La historia del desarrollo del torno CNC: del torneado básico a la revolución tecnológica en la fabricación de piezas complejas
Fecha:2025-02-24 Categorías:Blog Vistas:163
Como fósil viviente de la civilización industrial, la evolución del torno CNC traza la eterna búsqueda de la fabricación de precisión. Desde 1300 aC artesanos egipcios con cama giratoria de madera impulsada por cuerda, hasta el siglo 21 equipado con algoritmos de IA de cinco ejes de máquinas herramientas inteligentes, la tecnología siempre ha estado en la redefinición de la "precisión" de los límites del período de la revolución industrial de torno de vapor se comprimirá a 0,1 mm de error de procesamiento, mientras que el moderno sistema CNC a través de la escala de control de bucle cerrado ha logrado 0,0000 mm. Durante el período de la revolución industrial, los tornos accionados a vapor comprimían los errores de mecanizado a 0,1 mm, mientras que los modernos sistemas CNC han logrado un control microscópico de 0,001 mm mediante el control de escala de bucle cerrado. Especialmente en el sector de alto rendimientoaluminioEn el campo de la fabricación de componentes, la capacidad sinérgica multieje del torno CNC ha cambiado por completo el proceso tradicional: tomemos como ejemplo la carcasa del motor de un vehículo de nueva energía, el mecanizado compuesto de su pieza dentada de disipación de calor y la broca del cojinete se pueden completar a la vez en el sistema CNC integrado con la torreta de potencia del eje Y, que puede mejorar la eficiencia en 400% en comparación con el mecanizado secuencial tradicional, y controlar el error de coaxialidad dentro de 5μm, y este salto tecnológico no sólo reconfigura el proceso de producción, sino que también promueve el límite de ingeniería del diseño ligero. Este salto tecnológico no solo reconfigura el proceso de producción, sino que también impulsa los límites de ingeniería del diseño ligero.
El desarrollo de las máquinas herramienta CNC
Una máquina herramienta CNC es una máquina herramienta que utiliza información en forma de código digital (instrucciones de programa) para controlar la herramienta con el fin de realizar un mecanizado automático según un programa de trabajo, una velocidad de movimiento y una trayectoria determinados, denominada máquina herramienta CNC.
intervalo de tiempo | evento de desarrollo | Características técnicas |
1952 | Parsons y el Instituto Tecnológico de Massachusetts (MIT) colaboraron en la fabricación de la primera fresadora CNC vertical del mundo con acoplamiento de tres coordenadas que utiliza el principio del multiplicador de impulsos. | Primeras exploraciones de la tecnología CNC con control por tubo de electrones |
1954 | Bendix USA fabricó la primera máquina herramienta CNC industrial del mundo. | El comienzo de la aplicación industrial de las máquinas herramienta CNC marca la madurez inicial de la tecnología CNC |
1959 | Los sistemas CNC evolucionaron hacia la segunda generación con controles transistorizados | Mayor fiabilidad y estabilidad de los transistores en comparación con las válvulas |
1965 | Los sistemas CNC han evolucionado hasta la tercera generación, que utiliza circuitos integrados de control a pequeña escala. | El uso de circuitos integrados mejora el rendimiento y la fiabilidad de los sistemas CNC |
