Machining Basics
Date: 2025-02-27 Categories: Blog Views: 654
machining
As the core technology of modern manufacturing, machining, through lathes, milling machines, grinders and other specialized equipment for metal, plastic and other workpieces such as cutting, grinding, drilling and other procedures, precise control of the geometry of the parts, structural dimensions and surface finish, to ensure that from automotive engine components to aerospace precision parts of the whole field of manufacturing needs. With the deep integration of CNC technology and automated production lines, the machining process has realized the transformation and upgrading from traditional manual operation to intelligent programming control, which improves machining efficiency while effectively controlling production costs. The quality control system that strictly follows international standards ensures process stability in mass production through real-time monitoring of tool wear status and optimization of machining parameters. Under the current trend of Industry 4.0, machining is evolving in the direction of flexible production and digital management, providing reliable solutions for the customization of complex parts.
numerical control machining
CNC machining relies on computer programming to accurately control the trajectory of the machine tool, through the automated execution of turning, milling, boring and other precision machining processes, metal, engineering plastics and other raw materials are efficiently transformed into complex components that meet the design specifications. Its core advantage lies in the digital command-driven high repeatability and multi-axis linkage capability, which can be adapted to the full-scale manufacturing needs from micro-components of medical devices to large structural parts of energy equipment. Modern smart factories realize dynamic optimization of processing parameters and intelligent prediction of tool life by integrating CAM programming systems and online inspection devices, ensuring dimensional consistency in mass production while improving processing efficiency in high-end fields such as aerospace and automotive molds. With the deep application of Internet of Things technology and digital twin model, CNC machining is accelerating the evolution of cloud-based collaborative manufacturing and adaptive process adjustment, providing key technical support for intelligent manufacturing ecology.
Classification of machining
turning
The workpiece is rotated by the lathe spindle, combined with the radial/axial feed movement of the tool, specializing in the internal and external round machining of rotary parts such as shafts, disks and bushings, and demonstrating the advantages of high-efficiency cutting in mass production of automotive drive shafts, hydraulic cylinder barrels, etc. It is capable of handling carbon steel, aluminum The CNC lathe is capable of thread turning and precision machining of eccentric structures in a wide range of materials from high-temperature alloys to high-temperature alloys.
milling
The use of vertical/horizontal milling machine multi-flute tool rotary cutting, capable of complex cavities, three-dimensional curved surface molding processing, from the mold inserts of the parting surface to the robot joints of the joint groove are typical application scenarios, five-axis linkage CNC milling technology to break through the limitations of the spatial angle, impeller, propeller and other shaped parts in the field of processing is irreplaceable.
Grinding
The use of grinding wheel particles for micron-sized material removal is the ultimate process for obtaining mirror precision in hardened steel, ceramics and other super-hard materials. Bearing races in the manufacture of precision spindles and the surface treatment of artificial joints for medical devices rely on this technology, and sub-micron dimensional stability is ensured by an on-line measurement system and environmental control in a constant temperature workshop.
Drilling, reaming, tapping and other processing
Covering the complete hole solution from basic through-hole machining to precision thread forming, deep hole drilling technology to meet the needs of gun drilling, oil and gas pipelines and other special L/D ratios, the application of composite tools so that the drilling, reaming and tapping process can be completed in a single clamping, which significantly improves the machining efficiency of engine blocks, hydraulic valve blocks and other multi-hole system parts. Also commonly used in die casting mold Manufacturing.
Machining equipment
lathe
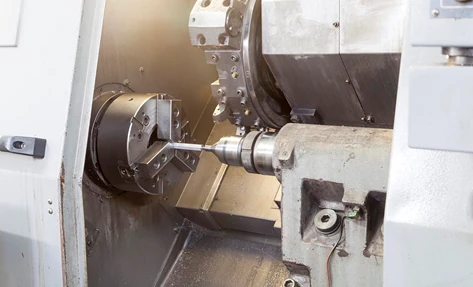
As the core equipment for rotary body machining, the lathe drives the bar or disk workpiece to rotate at a high speed through the spindle, and accurately completes the cylindrical turning, face cutting and thread machining by cooperating with the radial/axial composite feeding movement of the turret. Modern CNC lathe integrates power tool and Y-axis function, which can carry out milling-turning compound machining for stainless steel, titanium alloy and other hard-to-cut materials, and is widely used in mass production of automotive camshafts, hydraulic valve cores and other precision parts, and its dual spindle design can realize automated continuous machining.
