What is the difference between aluminum extrusion vs aluminum die casting?
Date: 2025-04-23 Categories: Blog Views: 22
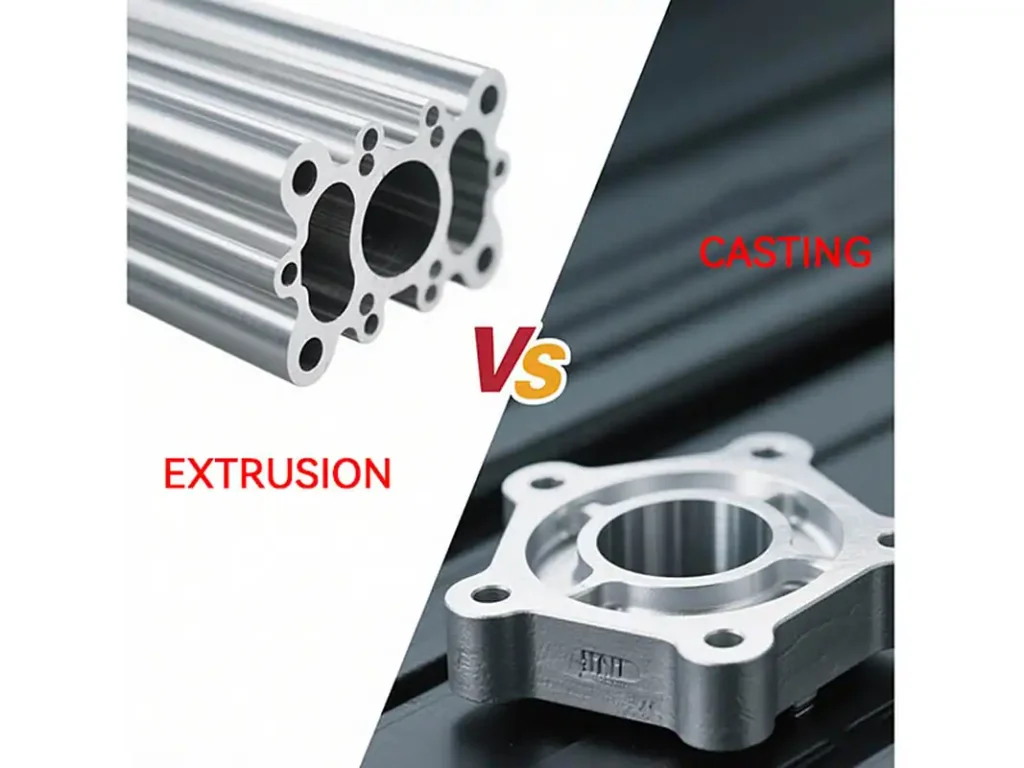
In the field of industrial manufacturing, aluminum has become the material of choice in the automotive, electronics, and construction industries due to its lightweight, corrosion-resistant, and high-strength characteristics. However.aluminum extrusion(Aluminum Extrusion)together withAluminum Die CastingThe core difference between the two processes directly affects the production cost, structural accuracy and mass production efficiency. As a deep-rooted aluminum die casting field20 yearsof technical experts.Ningbo Hexin Die Casting FactoryThrough this article to analyze the engineering logic of the two processes, and share how to reduce costs and increase efficiency for customers through precision die casting technology.
