Aluminum oil sump
Date: 2024-08-05 Categories: Blog Views: 2731
What's an oil pan?
The oil pan is located in the lower part of the engine crankcase, also known as the lower crankcase. It is used to seal the crankcase, collect the lubricating oil produced by engine friction back to prevent outside dust impurities into the lubricating oil.
Classification of oil sumps.
These are the common types of oil sumps
Plastic oil sump
Plastic oil pan means that the material of the oil pan is engineering plastics, and it is made of injection mold Processing technology manufacturing, this material made of oil pan quality is lighter and thinner, design freedom is higher, the price is relatively low, more convenient installation. Has a certain degree of toughness. However, the high temperature resistance and corrosion resistance of the plastic oil pan is relatively poor, relatively short life, suitable for low working temperature, low frequency of use, the weight requirements of the environment.
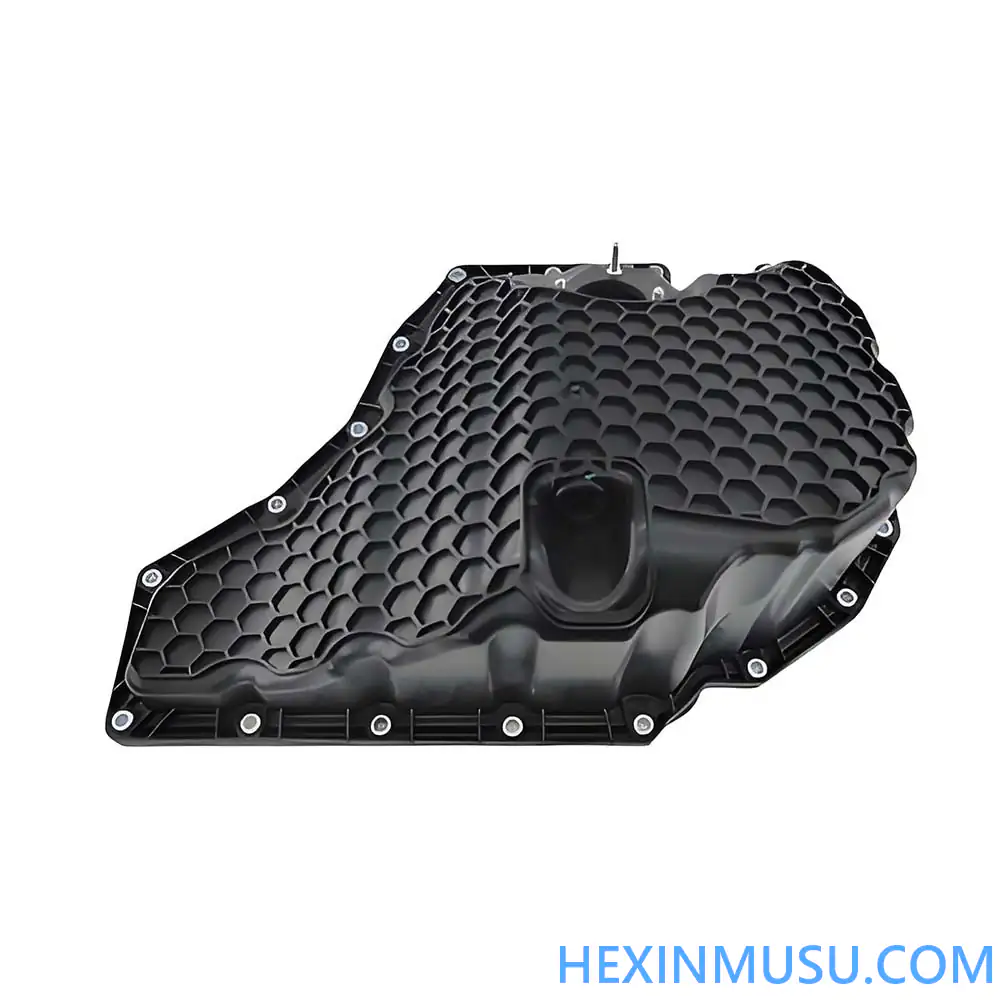
Aluminum oil pan
aluminum The oil pan is made of aluminum alloy, so it has good heat dissipation performance, light weight, strong corrosion resistance, can withstand a large amount of impact, and has a certain degree of strength. However, the aluminum alloy oil pan is usually die-cast, the process has a low cost of mass production, but the mold cost is high, not suitable for customized manufacturing. It is usually used by automobile factories for mass production. In order to further meet the demand for customization, some customers use Low-pressure casting or Gravitational castingThis process allows for the use of low-strength molds (relatively inexpensive) to greatly reduce costs, relatively thick products, heat-treated performance is higher than the die casting, usually in the tuning cars, racing cars, antique cars and other customized industry more.
iron oil sump
Iron oil sump according to the thickness of different process casting, there are stamping oil sump (about 2mm) and cast iron oil sump, stamping oil sump through the press brake with robotic arm Stamping made of light weight, manufacturing process, lower cost, suitable for mass production, however, due to the stamping of the oil pan is relatively thin and stamping process, product rigidity is poor (stamping equivalent to the product received an impact), can not manufacture complex structures, usually can not be repaired and can only be replaced. Cast iron oil bottom as a result of thicker after t6 heat treatment has a particularly high strength (much higher than aluminum alloy) weight, however, the shortcomings are also very obvious, the weight is greater, the cost is also higher, the lack of toughness, easy to crack by impact. Manufacturing cost is more expensive.
