipment.
- sand casting: Sand casting is much more adaptable and can cast virtually any metal, including cast iron, steel, aluminum, copper alloys and more. It is particularly suited to the production of large and heavy castings.
Die casting is like a professional chef, good at cooking exquisite dishes; while sand casting is like an all-round chef, what dishes can do.
4. Mold Cost and Life
- Die casting:die casting moldThe manufacturing cost is higher because it is usually made of high-precision, high-strength steel and has a complex design. Die casting molds have a longer life and are suitable for mass production.
- sand casting: Sand casting molds are inexpensive and simple to manufacture. Molds are made from materials such as sand and clay and can be made quickly, but the molds need to be remade after each production run, making them suitable for low volume or customized production.
parablesDie casting molds are like a precision-designed high-rise building that costs time and resources but lasts a long time, while sand casting molds are like building a temporary shed, which is low-cost but has a limited service life.
5. Size and complexity of applicable parts
- Die casting: Die casting is suitable for the production of fine, complex, small parts, especially in the need for high precision and high surface quality occasions, such as automobile engine parts, electronic shells, precision fittings and so on.
- sand casting: Sand casting is more suitable for the manufacture of larger size or heavier weight parts, especially in the less stringent precision requirements. It is suitable for casting large mechanical parts, heavy cast iron components and so on.
Die casting is like a sculptor, capable of carving detailed artifacts, while sand casting is like a builder, suitable for building large structures.
Hersin: The Best Partner to Take You to the Top
When choosing between die casting and sand casting, choosing the right partner is equally important. As a leading casting company in the industry, Hersin has a wealth of experience and a strong technical team to provide you with customized casting solutions. Whether it is precision die casting parts or large size sand casting parts, Hersin can provide you with high quality products and efficient services. We use advanced equipment and strict quality control system to ensure that each casting meets your requirements.
Frequently asked questions about die casting and sand casting
1. Which process is more suitable for high-volume production?
Die casting is the best choice if your production needs are for high volume and high precision parts. Its high productivity and precision make it an ideal process for mass production.
2. Can I use sand casting to make complex shaped parts?
Sand casting, while suitable for large and complex shaped parts, has lower precision and surface quality than die casting. If your parts require highly detailed surface and dimensional requirements, die casting would be a more appropriate choice.
3. Which process is more suitable for casting heavy parts?
Sand casting is suitable for casting heavy and large-sized parts, especially cast iron and steel castings. Die casting, on the other hand, is suitable for small and highly accuratealuminumThe components are made of zinc alloy, zinc alloy, etc.
reach a verdict
When choosing a casting process, die casting and sand casting each have their own advantages and limitations. Die casting is suitable for small parts that require high precision and productivity, while sand casting is suitable for the production of large or heavy parts. Understanding these differences and making a choice based on your production needs will help you improve your