machining center
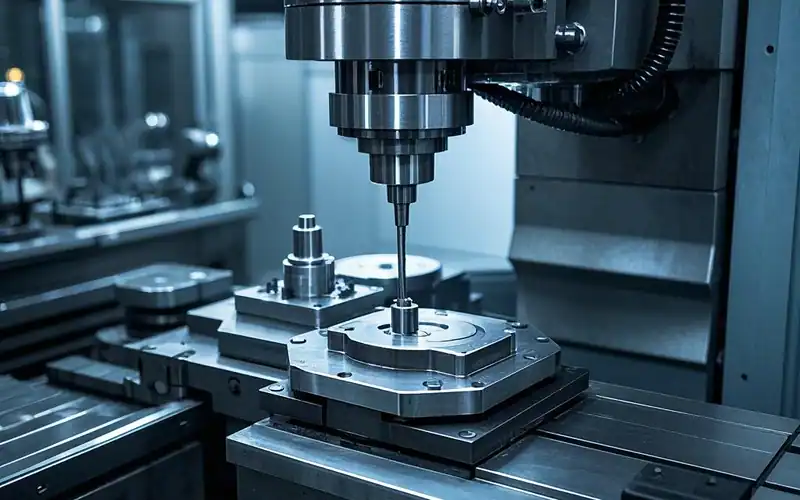
With the spatial machining capability of multi-axis linkage, the milling machine realizes complex surface molding with the help of vertical/horizontal spindle driving face milling cutter, ball-end cutter and other tools, and the five-axis CNC milling machine breaks through the spatial angle limitation through table swinging, which demonstrates the irreplaceability in the three-dimensional surface machining of the blades of aero-engine and the inserts of the plastic injection molds. The machining center equipped with automatic tool changer system can complete the complete process of aluminum alloy frame parts from rough machining to finish milling at one time.
drilling machine
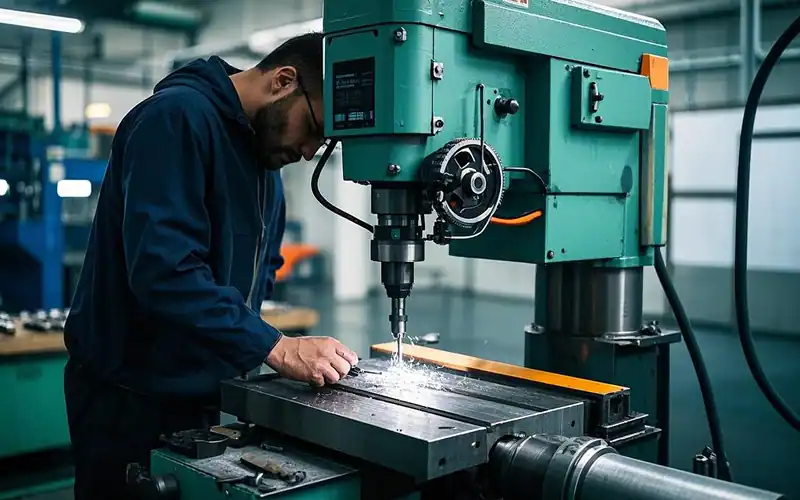
As a professional solution provider in the field of deep hole machining, the drilling machine realizes accurate hole machining by driving twist drills, deep hole drills and other tools through a high-speed spindle, and the gun drilling technology together with a high-pressure cooling system can complete deep hole drilling with an L/D ratio of more than 30:1. Intelligent drilling center integrates reaming and boring process modules to meet the demand for efficient machining of multi-specification holes such as energy equipment tube plates and automotive transmission shells, and is equipped with a laser tool setting instrument to realize real-time compensation for drill bit wear.
