Determination of machining allowances for CNC machine tools
Date: 2025-01-17 Categories: Blog Views: 2267
Confirmation of CNC machining allowances
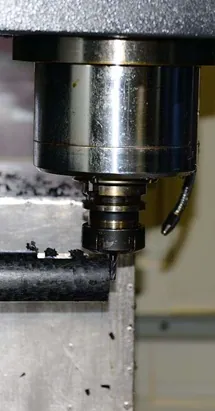
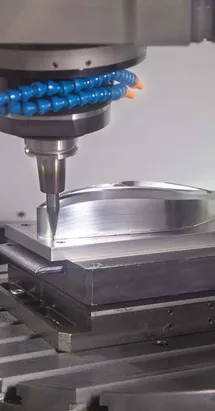
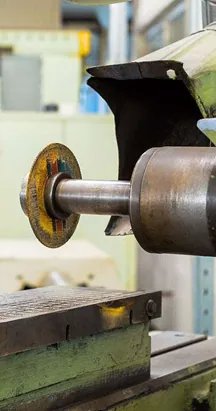
What is CNCtolerance (i.e. allowed error)?
1. Refers to the machining thickness reserved for processing the required products, and after removing the reserved thickness can get the size, shape and positional accuracy of the workpiece that meets the requirements.
2. The size of the machining allowance directly affects the machining efficiency and machining quality, so the reasonable determination of the machining allowance is an important part of the CNC machine tool processing.
CNCFactors affecting machining allowances:
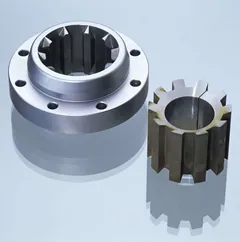
Workpiece materials
The hardness, strength, toughness and other physical properties of the workpiece material have a greater impact on the size of the machining allowance.
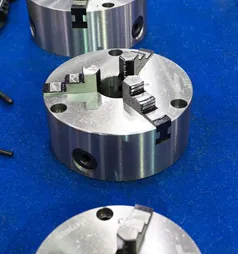
Tool performance
Properties such as tool sharpness, wear resistance, and rigidity affect the determination of machining allowances.
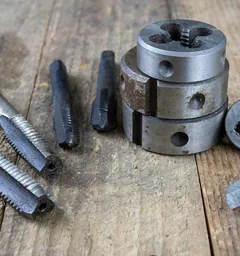
Machine accuracy
The positioning accuracy of the machine tool, the repeatability of the positioning accuracy, and the stability of the transmission system all affect the determination of the machining allowance.
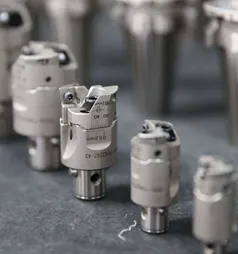
Processing
Different machining processes (e.g. roughing, semi-finishing, finishing) require different machining allowances.
CNCMethod of determining machining allowances:
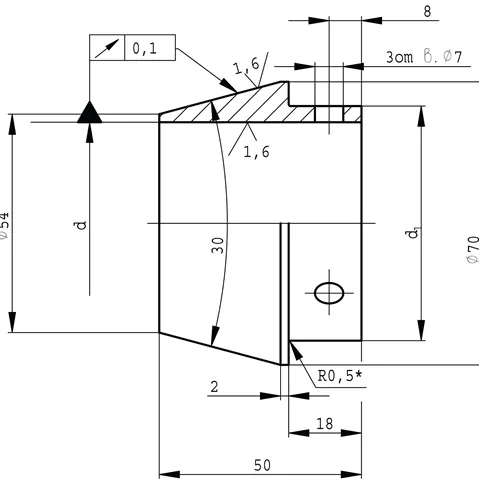
Determined on the basis of experience
Determine the size of the machining allowance based on actual machining experience and in conjunction with similar cases.
experimental method
By means of test cutting, we observe the change of cutting force, cutting temperature and other parameters to determine the reasonable machining allowance.
the analytic method
Through the establishment of mathematical models or simulation models, analyze the influence of workpiece materials, tools, machine tools and other factors on the machining allowance, so as to determine a reasonable machining allowance.