1970 | Apareció la cuarta generación de CNC y se empezaron a utilizar miniordenadores para CNC. | La aplicación de la tecnología informática hace que el sistema CNC tenga un mayor nivel de inteligencia y automatización. |
1974 | Apareció la quinta generación de CNC y se empezaron a utilizar microprocesadores en los CNC. | Las aplicaciones de microprocesadores hacen que los CNC sean más flexibles y eficaces |
Finales de los 70-principios de los 80 | Estados Unidos, Alemania, Japón y otros países han hecho progresos significativos en el campo de las máquinas herramienta CNC, lanzando una serie de máquinas herramienta CNC de alto rendimiento. | La tecnología de las máquinas herramienta CNC está madurando gradualmente y su campo de aplicación se está ampliando. |
1980s | La producción japonesa de máquinas herramienta CNC supera a la de Estados Unidos, lo que la convierte en el mayor productor mundial de máquinas herramienta CNC. | La innovación tecnológica y el control de calidad en el campo de las máquinas herramienta CNC han convertido a Japón en líder del mercado mundial. |
De 1990 a la actualidad | La tecnología de las máquinas herramienta CNC sigue desarrollándose, los países han introducido máquinas herramienta CNC de alto rendimiento y alta precisión | Las máquinas herramienta CNC mejoran constantemente en términos de control, precisión, automatización y flexibilidad, y se utilizan ampliamente en los sectores aeroespacial, automovilístico, electrónico y otras áreas de fabricación de gama alta. |
2020s | La industria china de máquinas herramienta CNC se está desarrollando rápidamente, con notables avances tecnológicos, rompiendo el monopolio tecnológico extranjero. | China ha realizado progresos significativos en el campo de las máquinas herramienta CNC de gama alta, y la competitividad de mercado de las máquinas herramienta CNC de producción nacional ha seguido mejorando. |
Torno manual antiguo
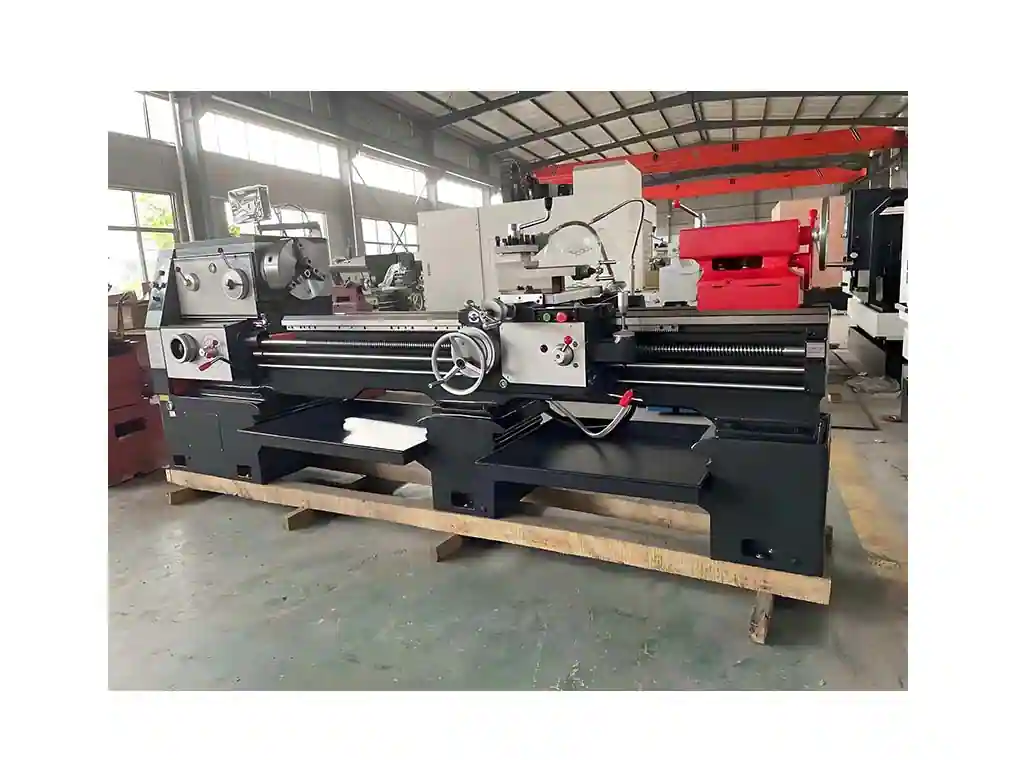
La esencia del mecanizado con torno es la delicada sinergia dinámica entre una pieza giratoria y una herramienta lineal. Los orígenes de esta técnica de fabricación se remontan a la antigua civilización egipcia, en el año 1300 a.C.: los artesanos utilizaban cuerdas hechas con tendones de animales para envolver la madera y conseguir un corte giratorio tirando hacia delante y hacia atrás, siendo pioneros en el primer método de mecanizado de componentes redondos.
El primer cambio cualitativo en la tecnología del torno se produjo durante la Revolución Industrial, cuando la explosiva demanda de la industria metalúrgica dio lugar al primer cambio cualitativo en la tecnología del torno. La introducción de la energía de vapor, la sustitución de la fuerza humana por un sistema de transmisión por correa y el diseño resistente a las vibraciones de la bancada de fundición dieron al torno la capacidad de producir piezas estándar en grandes cantidades por primera vez. El sistema de transmisión por correa nacido en esta época llevó la precisión del mecanizado al nivel milimétrico, sentando las bases de la ingeniería mecánica moderna.
