Diseño de moldes de fundición a presión de aluminio: guía práctica del proceso a la optimización
Fecha:2025-02-15 Categorías:Blog Vistas:867
Como ingeniero superior de Ningbo Hersin, que lleva más de 20 años dedicado a la industria de la fundición, conozco muy bien el sector del aluminio. molde de fundición a presión La posición central en la industria manufacturera. Ya se trate de piezas de automóviles, productos electrónicos 3C, o componentes aeroespaciales, proceso de fundición a presión de aluminio de alta eficiencia y precisión son inseparables del diseño de la matriz del soporte sutil. Este artículo se combinará con la experiencia práctica, el análisis sistemático de los puntos de diseño de moldes de fundición a presión de aluminio, las tendencias tecnológicas y la estrategia de optimización, para los colegas de la industria para proporcionar una guía práctica.
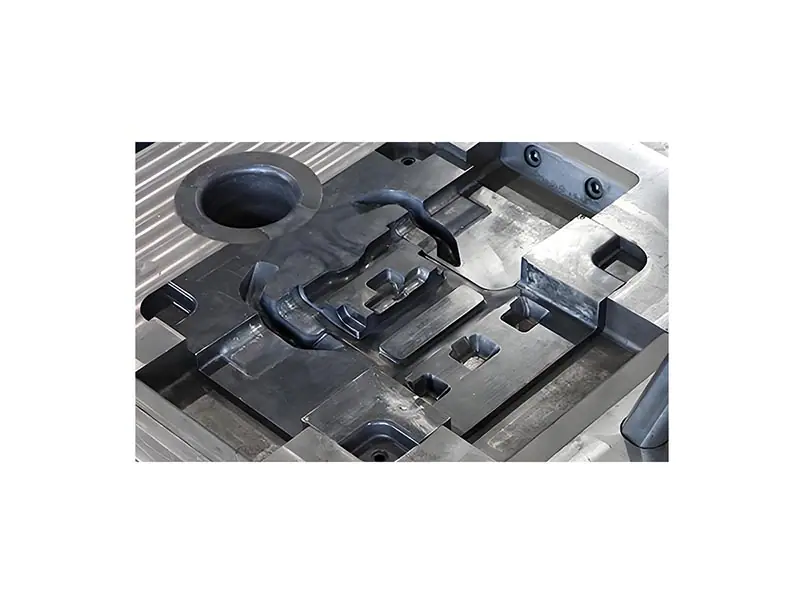
El valor fundamental de un molde de fundición a presión de aluminio: por qué es la clave del éxito o el fracaso del proceso
El molde de fundición a presión no es sólo la "plantilla" de conformado del metal, sino también la eficacia de la producción y la calidad del producto.factor determinanteLa importancia del programa es triple. Su importancia se refleja en tres ámbitos:
- Precisión exacta
El diseño de la cavidad del molde determina directamente la tolerancia dimensional (normalmente ±0,1 mm) y el acabado superficial (Ra 1,6~3,2μm) de la pieza fundida. Por ejemplo, en la fundición a presión de bloques de motor de automoción, el diseño del sistema de refrigeración del molde, si no es razonable, provocará una contracción local desigual, lo que desencadenará porosidad o deformación. - Alta eficacia de producción
Un conjunto de moldes multicavidad optimizados puede aumentar la eficiencia de la producción en más de 300%. Tomando como ejemplo un proyecto de carcasa de motor de un vehículo de nueva energía, tras adoptar un molde de 4 cavidades, la producción por hora pasó de 15 piezas a 60 piezas, mientras que la tasa de rendimiento se mantuvo estable en más de 98%. - Ventaja de costes
La vida útil del molde repercute directamente en el coste por pieza. Utilizando acero H13 para trabajo en caliente en los moldes, se puede aumentar la vida útil del molde de 100.000 a 500.000 moldes mediante el tratamiento TD superficial (método de difusión térmica), lo que reduce significativamente el coste por pieza.
Cinco tipos principales de moldes de fundición de aluminio a presión y estrategia de selección
Tipo de molde | Escenarios aplicables | ciclo de costes | Características técnicas |
---|---|---|---|
Molde prototipo | Validación de lotes pequeños (<500 unidades) | Bajo coste/2-3 semanas | Impresión 3D +mecanizadoproceso compuesto |
Utillaje rápido | Producción piloto (500-5000 piezas) | Coste medio/4-6 semanas | Fabricación aditiva de revestimientos láser |
Molde unitario | Multiespecies y lotes pequeños | Diseño modular | Cambio rápido de insertos de cavidades |
Molde de producción | Gran volumen (>100.000 piezas) | Coste elevado/8-12 semanas | Estructura multideslizante + sistema de refrigeración por puntos |
Molde de recorte | Desbarbado y separación de canales | necesario para | Servoaccionamiento hidráulico + guiado de precisión |
Sugerencias para la selección:
- Fundición inyectada a alta presión(HPDC)Se da prioridad a los moldes de producción con sistemas de vacío para reducir los agujeros de aire;
- Piezas complejas de paredes delgadas(por ejemplo, marcos centrales de teléfonos móviles) Se recomienda el mecanizado rápido, combinado con técnicas locales de fundición a presión;
- Producción flexible multivariedadLos moldes unitarios permiten reducir el tiempo de cambio a menos de 30 minutos.
