Análisis de las causas del granallado y soluciones recomendadas para los productos de fundición a presión de aleación de aluminio ADC12
Fecha:2025-04-07 Categorías:Blog Vistas:372
En este documento se analiza sistemáticamente la fundición a presiónaluminioSe correlacionan las propiedades materiales del ADC12 con el proceso de granallado y se propone una solución multidimensional para el frecuente problema de descascarillado por granallado en la industria. El artículo dilucida en primer lugar la influencia directa de la composición química de la ADC12 en las propiedades de los materiales, revelando la correlación intrínseca entre las fluctuaciones del contenido de silicio, cobre, magnesio y otros elementos, así como la fluidez, la fuerza y la resistencia a la corrosión de la aleación. Basándose en el principio del proceso de granallado, el artículo analiza el efecto cuantitativo de variables fundamentales como los parámetros de granallado y la velocidad de eyección sobre el efecto del tratamiento superficial, y señala que existen deficiencias comunes en la industria actual, que sólo se centra en la adherencia pero descuida la normalización de la calidad superficial. Mediante el análisis del flujo del molde, la optimización de los parámetros del proceso y la verificación experimental, hemos construido de forma innovadora un sistema de mejora de toda la cadena, desde el control del origen del material hasta el diseño del molde y el mantenimiento del equipo, y, combinado con el caso de la carcasa del motor, hemos demostrado la eficacia de medidas clave como la optimización del canal de escape y el ajuste de la presión de almacenamiento de energía. La investigación no solo proporciona una ruta técnica cuantificable para la mejora de la calidad del granallado ADC12, sino que también apunta a la nueva dirección de la optimización de procesos basada en la tecnología de IA de big data, que tiene una importancia orientativa práctica para promover la reducción de costes y el aumento de la eficiencia en la industria de la fundición a presión.
Propiedades del material de la aleación de aluminio fundido a presión ADC12
1. Composición química
Principales elementos y sus funciones
La ADC12 contiene principalmente silicio (Si), cobre (Cu), magnesio (Mg), manganeso (Mn), hierro (Fe), zinc (Zn) y aluminio (Al). Entre ellos:
Silicio: se permite que el contenido sea de 9,5~11,5%, si es inferior a 9,5%, habrá mala fluidez de la aleación y llenado incompleto del producto, si es superior a 11,5%, será fácil que haya segregación excesiva o que se formen cristales laminares con ferroaluminio, lo que desestabilizará la organización de la aleación y hará que el producto quede suelto;
Cobre: se permite que el contenido sea de 1,5~3,5%, si es inferior a 1,5%, habrá una disminución de la resistencia y dureza del producto, si es superior a 3,5%, habrá una disminución de la resistencia a la corrosión;
Magnesio: contenido en 0,1 ~ 0,3%, si el contenido de magnesio es inferior a 0,1%, se producirá una disminución de la resistencia y dureza del producto, si es superior a 0,3%, dará lugar a que los productos de fundición a presión produzcan grietas térmicas y otros defectos;
Manganeso: el contenido de 0,2 ~ 0,5%, si es inferior a 0,2%, habrá tosquedad de grano de aleación, resistencia a la tracción y límite elástico al mismo tiempo reducir, si es superior a 0,5%, habrá aumento de la fragilidad dura de aleación, difícil de procesar, fácil a la fractura frágil;
Hierro: contenido en 0,6~1,2%, si es inferior a 0,6%, fácil de pegarse al molde, la formación de deformación de la tensión del producto, si es superior a 1,2%, habrá aleación debido a la fragilidad dura y agrietamiento; (hierro y silicio al mismo tiempo ultra-alta, fácil de formar escamas de silicio-hierro - cristales de aluminio, lo que resulta en la corrosión intercristalina, la disminución de la resistencia de la aleación).
Zinc: contenido ≤ 1,2%, por lo que el zinc puede estar ausente de la aleación ADC12 (difícil de eliminar al refinar otras aleaciones), y si está presente, debe ser inferior a 1,2%.
Además, la proporción de material de refinado es también muy importante, si hay demasiado material de refinado, se producirá la cristalización del grano grueso del producto, la resistencia y la dureza del producto se reduce.
En resumen, la composición química (contenido porcentual) de una aleación determina básicamente sus propiedades mecánicas y también rige el aspecto y la organización cristalina interna del producto.