grinder
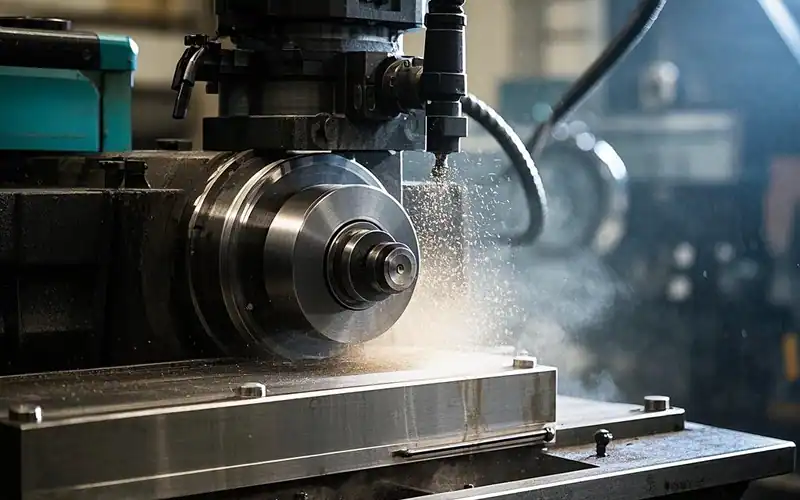
The last line of quality defense for precision manufacturing, the grinding machine adopts CBN grinding wheels or diamond grinding wheels to dress super-hard materials such as hardened steel and cemented carbide with nano-scale precision, and the CNC profile grinding machine can stably maintain the micrometer-scale contour precision of bearing raceways and screw threads through a closed-loop feedback system. Centerless grinding machines equipped with on-line measuring system provide fully automatic grinding solutions for large-volume high-precision parts such as guide pillar of optical instruments and hydraulic valve spools, etc. The environmental control of constant temperature workshop ensures the processing stability.
Other machining equipment
numerical control machine
As the core carrier of intelligent manufacturing, CNC machine tools seamlessly connect multi-axis linkage and CAM programming system to directly transform 3D modeling data of complex parts into precision machining instructions, showing technical advantages in multi-process integrated machining of aerospace titanium alloy structural parts and medical device implants. Intelligent machine tools equipped with adaptive control systems can sense the fluctuation of cutting force and tool wear status in real time, and combine with the industrial Internet of Things platform to realize the cloud optimization iteration of machining parameters, providing flexible production solutions for automotive molds, optical devices and other precision manufacturing fields.
laser cutting machine
Relying on high-power fiber laser and galvanometer positioning technology, the laser cutting machine realizes micron-level precision cutting of stainless steel, aluminum alloy and other metal plates by non-contact processing, and its intelligent monitoring system can automatically identify the oxidized layer of carbon steel and adjust the position of the focus, which significantly improves the efficiency in the processing of new energy automobile battery trays and electronic component heat sinks. The 10,000-watt laser cutting equipment breaks through the bottleneck of thick plate cutting, and with the automatic loading and unloading robotic arm, it provides all-weather continuous operation capability for the construction machinery and shipbuilding industries, and the heat-affected zone control technology effectively guarantees the subsequent welding quality of precision parts.
water jet cutting machine
Adopting the cold cutting process of ultra-high-pressure water jet mixed with garnet sand, the water cutting machine maintains the original properties of materials in the processing of carbon fiber composite materials and marble shaped decorative parts by virtue of the unique advantage of no thermal deformation. The five-axis dynamic cutting head realizes precise separation of three-dimensional contours of ceramic coatings on turbine blades and food-grade plastic containers through spatial angle compensation technology. Its environmental protection feature completely eliminates the dust pollution generated by traditional cutting, and it has become the preferred process for high-standard machining scenarios in the medical consumables and architectural curtain wall industries.
Machining process
Cutting Principle
Cutting Principle: The cutting motion is the relative motion between the tool and the workpiece, including the main motion and the feed motion.
cutting speed: Cutting speed is the instantaneous speed of a selected point on the cutting edge of a tool relative to the surface of the workpiece to be machined in the direction of the main motion.
Depth of cut: The depth of cut is the vertical distance between the surface to be machined and the surface to be machined.