Hoy en día, la penetración de la tecnología CNC ha reestructurado por completo el ADN del torno. El operario pasa de ser un trabajador manual a un arquitecto de programas, y la máquina herramienta evoluciona hasta convertirse en un terminal inteligente capaz de ejecutar de forma autónoma lógicas complejas. Esta transformación no sólo acorta el ciclo de procesamiento de superficies complejas en 60%, sino que también estabiliza la precisión dimensional a nivel de micras, marcando la entrada formal de la industria manufacturera en la era de la precisión digital.
Diseño básico y funcionamiento de los tornos manuales
El diseño modular del torno manual, piedra angular del mecanizado, sigue siendo hoy la inspiración de las máquinas-herramienta modernas. La sinergia de cada componente, desde la bancada de fundición hasta la transmisión de precisión, ilustra la sabiduría original de la ingeniería mecánica y proporciona la lógica subyacente para la evolución de la tecnología CNC.
sofá
La bancada de hierro fundido del torno manual adopta un diseño de estructura de caja, y el refuerzo interno tipo rejilla mejora significativamente la rigidez torsional, y su rendimiento de amortiguación de vibraciones puede absorber vibraciones de corte de más de 80%. La combinación de guía tipo V y guía plana con rectificado de precisión en la superficie de la bancada garantiza que la precisión lineal del movimiento de la placa de arrastre se controle dentro de 0,02 mm/m. Esta base de rigidez permite que el torno mantenga la estabilidad al procesar aleaciones de alta dureza, mientras que el material de hierro fundido con tratamiento de envejecimiento suprime eficazmente la deformación por aumento de temperatura y garantiza la precisión geométrica del mecanizado a largo plazo.
caja de husillo
La caja del husillo sirve como centro de potencia con un sistema de transmisión de engranajes de seis velocidades incorporado, que consigue una amplia gama de ajuste de velocidad de 45-2000rpm a través de un juego de engranajes deslizantes. El diseño modular del mandril autocentrante de tres mordazas y la pinza elástica permite cambiar rápidamente la solución de sujeción para piezas de Φ5-300 mm, lo que, junto con la interfaz del husillo con cono Morse, garantiza que la excentricidad radial de las piezas no supere los 0,03 mm. El diseño de la conexión de la palanca de velocidad variable y el embrague permite al operario cambiar sin problemas las velocidades de giro durante el proceso de corte, que se adapta a las necesidades de múltiples escenarios, desde el torneado de acabado de aleaciones de aluminio hasta el desbaste de acero inoxidable.
buggy
El sistema de placa de arrastre de material compuesto integra la función de alimentación longitudinal/transversal, guía de tornillo longitudinal de 6 mm/revolución, con dial para lograr una precisión de ajuste de 0,02 mm. El portaherramientas de torreta de cuatro estaciones soporta el cambio rápido de herramientas, completando el cambio multiproceso como torneado, ranurado y roscado en 15 segundos. Mediante la relación de engranajes de la caja de la rueda colgante, se pueden generar 60 pasos estándar de 0,5-10 mm para satisfacer la demanda de mecanizado de roscas de precisión de ejes de transmisión, tornillos y otras piezas, y su precisión de posicionamiento repetible alcanza ±0,01 mm.
Controles y sistemas sinérgicos
El sistema de control de tres volantes forma un paradigma único de interacción hombre-máquina: la mano izquierda regula el avance longitudinal (0,05-0,3 mm/r), la derecha controla la profundidad de corte transversal (±0,01 mm de precisión) y el pedal conecta el embrague para arrancar y parar el husillo. El tren de engranajes planetarios del portaherramientas descompone el movimiento del husillo en relaciones de avance precisas, mientras que el mecanismo de media tuerca sincroniza automáticamente el avance durante el roscado, una lógica mecánica que transforma los complejos procesos de mecanizado en operaciones manuales intuitivas.
Portaherramientas y lubricación
El portaherramientas cuadrilateral ajustable admite el ajuste fino de la altura de la herramienta ±2 mm y garantiza la rigidez del proceso de corte mediante el mecanismo de bloqueo de cuña. El sistema de lubricación por salpicadura proporciona un suministro continuo de aceite para los engranajes y 8 puntos de engrase manual para las piezas de fricción críticas, y el programa de lubricación compuesta permite que la máquina mantenga un coeficiente de fricción estable incluso después de 8 horas de funcionamiento continuo. El mecanismo de ajuste del ángulo del portaherramientas permite ajustar el ángulo de inclinación de -5° a 45°, lo que satisface los requisitos de mecanizado de conos, esferas y otros contornos perfilados.
