Utillaje rápido: soluciones innovadoras para acelerar el desarrollo y la fabricación de productos
Fecha:2025-02-14 Categorías:Blog Vistas:672
En esta era de rápidos cambios tecnológicos, la industria manufacturera está experimentando una profunda transformación, pasando de "primero la escala" a "ágil y eficiente". El utillaje rápido (Rapid Prólogo: El dilema de la fabricación de moldes en China y sus avances
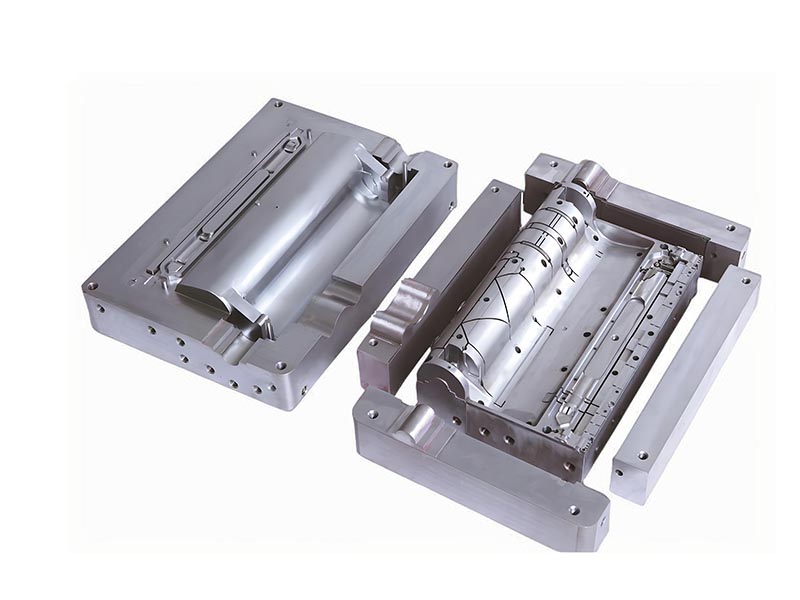
Como ingeniero profundamente comprometido con la industria de la fundición desde hace 23 años, yo (He Xin) he sido testigo de la metamorfosis de China, que ha pasado de ser un gran importador de moldes a la innovación independiente. En Ningbo, el punto de encuentro de la industria de moldes, hemos experimentado el largo ciclo tradicional de desarrollo de moldes de acero, el elevado coste de la prueba y error, pero también el revolucionario avance que ha supuesto la tecnología de moldes rápidos. Este artículo combinará la fundición a alta presión, fundición a baja presión y otros escenarios de aplicación práctica, revelando el papel del utillaje rápido en la aluminio Lógica técnica crítica en la fabricación de componentes.
1. La esencia de los moldes rápidos: no un compromiso, sino un ajuste preciso
1.1 Los tres principales puntos débiles de los moldes tradicionales
- tiempo costeEl desarrollo de un molde de fundición a alta presión puede llevar entre 8 y 12 semanas.
- presión financiera: El molde del cárter del motor de un automóvil cuesta más de 2 millones de dólares
- Riesgo de ensayo y error: fundición gravitacional Una modificación estructural del molde cuesta 150.000 dólares más
1.2 Orientación técnica del utillaje rápido
Logrado mediante la triple innovación en ciencia de materiales, procesamiento y tecnología de simulación:
- Ciclo Compresión 70%Mínimo 7 días laborables desde el diseño hasta el moldeo de prueba
- Reducción de costes 50%-80%El coste del molde de aluminio puede controlarse entre 80.000 y 150.000 dólares.
- Ajuste preciso de las cantidades de producción de pruebaAdmite requisitos de plantas piloto de 500 a 30.000 unidades.
2、Soluciones de molde rápidas para cuatro procesos de fundición principales
2.1 Escenario de la fundición a alta presión (HPDC)
La fundición a alta presión es un proceso en el que la sopa fundida de aleación de aluminio de 680-720°C se introduce a presión en la cavidad del molde a una velocidad de 10-50 m/s bajo una fuerza de cierre de 1600-2000T, y el reto principal es que el molde tiene que soportar cargas termomecánicas extremas. La innovación de Rapid Tooling en este escenario se refleja en la doble optimización del material y la estructura: el acero para trabajo en caliente QRO90 se utiliza para sustituir al tradicional acero H13, cuya composición de aleación de molibdeno-vanadio aumenta la resistencia a la fatiga térmica en 40%, y junto con el tratamiento de nitruración de la superficie (profundidad de capa de 0,2-0,3mm), puede prolongar la vida útil del utillaje hasta más de 30.000 ciclos de molde. El diseño estructural del sistema modular de insertos, para las zonas vulnerables (como las puertas, la posición del pasador de expulsión) para el refuerzo local, una empresa en Ningbo, la producción de nueva energía motor de la cubierta final, a través de la rápida sustitución de insertos para acortar el tiempo de mantenimiento del molde de 8 horas a 1,5 horas. En términos económicos, el coste por pieza se reduce de ¥18,6 a ¥7,3 para los moldes tradicionales, y el ciclo de desarrollo se comprime a 12 días, lo que resulta especialmente adecuado para proyectos de piezas estructurales de automoción con una producción anual inferior a 50.000 piezas.