Las seis reglas de oro del diseño de moldes de fundición de aluminio a presión
- Optimización de líneas fractales
La línea de separación debe evitar las superficies funcionales críticas. Por ejemplo, el radiador de una estación base 5G utiliza el tronzado de superficies curvas para que las rebabas se produzcan en superficies sin contacto, lo que reduce los costes de postprocesado. - Diseño hidrodinámico de sistemas de canales de flujo
adopciónColador transversal cónico(Entrada 8mm → Salida 4mm), junto con un ángulo de compuerta interior de 30°, puede lograr un llenado suave del líquido de aluminio y evitar la formación de escoria por oxidación causada por el flujo turbulento. - Control del balance térmico de los sistemas de refrigeración
La pieza central está incrustada con insertos de cobre de berilio (conductividad térmica 210 W/mK), y el control de la temperatura de gradiente se consigue con el termostato del molde (250°C en la zona de la compuerta → 180°C al final), lo que acorta el tiempo de enfriamiento en 20%. - Cálculo científico de la inclinación de desmoldeo
Dependiendo de la contracción de la aleación (aproximadamente 0,6% para ADC12) y de los requisitos de la superficie, la inclinación de la pared exterior se toma como 1°~1,5° y se aumenta a 2°~3° para piezas de cavidad profunda. Por ejemplo, la estructura de cavidad profunda de la carcasa de un UAV utiliza una inclinación de 3°, y la resistencia a la eyección se reduce en 40%. - Disposición precisa de los tanques de escape y rebosadero
Un tanque de desbordamiento escalonado (profundidad 0,3mm→0,8mm) se establece en el área de llenado final, y con la válvula de vacío (vacío ≤ 50mbar), la porosidad puede ser controlada por debajo de 0,5%. - Selección avanzada de materiales para moldes
- Piezas normales: acero H13 (dureza 48-52 HRC)
- Requisitos de alta resistencia al desgaste: acero DIEVAR (con adiciones de cobalto y molibdeno)
- Escenas resistentes a la corrosión: STAVAX ESR (pulido espejo a Ra 0,05μm)
Tecnología punta en la industria: la digitalización y la inteligencia potencian la mejora de los moldes
- Iteraciones de diseño basadas en simulación de IA
Con el software AnyCasting/MAGMA, el proceso completo de simulación de llenado, solidificación y tensión puede completarse en 48 horas, y el riesgo de contracción puede predecirse con antelación. En un proyecto de carcasa de caja de cambios se optimizó la posición de la compuerta mediante simulación, con lo que se redujo 3 veces el número de pruebas de molde. - Vías de refrigeración conformadas impresas en 3D
El uso de la tecnología de fusión por láser de zona seleccionada (SLM) para fabricar vías de agua conformadas ha permitido controlar la diferencia de temperatura del molde en ±5 °C, lo que ha reducido considerablemente los nudos térmicos. Tras la aplicación de un molde de pantalla LED, el tiempo de ciclo se acortó en 18%. - Sistema de supervisión de moldes basado en Internet de las Cosas (IoT)
Se implantan sensores de temperatura/presión en puntos clave del molde para controlar en tiempo real el estado de la superficie de la cavidad. Cuando se detectan fluctuaciones anormales en la fuerza de cierre (>5%), se activa automáticamente una alerta temprana para evitar defectos en los lotes.
Caso práctico: Optimización del molde de la bandeja de la batería de un vehículo de nueva energía
desafío:
- Tamaño del producto 1200×800mm, grosor medio de la pared 2,5mm, estanqueidad al aire ≤ 0,5Pa-m³/s requerida.
- El rendimiento inicial es de sólo 65%, los principales defectos son la segregación en frío y la deformación.
prescripción:
- Recorrido de llenado equilibrado con alimentación tangencial de compuertas dobles
- Núcleo del molde implantado con 12 juegos de tubos de refrigeración pulsada para el control dinámico de la temperatura.
- Sistema eyector con resortes de gas nitrógeno para una fuerza de liberación equilibrada
basado en los resultados:
- Rendimiento mejorado a 92%
- El ritmo de producción se reduce de 180 a 140
- La vida útil del molde supera los 300.000 ciclos de moldeo
Preguntas más frecuentes (FAQ)
Q1:¿Cómo evaluar la solidez técnica de los proveedores de moldes?
- Métricas clave: valores Cpk de casos anteriores (≥1,33), capacidad de análisis CAE, exhaustividad de los informes de moldes de ensayo.
P2: ¿Cómo elegir el revestimiento de la superficie del molde?
- Convencional: revestimiento CrN (dureza 2200 HV)
- Alta resistencia al desgaste: AlCrN (resistencia térmica 900°C)
- Mejora de la liberación: revestimiento DLC tipo diamante
P3: ¿Cuáles son las mejores prácticas para el mantenimiento de los moldes?
- Diariamente: Compruebe la lubricación del guardacabo (utilice grasa de alta temperatura NLGI grado 2)
- Cada 5000 moldes: EDM repara pequeñas grietas
- Cada 50.000 ciclos de moldeo: Tratamiento de revenido integral (550°C x 2h)
observaciones finales
El diseño de moldes de fundición a presión de aluminio es una combinación de ciencia y arte, que requiere rigurosos cálculos de ingeniería y se basa en una rica experiencia práctica. Con la profunda penetración de la tecnología digital, la industria del molde está abriendo paso al nuevo paradigma "diseño inteligente - fabricación de precisión - mantenimiento predictivo". Como profesional, la única forma de tomar la delantera en el juego triangular de costes, eficiencia y calidad es seguir abrazando la innovación.
Para soluciones de moldes personalizadas o asesoramiento técnico. Bienvenido a contactar Ningbo Hersin Casting Team - Con 20 años de experiencia, potenciamos sus productos con la máxima precisión y rendimiento.