Proceso de fundición en arena
Fecha:2024-10-08 Categorías:Blog Vistas:1997
¿Qué es el moldeo en arena?
fundición en arena La fundición en arena, también conocida como moldeado en arena, es un método de fundición tradicional con una amplia gama de aplicaciones en todo el mundo. Se trata de un método de proceso para producir piezas de fundición utilizando arena aglomerada con arcilla (o moldes de arena fabricados con otros materiales, como yeso y resina de silicona) como material de moldeo. El principio consiste en aprovechar la blandura y facilidad de moldeo del molde de arena, verter el metal fundido en el molde de arena y, cuando el metal se ha solidificado, romper el molde de arena para obtener la pieza moldeada deseada. Aplicada a una gran variedad de metales, la fundición en arena de aluminio común, la fundición en arena de hierro, la fundición en arena de cobre, dan paso ahora a la fundición en arena de China.aluminiofundiciónNingbo HexinSe explica detalladamente el proceso de fundición en arena.
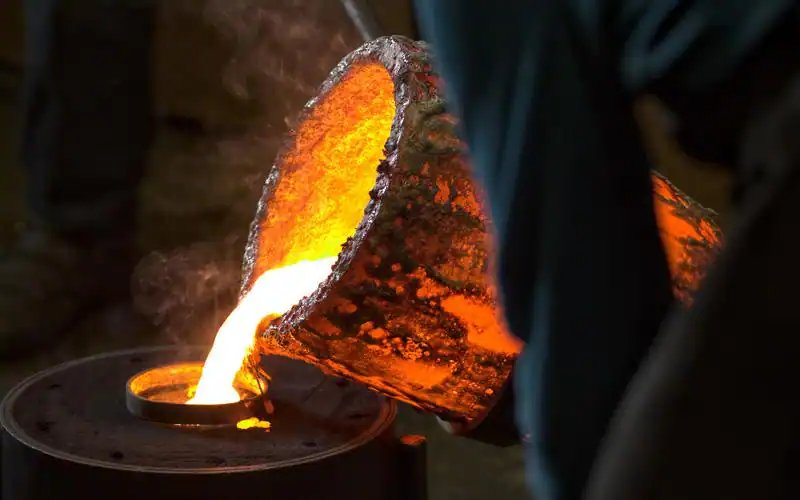
Flujo de proceso convencional para la producción de fundición en arena
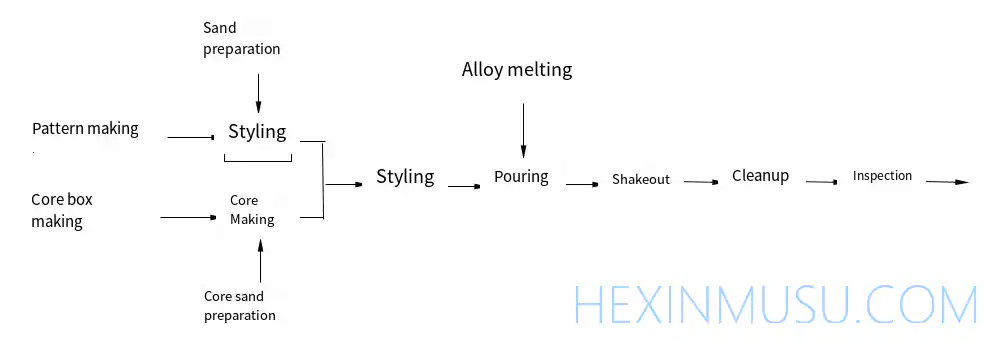
Proceso de fundición en arena
(1) Preparación de la arena de moldeo y la arena de machos
Los materiales de moldeo para la fundición en arena son principalmente la arena utilizada para fabricar el molde de arena y la arena de núcleo utilizada para fabricar el núcleo de arena. Por lo general, la arena se compone de arena bruta (arena de montaña o de río), arcilla y agua mezcladas en una determinada proporción, de la cual alrededor del 9% de arcilla, alrededor del 6% de agua, el resto de arena bruta. A veces también se añade una pequeña cantidad de aditivos como polvo de carbón, aceite vegetal, virutas de madera, etc. para mejorar el rendimiento de la arena y la arena de núcleo. La estructura de la arena compactada se muestra en la figura.
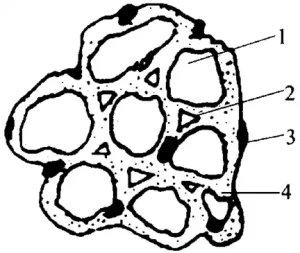
Diagrama esquemático de la estructura de la arena 1 - granos de arena 2 - huecos
3 - Fijación 4 - Membrana de arcilla
La arena para machos suele prepararse a mano debido a su escasa demanda.
El entorno en el que el núcleo es duro, por lo que los requisitos de rendimiento de arena de núcleo que la arena de alta, mientras que el aglutinante de arena de núcleo (arcilla, aceite, etc.) que la proporción del aglutinante en la arena es mayor que la de la arena, por lo que su permeabilidad no es tan buena como la arena, el núcleo debe hacerse para hacer un canal transpirable (agujeros); con el fin de mejorar el rendimiento del núcleo que se añade a añadir aditivos, tales como virutas de madera.
Algunas piezas de fundición pequeñas y exigentes se fabrican a menudo con machos de arena al aceite (aceite de tung + arena, cocidos hasta obtener un color marrón amarillento).
(2) Propiedades de la arena tipo
La calidad de la arena afecta directamente a la calidad de las piezas fundidas, la mala calidad de la arena hará que los productos de fundición de arena produzcan porosidad, tracoma, arena pegajosa, arena y otros defectos. Una buena arena debe tener las siguientes propiedades:
- ① Permeabilidad al gas El rendimiento de la arena del molde para dejar pasar el gas se llama permeabilidad al gas. Metal de alta temperatura de vertido en la fundición, el tipo se llena con un gran número de gases, estos gases deben ser echados de la fundición de la descarga suave, de lo contrario la fundición producirá porosidad, underpouring y otros defectos. Permeabilidad al aire fundido por el tamaño de partícula de arena, contenido de arcilla, contenido de humedad y compacidad de la arena y otros factores. Cuanto más fina sea la granulometría de la arena, cuanto mayor sea el contenido de arcilla y humedad, cuanto mayor sea la compacidad de la arena, peor será la permeabilidad al aire.