2、Propiedades físicas
Aleación de aluminio ADC12Densidad aproximada 2,7 g/cm³(matemáticas) géneroPunto de fusión 580~620°CEs importante señalar que los valores de estas propiedades físicas pueden variar en función de factores como las diferencias específicas de composición y los procesos de producción.
ADC12'sCoeficiente de dilatación térmicaRelativamente grande, esta característica está algo relacionada con el proceso de voladura.
3. Propiedades mecánicas
Los índices de propiedades mecánicas de la aleación de aluminio ADC12 suelen ser los siguientes:
Resistencia a la tracción: aprox. 228~296MPa;
Límite elástico: alrededor de 140~170MPa;
Dureza Brinell: alrededor de 70~95HB.
Alargamiento: 1~3%
Los indicadores específicos de rendimiento también pueden variar en función de factores como las diferencias de composición y los procesos de producción.
Visión general del proceso de granallado
1、El principio del granallado
Mecanismo de funcionamiento del equipo de granallado
El mecanismo de funcionamiento del granallado consta de las siguientes partes principales:
Sistemas de almacenamiento y transporte de granalla: La granalla suele almacenarse en tolvas específicas y transportarse a la granalladora mediante un transportador (por ejemplo, un transportador de tornillo);
Granalladora: es el componente central del equipo de granallado, granalladora dentro de la rotación de alta velocidad del impulsor, el impulsor tiene un número de cuchillas, cuando el impulsor gira a alta velocidad, las cuchillas impulsará el proyectil para acelerar y expulsado a alta velocidad;
Sistema de transporte de piezas de trabajo: Se utiliza para transportar la pieza de trabajo a tratar a la zona de granallado y enviarla fuera después de que el tratamiento se ha completado, los métodos de transporte comúnmente utilizados son orugas, tipo gancho, transportador de rodillos y así sucesivamente;
Sistema de eliminación de polvo: en el proceso de granallado se producirá una gran cantidad de polvo e impurezas, el sistema de eliminación de polvo a través del ventilador genera presión negativa, el polvo será aspirado en el colector de polvo para su filtración y purificación, con el fin de garantizar que el ambiente de trabajo es limpio y en línea con los requisitos ambientales.
El granallado es una tecnología de tratamiento de superficies, el principio es principalmente el uso de la rotación de alta velocidad del impulsor proyectil (por lo general granalla de acero, alambre de acero cortado tiro, etc) a la superficie de la pieza a procesar a una velocidad muy alta, en el proceso de granallado, el proyectil tiene un gran impacto de la energía cinética en la superficie de la pieza de trabajo para producir un fuerte impacto y el efecto de raspado, este impacto puede eliminar la superficie de la pieza de trabajo de óxido, herrumbre, suciedad y otras adherencias, y al mismo tiempo en la superficie de la pieza de trabajo. Al mismo tiempo en la superficie de la pieza de trabajo para producir tensión de compresión, de modo que la superficie se fortalece. Mejorar la resistencia a la fatiga y la resistencia a la corrosión bajo tensión; específicamente, el impulsor en el equipo de granallado en el motor de accionamiento de rotación de alta velocidad, el proyectil es acelerado por el impulsor lanzado en una dirección específica, cuando el impacto del proyectil en la superficie de la pieza de trabajo hará que la superficie del material de la pieza de trabajo para producir la deformación plástica y se caen, a fin de lograr el efecto de limpieza y fortalecimiento.
El efecto del granallado depende del material del proyectil, forma, tamaño, velocidad, ángulo de chorro, así como el tiempo de granallado y muchos otros factores, diferentes piezas de trabajo y los requisitos de procesamiento deben elegir los parámetros adecuados del proceso de granallado, con el fin de lograr la calidad deseada y la eficiencia del tratamiento.
