Aluminum 6061 and 7075: Performance Comparison and Application Scenarios In-depth Analysis
Date: 2025-02-20 Categories: Blog Views: 716
As a technical expert in the foundry industry for more than 20 years, I have witnessed thousands of aluminum Material at high pressure/low pressure/ Gravitational casting The performance of aluminum alloys. Among many aluminum alloy grades, 6061 and 7075 have always occupied a special position in the "golden combination". This article will be based on the engineering practice data of Ningbo Hexin, this article will be compared from the dimensions of chemical composition, mechanical properties, heat treatment process and application areas, in-depth analysis of the performance of these two benchmark material boundaries.
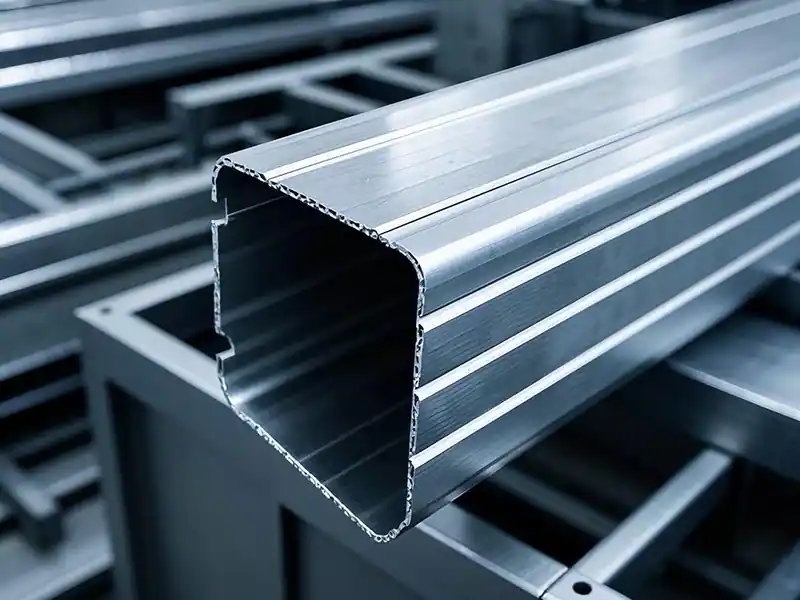
Aluminum 6061: All-purpose industrial alloys
As a "deformer" in the industrial field, 6061 aluminum alloy shows unique material wisdom under the subtle proportion of magnesium and silicon elements. This aluminum-based alloy through the intelligent control of the microscopic lattice, not only can withstand the mechanical test of the structural components, but also in the processing workshop elegant transformation - whether it is argon arc welding gun under the smooth walking wire, or extruder to extend into a complex cross-section profiles, it is always able to find a perfect balance between the solid state and plasticity. When you walk into the automobile assembly line, you will see it transformed into lightweight chassis components; step into the coastal construction site, and can be found after anodic oxidation treatment, in the salt spray invasion still maintains the bright nature of the color. What is even more rare is that this metal can still be 100% reborn after retirement, quietly practicing the green commitment of modern manufacturing.
The chemical composition of 6061 aluminum generally includes:
Aluminum (Al): 97.9%
Magnesium (Mg): 1.0%
Silicon (Si): 0.6%
Iron (Fe): 0.7%
Manganese (Mn): 0.6%
Copper (Cu): 0.28%
Zinc (Zn): 0.2%
Titanium (Ti): 0.15%
Chromium (Cr): 0.23%
Other elements: 0.15%
Aluminum 6061 toMagnesium (1.0%)respond in singingSilicon (0.6%)as the main alloying element, supplemented by trace amounts of copper, manganese, chromium, etc. (total aluminum content of 97.9%). This combination gives it excellentworkabilitytogether withcorrosion resistanceThe company also has good welding and molding capabilities.
Mechanical properties and heat treatment
- tensile strength: 310 MPa
- yield strength:: 276 MPa
- elongation: 12%
- Brinell hardness:: 95 HB
pass (a bill or inspection etc)Solid solution treatment (530°C) and age hardening (177°C)The new design is designed to provide further strength for scenarios where light weight and medium loads are required.
Typical application areas
- Construction and Transportation: Window frames, car chassis, bicycle frames
- Marine & Electronics: Hull fittings, radiator housings
- consumer good: Exercise equipment, furniture
Aluminum 7075: Aerospace Grade High Strength Alloy
With a golden ratio of zinc and magnesium at its core, 7075 aluminum alloy builds a high-strength crystalline structure within the aluminum matrix. This alloy is activated by a sophisticated heat treatment process to activate the internal reinforcing phases, allowing the material to exhibit load-bearing capacity comparable to that of specialty steels at T6, while maintaining aluminum's unique lightweight advantage. A ceramicized protective layer formed by micro-arc oxidation on the surface maintains structural integrity in extreme temperature and chemical attack environments. Despite being more difficult to process than conventional aluminum alloys, 7077 has become the preferred choice for aircraft keel forging due to its excellent specific stiffness, and has interpreted the metal's strength aesthetics in critical areas such as spacecraft fuel tanks and high-speed train bogies. From precision forgings for fighter jet wing beams to integrated frames for competitive bicycles, this material always seeks a perfect balance between safety and performance limits, and even realizes a recycling rate of more than 95% through a closed-loop recycling system, which interprets the wisdom of sustainable development in the field of high-end manufacturing.