- ② Resistencia La capacidad de la arena para resistir daños externos se denomina resistencia. La arena debe tener una resistencia suficientemente alta para no provocar colapsos en el proceso de moldeo, manipulación y cierre de la caja, y para no dañar la superficie de la pieza fundida al verterla. La resistencia de la arena no debe ser demasiado alta, de lo contrario la colada será defectuosa debido a la disminución de la permeabilidad al aire y las concesiones.
- La refractariedad se refiere a la capacidad de la arena para resistir altas temperaturas y calor. Si la refractariedad es baja, es fácil que la fundición produzca arena pegajosa. Cuanto mayor sea el contenido de SiO2 en la arena, cuanto más grandes sean las partículas de arena, mejor será la refractariedad.
- Se refiere a la capacidad de la arena de deformarse bajo la acción de una fuerza externa y de mantener la forma existente después de retirar la fuerza externa. Buena plasticidad, fácil operación de moldeo, forma precisa y contorno claro del molde de arena.
- ⑤ Concesividad Capacidad de la arena del molde para comprimirse cuando se condensa la colada. Si la concesividad no es buena, la pieza fundida es propensa a sufrir tensiones internas o grietas. Cuanto más apretada esté la arena, peor será la concesividad. Añadir virutas de madera a la arena de moldeo puede mejorar la concesionalidad.
En una sola pieza de la producción de pequeños lotes de proveedores de productos de fundición de arena en el taller, de uso común método de pellizco de la mano para juzgar aproximadamente algunas de las propiedades de la arena, como agarrar un puñado de arena, pellizco sentir suave y fácil de deformar; dejar ir de la arena después de que la masa no está suelto, no se adhieren a la mano, y las huellas de las manos claras; romperlo, la sección de la plana y uniforme y sin fenómeno de agrietamiento, y al mismo tiempo sentir un cierto grado de fuerza, se cree que la arena tiene los requisitos de rendimiento adecuados, la arena. Como se muestra en la figura.
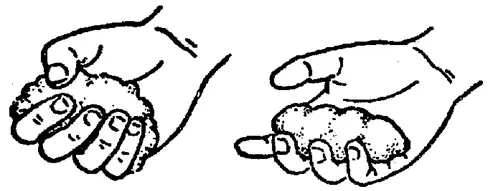
Cuando la humedad de la arena es la adecuada, puede verse cuando se suelta la mano.
Se puede amasar con la mano hasta formar una bola de arena Líneas manuales claras
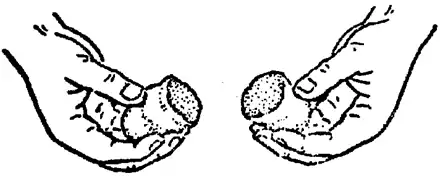
Fractura con un hueco roto con forma fragmentada
Al mismo tiempo hay suficiente fuerza
(3) Composición de los moldes
Los moldes para productos de fundición en arena se fabrican con material de moldeo según la forma de la pieza, y los moldes pueden ser de arena o metálicos. Un molde de arena se fabrica con material de moldeo hecho de arena (arena de núcleo). Se utiliza para verter líquido metálico y obtener piezas fundidas con la forma, el tamaño y la calidad requeridos.
Un molde consta generalmente de un molde superior, un molde inferior, un núcleo, una cavidad y un sistema de vertido, como se muestra en la figura de la derecha.
Las superficies de unión entre los componentes del molde se denominan superficies de separación. La parte de la cavidad rodeada por el material de moldeo del molde, es decir, la cavidad que forma el cuerpo de la pieza fundida, se denomina cavidad. El metal líquido fluye hacia la cavidad y la llena a través del sistema de vertido, y el gas producido se expulsa del molde de arena a través de la salida de aire, etc.
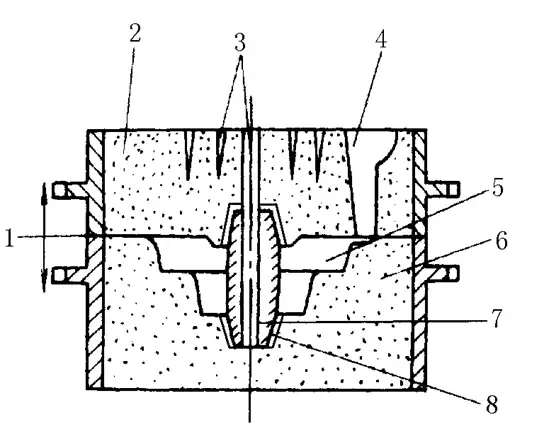
1-Superficie divisoria 2-Molde superior 3-Salida de aire 4-Sistema de vertido 5-Cavidad 6-Molde inferior
Porta-cabezas 7-Core 8-Core
(4)Sistemas de compuerta
- Sistema de vertido El sistema de vertido es una serie de canales en el molde para que el metal líquido fluya hacia la cavidad. Su función es:
① Inyecte el fluido metálico suave y rápidamente;
②Impedir la entrada de escoria, arena, etc. en la cavidad;
(iii) Regular la temperatura de cada parte de la colada para complementar la contracción del volumen del metal líquido durante el enfriamiento y la solidificación.
Ajustar correctamente el sistema de colada es de gran importancia para garantizar la calidad de las piezas fundidas y reducir el consumo de metal. Si el sistema de colada no es razonable, las piezas fundidas son propensas a defectos tales como soplado de arena, agujeros de arena, agujeros de escoria, bajo vertido, porosidad y agujeros de contracción. El sistema de colada típico consta de cuatro partes: compuerta exterior, bebedero recto, bebedero transversal y bebedero interior, como se muestra en la figura siguiente.
En el caso de piezas pequeñas con formas sencillas, puede prescindirse del bebedero transversal.