2, parámetros del proceso de granallado
Material y tamaño del granallado: para el granallado de la aleación de aluminio ADC12 se suele utilizar granalla de acero inoxidable 304 o granalla de acero cortada con alambre; el diámetro de la granalla es de 0,2 ~ 0,6 mm;
Velocidad de granallado: La velocidad de granallado utilizada para las aleaciones de aluminio ADC12 suele ser de 50~70 m/s;
Ángulo de chorreado: normalmente 30~75 grados;
Tiempo de granallado: según el tamaño, la forma y el estado de la superficie de la pieza, generalmente 5~15 minutos;
Caudal de granalla: según el equipo de granallado y la pieza, suele oscilar entre 90 ~ 280 kg / min;
Principio de ajuste: en la producción real, a través de pruebas e inspección de calidad para determinar el más adecuado para la pieza de trabajo que se granallado parámetros del proceso, con el fin de obtener el efecto deseado de tratamiento de superficie y evitar la descamación, arrugas y otros problemas, para obtener el efecto ideal de tratamiento de superficie con el parámetro más pequeño es la mayor búsqueda de los ajustes de parámetros de granallado, sino también una de las maneras de maximizar los beneficios.
3, proceso de granallado en productos de fundición a presión de aleación de aluminio ADC12 en la aplicación de la situación actual
Prácticas habituales en el sector
El propósito del granallado de piezas de trabajo es sólo para aumentar la adherencia de la pintura de hornear o los requisitos de pulverización de plástico, el uso de gránulos de granalla gruesa, el tiempo de granallado es más corto, el granallado de piezas de trabajo despellejadas utilizando el tratamiento de lijado de retrabajo, ninguna investigación fina de las causas de problemas tales como la piel de granallado, así como el desarrollo de programas de mejora;
Requisitos estrictos sobre la calidad de la superficie de la pieza de trabajo después del granallado, tales como la diferencia de color (la norma es de color blanco plateado), despellejamiento (no fuera de las piezas irregulares suspendidas en la superficie del producto), arrugas (la superficie de las arrugas de granallado), la deformación y otros defectos en la recepción de la normalización del límite inferior, de modo que el proceso de fundición a presión de todas las causas de los agujeros de aire del producto, el aflojamiento, la segregación en frío, marcas de flujo (estancamiento) y otros defectos en el análisis de las causas, y el desarrollo de medidas de mejora para la máquina de granallado. Algunas de las funciones de la máquina de granallado para la mejora, la optimización continua, la búsqueda de la calidad de la superficie de granallado para lograr el objetivo de 0 defectos.
Problemas y retos
Las piezas de granallado de aleación de aluminio ADC12 calificadas de alta calidad son palanquillas de fundición a presión calificadas de alta calidad en la finalización del procesamiento del equipo de granallado, si las piezas de granallado aparecen despellejamiento y otros problemas, el final del análisis inverso de las razones: ¿el equipo de granallado está intacto? → ¿Es adecuado el uso de partículas de granallado? → Establecer el tiempo, la velocidad y el flujo de granallado es apropiado? → ¿Se ajusta el esmerilado de la pieza bruta de fundición a presión a los requisitos? → ¿Tiene la pieza bruta de fundición a presión defectos de aspecto (segregación en frío, marcas de flujo, manchas, poros, grietas, etc.)? →¿Están intactos la producción de fundición a presión, la máquina de fundición a presión y los equipos periféricos? → ¿Son óptimos los parámetros del proceso (presión de expulsión, velocidad de expulsión, temperatura de colada, concentración de revestimiento y volumen de pulverización, etc.)? →molde de fundición a presiónEl sistema de vertido, el sistema de refrigeración, el mecanismo de expulsión, el acabado de la cavidad, la pendiente de desmoldeo, la dureza de las partes de la cavidad, la esquina redondeada de la cavidad, etc.), ¿cumplen los requisitos? →¿El mecanismo móvil del molde de fundición a presión funciona de forma estable y fiable? →¿Son óptimos los parámetros del proceso de fusión (material del horno con, temperatura de fusión, temperatura de refinado, relación de dosificación del agente de refinado, presión y flujo de ajuste del nitrógeno, etc.)? →¿Se ajustan los elementos químicos del ADC12 a los requisitos?
En la producción real, puede analizarse que existe un problema en un determinado eslabón, pero al resolver su problema, debe considerarse exhaustivamente si traerá otros problemas, por lo que necesita comunicación y colaboración en equipo, y necesita argumentación polifacética y verificación experimental múltiple.
03.
