Moldes de fundición a baja presión
Fecha:2025-02-25 Categorías:Blog Vistas:1104
fundición a baja presión Es un método de fundición en el que el metal fundido se inyecta en la cavidad del molde mediante presión de gas. En comparación con la fundición a alta presión, la fundición a baja presión puede mejorar la calidad de la superficie de las piezas fundidas, reducir la porosidad y es adecuada para fundir formas más complejas. En el proceso de fundición a baja presión, la composición y el diseño del molde son cruciales, lo que afecta directamente a la calidad de la pieza fundida, la eficiencia de la producción y la vida útil del molde. En este artículo se analiza Molde de fundición de baja presión Los principales componentes de la fundición y su influencia en la calidad de la misma.
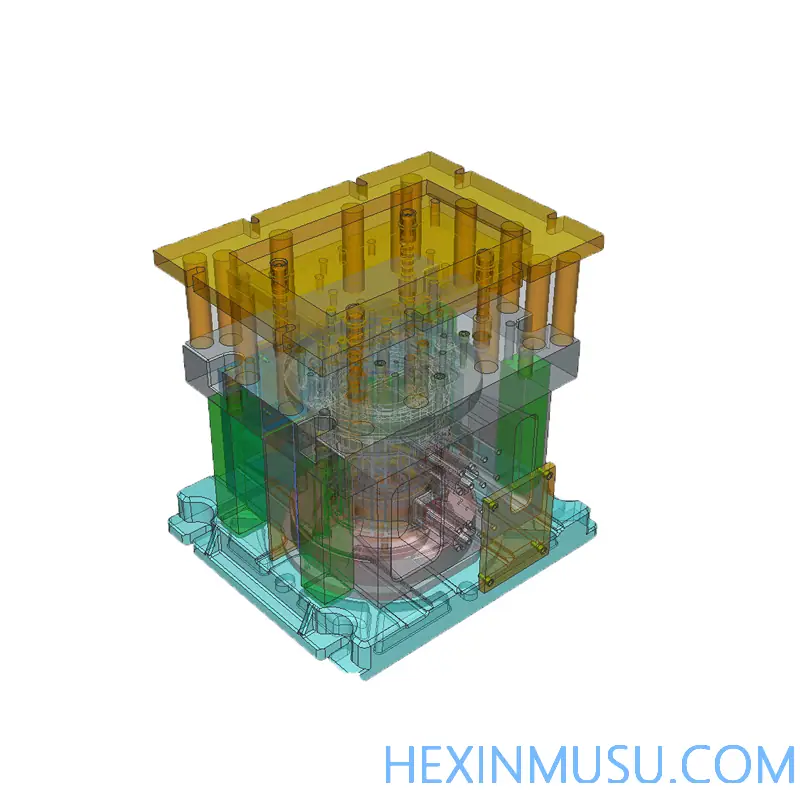
Los principales componentes de un molde de fundición a baja presión
Moldes de fundición de baja presión por los seis componentes principales de la sinergia: cavidad del molde como el núcleo de la formación, utilizando H13 de trabajo en caliente de mecanizado de precisión de acero del molde, para garantizar ± 0,15 mm de tolerancia dimensional y Ra ≤ 0,8μm acabado de la superficie; puerto de inyección a través del diseño de 60 ° tangente cónica para lograr el llenado de flujo laminar, la velocidad de flujo se controla en el 0,8-1,2m / s para evitar que el volumen de gas; integración del sistema de escape de la superficie de separación de la micro-gap ( 0,05-0,08mm), ranura de vacío y tapones de cerámica porosa para reducir la tasa de defectos de porosidad de más de 80%; sistema de refrigeración incorporado perfilado con la forma de la vía de agua, 8-12mm de la disposición de la superficie, combinado con la válvula de control de flujo para hacer que el gradiente de temperatura del molde <15 ℃; el marco del molde adopta la estructura de caja de hierro dúctil QT600, la elasticidad de la deformación de <0,02mm/1000kN; el sistema de sellado es a través de un anillo de caucho fluorado de alta temperatura y sello duro de metal. El sistema de sellado se combina con un anillo de caucho fluorado de alta temperatura y un sello duro de metal, la tasa de fuga es <0,5Pa-m³/s, lo que garantiza el funcionamiento estable de 150.000 moldes.