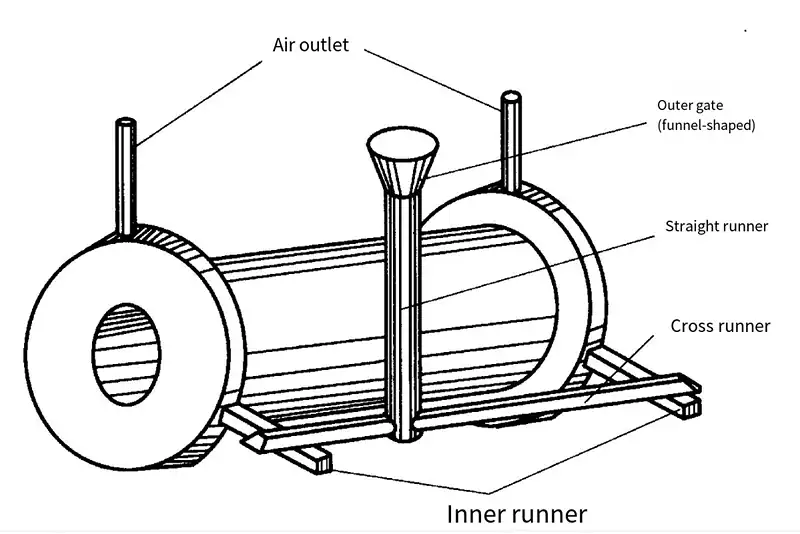
Sistemas de fundición típicos
- ① Compuerta exterior Su función es contener el metal líquido inyectado y facilitar el impacto del metal líquido en el molde de arena. Las piezas de fundición pequeñas suelen tener forma de embudo (llamada taza del bebedero), mientras que las piezas de fundición más grandes tienen forma de cubeta (llamada olla del bebedero).
- ② Canal recto Es el canal vertical que conecta la compuerta exterior con el canal horizontal. Cambiando la altura del canal recto puede cambiar la presión estática del metal líquido y cambiar la velocidad de flujo del metal líquido, cambiando así la capacidad de llenado del metal líquido. Si la altura o el diámetro del canal recto es demasiado grande, la pieza fundida se vaciará por debajo de su capacidad. Para facilitar la extracción de la varilla, el canal recto suele tener forma cónica con una parte superior grande y una inferior pequeña.
- ③ Canal transversal Es un canal horizontal para introducir el metal líquido desde el canal recto al canal interior, generalmente se abre en la superficie de separación del molde de arena, y su forma de sección transversal es generalmente trapezoidal alta y se sitúa en la parte superior del canal interior. La función principal del canal transversal es distribuir el metal líquido en el canal interior y bloquear la escoria.
- Está directamente conectado a la cavidad y puede regular la dirección y la velocidad del flujo de metal líquido en la cavidad y la velocidad de enfriamiento de cada parte de la pieza fundida. La forma de la sección transversal del bebedero interior es generalmente trapezoidal plana y en forma de media luna, y también puede ser triangular.
- Contrahuellas Los defectos comunes, como los agujeros de contracción y el aflojamiento por contracción, se deben a la contracción del volumen de la pieza fundida cuando se enfría y solidifica. Para evitar la contracción y el aflojamiento, se suele colar la parte superior o gruesa de la contrahuella. Las bandas son las cavidades y el metal inyectado en las cavidades de la pieza fundida. El metal líquido en la contrahuella puede reponer constantemente la contracción de la pieza fundida, de modo que la pieza fundida puede evitar los agujeros de contracción y el aflojamiento por contracción. Las bandas son redundantes y deben retirarse durante la limpieza. Las bandas, además de complementar la función de contracción, también desempeñan la función de escape y recogida de escoria.
(5) Fabricación de moldes y cajas de machos
El molde es el equipo de proceso necesario en la producción de piezas de fundición. Para piezas de fundición con una cavidad interna, la fundición de la cavidad interna formada por el núcleo de arena, y por lo tanto también para preparar la caja de núcleo para el núcleo de arena. Los materiales más utilizados para la fabricación del molde y la caja de machos son la madera, el metal y el plástico. En una sola pieza, la producción de lotes pequeños es ampliamente utilizado en el molde de madera y caja de núcleo, en la producción en masa de metal o plástico molde, caja de núcleo. La vida útil de los moldes y cajas de machos de metal es de 100.000 a 300.000 veces, la de los de plástico es de varias decenas de miles de veces, mientras que la de los de madera es sólo de unas 1.000 veces. Con el fin de garantizar la calidad de las piezas fundidas, en el diseño y la fabricación de moldes y cajas de machos, es necesario diseñar un mapa de proceso de fundición y, a continuación, de acuerdo con la forma y el tamaño del mapa de proceso, fabricar moldes y cajas de machos. Véase el diagrama siguiente.
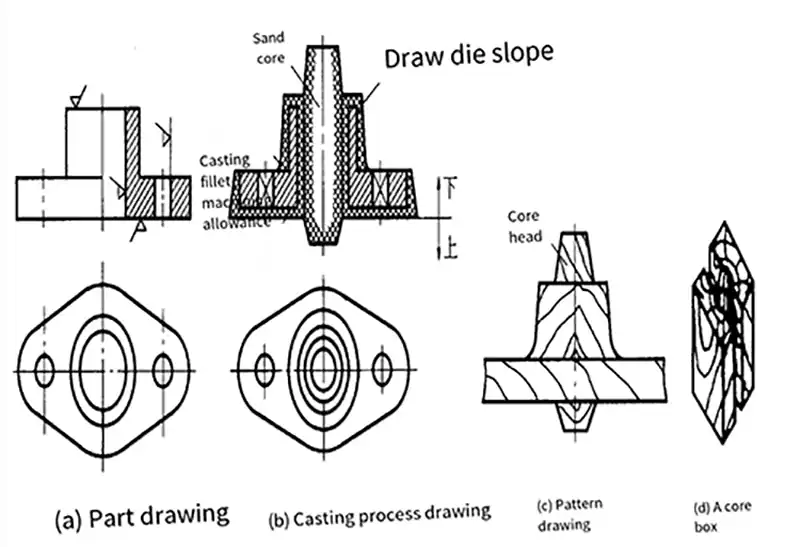
Al diseñar un mapa de procesos, tenga en cuenta algunos de los siguientes aspectos:
- ① Selección de la superficie de separación La superficie de separación es la interfaz entre la arena superior e inferior, y la selección de la superficie de separación debe permitir sacar el molde de la arena, y hacer que el modelado sea conveniente y propicio para garantizar la calidad de las piezas fundidas.