Dificultades técnicas:
- El molde debe soportar una fuerza de cierre de 1600T
- Las aleaciones de aluminio se funden a temperaturas de hasta 700°C
- Requisitos de vida útil del módulo >50.000 ciclos
Soluciones de mecanizado rápido:
- Mejoras materiales: Sustitución del acero convencional H13 por el acero para trabajos en caliente QRO90
- Optimización estructural: Se utilizan insertos en el núcleo para reforzar localmente las zonas críticas.
- datos en tiempo realCarcasa del disipador térmico de la estación base 5G con una vida útil del molde de 32.000 ciclos en Ningbo (China).
2.2 Escenarios de fundición a baja presión (LPDC)
La fundición a baja presión inyecta líquido de aluminio suavemente en la cavidad del molde mediante una presión de aire de 0,5-0,8 MPa, lo que resulta especialmente adecuado para la producción de piezas de paredes finas que requieren altas densidades. El avance del molde rápido en este campo se centra en el control de la temperatura y la optimización del sistema de vertido: el desarrollo del sistema de control de la temperatura del molde multizona (±2℃ de precisión) con diseño de canal de refrigeración de gradiente, de modo que el rendimiento de la bandeja de batería de nueva energía producida por una empresa de Ningbo ha aumentado de 81% a 95%. El sistema de vertido diseñado mediante tecnología de optimización topológica ha acortado el tiempo de llenado de 9,2 segundos a 6,8 segundos, y ha aumentado la tasa de utilización del metal en 12%. La solución de utillaje rápido adopta insertos de acero preendurecido P20 + aleación de cobre local, lo que reduce el coste del utillaje a 45% de la solución tradicional. Es especialmente adecuada para las pruebas piloto de piezas estructurales complejas, como las carcasas hidráulicas aeroespaciales, con un plazo de entrega de proyecto típico de 15-20 días, y admite la producción de lotes pequeños de 3.000-8.000 piezas.
avance tecnológico:
- Desarrollo de un sistema especial de control de la temperatura del molde (precisión de ±2℃).
- Diseño de canal de refrigeración de gradiente
- caso (derecho)Un nuevo proyecto de carcasa de motor para vehículos de energía, el rendimiento del producto aumentó de 78% a 93%.
2.3 Escenario de fundición por gravedad
La fundición por gravedad se basa en el llenado por peso propio del líquido metálico y se utiliza habitualmente en la producción de piezas grandes y complejas. Rapid Mould ha logrado tres innovaciones importantes en este campo: en primer lugar, la tecnología de impresión 3D de molde de arena y molde de metal compuesto, a través del proceso SLS para producir un núcleo de arena (nivel de precisión CT8) combinado con el molde exterior de acero, de modo que el ciclo de producción de prueba del bloque de cilindros del motor de 45 días a 12 días; en segundo lugar, el sistema de control de equilibrio térmico, incrustado en las áreas clave de los insertos de aleación de cobre del molde (conductividad térmica 380W/m-K), de modo que una culata de cilindro de motor diesel marino de los El gradiente de temperatura se redujo en 40%; En tercer lugar, el diseño inteligente del escape, utilizando tapones de ventilación de metal poroso en lugar de las ranuras de escape tradicionales, redujo la tasa de defectos de porosidad de la fundición de 15% a menos de 3%. Los datos económicos muestran que el número de moldes de prueba del programa de molde rápido se reduce en 2,3 veces de media, y el coste de un solo molde de prueba se ahorra entre 12 y 18.000 yuanes, lo que resulta especialmente adecuado para el desarrollo de componentes de maquinaria de construcción a gran escala con un peso de pieza única de más de 50 kg.
Prácticas innovadoras:
- Tecnología de combinación de arena de impresión 3D y molde metálico
- Incrustación localizada de aleación de cobre para mejorar el equilibrio térmico
- beneficio económicoReducción de 40% en el número de pruebas de molde y de 65% en el tiempo de ciclo para la optimización del sistema de colada.