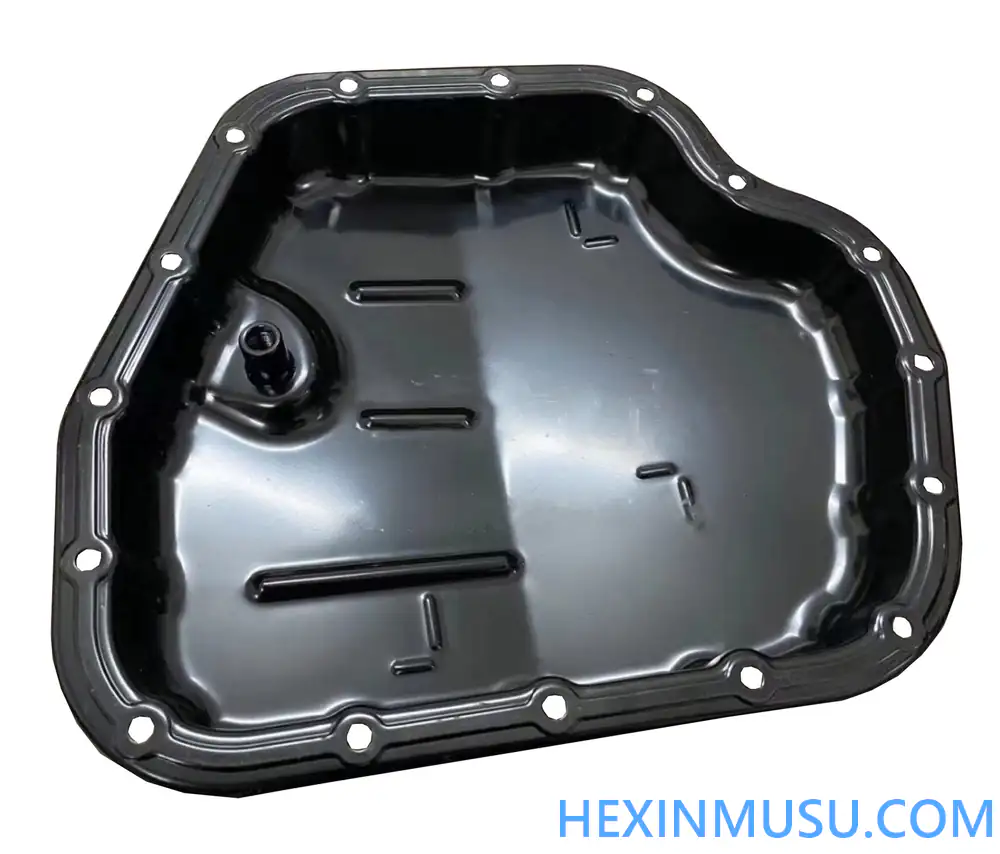
Aluminum alloy oil pan production process.
Ningbo Hexin aluminum alloy oil pan manufactured by die-casting and low-pressure casting, gravity casting of the three production processes, low-pressure casting and gravity casting in addition to the production of different machines process is relatively similar.
Die casting oil sump production process.
Oil sump raw material melting (die-cast aluminum alloy)→ machining → De-gating/Slagging Packaging → Grinding → Shot Peening → Product Machining → Packaging & Shipping → Inspection
Low pressure casting/gravity casting oil sump production process.
