Cálculo del coste de la fundición a presión: cómo calcular el precio de la fundición a presión
Fecha:2025-02-03 Categorías:Blog Vistas:894
En la industria manufacturera, el proceso de fundición a presión se utiliza ampliamente en la producción de todo tipo de piezas y componentes por su gran precisión y alta eficiencia de producción. Sin embargo, el cálculo del coste de la fundición a presión es a menudo una parte importante de la empresa para la fijación de precios y control de costes. La correcta comprensión del coste de los componentes de fundición a presión, no sólo ayuda a fijar precios razonables, sino que también ayuda a las empresas a optimizar el proceso de producción, mejorar los beneficios. En este documento, analizaremos el coste de la fundición a presión, proporcionaremos un método de cálculo de costes detallado y discutiremos cómo optimizar el coste para reducir el coste total de la fundición a presión.
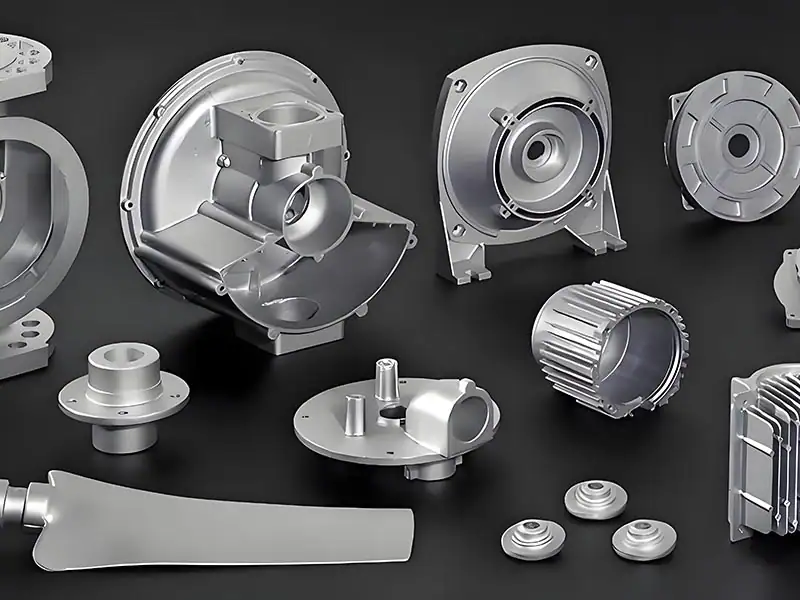
¿Es costosa la fundición a presión?
En efecto, el coste de la fundición a presión no es bajo, razón principal por la que muchas empresas dudan en elegir este proceso. Aunque la fundición a presión destaca en precisión, eficiencia y fabricación de piezas complejas, su elevado coste, especialmente en la producción de lotes pequeños, suele desanimar a las empresas. Por lo tanto, Ningbo Hexin sugiere que las empresas adopten el proceso de fundición a presión cuando lleven a cabo una producción en masa, con el fin de diluir el coste. Los siguientes son algunos factores clave que afectan al coste de la fundición a presión:
Modelización métrica tridimensional de los costes de fundición a presión (en ADC12)aluminio(conchas como ejemplo)
1. Control dinámico de los costes de material
- Fórmula de base: C_m=(W_p×ρ×P_m×(1+15% pérdida))/tasa de rendimiento
- Valores medidos de variables clave:
- Volatilidad de los materiales: diferencia entre los precios máximos y mínimos del aluminio ADC12 de 4.200 $/t en 2023 (véase el gráfico 1).
- Optimización de la pared delgada: el grosor de la pared de una tapa de extremo de motor eléctrico se redujo de 3,5 mm a 2,8 mm, y el coste de material de una sola pieza se redujo en 19%.
- Control del material de retorno: el material de retorno 30% se añade cuando las propiedades mecánicas del 12% disminuyen, para equilibrar la ventana de proceso.
2. Gestión del ciclo completo de los costes de los moldes
Tipo de molde | Coste inicial (millones de dólares) | Duración de la vida (módulos) | Evaluación individual ($) |
---|---|---|---|
Cavidad simple H13 | 48 | 80,000 | 0.60 |
SKD61 de cuatro cavidades | 126 | 150,000 | 0.21 |
Fuente de datos: Ningbo Hexin 2022 Mould Database |
3. Deconstrucción de los elementos del coste de fabricación
- Estructura de costes de una unidad de fundición a presión de 2800T:
- Amortización del equipo: 23 $/hora (amortización lineal en 5 años)
- Coste del consumo de energía: 18 kW-h/módulo x 1,2 $ = 21,6 $.
