How the low pressure casting machine operates
Date: 2024-12-13 Categories: Blog Views: 4640
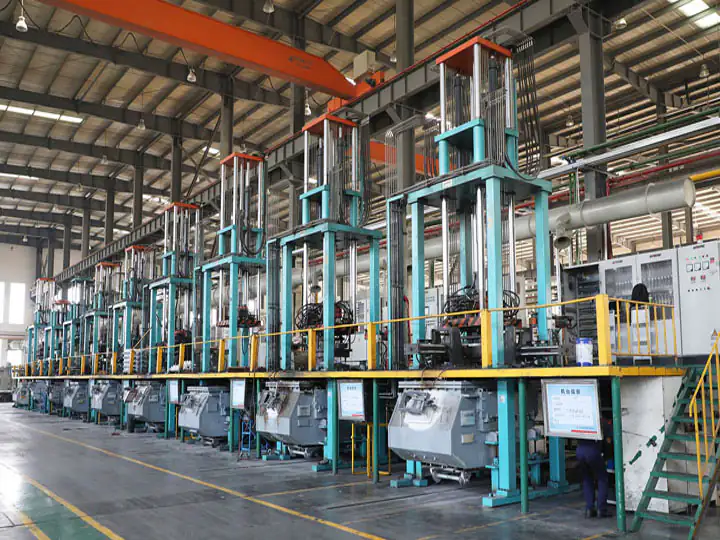
I. Operational overview
Low-pressure castingMachine is an important casting equipment that utilizes the principle of air pressure to realize metal liquid casting. In order to ensure the safe, stable and efficient operation of the equipment and to improve the quality and productivity of the casting products, this operating procedure has been developed. This procedure details the operation, maintenance and upkeep of the low pressure casting machine and is designed to ensure the safety of the operator and the normal operation of the equipment.
II. Operational content
1. preliminary
- Inspection equipment: Before starting a low pressure casting machine, first check that all systems of the equipment are working properly. This includes the furnace, injection system, mold and control system.
- Checking the mold: Check the cleanliness and integrity of the mold to make sure there are no breaks, dirt, or excessive buildup. If necessary, clean the mold and check the mold's cooling channels and exhaust system.
- Preparation of molten metal: The metal is prepared and heated to the appropriate temperature range for the type of alloy required. The temperature in the furnace is usually controlled ataluminumof the liquid temperature range (approx. 700°C - 750°C).
2. Heating and melting metals
- The metal is heated to a molten state by adding it to the furnace and starting the heating system. A constant temperature is maintained during heating to ensure the fluidity of the metal.
- The melted metal flows through the furnace opening into the injection system of the low pressure casting machine.
3. Setting Injection Parameters
- injection pressure: Setting the pressure for low-pressure injection. A common low pressure range is 0.1 MPa to 0.6 MPa. The choice of injection pressure affects the fluidity and quality of the casting.
- Injection time: Set the time for injecting the metal. The time for metal injection into the mold is usually controlled to ensure that the metal will fill the mold evenly.
- cooldown: According to the size of the casting and the design of the mold, set a reasonable cooling time to ensure that the casting can be completely cooled and solidified in the mold.
4. low-pressure injection
- Starting a low-pressure injection system. A low-pressure casting machine injects molten metal at low pressure into the mold cavity by means of a compressed gas (usually air or nitrogen). The pressure of the gas is usually between 0.1 and 0.6 MPa, and the process of low-pressure injection is somewhat slower than high-pressure casting.
- During the injection process, ensure that the injected metal is uniform and free of air bubbles. The gas compression system needs to provide a steady pressure to ensure that the metal completely fills the mold.
5. Cooling & Curing
- After the molten metal is injected into the mold, it is rapidly cooled and solidified by the cooling system. The control of the cooling process is critical, and the cooling time and rate directly affect the quality of the casting.
- Cooling water pipes or other cooling medium channels inside the mold ensure uniform temperature control of the mold to prevent castings from warping, cracking and other defects.
6. Venting and deslagging
- The venting system ensures that gas and excess air in the mold is vented when the molten metal is injected into the mold, avoiding porosity or other defects in the casting.
- The slag removal system removes impurities and oxides from the molten metal of aluminum alloys, ensuring a smooth surface of the casting.
7. Ejector castings
- Once the casting has finished cooling and solidified, the ejection system of the low pressure casting machine starts working. The casting is ejected from the mold by a pneumatic or hydraulic device.
- When ejecting, it is necessary to ensure that the casting is not damaged and to avoid surface scratches or deformation.
8. reprocess
- Aluminum alloy castings completed by forging usually need to go through deburring, polishing, cleaning and other post-treatment steps to improve the appearance and surface quality of the castings.
- Some castings may also require heat treatment to increase strength and hardness.
9. Inspection and Maintenance
- After each casting, check the quality of the castings to ensure that they meet the design requirements. Check the castings for defects such as porosity, cracks and deformation.
- Regular maintenance and servicing of the equipment, including inspection of key components such as molds, injection systems, cooling systems, etc., to ensure proper operation of the equipment.
III. Precautions
Control of molten metal temperature
- Keep the temperature of the molten metal in the right range to avoid too high or too low temperatures, which can affect the fluidity of the metal and thus the quality of the casting.
Reasonable setting of injection pressure and speed
- Setting the right injection pressure and speed ensures that the metal fills the mold evenly and avoids porosity and inclusions.
Optimization of the cooling system
- Ensure that the cooling system works well and maintains the uniformity of the mold temperature, which contributes to the stability and precision of the castings.
Regular cleaning and inspection of molds
- Regularly clean the molds to remove deposited impurities and check the cooling channels and exhaust system of the molds to ensure that the molds are not clogged or damaged in long-term use.
Technical requirements for operators
- The operation of the low pressure casting machine requires skilled operators, operators should be regularly trained to master the operation process, maintenance and troubleshooting skills of the equipment.
These operating procedures are the latest operating requirements for low-pressure casting machines and should be strictly observed by the operator to ensure safe, stable and efficient operation of the equipment.