Consideraciones clave para el diseño de moldes de fundición a baja presión
El diseño de moldes requiere un equilibrio exhaustivo entre las propiedades de los materiales, la mecánica estructural y los costes de mantenimiento. Se da prioridad al acero H13 (dureza HRC48-52) o SKD61 (tratamiento superficial TD) para hacer frente al lavado del aluminio y al estrés térmico; se utiliza MAGMAsoft para llevar a cabo una simulación acoplada de campos múltiples de llenado-solidificación para garantizar que la diferencia de temperatura entre los frentes metálicos sea 1,5; se utiliza un diseño modular para lograr una rápida sustitución de los insertos, y se combina con las galgas extensométricas para controlar la expansión de las grietas de fatiga en los moldes en tiempo real. El trazado del circuito de agua de refrigeración debe optimizarse mediante termodinámica ANSYS, de modo que la diferencia de temperatura entre los puntos calientes locales pueda controlarse dentro de ±3℃; al mismo tiempo, el sistema de barra de elevación hidráulica preajustada (densidad de 1/100cm²) y la interfaz de posicionamiento cero pueden acortar el tiempo de inactividad por mantenimiento a 12 minutos.
Ventajas y aplicaciones de los moldes de fundición a baja presión
Moldes de fundición a baja presión en los sectores de automoción y aeroespacial para mostrar ventajas únicas: a través de la tecnología de conformado casi neto de 0,3 mm de margen de mecanizado, un nuevo brazo de control del vehículo de energía de ahorro 62%mecanizadoCostes; fundición asistida por vacío para que las piezas de pared fina de 1,2 mm califiquen a una tasa de 98%, en comparación con la reducción de peso del proceso tradicional de 35%; tecnología de control de gradiente de temperatura para mejorar laaluminioTamaño de grano a grado 7 (ASTM E112), la vida de fatiga de fundición de ruedas aumentó en 3 veces. En el campo de la aviación, los moldes de las bisagras de las escotillas de aleación de titanio Ti6Al4V alcanzan una resistencia a la tracción > 950 MPa, y los moldes de las palas de solidificación direccional tienen más de 80% de cristales columnares. En comparación con la fundición a alta presión, el coste del material de una sola pieza se reduce en 29% (85 $ frente a 120 $), y la vida útil del molde aumenta en 87,5% (150.000 veces frente a 80.000 veces).
Características principales de los moldes de fundición a baja presión
La tecnología combina rentabilidad y precisión en la fabricación: acorta el ciclo de desarrollo del molde en 40% (el gemelo digital solo necesita 2 pruebas), rugosidad superficial de hasta Ra0,8μm (mejor que la de la fundición a alta presión de 1,6μm); se adapta al rango de grosores de pared de 0,8-150mm, especialmente bueno en cavidades internas complejas, como bloques de motor; producción totalmente automatizada mediante integración PLC con un ritmo de producción de ≤90 segundos por pieza, ahorrando 45% en costes de mano de obra; utilización de material de hasta 95% (30% superior a la fundición en arena); reduce aún más la huella de carbono con aplicación de aluminio reciclado. Ahorro de 45%; tasa de utilización del material de hasta 95% (30% superior a la fundición en arena), con aplicación de aluminio reciclado para reducir aún más la huella de carbono.
Preguntas más frecuentes (FAQ)
¿Cómo elegir entre acero para moldes H13 y SKD61?