- Coste laboral: 0,38 personas/turno x 45 $/hora = 17,1 $.
- Consumo de materiales auxiliares: agente de pulverización 2,3 yuanes / veces molde
Seis vías tecnológicas de ingeniería para reducir costes
Trayectoria 1: Optimización de la ingeniería sincronizada con DFM
- Caso: carcasa del filtro de una estación base 5G
- Programa original: 8 grandes secciones gruesas (grosor máximo de pared 8 mm)
- Solución optimizada: optimización de la topología + canal seguidor, reducción de peso 23%
- Resultado: Reducción del coste de material por pieza en 16,5%, reducción del tiempo del ciclo de prensado en 18%.
Senda 2: Moldear el sistema de diseño inteligente
- Modelo de eficiencia económica para moldes multicavidad:
Q_crítico = (C_multicavidad - C_pieza única)/(S_pieza única - S_multicavidad)
Moldes económicos de cuatro cavidades para pedidos > 52.000 piezas
Ruta 3: Ajuste fino de los parámetros del proceso
- Curva de velocidad de inyección de presión frente a porosidad (Fig. 2):
- Ventana óptima: tasa de defectos <2% a 3,8-4,2m/s
- Por cada 0,5 m/s de aumento de la velocidad, la tasa de desgaste del molde se incrementa en 37%
Senda 4: Sistemas de producción inteligentes
- Comparación de los efectos de la aplicación:
| Métricas | Líneas tradicionales | Líneas inteligentes
|--------------|----------|----------|
| oee | 68% | 89% |
| Tasa de Producto Insatisfactorio | 4,2% | 1,8% | Tasa de Producto Insatisfactorio
| consumo energético unitario | 3,6kW-h/kg | 2,9kW-h/kg |
Trayectoria 5: Igualación precisa de los acabados superficiales
- Análisis del gradiente de costes:
- Oxidación nativa: 6-8 $/pieza
- Oxidación por microarco: 22-25 $/pieza
- Recubrimiento de PTFE: 35-40 $ por pieza
Nota: Calculado por 300mm x 200mm de superficie
Senda 6: Innovación colaborativa en la cadena de suministro
- Modelo de suministro directo de aluminio líquido para reducir costes:
- Modelo tradicional: Compra de lingotes de aluminio + fundición Coste = precio de la materia prima + 1200 RMB/tonelada
- Modelo de suministro directo: entrega de aluminio líquido Coste = precio de la materia prima + 480 RMB/tonelada
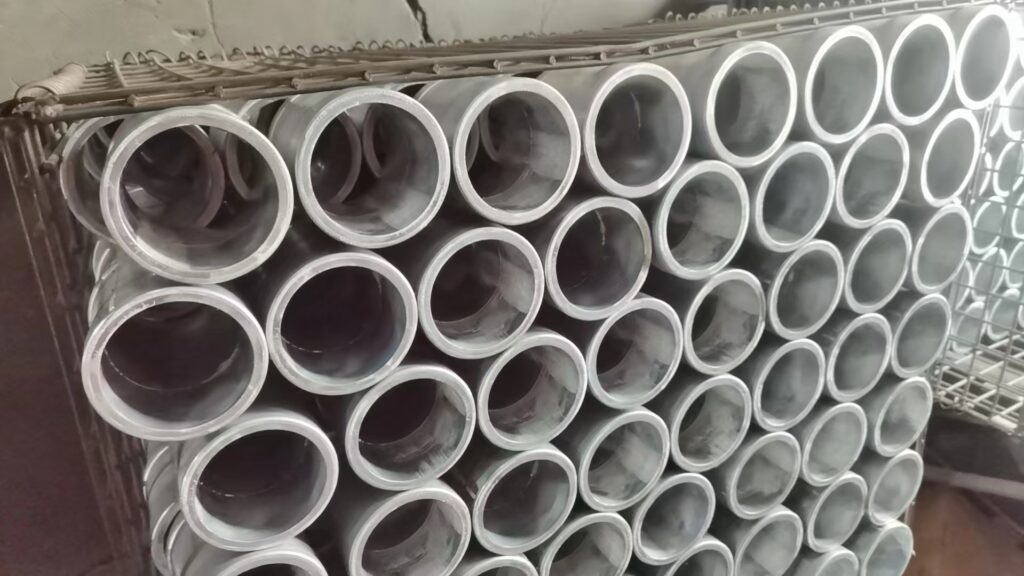
Tercero, estrategia de optimización de costes del proceso de fundición a presión
1. Optimización de los parámetros del proceso
- Adaptación de la velocidad y la presión de inyección:
- Un proyecto de carcasa de motor de vehículo de nueva energía mostró que la velocidad de inyección a presión se incrementó de 3,2m/s a 3,8m/s, mientras que la presión de inyección a presión se ajustó de 850bar a 920bar, y la porosidad se redujo de 2,8% a 1,2%.