- Para sacar fácilmente el molde del molde de arena, todas las superficies perpendiculares a la superficie de separación se hacen con 0,5º~4º de inclinación de tiro del molde.
- ③ Sobremedida de mecanizado La superficie de la pieza fundida a procesar debe dejarse con una sobremedida de mecanizado adecuada.
- ④ Contracción La pieza fundida debe contraerse al enfriarse, y el tamaño del molde debe tener en cuenta la influencia de la contracción de la fundición. Suele utilizarse para piezas de fundición para aumentar un 1%; piezas de fundición de acero para aumentar entre un 1,5% y un 2%; piezas de aleación de aluminio para aumentar entre un 1% y un 1,5%.
- ⑤ Esquinas redondeadas de la colada Todos los puntos de inflexión de cada superficie de la colada deben convertirse en esquinas redondeadas de transición para facilitar el modelado y garantizar la calidad de la colada.
- (6) Cabezal de machos Para los moldes de arena con machos, debe fabricarse el correspondiente cabezal de machos en el molde.
Métodos de modelización
La elección del método de moldeo no sólo debe ajustarse al tipo de producción, sino también a las condiciones de equipamiento de la fábrica, el tamaño y la complejidad de la colada y los requisitos de calidad, para su seguimiento y consideración. Los métodos de moldeo pueden dividirse en dos categorías: moldeo manual y moldeo a máquina.
El moldeado a mano se utiliza principalmente para la producción de pequeños lotes de piezas únicas, mientras que el moldeado a máquina se utiliza principalmente para la producción de grandes lotes.
(1). Modelado manual
- (A) Las características del moldeo integral son: el molde es una estructura integral, la mayor sección transversal es plana en un extremo del molde; las superficies de separación son planas en su mayoría; y el funcionamiento es sencillo. El molde integral es adecuado para piezas de fundición con formas sencillas, como discos y tapas.
- (B) Las características del moldeo en molde partido son: los moldes están separados, y la superficie separada de los moldes (conocida como superficie de separación) debe ser la mayor sección transversal de los moldes, para facilitar el levantamiento del molde. El proceso de moldeo en molde partido es básicamente similar al de moldeo en molde entero, con la diferencia de que se añaden dos operaciones al hacer el molde superior, a saber, poner el molde superior y tomar el medio molde superior. El moldeo partido es adecuado para piezas de fundición con formas complejas, como manguitos, tubos y cuerpos de válvulas.
- (C) moldeado de bloque vivo en la parte extraíble o móvil se llama bloque vivo. Cuando hay un obstáculo en el molde en el lado del molde para extender la pieza (como una pequeña pestaña), la pieza se hace a menudo en un bloque vivo. Cuando se saca el molde, primero se saca el cuerpo principal del molde, y luego se saca por separado el bloque vivo que queda en la fundición, este método se llama moldeo de bloque vivo. Al moldear el bloque vivo unido con clavos, hay que tener en cuenta que primero hay que rellenar bien la arena alrededor del bloque vivo, y luego sacar los clavos.
- (D) moldeo en arena cuando la fundición de acuerdo con las características estructurales de la necesidad de moldeo, pero debido a las condiciones (como el molde es demasiado delgada, las dificultades de fabricación de moldes) todavía se hace en un molde entero, con el fin de facilitar el molde, la superficie de separación inferior debe ser excavado en una superficie curva o tener un alto y bajo cambios en la forma de la escalera (llamada superficie de separación desigual), este método se llama moldeo en arena.
- (F) Moldeo en tres cajas El proceso de utilizar tres cajas de arena para fabricar la pieza moldeada se denomina moldeo en tres cajas. Todos los métodos de moldeo mencionados anteriormente utilizan dos cajas de arena, que son fáciles de manejar y muy utilizadas. Sin embargo, algunas piezas de fundición, tales como los dos extremos del tamaño de la sección transversal es mayor que la sección transversal media, la necesidad de utilizar tres cajas de arena, a partir de dos direcciones, respectivamente, del molde.
- (G) rascador de moldeo de tamaño superior a 500 mm piezas de fundición de cuerpo giratorio, tales como poleas, volantes, engranajes grandes y otra producción única, con el fin de ahorrar madera, moldear el tiempo de procesamiento y el costo, se puede utilizar el moldeo rascador. Rascador es un pedazo de tabla de madera y la forma de la sección transversal de fundición. Al moldear, el rascador gira alrededor de un eje central fijo y raspa la cavidad requerida en el molde de arena.
- (H) El moldeado de caja ficticia es el uso de una placa base prefabricada con forma o caja ficticia para sustituir la arena excavada en el moldeado de excavación de arena.
- (I) Moldeo en foso El método de moldeo directamente en el fondo de arena o en el foso de arena de la fundición se denomina moldeo en foso. Cuando se fabrican grandes piezas de fundición en una sola pieza, el moldeo en foso se utiliza a menudo para ahorrar el cajón de arena, reducir la altura de colada y facilitar las operaciones de vertido. La estructura del moldeado en foso debe tenerse en cuenta a la hora de verter, ya que el gas del foso puede salir suavemente del suelo, a menudo del fondo de coque, escoria y otros materiales transpirables, y sacar el gas de la tubería de hierro.
(2). Modelización de máquinas
La productividad del moldeo manual es baja, la calidad de la superficie de las piezas fundidas es pobre, el requisito de trabajadores con alto nivel técnico, la intensidad de mano de obra, por lo que en la producción en masa, se utilizan generalmente en el moldeo a máquina. El moldeo a máquina es la operación principal del proceso de moldeo ---- apriete de arena y moldeo para lograr la mecanización. Según las diferentes formas de apretar la arena y empezar a moldear, hay moldeo neumático de compactación por micro vibración, moldeo por presión de disparo, moldeo por alta presión y moldeo por lanzamiento de arena.