Calculation of machining allowances for CNC machine tools
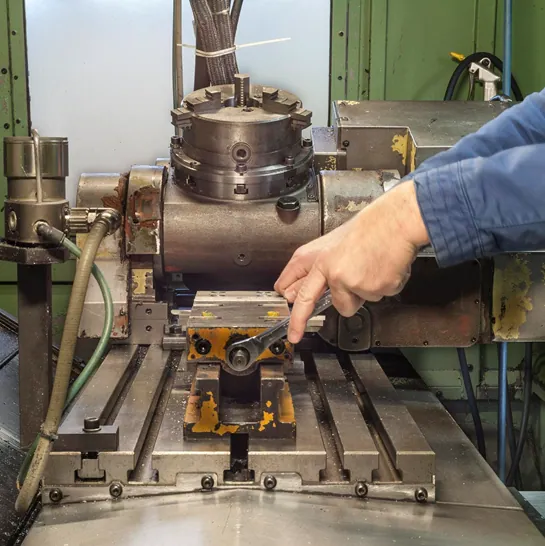
Depth of cut
Depending on the workpiece material and machining requirements, the depth of cut is determined so that the machining allowance can be calculated.
cutting speed
Different cutting speeds affect the magnitude of the cutting forces, which in turn affects the determination of the machining allowances.
Feed rate
The size of the feed rate affects the roughness of the cutting surface and thus the determination of the machining allowance.
Machining allowance calculation based on workpiece material
Material hardness
Harder materials may require larger machining allowances.
Material toughness
Tougher materials tend to generate heat and cutting forces during machining and therefore require larger machining allowances.
Material heat treatment status
Materials in different states of heat treatment will have different hardnesses and toughnesses, which will affect the determination of machining allowances.
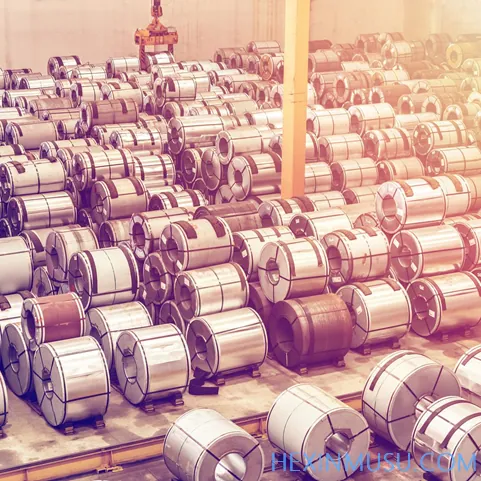
Machining allowance calculation based on tool wear
Tool wear level
A tool with a high degree of wear affects the roughness of the cutting surface and thus the determination of the machining allowance.
Tool life
When tool life is short, larger machining allowances are required to avoid tool breakage.
Tool Type
Different types of tools have different cutting properties, so it is necessary to determine the appropriate machining allowance according to the type of tool.
Optimization objectives and constraints
Optimization goals
Minimize machining allowance and improve machining efficiency under the premise of meeting machining accuracy and surface quality.
restrictive condition
Cutting forces, cutting heat, tool wear and other factors during machining need to be within tolerable limits, while ensuring the stability and reliability of the machining process.
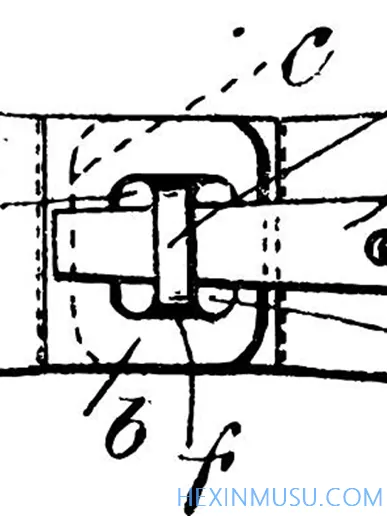
Selection and Application of Optimization Algorithms
genetic algorithm
Global search for optimal solutions by modeling the genetic mechanism in biological evolution. Applicable to multivariate, nonlinear, discrete optimization problems.
particle swarm algorithm
Simulate the foraging behavior of biological groups such as bird flocks and fish schools to find the global optimal solution through information sharing and collaboration among individuals. Applicable to continuous type optimization problems.
simulated annealing algorithm
Drawing on the principle of solid annealing, avoiding falling into local optimal solutions through stochastic search and probabilistic acceptance of inferior solutions. Applicable to multi-constraint, nonlinear optimization problems.
Machining allowance optimization case study
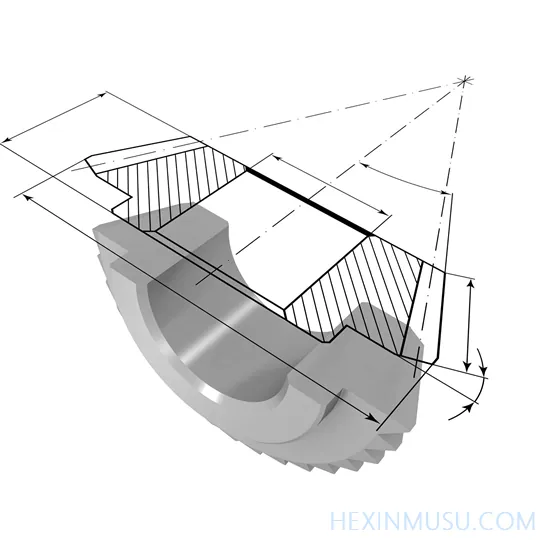
Example 1
For the machining allowance optimization of a complex surface part, genetic algorithm is used to optimize the machining parameters, which achieves a significant reduction of machining allowance and improves the machining efficiency.