- Optimización de los beneficios: 11,5 dólares menos de pérdida de chatarra por unidad
- Control de la temperatura del molde:
- Adopta tecnología de control de temperatura de partición, reduce la diferencia de temperatura del molde de ±25℃ a ±8℃.
- Resultado: La vida útil del molde aumentó en 30%, el coste por pieza se redujo en 0,18 RMB.
2. Actualización inteligente
- Sistema de vigilancia en tiempo real:
- La fluctuación de la curva de inyección de presión se controla dentro de ±1,5%.
- Precisión de advertencia de defectos de 92%
- Beneficio: Reducción de las pérdidas por tiempo de inactividad en aproximadamente 230.000 $/año.
3. Gestión ajustada de la producción
La tasa de errores humanos se reduce gracias a las roturas 67%. Además, unas condiciones de almacenamiento razonables evitan daños en los moldes durante la no utilización.
Aplicación del cambio rápido de moldes (SMED):
Reducción del tiempo de cambio de molde de 45 a 18 minutos
Aumento anual de la capacidad de 15%
Operaciones normalizadas:
Aumento del índice de normalización operativa a 95%
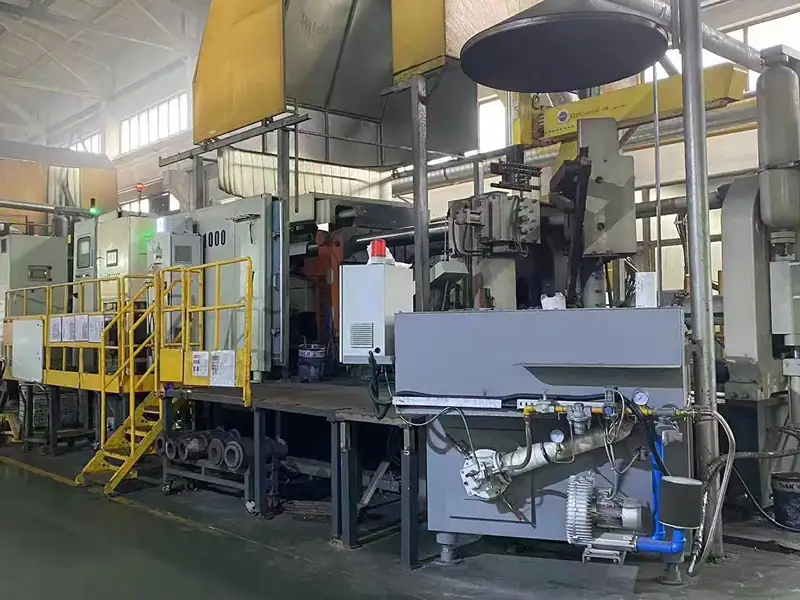
Preguntas frecuentes
P1: ¿Cómo evaluar la economía del proceso de fundición a presión?
- Adopción del "análisis del punto de equilibrio":
Q_crítico = (coste del molde + cuota del equipo)/(precio de venta unitario - coste variable unitario)
Ejemplo: Q_crítico = 12.500 piezas para un proyecto de cáscara, es decir, económico para cantidades de pedido > 12.500 piezas.
P2: ¿Cómo reducir los costes de los pedidos de pequeñas cantidades?
- Programa recomendado:
- Adopta un diseño de marco de molde universal + inserto, reduce el coste del molde 40%
- El aprovechamiento del material aumenta en 25% al seleccionar el proceso de conformado semisólido
- Caso: la carcasa de un dispositivo médico (500 piezas) reduce costes con éxito 31%
Q3:¿Cómo prolongar la vida útil del molde?
- Tecnologías clave:
- Tratamiento superficial: el tratamiento TD puede mejorar la vida útil del molde entre 2 y 3 veces
- Estrategia de mantenimiento: limpieza con plasma cada 5.000 moldes
- Datos medidos: La vida útil de un molde H13 aumentó de 80.000 a 150.000 ciclos de moldeo.