- (A) neumática micro-vibración de compactación de moldeo se utiliza la vibración (frecuencia 150 ~ 500 veces / min, amplitud 25-80mm) - compactación - micro-vibración (frecuencia 700 ~ 1000 veces / min, amplitud 5 ~ l0mm) arena compactada. l0mm) para compactar la arena de moldeo. Este tipo de máquina de moldeo tiene menos ruido, compactación uniforme de la arena y alta productividad.
- (B) El moldeo por inyección se caracteriza por el uso de aire comprimido para disparar arena en la cavidad para la compactación inicial, y luego el pistón de compactación compactará la arena de nuevo, y después de lanzar la arena, la superficie de contacto entre los dos tipos de arena antes y después es la superficie de separación. El tamaño de fundición de moldeo por inyección es preciso, la rugosidad de la superficie es pequeña, y la productividad es alta. Puede producir 240-300 moldes por hora, y se utiliza comúnmente en la producción en masa de piezas de fundición de tamaño pequeño y mediano.
- (C) El moldeo por alta presión utiliza un sistema hidráulico que genera una presión muy alta para compactar el molde de arena. Se caracteriza por unas dimensiones de fundición precisas, una baja rugosidad superficial y una alta productividad. El moldeo por alta presión es adecuado para piezas de fundición pequeñas y medianas con formas más complejas, múltiples variedades y lotes medianos o más.
- (D) El moldeo por lanzamiento de arena consiste en utilizar la cuchilla giratoria de alta velocidad para lanzar hacia abajo la arena transportada por la cinta transportadora a gran velocidad para compactar el molde de arena. El moldeo por lanzamiento de arena tiene una gran capacidad de adaptación, no necesita caja de arena ni plantilla especiales, y es adecuado para la producción de piezas únicas y lotes pequeños de piezas de fundición de gran tamaño.
perforación
Con el fin de obtener la cavidad interior o la forma local de la colada, hecha de arena de núcleo u otros materiales, colocados en la cavidad dentro de los elementos de fundición llamados núcleo. La gran mayoría de los machos se fabrican con arena de machos. La calidad del machos depende principalmente de la preparación de arena de machos cualificada y del uso de un proceso de fabricación de machos correcto para garantizarla.
Al fundir el núcleo de arena por el impacto de metal líquido a alta temperatura y rodeado, por lo que además de los requisitos del núcleo de arena con la fundición de la forma correspondiente de la cavidad interior, también debe tener una mejor permeabilidad, refractariedad, concesiones, la fuerza y otras propiedades, por lo que la selección de arena de cuarzo con menos impurezas y aceite vegetal, vidrio de agua y otros aglutinantes para formular el núcleo de arena, y en el núcleo de la arena en el núcleo del hueso de metal y atar los orificios de ventilación con el fin de mejorar la resistencia y permeabilidad.
Los machos grandes y medianos con formas sencillas pueden fabricarse con arena de arcilla. Sin embargo, para machos con formas complejas y requisitos de alto rendimiento, deben utilizarse aglutinantes especiales para formularlos, como arena de aceite, arena de grasa y arena de resina.
Además, la arena para machos también debe tener algunas propiedades especiales, como baja higroscopicidad (para evitar que el macho vuelva a humedecerse después de cerrar la caja); menos gaseado (después de verter el metal, el material del macho debe producir el menor gas posible cuando se caliente); y buen lijado (para facilitar la extracción del macho durante la limpieza).
Los machos se fabrican generalmente a partir de cajas de machos, y su fabricación manual a partir de cajas de machos abiertas es un método muy utilizado para fabricar machos más complejos con secciones transversales redondas.
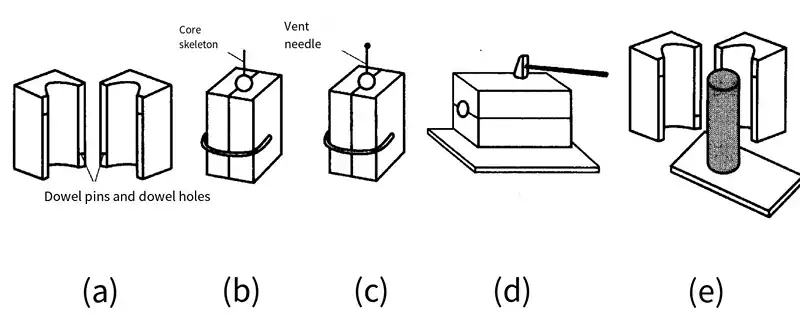
Folio core box fabricación de núcleos
(a) Preparar la caja de machos (b) Sujetar la caja de machos, añadir arena de machos, hueso de machos y machacar la arena por etapas (c) Raspar y atar los orificios de ventilación (d) Aflojar las abrazaderas y golpear la caja de machos (e) Abrir la caja de machos, sacar el macho de arena y aplicar el revestimiento
Operaciones básicas de modelización
Existen muchos métodos de moldeo, pero la mayoría de ellos incluyen el machacado con arena, el arranque del molde, la reparación del molde y el cierre de la caja.
(1) mira
La forma original de la pieza de fundición de madera, metal u otros materiales se denomina colectivamente molde, que se utiliza para formar la cavidad de la pieza de fundición. El molde de madera se conoce como molde de madera, el molde de metal o plástico se conoce como molde de metal o molde de plástico. En la actualidad, la mayoría de las fábricas utilizan moldes de madera. La forma del molde es similar a la forma de la fundición, la diferencia es que la fundición, tales como agujeros, en el molde no sólo es sólido sin agujeros, sino también en la posición correspondiente para hacer la cabeza del núcleo.