3、Cinco tecnologías básicas de moldeo rápido
3.1 Matriz de selección de materiales
escenario de aplicación | material de recomendación | Dureza (HRC) | Conductividad térmica (W/m-K) | índice de costes |
---|---|---|---|---|
fundición a alta presión | H11+ nitruración superficial | 48-52 | 24.3 | ★★★★ |
Aleaciones de aluminio en pequeñas cantidades | Aluminio aeroespacial 7075 | 35-40 | 130 | ★★★ |
Piezas estructurales de alta precisión | Acero para herramientas S7 | 54-56 | 29.4 | ★★★★☆ |
3.2 Comparación de los procesos de tratamiento de superficies
- oxidación por microarcoFormación de una capa cerámica de 10-30μm, resistencia térmica >800°C
- Revestimiento DLCCoeficiente de fricción reducido a 0,1, lo que multiplica por 3 la vida útil del molde.
- ejemplo real: Un molde de carcasa de turbocompresor se trata con un revestimiento compuesto, y la vida útil del molde supera las 80.000 veces.
3.3 Modelo de predicción de vida útil
Basado en datos de simulación de Moldflow con seguimiento sobre el terreno:
L=K× (σappliedσUTS)m×Nthermal
Entre ellas:
- KConstantes del material (0,8-1,2 para las aleaciones de aluminio)
- mÍndice de fatiga (6,5 para moldes de acero, 4,2 para moldes de aluminio)
- Ejemplos de aplicacionesError de predicción dentro de ±8%
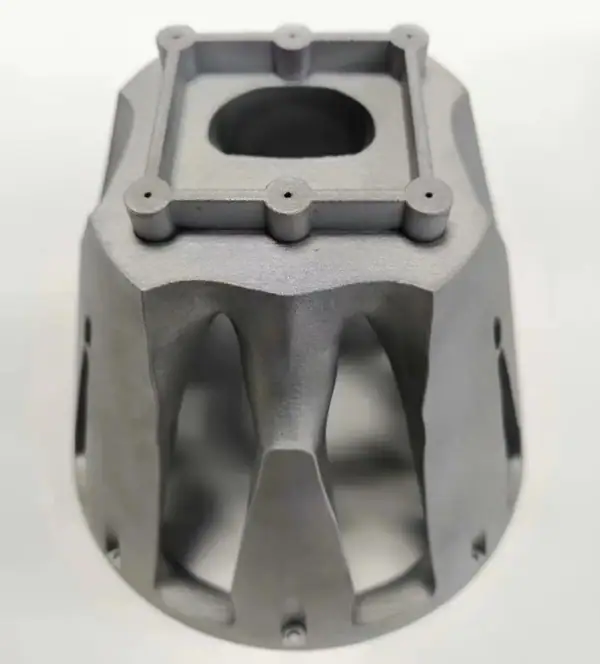
Impresión 3D Prototipado rápido
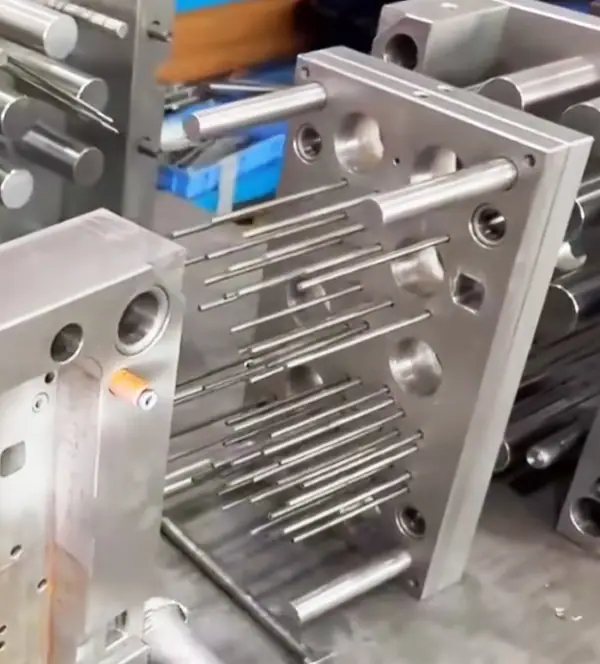
Utillaje rápido
4、La integración de la impresión 3D y la innovación rápida de moldes
El canal de agua de refrigeración conformado es la principal ventaja de los moldes de impresión 3D: en los moldes fabricados con tecnología SLM, la separación entre el canal de refrigeración y el contorno del producto puede controlarse entre 1,5 y 2 mm (proceso de perforación tradicional ≥ 8 mm), por lo que el ciclo de inyección de una rejilla de automóvil se acorta de 48 a 32 segundos, y la cantidad de deformación se reduce de 0,8 mm a 0,3 mm.La tecnología de impresión de material de gradiente puede lograr la combinación de la alta dureza de HRC55 en la superficie del núcleo y la alta tenacidad de HRC35 en el núcleo. La combinación de la alta dureza de HRC35 en la superficie del núcleo y la alta tenacidad de HRC35 en el núcleo, un molde de soporte de dron se ha tratado con esta tecnología, y la resistencia al impacto se ha mejorado en 60%. El análisis económico muestra que para los moldes complejos con más de 5 vías de agua conformadas, el coste total de la solución de impresión 3D se puede reducir en 42% en comparación con CNC, lo que es especialmente adecuado para escenarios de precisión como los moldes de chips microfluídicos médicos. Las limitaciones técnicas actuales residen en el tamaño máximo de moldeo (la mayoría de los dispositivos ≤ 500 mm) y los requisitos de posprocesamiento (las superficies de acoplamiento clave aún requieren acabado CNC), pero con el desarrollo de la tecnología multiláser, se espera que la impresión global de moldes a escala de un metro pueda lograrse en 2025.