Análisis de las causas del granallado de productos de aleación de aluminio fundido a presión ADC12
1. Factores materiales Fuente-ADC12
Contenido en silicio (Si) ≥ 11,5%: Hierro (Fe) ≥ 1,2%, lo que da lugar a un exceso de quimiosíntesis, así como a una organización laminar, una organización superficial suelta y una descamación bajo el impacto del granallado y el raspado;
Magnesio (Mg) ≥ 0,3%: manganeso (Mn) ≥ 0,5%, zinc (Zn) ≥ 1,2%; producen superficies duras quebradizas o superficies agrietadas, bajo el impacto del granallado, se producirá una grave descamación y falta de material;
Cobre (Cu) ≤ 1,5%: La resistencia y dureza superficial del producto es insuficiente, bajo el impacto del granallado y raspado, se producirá deformación cóncava y despellejamiento o arrugas;
Relación de material de retorno del horno ≥ 50%: la eliminación de la escoria de fusión y la desgasificación son muy difíciles, las propiedades físicas y las propiedades mecánicas se reducirán, los productos de fundición a presión son difíciles de lograr una buena superficie (porosidad e impurezas presentes en el producto llenan la superficie final), el granallado es fácil de pelar.
2、Factores de diseño del molde de fundición a presión
La sección transversal del canal de vertido recto del molde y la relación de la sección transversal del canal de vertido transversal no es adecuada, la sección transversal total del canal de vertido transversal es mayor que la sección transversal del canal de vertido recto, en el canal de vertido transversal a la presión negativa generada por el volumen de gas, el gas entra en la cavidad del molde para aumentar la carga del canal de escape, el gas es fácil de ser retenido en el producto, la formación de agujeros de aire, la distribución de los agujeros de aire a la superficie poco profunda del producto, el granallado será despellejado o ampollado;
Llenado del bebedero con ramales múltiples, el espaciado del bebedero es demasiado grande, dos ramales del bebedero en medio de la formación de reflujo de gas atrapado; dos o más ramales del bebedero en dirección de llenado de cobertura, la formación de turbulencia, la superficie del producto tendrá agujeros de aire (comúnmente conocido como estancamiento del tumor), por el impacto de la fuerza de granallado, se despellejará;
El diseño del molde hace que circule el agua de refrigeración, se llega al final del llenado del bebedero, lo que resulta en que la temperatura del molde está siempre en un estado bajo, la superficie del producto poco profunda aparece segregación en frío, marcas de flujo, marcas de viruela y otras condiciones sueltas, el impacto de la fuerza de granallado, será un despellejamiento grave;
El diseño del molde del canal de escape no puede satisfacer la demanda de escape (velocidad de escape superior a 350 m / s), la ubicación del canal de desbordamiento no está al final del llenado o posición defectuosa, lo que resulta en el escape y la escoria de escape no es suave y el aire atrapado, el producto de llenado al final de la ubicación de la capa superficial poco profunda de los agujeros de aire, granallado fuerza de impacto, despellejamiento;
La sección transversal del molde y de la compuerta interior es demasiado pequeña, la presión de llenado está bloqueada, aumentando las dificultades de transferencia de presión, el producto está suelto - la resistencia y la dureza no están a la altura de los requisitos del impacto de la fuerza de granallado, se despellejará o deformará.
3, máquina de fundición a presión y factores periféricos del equipo
Tipo de máquina de fundición a presión placa paralelismo y planitud (≤ 0,5) error es grande, la sujeción no es sólida, lo que resulta en la superficie de separación ejecutar agua de aluminio, agotamiento de la presión de colada, la fuerza del producto y la disminución de la dureza, el impacto de la fuerza de granallado, desollado del producto.
Excentricidad entre el centro de expulsión del mecanismo de expulsión y el centro del orificio de expulsión de la placa modelo fija, lo que provoca el estancamiento del punzón de expulsión, el agotamiento de la presión, la reducción de la resistencia y dureza del producto, el impacto de la fuerza de chorreado y el despellejamiento del producto;
Holgura excesiva entre el punzón y el vaso de fusión, retroceso del agua de aluminio durante la inyección por compresión, lo que provoca el estancamiento del punzón, el agotamiento de la presión, la disminución de la resistencia y la dureza del producto, el impacto de la fuerza de granallado, la descamación del producto.
Fundición a presión alrededor de la máquina de vacío-válvula de vacío obstrucción, fallo de vacío, el producto atrapado gas, la superficie del producto aparece segregación en frío, marcas de flujo, picaduras y otras condiciones sueltas, el impacto de la fuerza de granallado, será grave despellejamiento;
Punto de fallo de la máquina de refrigeración, la presión del agua de refrigeración es insuficiente, el flujo insuficiente, lo que resulta en el sobrecalentamiento de las piezas de concentración de calor del molde, el producto debe ser parte de la contracción de calor y la capa de piel de óxido, el impacto de la fuerza de granallado, el desollado del producto.