Explicación detallada de las limitaciones del torno manual
automatización limitada
Cuando se mecanizan engranajes de transmisiones de automóviles, el operario tiene que sincronizar la velocidad de avance, la profundidad de corte y la velocidad del husillo, lo que lleva hasta 50 minutos para una sola pieza de mecanizado, mientras que el equipo CNC sólo tarda 12 minutos. Esta gran dependencia de la intervención manual provocó una pérdida de eficiencia de 35% en la producción en serie, y la tasa de desechos de los operarios novatos era cinco veces superior a la de la mano de obra cualificada.
La complejidad de la precisión
En el mecanizado de carcasas de inyectores diésel, las diferencias en la experiencia del operario pueden provocar fluctuaciones en los tamaños críticos de los orificios de entre 0,05 y 0,12 mm. La deformación térmica de la bancada desplaza el contrapunto 0,03 mm tras 4 horas de mecanizado continuo y el desgaste de las herramientas acumula un error de 0,1 mm por cada 20 piezas, variables que dificultan garantizar la uniformidad en las piezas por lotes.
Ajustes que consumen tiempo
Un lote de 1.000 piezas del caso de procesamiento de la carcasa del cojinete muestra que el cambio de torno tradicional necesita ajustar la posición del contrapunto (que consume tiempo de 25 minutos), la recarga de los accesorios (15 minutos), la calibración de corte de prueba (30 minutos), el tiempo de preparación representó el total de horas-hombre de 28%. En contraste, el equipo CNC puede ser llamado a través del programa para completar toda la gama de parámetros en 8 minutos para cambiar, lo que pone de relieve el cuello de botella de la eficiencia del modo manual de producción de gran volumen.
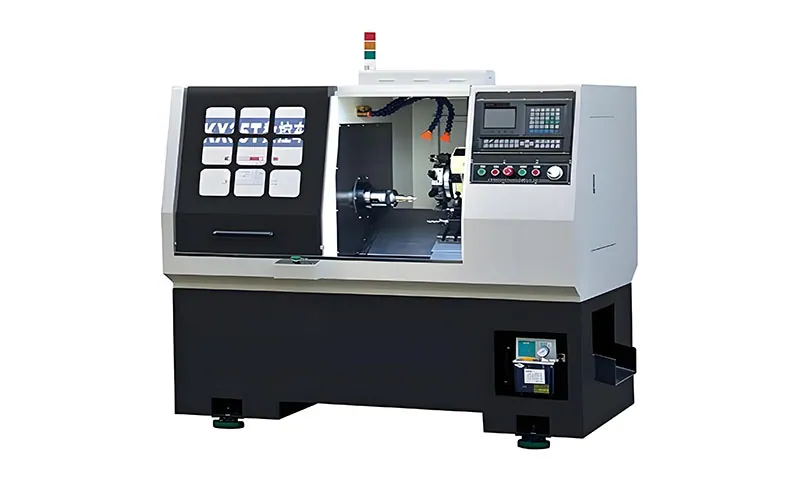
Torno CNC moderno
Como equipo central del sistema de fabricación inteligente, el torno CNC moderno está redefiniendo los límites de la fabricación de precisión mediante la profunda integración de la tecnología digital y la ingeniería mecánica. Su evolución tecnológica no solo se refleja en la actualización del hardware, sino también en el desarrollo pionero del sistema de control inteligente.
sistema de control
Los tornos CNC modernos están equipados con un sistema de control digital que actúa como sistema nervioso central del equipo, coordinando el funcionamiento coordinado del husillo, los ejes de avance y los dispositivos auxiliares en tiempo real a través de un bus de datos de alta velocidad. El módulo de compensación de errores incorporado en el sistema puede corregir automáticamente la holgura de transmisión mecánica y la deformación térmica provocada por una pequeña desviación, con el mecanismo de retroalimentación de bucle cerrado de la báscula, para estabilizar la precisión de posicionamiento en la categoría de nivel de micras. Esta lógica de control digital cambia por completo el modo de funcionamiento del mecanizado tradicional, que se basa en la experiencia manual, y permite que la precisión del contorno de superficies complejas alcance el nivel de 1/10 del diámetro de un cabello.