El acero H13 (dureza HRC48-52) es adecuado para condiciones de ciclos de alta temperatura (por ejemplo, moldes de bloques de motor), y su resistencia a la fatiga térmica es 30% superior a la del SKD61; mientras que el SKD61 con tratamiento de infiltración de vanadio por TD tiene una dureza superficial de HV1800, que es más adecuada para sistemas de pasadores eyectores con elevados requisitos de resistencia al desgaste, y puede ampliar la vida útil a más de 200.000 ciclos de molde.
2. ¿Cómo resolver el problema de la adherencia del aluminio al molde?
El uso de la tecnología de rebaba láser (rugosidad superficial Sa 2,5μm) combinada con un revestimiento de carbono amorfo (coeficiente de fricción 0,1), junto con la pulverización cuantitativa de agentes desmoldeantes (3-5g/m²), reduce la tasa de adherencia del aluminio a menos de 0,1%. Tras la aplicación de un molde de carcasa de caja de cambios, el tiempo de limpieza se redujo de 30 minutos/molde a 5 minutos.
3. ¿Cómo se puede optimizar el sistema de refrigeración del molde?
El uso de la impresión 3D con la forma del circuito de agua de refrigeración, la distancia desde la superficie del molde se acorta a 5 mm, con control de flujo dinámico (regulación del algoritmo PID), puede hacer que la diferencia de temperatura del molde local de ± 15 ℃ hasta ± 3 ℃, el tiempo de solidificación de la colada se reduce en 25%, el rendimiento se incrementa en 12%.
4. ¿Cuál es la diferencia de coste entre los moldes de fundición de baja presión y los de alta presión?
La inversión inicial en moldes de fundición a baja presión es inferior en 40% (unos 500.000 RMB frente a 850.000 RMB), pero el coste de material por pieza se ahorra en 29% (85 RMB frente a 120 RMB). Con una capacidad de producción anual de 100.000 piezas, el coste total del proceso de baja presión puede reducirse en 2,1 millones de yuanes.
5. ¿Cómo prolongar la vida útil de los moldes?
El tratamiento de nitruración (espesor de la capa blanca brillante 0,08-0,12 mm) combinado con el recocido bajo tensión (300 °C x 4 horas) cada 50.000 ciclos de moldeo puede aumentar la vida útil del molde de acero H13 de 100.000 a 180.000 ciclos de moldeo, con una reducción de los costes generales de mantenimiento de 35%.
6. ¿Cómo garantizar la calidad de las piezas moldeadas de paredes finas (<1,5 mm)?
Adoptando la tecnología asistida por vacío (vacío de cavidad ≤ 50mbar) superpuesta a la extrusión y la contracción (presión 80-100MPa), puede lograrse una producción estable de piezas de aleación de aluminio con un espesor de pared de 1,2mm, con un índice de porosidad de <0,5% y un aumento de resistencia de 20%.
7. ¿Cuáles son las futuras tendencias tecnológicas?
En 2026 se fabricarán en serie moldes inteligentes (dotados de sensores de fibra óptica para controlar la tensión en tiempo real) y revestimientos autorreparadores (microcápsulas que liberan agentes restauradores), que se espera reduzcan los costes de mantenimiento de los moldes en 40% más. La tecnología de fundición semisólida reducirá el límite de grosor de las paredes a 0,5 mm, lo que impulsará la reducción del peso de los vehículos de nueva energía en más de 15%.
llegar a un veredicto
La composición del molde de fundición a baja presión determina directamente la calidad y la productividad de las piezas fundidas. Mediante el diseño razonable de los diversos componentes del molde, incluida la cavidad del molde, el puerto de inyección, el sistema de escape, el sistema de refrigeración, etc., se puede mejorar significativamente la calidad de la superficie de la pieza fundida, reducir los defectos y prolongar la vida útil del molde. Con el desarrollo de la tecnología, el material y el diseño de los moldes de fundición a baja presión siguen innovando, y desempeñarán un papel importante en más campos en el futuro.