Cutting tools
Cutting tool materials:: Commonly used tool materials include high-speed steel, cemented carbide, ceramics and super-hard materials.
Tool Geometry: The geometrical parameters of the tool, including front angle, back angle, main deflection angle and camber, have an effect on cutting forces, cutting heat, durability and surface quality of the workpiece.
Tool sharpening:: Tool sharpening includes the selection of grinding wheels, sharpening process and inspection of sharpening quality.
cutting fluid
The role of cutting fluids:: The role of cutting fluid includes cooling, lubrication, cleaning and rust prevention.
Types of cutting fluids:: Types of cutting fluids include emulsions, synthetic fluids and cutting oils.
Cutting fluid selection:: The selection of cutting fluid should be based on processing requirements, workpiece materials and tool materials and other factors.
Machining Process
Gross preparation
Based on the mechanical properties of the parts, the near-net-shape blanks are prepared by casting, forging or 3D printing, the hot isostatic pressing process is used to eliminate internal defects for titanium alloy aerospace structural parts, and the aluminum alloy die-casting blanks need to be X-ray detected to ensure that the porosity rate is <0.2%. Intelligent Manufacturing Workshop automatically matches the batch of blanks with the machining orders through the MES system to realize the whole process of tracing from the raw materials to the rough machining. Intelligent Manufacturing Workshop
Workpiece positioning
Using six-point positioning principle to design modular fixture system, hydraulic expansion mandrel ensures 0.005mm radial runout accuracy for thin-walled cylinder parts, and pentahedral vacuum suction cup provides non-destructive clamping solution for shaped composite materials. For the processing of new energy vehicle motor housing, laser scanning and adaptive clamping force control technology are adopted to compensate for the effect of fluctuations in blank size on the positioning reference.
Tool Preparation
Based on the cutting simulation data to predict the tool life, PVD coated carbide tools can cope with the intermittent cutting of high temperature alloys, and diamond coated drills can realize burr-free machining of carbon fiber composite materials. Intelligent tool magazine automatically identifies tool parameters through RFID chips, and synchronously calibrates tool compensation values during tool change in machining centers to ensure dimensional consistency in automotive mold cavity machining.
machining
Multi-axis CNC machine tools implement full sequential machining strategies, mill-turn centers complete internal and external profile machining of aero-engine magazines in a single clamping, and micro-lubrication technology increases the cutting efficiency of Inconel 718 material by 40%. 5-axis machining centers extend deep groove machining tool life by 3 times through the oscillating milling process, and work with online measurement systems to correct tool path deviations in real time.
Workpiece Inspection
Coordinate Measuring Machine (CMM) to build a digital inspection closed loop, blue light scanner to capture turbine blade blade profile deviation, industrial CT non-destructive testing of aluminum alloy casting internal shrinkage. SPC system statistical analysis of the key dimensions of the CPK value, AI visual inspection of surface defects identification accuracy of 99.7%, the inspection data is automatically uploaded to the QMS system to generate an electronic quality file.
Machining quality control
Machining Error Analysis
original error:: Related to machine tools, fixtures, tools and the workpiece itself, such as manufacturing and assembly errors.
Machining errors:: Errors due to various factors in the machining process, such as cutting forces, cutting heat, tool wear, etc.
detection error: Errors caused by factors such as measurement equipment, measurement methods, and measurement environment during the measurement process.
Quality control methods
prophylactic control:: Reduce errors and improve product quality through design and process control.
process control:: Ensure consistent product quality by monitoring and adjusting processing in real time.
Finished Product Inspection: Inspect and test finished products to ensure that they meet specified requirements.
Machined surface quality
surface roughness:: The height of surface microscopic unevenness, which affects the wear resistance and fatigue strength of the part.
Surface Ripple Degree:: The shape and size of the surface corrugations, which affect the fatigue strength and sealing of the part.
Surface Finishing Texture:: Surface machining leaves marks and textures that affect the appearance and fit accuracy of the part.
Machining dimensional accuracy control
Dimensional accuracy: The degree of conformity of the actual dimensions of a machined part with the specified dimensions.
position accuracy: The positioning accuracy of the workpiece relative to the machine tool during machining affects the assembly accuracy of the part.