4、Factores de ajuste del proceso de fundición a presión
Ajuste de la temperatura del horno de retención es baja (≤ 640 ° C), fácil a la precipitación de silicio, fácil de llenar el líquido de aluminio movilidad del líquido se reduce, fácil de llenar el producto no está lleno, la capa superficial del producto poco profunda de la segregación en frío, las huellas de flujo, marcas de viruela y otras condiciones sueltas, por el impacto de granallado, será un despellejamiento grave;
El ajuste de la presión de colada y la velocidad de llenado es bajo, la resistencia y la dureza del producto disminuyen, el impacto de la fuerza de granallado, el despellejamiento del producto;
Llenado de alta velocidad punto de partida ubicación no está configurado correctamente: 1. De alta velocidad punto de partida posición antes de la taza de fusión de aire estará involucrado en la cavidad, el canal de escape de escape aumenta la carga, el gas es difícil de escape, llenando el final producirá agujeros de aire, el producto superficial agujeros de aire por el impacto de granallado, pelado, 2. De alta velocidad punto de partida posición después de que el aluminio líquido en la cavidad a un ritmo lento, se enfría rápidamente, el producto será la formación de capas intermedias (segregación en frío), suelto, el impacto de la fuerza de granallado, el producto pelado. Pelado del producto;
El tiempo de pulverización es demasiado largo, lo que resulta en baja temperatura del molde (185 ~ 230 ° C) o desequilibrio de calor, el producto aparecerá segregación en frío, marcas de flujo, marcas de viruela y otras condiciones sueltas, por el impacto de la fuerza de granallado, será grave despellejamiento;
Punto de alta presión de agua fría conjunto de tiempo (estándar para el final de la inyección a presión de retardo de 3 ~ 8 segundos) es demasiado largo, lo que resulta en baja temperatura local (185 ~ 230 ° C) o el desequilibrio de calor en el molde, el producto aparecerá segregación en frío, marcas de flujo, marcas de viruela y otras condiciones sueltas, por el impacto de la fuerza de granallado, será grave pelado;
El tiempo de inicio y fin de vacío de la máquina de vacío no está ajustado correctamente, lo que resulta en un fallo de vacío, cavidad de gas atrapado, la capa superficial del producto poco profunda de los agujeros de aire por el impacto de la fuerza de granallado, será grave despellejamiento;
5, factor de rectificado de piezas en bruto de fundición a presión
Los bordes volantes de las piezas brutas de fundición a presión y los materiales múltiples no se limpian y pulen, y la piel volante residual después del granallado - descascarillado;
Las piezas en bruto de fundición lijadas en exceso, la superficie en bruto de la capa densa de lijado, el impacto de la fuerza de granallado, se despellejará.
6, factores granulométricos
El diámetro de los gránulos de granalla comprados es inconsistente y mayor que el tamaño del diámetro establecido en el proceso, lo que resulta en un aumento de la fuerza de granallado, que impacta en el producto a pelar;
7, factores de ajuste de los parámetros del proceso de granallado
Si se ajusta la velocidad de granallado demasiado alta, aumenta la fuerza de impacto, lo que provoca el despellejamiento del producto;
Si el tiempo de granallado es demasiado largo, se produce un raspado por impacto continuo, lo que provoca la descamación de la capa densa del producto y el despellejamiento del producto;
Si el flujo del proyectil de granallado es demasiado grande, aumenta el impacto del raspado, lo que provoca el desprendimiento de la capa densa del producto y su despellejamiento.
8. Factores medioambientales
El entorno del granallado no está ventilado y la temperatura es elevada, lo que provoca el reblandecimiento de la superficie del producto y la descamación del granallado.
Soluciones recomendadas para el shot peening de productos de aleación de aluminio ADC12 moldeados a presión.
1. Medidas de mejora material
La composición química de la materia prima ADC12 adquirida se ajusta en la medida de lo posible a los valores intermedios admisibles;
El material recuperado se convierte en material recuperado secundario mediante un tratamiento graduado, se utiliza con material nuevo y se reduce la proporción de material recuperado.