Example 2
For the machining allowance optimization of an aero-engine blade, the particle swarm algorithm is used to plan the cutting path, which effectively reduces the machining allowance and reduces the tool wear under the premise of ensuring the machining accuracy.
Example 3
For the optimization of machining allowance of a mold cavity, the cutting parameters are optimized by simulated annealing algorithm, which achieves the minimization of machining allowance and improves the machining quality and efficiency.
Control of machining allowances on CNC machine tools
Real-time data collection
Through sensors and monitoring equipment, real-time acquisition of CNC machine tool machining data, such as cutting force, cutting temperature, tool wear and so on.
Data analysis and processing
The collected real-time data is processed and analyzed to assess the stability of the machining process and to predict margin variations.
Abnormality Detection and Alarm
Through the real-time monitoring system, abnormalities in the machining process, such as excessive tool wear, abnormal cutting force, etc., are detected in a timely manner and alarms are issued.
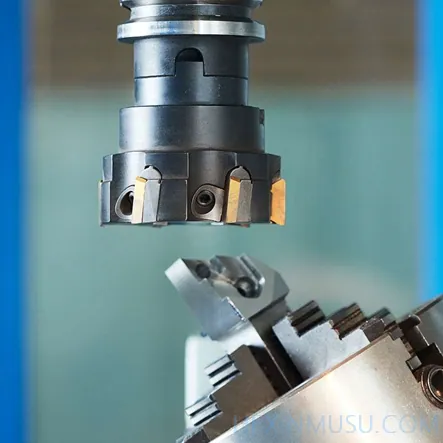
CNC machiningEarly warning system in case of insufficient margin
- Residual threshold setting : According to the processing requirements and process parameters, a reasonable margin threshold is set, and the warning is triggered when the margin is lower than the threshold.
- Early warning methods : Through sound and light and other means, timely warning signals are sent to the operator to remind the operator to pay attention and take corresponding measures.
- Early warning recording and handling : Early warning information is recorded and organized for subsequent analysis and processing, while appropriate measures are taken to adjust machining parameters or change tools.
Design and realization of margin control system
System Architecture Design
According to the demand of CNC machine tool machining allowance control, design a reasonable system architecture, including hardware and software parts.
Data processing algorithms
Research and development of data processing algorithms applicable to real-time monitoring and early warning systems to improve data processing speed and accuracy.
System Integration and Commissioning
Integration of individual modules into the system, debugging and optimization of the
Trends in margin determination techniques
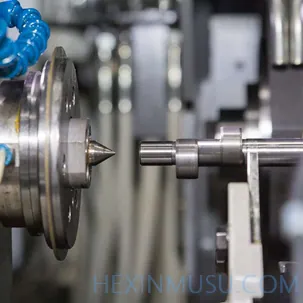
intellectualize
Utilizing artificial intelligence and machine learning technology to realize automatic identification and prediction of machining allowances to improve machining accuracy and efficiency.
refinement
Realize precise control of machining allowances to meet the demand for high precision machining through high precision measurement and data processing technology.
integration
Integration of margin determination technology with process planning, machining simulation, etc., to achieve comprehensive optimization of the machining process.
Innovative directions in margin optimization technology
Technological innovations
Research new machining processes and methods to reduce machining allowance and improve machining efficiency.
Material Innovation
Development of new materials to reduce the influence of materials on machining allowances and improve machining quality.
Algorithmic Innovation
Research new algorithms and technologies to optimize the calculation and control of machining allowances and improve machining accuracy.
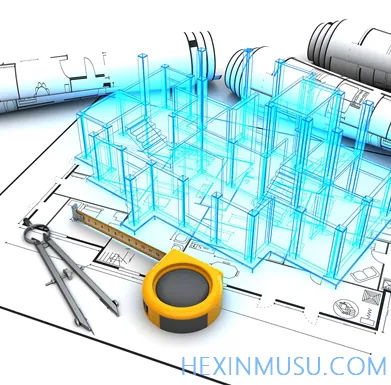
CNCFuture prospects for margin control technology
Real-time monitoring
Realize real-time monitoring of the machining process, timely adjustment of the machining allowance to ensure the quality of machining.
automatic control
Realize automatic control of machining allowance and improve machining efficiency.
Intelligent Decision Making
Intelligent decision-making and control of machining allowances using artificial intelligence technology.