Oil pan raw material melting (cast aluminum alloy) → low pressure/gravity casting machining → de-gating → grinding → heat treatment solution → heat treatment tempering → shot blasting → product machining → testing → packaging and shipping
Oil sump production quality control
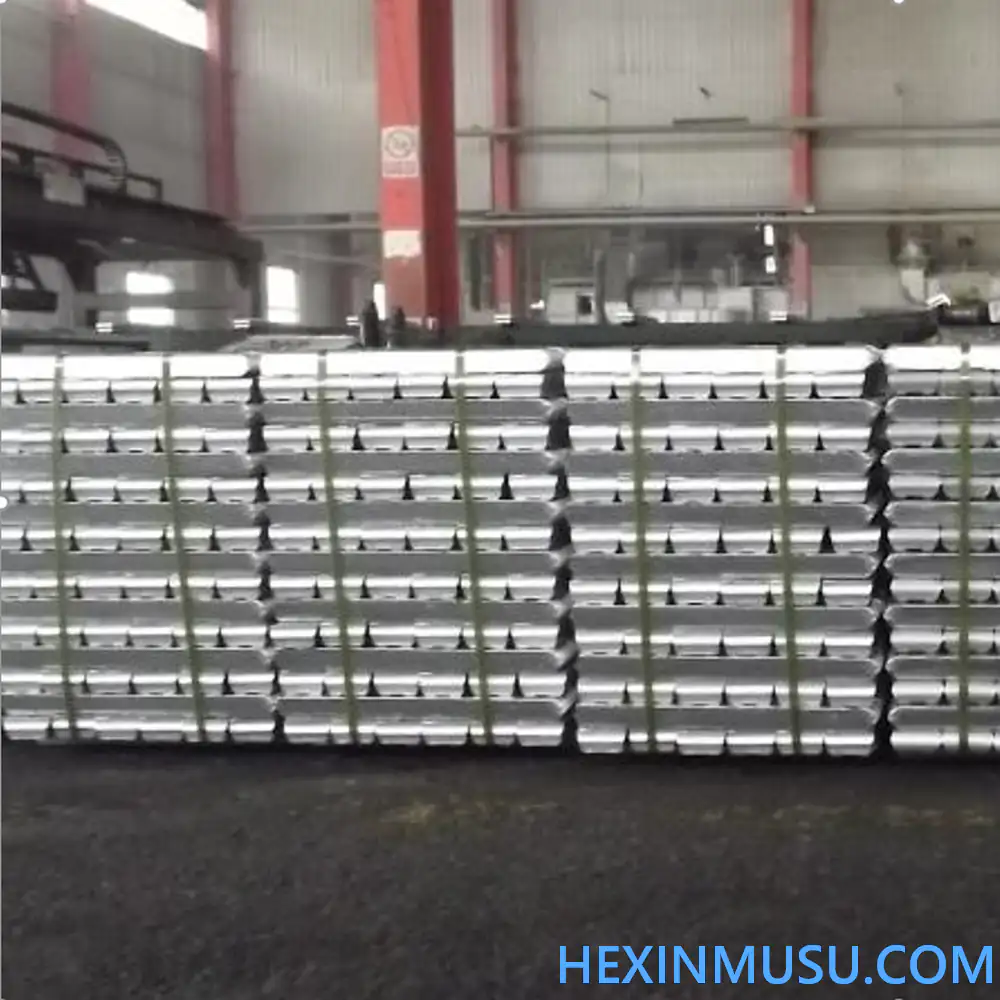
1. Material stabilization
Ningbo Hexin selects electrolytic aluminum ingots (non-recycled aluminum) from listed factories of Yunnan Aluminum Industry, which are good materials with good products. From the material to ensure that the product new energy is excellent and stable.
2. Reasonable production process
- A. Reasonable mold structure design, decades of experience in mold manufacturing makes the mold structure more reasonable.
- B. Advanced cae fluid squaring technology for perfect mold casting system
- C. Complete equipment, independent and controllable production makes the product more stable.
Common problems with aluminum oil pan production?
1. Material issues
The quality of aluminum alloy oil pan is directly affected by the raw materials. If the raw material does not meet the standard, such as uneven alloy composition, high impurity content, etc., it may lead to stretching and extrusion deformation of the oil pan in the process of use, which may cause cracks and other problems.
2. Casting defects
- stoma: Porosity is one of the common casting defects in aluminum alloy oil sumps. Porosity is caused by various reasons, including improper selection of gate location, poor exhaust, too deep mold cavity location, etc.. Porosity not only affects the appearance quality of the oil pan, but also may reduce its strength and sealing performance.
- cold storage: Cold segregation is a defect formed when two or more metal streams are not completely fused at the confluence due to low temperatures or poor flow of molten alloy during the mold filling process. Cold segregation also reduces the mechanical and sealing properties of the oil sump.
- Shrinkage and Shrinkage: Shrinkage and shrinkage are defects formed when the volume of liquid metal shrinks during solidification and is not replenished by sufficient liquid metal. These defects usually appear in the thick parts or hot joints of the casting, which adversely affect the strength and service life of the oil sump.
3. Processing issues
Poor surface quality: Poor surface quality is mainly characterized by large surface roughness and scratches. These problems not only affect the aesthetic appearance of the oil sump, but also may affect its sealing performance and wear resistance.
Insufficient dimensional accuracy: During the machining process, if the cutting parameters are not set properly or the tool is badly worn, it may lead to insufficient dimensional accuracy of the oil sump to meet the design requirements.