2, medidas de optimización de la fila de moldes de fundición a presión y del sistema de refrigeración
A través del análisis del flujo del molde, encontrar la esquina muerta de llenado del bebedero, la turbulencia de aire de presión negativa, el final de la intersección y otros malos modos de llenado, optimizar el modo de llenado del bebedero, reducir el reflujo de la esquina muerta, reducir el volumen de aire de presión negativa, aumentar los ajustes de desbordamiento y escape;
A través del análisis de flujo del molde, encontrar la parte de escoria de oxidación, nodo térmico, añadir el dispositivo de refrigeración del punto de molde (mecanismo), de modo que el equilibrio térmico del molde para mejorar.
3, inspección y mantenimiento de la máquina de fundición a presión y el equipo periférico
Presión del sistema de la máquina de fundición a presión;
Fuerza de sujeción en máquinas de fundición a presión - fuerzas equilibradas en las cuatro columnas Göring;
Precisión de la presión, la velocidad y la posición de funcionamiento del punzón del sistema de expulsión de la máquina de fundición a presión;
Compresor de aire, máquina de vacío, enfriador por puntos de alta presión, horno de mantenimiento, máquina de pulverización, etc.
4、Optimización de los parámetros del proceso de fundición a presión
Ajuste de la temperatura del horno de mantenimiento 660°C±10°C
Punto de inicio de alta velocidad de fundición a presión en el punto de inicio de alta velocidad teórica sobre la base de 60 ~ 100 mm de antelación, la prueba de fundición a presión de producción de piezas en bruto enviadas a la granallado para verificar que la mejor posición;
Presión de colada según el espesor medio de la pared del producto valor recomendado para tomar el límite superior (1 ~ 3mm - presión de colada 45 ~ 60MPa; 3 ~ 6mm - presión de colada 60 ~ 80MPa; 6-10mm - presión de colada 80 ~ 110MPa).
5、Esenciales de limpieza y pulido de piezas brutas de fundición a presión actualización estándar.
Die casting blanks limpieza y pulido de las normas, debe ser pulido y limpiado después de la muestra para llevar a la verificación de granallado, sin borde de vuelo pelado, pulido y limpieza de la muestra estándar para ser sellado, liberado, y estrictamente de acuerdo con la muestra para pulir y limpiar los espacios en blanco de fundición a presión.
6, mantenimiento de la granalladora
La granalladora debe cumplir los ajustes de cada parámetro del proceso;
Los datos mostrados en el monitor de la granalladora deben ser precisos.
7, la selección de partículas de granallado y la colocación de nuevas y viejas
Los pellets de granallado deben ser tamizados con un tamiz especial, más grande que el diámetro de los requisitos del proceso de los pellets tamizados por el proveedor de pellets necesita ser molido de nuevo antes de su uso, y la necesidad de ser re-tamizado; la proporción de nuevos pellets añadido no más de 60%.
8. Curado de los parámetros del proceso de granallado
Los parámetros del proceso de granallado deben ser primero de acuerdo con una velocidad relativamente baja y el flujo de proyectil de granallado, el tiempo de granallado es tan corto como sea posible, después de la verificación de disparo de prueba, para confirmar que el producto cumple con la calidad del granallado (sin despellejamiento, sin diferencia de color) con el fin de solidificar los parámetros del proceso.
9, el control de la temperatura del entorno de chorreado
El entorno de chorreado debe mantenerse seco y ventilado, con la temperatura controlada dentro de los 30°C.