Repeat Positioning Accuracy:: The accuracy of repeated positioning of a machine tool under the same conditions, reflecting the stability and reliability of the machine tool.
Begin custom machined parts
Ningbo Hersin provides one-stop CNC machining solutions for complex parts, offering full-cycle precision machining services from rapid prototyping to mass production. Relying on five-axis linkage machining centers, mill-turn equipment clusters, and Swiss Baumatic ultra-precision machine tools, Hersin specializes in the production of automotive parts and other products. Upload your drawings to our intelligent quotation system and get an actuarial report with DFM optimization and tool wear analysis.Contact
Processing Equipment Safety Regulations
Pre-startup inspection of equipment
Verify the pressure stability of the hydraulic system (20-25MPa) and the sealing of the pneumatic pipeline, use infrared thermography to detect the spindle motor winding temperature abnormality, and check the dual protection settings of the CNC system for soft limit and hard limit. For five-axis machining centers need to additionally check the rotary table locking mechanism, laser interferometer detection guideway positioning accuracy error ≤ 0.02mm, to ensure that the carbon steel workpiece clamping magnetic suction cups residual magnetic strength ≤ 5 gauss.
Equipment Operating Procedures
Strictly implement the SOP parameter setting specification: the rough milling cutting speed of cast iron is limited to 150-220m/min, and the carbide tool feed rate is adjusted according to the gradient of ap=2mm×ae=35mm. When machining titanium alloy, the micro lubrication (MQL) system must be activated and the concentration of smoke in the cutting area must be monitored, the operator must wear an impact-resistant mask and flame-retardant clothing, and the emergency brake button must be triggered immediately in the event of a spindle overload alarm.
Maintenance of equipment after shutdown
Closed-loop cleaning of metal debris in cutting fluid tank and testing of pH value (8.5-9.2), using ultrasonic cleaning machine to remove micron-sized oil film residue on the taper surface of tool shank. Perform monthly ball screw backlash compensation (C3 grade precision screw compensation ≤ 0.015mm), prejudge spindle bearing life through vibration spectrum analysis, and lubricating grease filling volume is accurate to ±0.5ml.
Machining Accident Case Study
Accident Case I
An auto parts factory CNC lathe spindle overheating fire: the operator violated the shutdown of coolant for stainless steel continuous turning, cutting temperature exceeded 900 ℃ lead to fuel mist. After the accident, it was mandatory to install a thermal imaging monitoring system and implant a cutting thermodynamic model in the PLC to realize temperature-speed linkage control.
Accident case II
Gantry milling machine protection door interlock failure to disability: equipment transformation shielding safety grating signals, iron filings splash through the 5mm acrylic baffle. Rectification program upgraded to IP67 protection level of pressure-sensing floor mats and dual circuit grating, trigger response time ≤ 0.3 seconds.
Machining Development Trends and Challenges
Development trend of machining technology
- Digital twin drive: real-time mapping of machine tool status to the cloud, machining error prediction accuracy of 99.2%
- Composite machining revolution: integrated turning, milling, boring and grinding equipment reduces the number of clamping times and shortens impeller machining cycle time by 60%
- Green Manufacturing: Hydrogen Cutting Technology Replaces Emulsions, Reduces Carbon Footprint by 451 TP3T
Challenges facing the machining industry
- High-skilled talent fault: five-axis programming technician shortage of 37%, need to AR remote guidance system to fill the gap
- Bottleneck of superhard material processing: Silicon carbide mirror processing tool life of only 15 minutes, urgent need for plasma-assisted cutting technology breakthroughs
- Data security risk: CNC system vulnerability leads to G-code tampering, blockchain encrypted transmission required
Prospects for the development of machining technology
Quantum measurement technology advances dimensional inspection accuracy to the nanometer level, and AI self-evolutionary algorithms increase the efficiency of dynamic optimization of cutting parameters by 300%. By 2030, brain-computer interface-based gesture control of machine tools and zero-emission dry machining centers will become standard in high-end manufacturing, and the microfactory model will reconfigure the aerospace supply chain.