Interfaz de programación de fácil manejo
La interfaz hombre-máquina inteligente revoluciona la creación de programas de mecanizado, con un módulo de simulación 3D que visualiza las trayectorias de las herramientas y los procesos de arranque de material. El operario puede generar rápidamente código G mediante la función de programación de arrastrar y soltar, y el sistema optimiza automáticamente la combinación de parámetros de corte e incluso reconoce las características del dibujo para recomendar estrategias de mecanizado. El diseño de fusión de pantalla táctil y comando de voz mejora la eficacia de depuración del equipo por 60% y reduce significativamente el umbral de dependencia de los conocimientos de programación.
Algoritmos de control adaptativo
El núcleo inteligente de la máquina ajusta dinámicamente la velocidad de avance y la carga del husillo mediante una red multisensor que recopila datos en tiempo real sobre fuerzas de corte, espectros de vibración y cambios de temperatura. Al mecanizar componentes aeroespaciales de titanio, el algoritmo identifica los puntos duros del material y reduce automáticamente la profundidad de corte para evitar el astillado de la herramienta. Esta capacidad de autooptimización permite a la máquina mantener la máxima eficiencia durante el mecanizado continuo, prolongando la vida útil de la herramienta en más de 30%, al tiempo que garantiza una rugosidad superficial estable de Ra0,8μm o inferior.
Capacidades de procesamiento más avanzadas
La tecnología de unión de 5 ejes rompe la limitación de la dimensión de movimiento de las máquinas herramienta tradicionales y realiza el mecanizado completo de piezas complejas, como álabes de turbina, mediante la sinergia del cabezal pendular del eje B y la mesa giratoria del eje C. El diseño de la torreta motorizada con husillo de fresado integrado permite el mecanizado simultáneo de orificios transversales y características finales durante el torneado, eliminando los errores de sujeción secundarios. La capacidad multitarea permite concentrar en una sola máquina procesos que de otro modo requerirían 3 máquinas para completarse, comprimiendo el tiempo del ciclo de producción en 40%.
Tecnología de automatización integrada
El sistema modular de cambio automático de herramientas está equipado con un almacén de herramientas de 40 estaciones, que puede completar el cambio de herramientas en 0,8 segundos y comprobar automáticamente los parámetros de las herramientas mediante chips RFID. El sistema de refrigeración inteligente ajusta el ángulo de pulverización del fluido de corte y el caudal en función de las características del material procesado, y se adopta la tecnología de microlubricación para reducir el consumo de refrigerante en 85% durante el mecanizado de aleaciones de aluminio.La sonda de inspección de piezas incorporada mide las dimensiones clave automáticamente durante el hueco de mecanizado, y los datos de retroalimentación en tiempo real se retroalimentan al sistema de control para realizar correcciones compensatorias, formando así una gestión completa de bucle cerrado de la calidad.
Comparación entre el núcleo del torno manual y el del torno CNC
dimensión de comparación | torno artesanal | Torno CNC |
---|---|---|
Precisión de mecanizado | ±0,05~0,1 mm (depende de la habilidad del operario) | ±0,005~0,01 mm (control de bucle cerrado de escala) |
eficacia de la producción | Elevado consumo de tiempo por pieza (por ejemplo, 30 minutos para el mecanizado de ejes escalonados). | Producción rápida de lotes (mecanizado de la misma pieza en 5 minutos) |
complejidad operativa | Se requiere un técnico cualificado (más de 3 años de experiencia) | Programado para funcionar automáticamente (1 semana de formación en funcionamiento básico para empezar a trabajar) |
Coste inicial | 30.000~100.000 yenes (equipo básico) | ¥200.000~2 millones (modelo de 5 ejes) |
Capacidad de producción flexible | Adecuado para una sola pieza/lote pequeño (el ajuste de cambio tarda 1~2 horas) | Admite piezas de gran volumen/complejas (el proceso de cambio dura sólo 5 minutos) |
aplicación típica | Mantenimiento de moldes, enseñanza práctica, producción artesanal | Piezas aeroespaciales, piezas de automoción, dispositivos médicos |
ratio de consumo de energía | Consumo medio 3~5 kW-h (sin pérdida en modo de espera) | Consumo medio de energía 10~30 kW-h (incluido el sistema de refrigeración/cambio de herramientas) |
coste de mantenimiento | Cuota de mantenimiento anual ¥0,5~10.000 (las piezas mecánicas son fáciles de sustituir) | Cuota anual de mantenimiento ¥30.000~100.000 (requiere ingenieros profesionales para su mantenimiento) |
Análisis en profundidad de las ventajas e inconvenientes
Ventajas de los tornos manuales
- Producción flexible a bajo coste
- Adecuado para empresas de nueva creación: 1/10 del coste de adquisición del equipo CNC
- Rápida respuesta a los cambios: no es necesario programar para ajustar las trayectorias de las herramientas (por ejemplo, mecanizado de piezas de bronce conformadas).