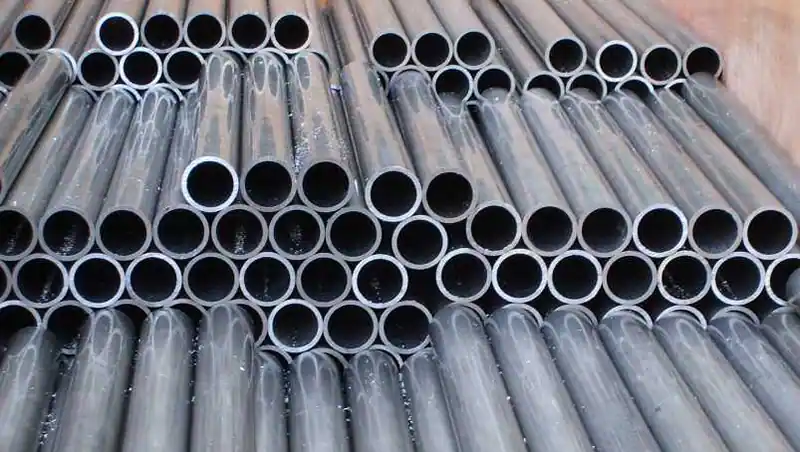
The chemical composition of 7075 aluminum generally includes:
Aluminum (Al): 87.1%
Magnesium (Mg): 2.5%
Silicon (Si): 0.16%
Zinc (Zn): 5.6%
Titanium (Ti): 0.04%
Manganese (Mn): 0.05%
Copper (Cu): 1.6%
Iron (Fe): 0.15%
Chromium (Cr): 0.23%
Other elements: 0.15%
Aluminum 7075 in zinc (5.6%)respond in singingMagnesium (2.5%) is dominant (total aluminum content 87.1%), supplemented by copper, chromium and other elements. Its high strength comes from the reinforced phase formed by zinc and magnesium, but it is difficult to weld and requires special process support.
Mechanical properties and heat treatment
- tensile strength: 570 MPa (1.8 times that of 6061)
- yield strength: 503 MPa
- elongation: 11%
- Brinell hardness:: 150 HB
pass (a bill or inspection etc)Precision solution treatment (477°C) with low temperature aging (120°C)In addition, it can maximize its strength potential, but the process complexity is significantly higher than that of 6061.
Typical application areas
- aerospace: Aircraft wing girders, landing gear
- high-end equipment: Racing driveshafts, high-performance bicycle frames
- Mold Manufacturing: High Stiffness Stamping Die
Aluminum 6061 vs 7075: Key Performance Comparison
parameters | Aluminum 6061 | Aluminum 7075 |
---|---|---|
tensile strength | 310 MPa | 570 MPa |
yield strength | 276 MPa | 503 MPa |
malleable | 12% (better) | 11% |
corrosion resistance | Excellent (high silicon content) | Medium (surface treatment required) |
processing difficulty | Low (easy to weld/mold) | High (specialized equipment required) |
(manufacturing, production etc) costs | economy model | High-end (30-50% higher price) |
Selection Decision Guide
- Prioritize 6061 scenarios:
- Outdoor or marine environments where good weldability and corrosion resistance are required (e.g. marine fittings).
- Low and medium loaded structural elements (e.g. building frames) with limited budgets.
- Consumer products that require complex molding (e.g. furniture).
- Prioritize 7075 scenarios:
- Highly stressed, fatigue resistant requirements (e.g., airplane wings, racing car parts).
- Weight-sensitive but strength-critical gear (e.g., mountain bike frames).
- Mold or military fields where additional processing costs are acceptable.
Professional advice from engineers
- Process Matchability7075 is sensitive to heat treatment parameters and requires strict temperature control and quenching speed; 6061 is more suitable for conventional workshop conditions.
- Anti-corrosion design: 7075 Additional anodizing or coating protection is recommended in salt spray environments.
- economic trade-off: If strength requirements are close to the upper limit of 6061, 7075 may be prioritized to extend part life.
concluding remarks
Aluminum 6061 and 7075 have their own advantages, the choice needs to be based on theStrength, cost, processing conditions and environmental requirementsComprehensive Evaluation. For casting companies such as Ningbo Hexin, a deeper understanding of customer application scenarios (e.g., automotive lightweight or aerospace precision parts) will help you recommend material solutions more accurately and enhance product competitiveness.
Extended Thinking: With the rise of new energy vehicles and UAV industry, how to further optimize the performance boundary of these two materials through alloy modification or composite process? This may be one of the directions for future technological breakthroughs.