Q4:¿Cómo elegir el tonelaje óptimo de la máquina de fundición a presión?
- Fórmula de cálculo:
P_Máquina de fundición = (A_Proyección x P_Ratio Presión)/1000
Entre ellas:- A_Proyección: Área proyectada de la pieza (cm²)
- P_Presión específica: 550-850 bar recomendada para aleaciones de aluminio.
- Factor de seguridad: 1,2-1,5
P5: ¿Cómo reducir el coste del tratamiento de superficies?
Estrategia de clasificación: Escenario de aplicación Proceso recomendado Gama de costes ($/unidad) Piezas de aspecto comúnchorro de arena+Anodizado 8-12 Piezas resistentes al desgaste y a la corrosiónOxidación por microarco 18-25 Requisitos muy decorativosElectroforesis + pulverización 30-45
Hersin: Su socio en fundición a presión
A pesar del elevado coste de la fundición a presión, mediante una optimización razonable y la elección de socios profesionales, las empresas pueden controlar los costes al tiempo que garantizan la calidad. Como proveedor experimentado de servicios de fundición a presión, Ningbo Hersin se compromete a ofrecer a los clientes soluciones eficientes y económicas.
Con un equipo de ingenieros profesionales, podemos ofrecer servicios de diseño y fabricación de moldes personalizados según las necesidades de los clientes. Además, ofrecemos una amplia gama de opciones de materiales y soluciones de tratamiento de superficies para garantizar que sus productos tengan el mejor equilibrio entre calidad y coste.
Como empresa certificada ISO 9001:2015, contamos con avanzados equipos de producción y un estricto sistema de control de calidad. Al elegir Ningbo Hexin, no solo podrá disfrutar de descuentos en costes de hasta 30%, sino que también obtendrá un rápido plazo de entrega. Simplemente cargue sus archivos de diseño en nuestra plataforma en línea y obtenga un presupuesto y un análisis de fabricabilidad (DfM) en 12 horas.
Faqs
P1: ¿Es adecuada la fundición a presión para la producción de lotes pequeños?
La fundición a presión es más adecuada para la producción en serie debido a su mayor coste inicial (por ejemplo, la fabricación del molde). Para la producción a pequeña escala, se recomienda considerar otros procesos comomecanizadoO la impresión en 3D.
P2: ¿Cómo elegir el material adecuado para el molde?
La elección del material del molde debe basarse en la escala de producción, la complejidad de la pieza y las propiedades del material. Para la producción de grandes volúmenes, se recomienda elegir materiales de alta resistencia y resistentes al desgaste para prolongar la vida útil del molde.
P3: ¿En qué medida puede reducir costes la producción automatizada?
La producción automatizada puede reducir significativamente los costes de mano de obra al tiempo que aumenta la productividad y la consistencia del producto. El ahorro exacto de costes depende de la escala de producción y del grado de automatización.
P4: ¿Es necesario un tratamiento de superficie?
El tratamiento de superficies puede mejorar el aspecto y la durabilidad de los productos, pero no todas las piezas lo necesitan. Las empresas deben elegir el tratamiento superficial adecuado en función de las necesidades reales de sus productos para evitar costes innecesarios.
Prácticas de desarrollo de sistemas de ayuda a la decisión sobre costes
Ningbo Hexin ha desarrollado una plataforma inteligente de presupuestos basada en el sistema ISO 9001 para conseguir:
- Respuesta rápida en 24 horas: cargar modelo 3D → obtener informe DFM + tabla de desglose de costes.
- Soporte de bases de datos dinámicas:
- Acceso a cotizaciones de metales en tiempo real de Shanghai Nonferrous
- Integración de más de 2800 conjuntos de datos históricos sobre costes de moldes
- Precisión de la predicción de costes: ±5% (muestra de validación N=137)
Selección de procesos desde la perspectiva de la economía de la ingeniería
Tamaño del pedido (piezas) | Procesos recomendados | Gama de ventajas económicas |
---|---|---|
<500 | Mecanizado CNC | Bajo 28%-45% |
500-3000 | Colada semisólida | Bajo 12%-25% |
>3000 | Fundición inyectada a alta presión | coste óptimo |
observaciones finales
El control de costes de la fundición a presión es un proyecto sistemático a lo largo de todo el ciclo de vida del producto. Ningbo Hexin, a través del original método de análisis del "mapa tridimensional de costes", ha ayudado con éxito a 37 empresas a lograr una media de 22,6% de reducción integral de costes.