- Valor técnico del patrimonio
- Desarrollo de la intuición mecánica: el operario puede visualizar las fuerzas de corte y las propiedades del material.
- Estadísticas de una escuela técnica de Ningbo: la formación práctica en torno manual permite a los estudiantes mejorar la precisión en la selección de herramientas 40%
Ventajas del torno CNC
- Capacidad de mecanizado de piezas complejas
- Vinculación de 5 ejes: se pueden mecanizar álabes de turbina (precisión de superficie ±0,005 mm)
- Fresado-torneado: taladrado y roscado simultáneos (por ejemplo, ahorro de 3 procesos en el mecanizado de manguetas de dirección de automóviles).
- Garantía de coherencia de la producción
- Fluctuación dimensional <0,01 mm para procesamiento por lotes de 2000 piezas.
- Datos de una fábrica de productos sanitarios:mecanizado por control numéricoTasa de aprobación de rosca de clavo óseo 99,7%, sólo manual 82%
Sugerencias para la selección
Escenarios de requisitos | Equipamiento recomendado | razonamiento |
---|---|---|
Enseñanza/prototipos (presupuesto limitado) | torno artesanal | Ensayo y error de bajo coste para desarrollar habilidades básicas |
Pequeños lotes con muchas variedades (<100 piezas) | Torno CNC económico | Reducción del coste unitario gracias a la reutilización de procesos |
Grandes cantidades de piezas de precisión (>1000 piezas) | Torno CNC de alta gama | Producción automatizada + sistema de trazabilidad de la calidad, reducción integral de los costes de 40% |
Piezas ultracomplejas (por ejemplo, aeroespaciales) | Centro de torneado y fresado de 5 ejes | Mecanizado de varias caras en una sola sujeción, evitando errores de referencia. |
Escenarios de aplicación diversificados para los tornos CNC
Como equipo central de la industria manufacturera moderna, el torno CNC ha penetrado en varias áreas clave de la producción industrial en virtud de su alta precisión y alta flexibilidad. Desde piezas de precisión micrométrica hasta el procesamiento de componentes grandes y complejos, sus ventajas tecnológicas están reconfigurando el panorama de la fabricación mundial.
Fabricación de piezas geométricas complejas
En el campo aeroespacial, el torno CNC de enlace de cinco ejes puede completar una sola vez el álabe de turbina (como la Figura 1) de la mortaja y ranura de la raíz de la hoja y el procesamiento del orificio de enfriamiento de la película de aire, el proceso tradicional de 12 procesos reducidos a 3, la precisión del contorno de la hoja de ± 0,005 mm. un modelo de caso de mecanizado de disco presurizado de alta presión de motor de avión muestra que el uso de fresado y torneado de tecnología compuesta, el ciclo de producción se comprime de 72 a 18 horas, y la excentricidad. El error se controla dentro de 5μm.
Fabricación de moldes de precisión
Ningbo, ciudad subprovincial de Zhejiangmolde de fundición a presiónEn el clúster industrial, los tornos CNC se encargan del mecanizado de precisión de los núcleos clave de los moldes. Al procesar moldes de carcasas de motores de vehículos de nueva energía, el torneado multiángulo de agujeros profundos (con una relación profundidad-diámetro de 15:1) mediante el sistema de canal caliente aumenta la vida útil del molde hasta 500.000 ciclos de troquelado. El módulo de mecanizado de roscas de precisión puede generar micropasos de 0,2 mm para satisfacer los requisitos de moldeo de microconectores.
Producción en serie de piezas de automoción
- sistema del motor: Torneado escalonado de muñones de cigüeñal con error de redondez ≤ 0,003mm.
- sistema de transmisiónTorneado en duro de piezas brutas de engranajes para cajas de cambio (HRC60) como alternativa a los procesos de rectificado convencionales
- Componentes electrificadosEquilibrado dinámico de alta velocidad de rotores de motor con amplitud <0,01 mm a 8000 rpm.