(2) Preparación antes del moldeo
- ① Prepare las herramientas de moldeo, elija una placa base plana y un cajón de arena del tamaño adecuado. Si la caja de arena es demasiado grande, no sólo consumirá demasiada arena, sino que también desperdiciará tiempo de machacado de arena. Si el cajón de arena es demasiado pequeño, la arena alrededor del molde de madera no se golpeará con fuerza y el metal líquido saldrá fácilmente de la superficie de separación, es decir, entre las interfaces, al verterlo. Por lo general, la distancia entre el molde de madera y la pared interior y la parte superior del cajón de arena debe ser de 30~100 mm, lo que se denomina cantidad de arena comestible. Esta distancia se denomina capacidad de alimentación de arena. El valor específico de la capacidad de alimentación de arena depende del tamaño del molde de madera.
- ② Limpie el molde de madera, para evitar que la arena de moldeo se pegue al molde de madera y se dañe la cavidad al levantar el molde.
- ③ Al colocar el molde de madera, preste atención a la dirección de la pendiente en el molde de madera y no lo coloque en el lugar equivocado..
(3)libra de arena
- ① Golpear la arena debe ser añadido a la arena en etapas. Para la pequeña caja de arena cada vez para añadir espesor de arena de unos 50 ~ 70 mm.Demasiado golpeteo de arena no es apretado, y demasiado poco de arena y el costo de horas-hombre. Al añadir arena por primera vez, la arena alrededor del molde de madera debe ser presionado firmemente con la mano para evitar que la posición del molde de madera en la caja de arena se mueva. A continuación, utilice el extremo puntiagudo del martillo de arena para golpear firmemente en etapas y, finalmente, utilice el extremo plano del martillo de arena para golpear firmemente la capa superior de arena.
- ② Golpear la arena debe llevarse a cabo en una ruta determinada. No este un poco, al oeste un poco caótica golpeando, a fin de evitar las diferentes partes de la opresión.
- ③ Golpear la arena debe ser apropiado. Demasiada fuerza, la arena es demasiado apretado, verter la cavidad del gas no puede salir. Demasiado poca fuerza, la arena es demasiado flojo y fácil de colapsar la caja. La estanqueidad de cada parte de la misma arena es diferente, cerca de la pared interior de la caja de arena debe ser golpeado con fuerza para evitar el colapso de la caja. Cerca de la parte de la cavidad, la arena debe ser ligeramente más apretado para soportar la presión del metal líquido. Lejos de la cavidad de la capa de arena debe ser adecuadamente suelto, con el fin de facilitar la permeabilidad al aire.
- ④ Al golpear la arena se debe evitar que el martillo golpee el molde de madera. Por lo general, la distancia entre el martillo y el molde de madera es de 20-40 mm, de lo contrario es fácil dañar el molde de madera.
(4) espolvorear arena
Antes de construir el modelo de arena, se debe esparcir una capa de arena seca de grano fino y no arcillosa (es decir, arena) sobre la superficie de separación para evitar que los areneros superior e inferior se peguen entre sí y no se pueda abrir la caja. Al esparcir la arena, la mano debe estar ligeramente más alta del cajón de arena, mientras se gira, mientras se balancea, de modo que la arena a través de las grietas de los dedos se esparza lenta y uniformemente hacia abajo, cubriendo finamente la superficie de separación. Por último, el molde de madera debe ser soplado fuera de la arena de separación, a fin de no hacer en el modelo de arena, la arena de separación se adhieren a la superficie del modelo de arena, y en el vertido del metal líquido se lava hacia abajo en la fundición, por lo que produce defectos.
(5)hacer un agujero
Además de asegurarse de que la arena tiene una buena permeabilidad al aire, también en la arena ha sido golpeado y raspado plana, con una aguja de ventilación para atar los orificios de ventilación, de modo que el gas es fácil escapar cuando se vierte. Los orificios de ventilación deben ser verticales y estar distribuidos uniformemente.
(6)Sprue abierto
La compuerta exterior debe excavarse en un cono de 60°, con un diámetro de 60-80 mm en el extremo grande, y la superficie de la compuerta debe pulirse, y la conexión con el bebedero recto debe hacerse en una transición redondeada, para guiar el metal líquido para que fluya suavemente en el molde de arena. Si la compuerta exterior se excava demasiado poco y adquiere forma de disco, el metal líquido salpicará y dañará a las personas al verterlo.
(7)Hacer la recta final
Si los areneros superior e inferior no tienen clavijas de localización, se debe trazar una línea de cierre en la pared del arenero antes de abrirlos. La forma más sencilla es aplicar polvo de tiza en la pared del arenero y, a continuación, utilizar una aguja para trazar una línea fina. Necesidad de entrar en el horno para cocer la caja de arena, la arcilla de arena se utiliza para pegar en la pared de la caja de arena, con un cuchillo de yesero calcetín plana, y luego tallar la línea, conocida como jugando número de barro. La línea debe situarse en el punto más alejado de los dos bordes en ángulo recto de la pared del arenero para garantizar que se puedan colocar las direcciones x e y y limitar la rotación del patrón de arena. El número de líneas en dos lugares no debe ser igual, para no cometer un error al cerrar la caja. Do línea terminada, puede abrir la caja para iniciar el molde.
(8)tomar un molde
- ① Antes de coger el molde, moje el cepillo de agua en un poco de agua y cepille la arena alrededor del molde de madera para evitar que la cavidad de arena se dañe al coger el molde. Cepillo de agua debe ser un cepillo, no hacer que el cepillo de agua para permanecer en un lugar determinado, a fin de evitar el exceso de agua local y producir una gran cantidad de vapor de agua durante el vertido, por lo que la fundición produce defectos de porosidad.
- ② La posición del perno de arranque del molde debe coincidir con el centro de gravedad del molde de madera en la medida de lo posible. Antes de poner en marcha el molde, golpee suavemente con un pequeño martillo la parte inferior de la espiga de inicio del molde para aflojar el molde de madera y facilitar la puesta en marcha del molde.
- ③ Cuando levante el molde, levante lentamente el molde de madera verticalmente, cuando el molde de madera esté a punto de ser levantado completamente, entonces sáquelo rápidamente. Tenga cuidado de no desviarse ni balancearse al levantar el molde.