Casos de validación experimental
ADC12 Die Casting - Motor Shell Blank Shot Peeling Lista de problemas
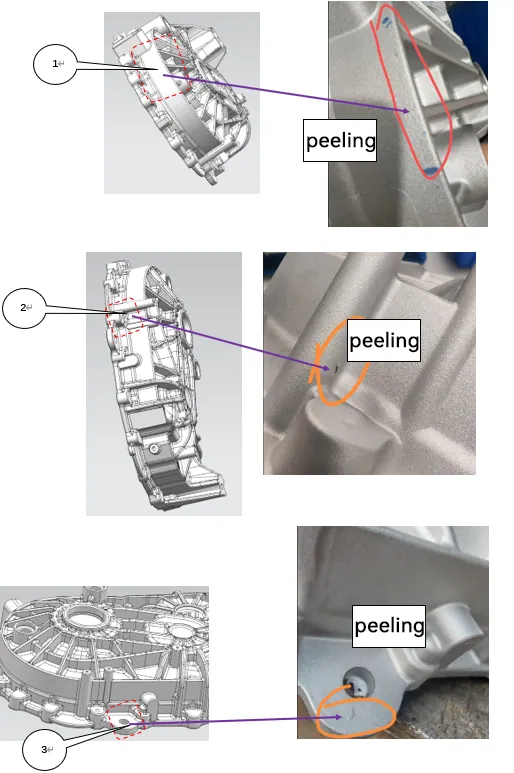
1. Análisis de las causas de cada despellejamiento
La posición de pelado ① ② ③ son finales de llenado, el gas de escape no es suave y la presión de llenado es pequeña es la razón principal, seguida de la temperatura de vertido de aluminio es baja; la posición ② muestra que el tiempo de granallado es demasiado largo, la superficie del fenómeno de arrugas, en esencia, la resistencia y la dureza del producto es desigual y baja (tocho de fundición a presión en las proximidades de pelado con segregación en frío y marcas de flujo).
2、Desarrollar medidas de mejora para cada zona despellejada.
(1) Desatasque el canal de escape y profundícelo 0,05 mm.
(2) Optimización de los parámetros del proceso de fundición a presión ~ dos acumuladores rápidos para añadir nitrógeno (de 11,5MPa a 12MPa), aumento de la presión de almacenamiento de energía (de 13,5MPa a 14,5MPa); aumento del ajuste de la temperatura del horno de mantenimiento (de 645°C a 660°C);
(3) Optimización de los parámetros del proceso de granallado ~ reducción del tiempo de granallado (de 6 minutos a 5 minutos para el granallado de una sola cara en colgaduras expuestas).
3. Medidas de aplicación de las tareas del equipo
(1) Equipo de reparación de moldes para reparar la placa de escape del molde, profundidad de escape de 0,05 mm.
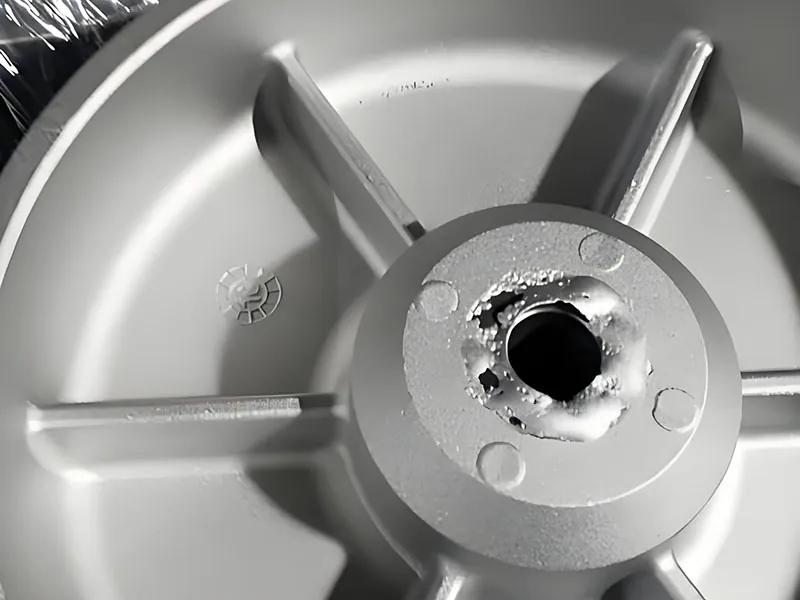
(2) grupo de proceso de fundición a presión de acuerdo con las medidas de mejora para restablecer los parámetros de la segunda presión de almacenamiento rápido de 14.5MPa, la temperatura del horno de mantenimiento se establece en 660 ° C;.
(3) El equipo del proceso de fundición a presión reajusta el tiempo de chorreado a 5 minutos.