4.1 Avances tecnológicos
- Canales de refrigeración conformadosAcorta el tiempo del ciclo de inyección en 23% y reduce la deformación en 40%.
- Impresión de material degradadoDureza de la superficie del núcleo HRC55, dureza interna HRC35
- Datos del casoAumento de la eficacia de refrigeración del molde de la pantalla LED de 37%
4.2 Análisis económico
norma | Moldes CNC convencionales | Moldes impresos en 3D |
---|---|---|
ciclo de desarrollo | 18 días | 6 días |
Costes estructurales complejos | 100% | 65% |
Gastos de modificación | 30% | 8% |
5. Tres recomendaciones prácticas para las empresas manufactureras
- Establecimiento de un sistema de clasificación de moldes:
- Moldes de clase A (>100.000 moldes): moldes de acero convencionales
- Moldes de clase B (10.000-50.000 moldes): Moldes de acero de prototipado rápido
- Moldes de clase C (<10.000 moldes): impresión 3D/moldes de aluminio
- Implantación de gemelos digitales:
- Introducción del sistema de simulación MAGMA en la fase de diseño del molde
- Instalación de sensores IoT para controlar la distribución de la tensión durante la fase de producción
- Creación de un mecanismo de respuesta rápida:
- Biblioteca de reserva de molduras normalizadas (cubre la especificación común 80%)
- Establecimiento de redes regionales de colaboración (Ningbo ha formado un círculo de cadena de suministro de 2 horas)
Conclusión: Los próximos diez años de la industria del molde
Desde el proyecto Ningbo Mould Cloud Platform que estamos implementando, el molde rápido se está transformando en inteligente y orientado al servicio:
- Sistema inteligente de oferta: 5 minutos para generar una solución de molde introduciendo parámetros
- trazabilidad blockchainTrazabilidad de la calidad durante todo el ciclo de vida
- Biblioteca de moldes compartidaReduzca los costes de inventario de la PYME 30%
Utillaje rápidoPreguntas más frecuentes (FAQ)
P1: ¿Puede utilizarse el utillaje rápido para la producción en serie?
R: Se requiere una evaluación basada en escenarios:
- Molde de aleación de aluminio: adecuado para lotes pequeños <5000 piezas
- Moldes de acero preendurecido: pueden soportar 30.000-50.000 piezas
- Se recomienda incorporar un sistema de monitorización digital para evaluar el estado del molde en tiempo real
P2:¿Cómo controlar la precisión dimensional del utillaje rápido?
R: Programa recomendado:
- Fase de mecanizado: mediante máquinas herramienta de 5 ejes + medición en línea (precisión ±0,02 mm)
- Fase de prueba del molde: inspección completa de las dimensiones críticas mediante una máquina de medición de coordenadas (MMC).
- Fase de producción en serie: muestreo y pruebas cada 500 moldes
P3: ¿Cuáles son las tecnologías innovadoras para el tratamiento superficial de herramientas rápidas?
R: Tres tecnologías de vanguardia:
- Revestimiento láser: reparación de zonas desgastadas con un coste reducido de 40%
- Revestimiento nanocompuesto: coeficiente de fricción reducido a 0,08
- Nitruración por plasma: dureza superficial hasta HV1200
P4: ¿Cuáles son las limitaciones de los moldes impresos en 3D?
R: Principales limitaciones actuales:
Requisitos de postprocesamiento: a menudo es necesario el acabado CNC de superficies de acoplamiento críticas.
Tamaño máximo: la mayoría de los dispositivos están limitados a 500 x 500 x 500 mm.
Selección de materiales: Actualmente el soporte principal es el acero para troqueles, la aleación de aluminio