(9) manicura
Después de sacar el molde, si la cavidad está dañada, hay que utilizar correctamente todo tipo de herramientas de reparación según la forma de la cavidad y el grado de daño. Si el daño de la cavidad es grande, se puede volver a introducir el molde de madera en la cavidad para repararlo y, a continuación, volver a sacarlo.
(10)cerrar un caso
El cierre de la caja es el último proceso del moldeo, que desempeña un papel importante en la calidad del molde de arena. Antes de cerrar la caja, hay que comprobar cuidadosamente si el molde de arena está dañado, si hay arena suelta y si el bebedero está recortado. Si desea colocar el núcleo, debe comprobar si está seco, si presenta daños y si los orificios de ventilación están obstruidos. La posición del núcleo en el molde de arena debe ser precisa y estable, para no afectar a la precisión de la colada y evitar que el metal líquido lo arrastre al verterlo. Al cerrar la caja, se debe prestar atención a la caja de arena superior para mantener el nivel bajo, y se debe alinear con la línea de cierre para evitar la caja equivocada. Después de cerrar la caja, es mejor cubrir el bebedero con papel o un trozo de madera para evitar que caiga arena o residuos en el bebedero.
Selección de la posición de colada y de la superficie de separación
piezas de fundiciónLa posición de vertido de la pieza es la posición de la pieza en el molde durante el vertido.
La superficie de separación es la superficie en la que las dos mitades de la pieza fundida entran en contacto.
Su principio de selección es principalmente garantizar la calidad de las piezas fundidas y simplificar el proceso de moldeo. En términos generales, la posición de fundición debe seleccionarse en primer lugar después de decidir la superficie de separación, pero en la producción, debido a que la selección de la posición de fundición y la determinación de la superficie de separación a veces se contradicen, es necesario analizar exhaustivamente las ventajas y desventajas de las distintas opciones y elegir la mejor opción.
(1) .Principio de selección de la posición de colada
- (A) la superficie de procesamiento importante de la fundición debe estar mirando hacia abajo los agujeros de aire, agujeros de arena, escoria, agujeros de contracción es probable que aparezcan en la superficie superior, mientras que la parte inferior del líquido de metal es relativamente puro, la organización de metal es relativamente denso. A veces, cuando la superficie de mecanizado importante está mirando hacia abajo por algunas razones, se debe hacer en la posición de la superficie de ejemplo en la medida de lo posible.
- (B) El plano grande de la colada debe estar orientado hacia abajo Debido al efecto de radiación de calor durante el vertido, la arena de la superficie superior de la cavidad de la colada es propensa a arquearse y agrietarse, dando lugar a defectos de arena e inclusión en la superficie superior de la colada, por lo que el plano grande debe estar orientado hacia abajo.
- (C) la pieza de pared delgada de fundición debe colocarse en la parte inferior de la pieza de pared delgada es fácil producir vertido insuficiente y segregación en frío, por lo que en la parte inferior de la puede aumentar la presión de llenado, mejorar la capacidad de llenado de metal.
- (D) debe asegurarse de que la fundición para lograr la solidificación direccional Para la contracción de la aleación, el espesor de pared de la fundición no es uniforme, el espesor de la mayor parte de la fundición debe ser colocado en la fundición de la parte superior o cerca de la superficie de separación, con el fin de facilitar la colocación de bandas, para lograr la solidificación direccional
- (F) Debe ser fácil para la fijación del núcleo, la instalación y la ventilación, y fácil de cerrar el molde.
(2).Principio de selección de las superficies de separación
- (A) La superficie de separación debe seleccionarse en la sección transversal más grande del molde para facilitar la recogida del molde, prestando especial atención al moldeo en arena de excavación.
- (B) Debe reducirse al mínimo el número de superficies de separación y evitarse el modelado en tres cajas para la producción en serie.
- (C) Todas o la mayoría de las piezas fundidas se fabricarán en el mismo molde de arena para reducir los errores de encajado, los bordes volantes y las rebabas, y para mejorar la precisión de las piezas fundidas.
- (D) El número de machos y bloques vivos debe reducirse al máximo para simplificar el proceso de moldeo y fabricación de machos y mejorar la productividad.
Selección de los parámetros del proceso
(1) Indemnización por mecanizado
Las piezas de fundición necesitan ser cortadas en la superficie, por lo que se debe reservar de antemano una cierta cantidad de tolerancia de mecanizado, cuyo tamaño depende del tipo de aleación de fundición, métodos de modelado, tamaño de la pieza de fundición y superficie de procesamiento en la fundición de la ubicación de muchos factores. Rugosidad de la superficie de acero fundido, la deformación, la asignación de procesamiento; superficie de aleación no ferrosa es más pulido, la asignación de procesamiento es pequeño; modelado de la máquina de alta precisión, la asignación de procesamiento se puede seleccionar más pequeño; una sola pieza de la producción de lotes pequeños más factores que afectan a la asignación de procesamiento para ser aumentado; fundición de la más grande, más complejo, mayor es la asignación de procesamiento; fundición de la superficie superior de la parte inferior y el lado de la asignación de mecanizado es grande.
Una sola pieza de la producción de lotes pequeños de piezas pequeñas de hierro fundido de mecanizado subsidio de 4,5 ~ 5,5 mm; pequeñas piezas de fundición de metales no ferrosos de mecanizado subsidio de 3 mm; piezas de fundición gris de mecanizado valor subsidio puede referirse a JB2854-80.