4. Fabricación de productos sanitarios
El torneado de aleaciones de titanio para articulaciones artificiales utiliza tecnología de microlubricación con rugosidad superficial Ra0,2μm para cumplir los requisitos de implantación. El mecanizado de microroscas de tornillos ortopédicos (M0,6×0,125) consigue una precisión de posicionamiento de 0,01° mediante indexación en el eje C, lo que garantiza la fiabilidad del engranaje de la rosca.
5. Tratamiento de equipos energéticos
El mecanizado de la aleación de alta temperatura Inconel 718 para el impulsor de la bomba principal de una central nuclear prolonga la vida útil de la herramienta en 40% ajustando dinámicamente los parámetros de corte mediante algoritmos de control adaptativo.El torneado intermitente de los anillos de los rodamientos de las turbinas eólicas adopta una tecnología de supresión de vibraciones para aumentar 3 veces la eficacia del mecanizado.
Comparación de datos de aplicaciones industriales
Ámbitos de aplicación | Piezas típicas | Requisitos de precisión | Aumento de la eficiencia |
---|---|---|---|
aeroespacial | pala de turbina | ±0,005 mm | 300% |
fabricación de automóviles | muñón del cigüeñal | Redondez 0,003 mm | 150% |
equipamiento médico | articulación artificial | Ra0,2μm | 200% |
Equipamiento energético | Impulsor nuclear | Contorno 0,01 mm | 250% |
Preguntas y respuestas frecuentes
¿Cómo dieron los tornos CNC el salto del mecanizado básico a la fabricación compleja?
Los tornos CNC han evolucionado a través de tres grandes revoluciones tecnológicas:
- Fase mecatrónica (1950-1970):
- Mecanizado automatizado de piezas de eje sencillas mediante programación con cinta perforadora (precisión ±0,1 mm)
- Caso típico: GM utiliza el primer torno CNC para mecanizar engranajes de transmisión, aumentando la eficiencia en 200%.
- Fase de control digital (1980-2000):
- Introducción de la tecnología de microprocesador, compatible con la interpolación de arco y la conexión multieje (precisión ±0,02 mm)
- Caso innovador: mecanizado en 5 ejes de discos de turbina de motores Boeing 747, reduciendo el plazo de producción de 30 a 7 días.
- Fase de fabricación inteligente (2010 hasta hoy):
- Integración de algoritmos de IA y tecnologías IoT como Mazak iSMART Factory para el control a nivel de 0,0001 mm.
- Una empresa de moldes de fundición a presión de Ningbo redujo el número de pruebas de moldes de 15 a 3 gracias a la tecnología de gemelos digitales.
¿Cómo equilibrar la eficiencia y la protección medioambiental del torno CNC?
- Tecnología de mejora de la eficiencia:
- El sistema de cambio automático de herramienta (tiempo de cambio de herramienta ≤ 0,8 s) aumenta la eficiencia del procesamiento por lotes en 60%.
- La tecnología de corte de alta velocidad (velocidad del husillo de 30.000 rpm) comprime el tiempo del ciclo de mecanizado de aleaciones de aluminio en 40%
- Innovación sostenible:
- Sistema de lubricación micro-cantidad (MQL) para reducir el uso de fluido de corte 90%, ahorro de costes anuales de ¥ 150.000 / unidad.
- El módulo de recuperación de energía convierte la energía de frenado en energía eléctrica para su reutilización, reduciendo el consumo de energía en 25%
- Una fábrica de piezas de automóviles de nueva energía optimizó la disposición de materiales mediante CNC, la tasa de utilización de materiales aumentó de 68% a 92%.
¿Pueden los modernos tornos CNC manipular tanto piezas sencillas como complejas?
- Mecanizado de piezas sencillas:
- Producción estable de 60 piezas por minuto mediante macros para la producción por lotes de tornillos
- El error de mecanizado del eje escalonado se controla en ±0,005 mm, lo que supone una precisión 5 veces superior a la de los tornos tradicionales.
- Avance en piezas complejas:
- Mecanizado por fresado-torneado en 5 ejes de cargadores de motores aeronáuticos con 200 características en una sola sujeción.
- Procesamiento de articulaciones artificiales de cadera en el ámbito médico con una precisión esférica de Ra0,1μm (equivalente al efecto espejo).
- Una empresa de Ningbo procesa carcasas de aleación de aluminio de pared fina de 0,2 mm con un torno CNC, con una deformación <0,03 mm.