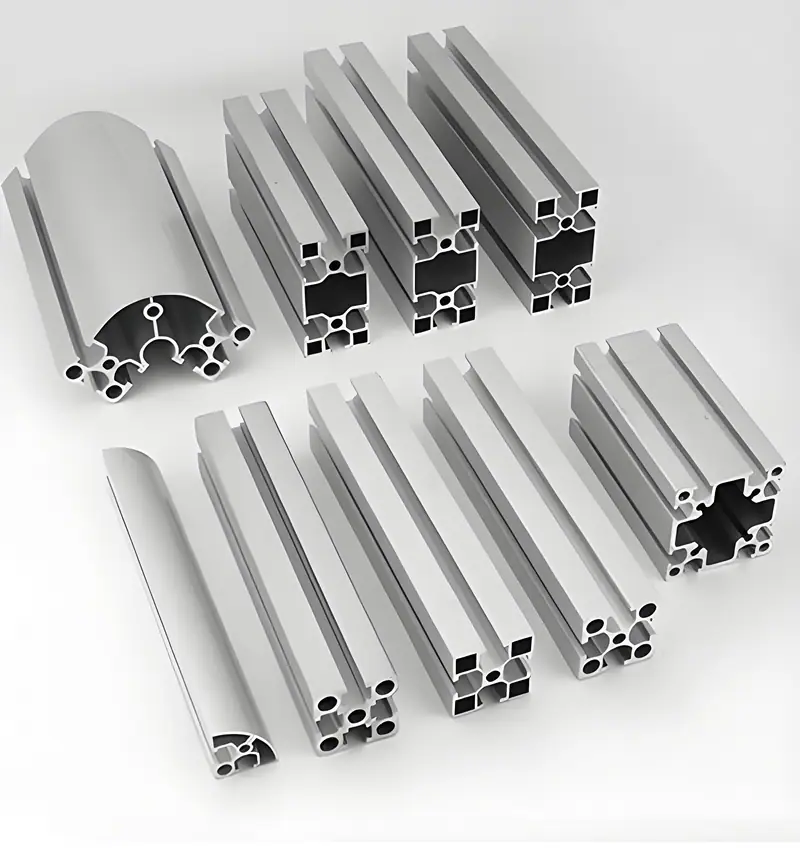
Comparison of the essence of molding principles
(Fundamental differences in the way materials flow)
The aluminum extrusion process forces ingots heated to 400-500°C through special die holes by means of hydraulic pressure of up to 15,000 tons, a continuous plastic deformation process similar to the "toothpaste squeezing" principle. The metal is reshaped in the solid state, maintaining the continuity of the original grain structure of the aluminum. In contrast, aluminum die casting uses liquid aluminum broth at 680-720°C, which is injected into the cavity of the steel mold at a speed of 30-100m/s under high pressure of 800-1200bar, and solidified by rapid cooling (cooling rate up to 1000°C/sec).
This difference in physical state leads to a fundamental difference in product performance: extruded parts have anisotropic mechanical characteristics, along the direction of extrusion strength enhancement 20-30%; die casting is due to rapid solidification to form a fine crystalline organization, but there is a porosity defect of 3-5%. From the microstructure, extruded aluminum grains are elongated to form a fibrous organization, die casting presents a mesh structure of inter-dendritic eutectic phase.
Process duel in equipment systems
(Comparison of the entire process from furnace to finished product)
The core equipment of the extrusion line consists of a long bar heating furnace, extrusion barrels, die temperature control system and haul-offs, with an equipment investment of approximately US$2-5 million. Typical extrusion speeds are 5-50 m/min, and die life is up to 50-100 tons production. Die casting system, on the other hand, consists of melting furnace, injection unit, mold closing mechanism, cold chamber die casting machine clamping force range of 800-5,000 tons, equipment cost of $ 3-8 million, die life of about 100,000-200,000 die times.
In terms of energy consumption, extrusion tons of aluminum power consumption of about 500-800kWh, the main energy consumption is concentrated in the plastic deformation process; die casting tons of aluminum power consumption of 800-1200kWh, of which 60% energy consumption for metal melting and die temperature control. Environmental performance, extrusion process of waste recycling rate of up to 95% or more, while die-casting due to the soup stock and scrap rate (about 5-15%) produce more need to return to the furnace waste.
Application analysis of product characteristics
(Logic of choice from smartphones to spacecraft)
Extrusion process is good at producing linear components with constant cross-section, typical wall thickness 1.5-25mm, surface roughness Ra0.8-3.2μm. in the field of architectural curtain wall, 6063-T5 alloy extruded profiles accounted for more than 80%; the length of the whole extruded floor of the rail transit carriages can be up to 26 meters. Die casting is suitable for complex three-dimensional modeling, the minimum wall thickness of up to 0.6mm, surface Ra1.6-6.3μm, automotive engine block commonly used A380 die casting, integrated more than 30 functional structures in one.
In terms of mechanical properties, extruded T6 statealuminumTensile strength up to 350MPa, suitable for structural load-bearing parts; die casting ADC12 alloy typical strength of 280MPa, more focused on shape complexity. Emerging vacuum die casting technology can casting elongation to 10% above, is changing the traditional die casting brittle perception.
The choice of process needs to be considered comprehensively: monthly output of 50,000 pieces of the following recommendations for extrusion (mold costs as low as $ 10,000), high-volume production of die-casting (although the mold cost of $ 50,000-20,000, but the cost of a single piece can be reduced by 60%). For the need to anodize the shell of electronic products, the priority choice of lower impurity content of extrusion 6063 alloy; and automotive transmission shell due to the complex design of the oil channel, inevitably choose die-casting process. With the popularity of hybrid technology, integrated die-casting body parts are triggering a revolution in automobile manufacturing, Tesla Model Y rear bottom plate using 6000 tons of die-casting machine, will be 70 parts integrated into one.