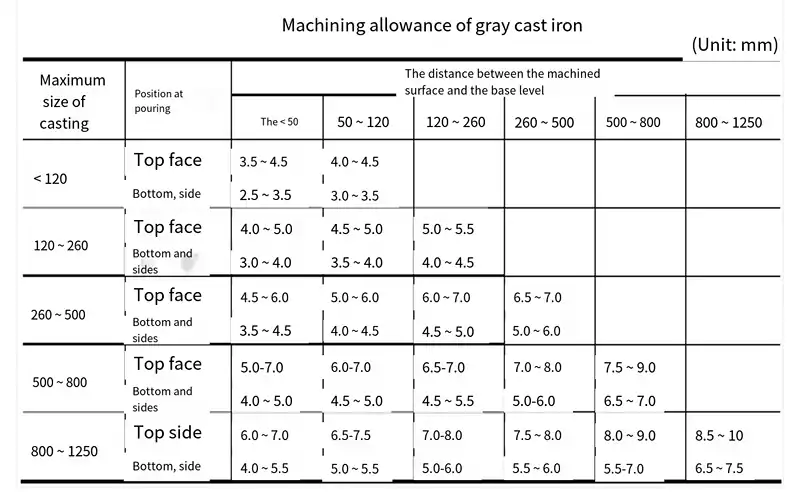
Además, las piezas de acero fundido con un diámetro inferior a ф35mm y piezas de hierro fundido con un diámetro inferior a ф25mm agujeros generalmente no se funden, dejando el mecanizado más económico y conveniente. Para el modelado a máquina de piezas pequeñas, no fundido el agujero puede ser más pequeño. Para formas especiales que no requieren procesamiento, dificultades de mecanizado en el agujero, ranura, debe ser fundido.
(2) Inclinación del moldeado
Para que la prueba sea fácil de sacar de la fundición, la pendiente añadida a la pared vertical perpendicular a la superficie de separación es la pendiente inicial del molde. Cuanto más alto es el molde, menor es el valor de la pendiente, y la pendiente de la pared interior es mayor que la de la pared exterior. La pendiente de la pared interior es mayor que la de la pared exterior. La pendiente del moldeo a mano es mayor que la del moldeo a máquina. Cuando el molde es corto (≤100mm), es de aproximadamente 3º, y cuando el molde es alto (101~160mm), es de 0.5°~1°.
(3) Fundición de esquinas redondeadas
Para evitar que la pieza de fundición sufra tensiones y grietas en las uniones de las paredes y las esquinas, y para evitar daños en las esquinas afiladas de la pieza de fundición y la producción de agujeros de arena, las uniones de las paredes de la pieza de fundición y las piezas de las esquinas deben diseñarse en cuatro esquinas al diseñar la pieza de fundición.
(4) Jefes de núcleo
Para garantizar la colocación, fijación y ventilación del núcleo en el molde de fundición, tanto el molde como el núcleo están diseñados con una cabeza de núcleo.
La cabeza del núcleo es la parte extendida del núcleo, que cae en el asiento del núcleo del modelo de fundición y sirve para ubicar y sostener el núcleo.
La forma de la cabeza del noyo depende del tipo de noyo, la cabeza del noyo debe tener suficiente altura (h) o longitud (l) e inclinación adecuada, para que el noyo sea cómodo, preciso y se fije firmemente en el molde de colada, a fin de evitar que el noyo flote, se desvíe y se mueva durante el vertido.
(5) Reducción por contracción
Como la fundición después de verter la contracción de enfriamiento, la producción de moldes debe añadirse a esta parte del tamaño de la contracción. General de hierro fundido gris contracción asignación de 0,8 por ciento - 1,0 por ciento, fundición de acero para l,8 por ciento - 2,2 por ciento, fundición de aleación de aluminio para el 1,0 por ciento - 1,5 por ciento. El tamaño de la tolerancia de contracción, además del tipo de aleación, sino también con el proceso de fundición, piezas de fundición en la contracción de la situación de bloqueo y así sucesivamente.
Tipo de aleación | Contracción por colada | ||
contracción libre | contracción | ||
gris metales fundidos o encontrados hierro (metal) | Piezas moldeadas pequeñas y medianas | 1.0 | 0.9 |
Coladas medianas y grandes | 0.9 | 0.8 | |
Coladas extragrandes | 0.8 | 0.7 | |
hierro dúctil | 1.0 | 0.8 | |
Acero al carbono y de baja aleación | 1.6~2.0 | 1.3~1.7 | |
estaño bronce | 1.4 | 1.2 | |
Wuxi Bronce | 2.0~2.2 | 1.6~1.8 | |
latón siliconado | 1.7~1.8 | 1.6~1.7 | |
Aleaciones de aluminio-silicio | 1.0~1.2 | 0.8~1.0 |
Ventajas e inconvenientes de la fundición en arena
Ventajas de la fundición en arena
- Bajos costes de fabricaciónLa fundición en arena utiliza materias primas (por ejemplo, arena, arcilla, etc.) de bajo coste, y el proceso de fabricación es relativamente sencillo, por lo que los costes de fabricación son relativamente bajos.
- Gran flexibilidad de fabricaciónLa fundición en arena permite producir piezas fundidas de formas y tamaños muy diversos, desde unos pocos gramos hasta varias toneladas de piezas con facilidad y gran aplicabilidad.
- Ciclo de fabricación cortoEl proceso de fundición en arena es relativamente sencillo y requiere menos tiempo de secado y endurecimiento, lo que se traduce en un ciclo de fabricación relativamente corto.
- Amplia gama de fuentes de materias primasFundición en arena : La fundición en arena tiene una amplia gama de fuentes de materia prima, arena, arcilla, etc se puede utilizar como material de moldeo, y barato.
Desventajas de la fundición en arena
- Calidad superficial media de las piezas fundidasLa calidad superficial de las piezas fundidas en arena puede presentar algunos defectos, como agujeros de arena, agujeros de arena, arena pegajosa, etc.
- El núcleo de arena es propenso al colapsoEn la fundición en arena, los machos de arena pueden ser necesarios para fabricar piezas con formas complejas. Los machos de arena son propensos a deformarse y colapsarse, lo que provoca un alto índice de rechazos.
- Menor productividadLa productividad de la fundición en arena es relativamente baja, ya que cada molde de arena debe fabricarse a mano y los moldes sólo pueden utilizarse una vez.
- Alto consumo de energía y elevadas emisiones contaminantesLa fundición de arena consume mucha energía durante el proceso de producción y puede producir ciertas emisiones contaminantes, como polvo y gases de escape. Esto puede tener cierto impacto sobre el medio ambiente y la salud de los trabajadores.