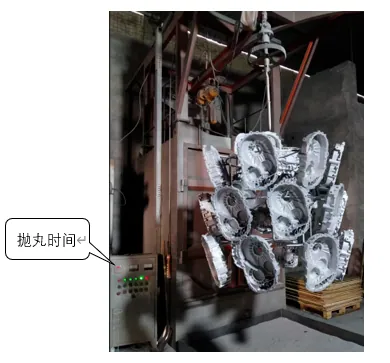
4. Aplicación y ensayo de las medidas
Tras la aplicación de las medidas de mejora, se verificó mediante granallado y la inspección del departamento de calidad la consideró apta, como se muestra en la figura siguiente:
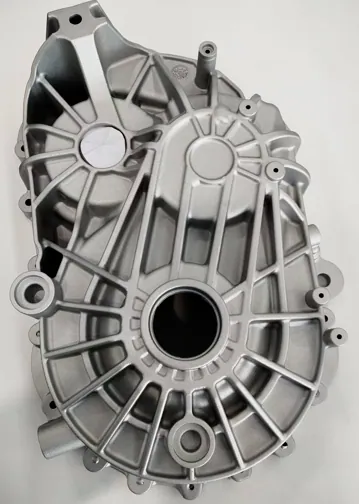
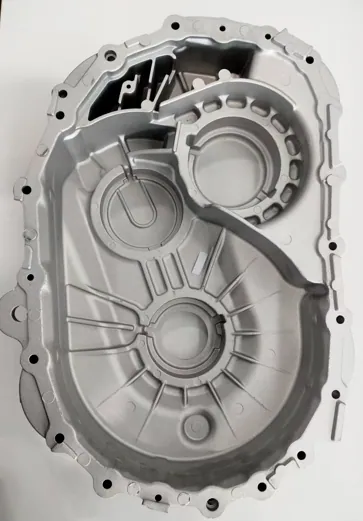
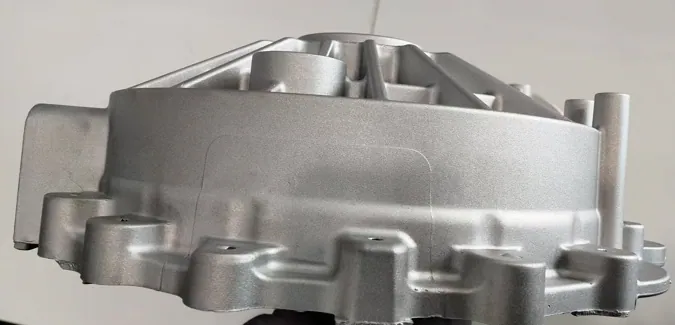
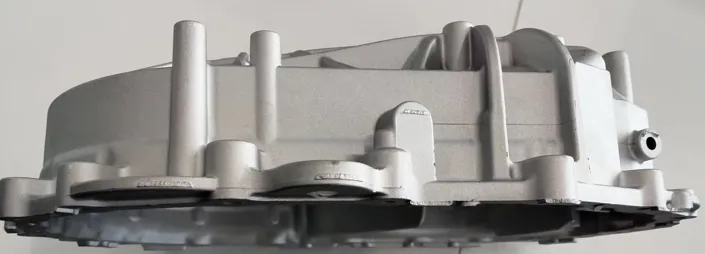
Resumir los resultados de las mejoras
Utilizando el método de eliminación para encontrar la causa exacta de granallado, y luego formular las medidas correspondientes para resolver el problema de granallado de productos de aleación ADC12 a un pequeño costo experimental, este resultado es la búsqueda de la industria de fundición a presión, sino también el objetivo.
Conclusiones y perspectivas
1. Conclusiones del estudio
A través del análisis de la composición química, propiedades físicas, propiedades mecánicas del material de aleación de aluminio ADC12, a través del análisis del proceso de fundición a presión, resumió para asegurar que la resistencia y la dureza de los productos de aleación de aluminio ADC12 condiciones necesarias, a través de la comprensión de los perdigones de granallado, a través del análisis del proceso de granallado, resumió el proceso de granallado en el producto con el impacto y la fuerza de raspado, el análisis exhaustivo para: si ADC12 La resistencia y la dureza de la aleación de aluminio no cumplen las normas, el granallado es fácil de pelar; si las partículas de granallado, el flujo del proyectil de granallado, el tiempo de granallado es demasiado largo, los productos de aleación ADC12 por granallado también son fáciles de pelar, por lo que es necesario un equilibrio entre ambos.
Como se mencionó en el caso anterior, la resistencia y la dureza del producto no estaban a la altura de la norma, y la resistencia y la dureza se mejoraron a través de la mejora, y el tiempo de granallado era demasiado largo, y el tiempo de granallado se acortó a través de la mejora, y finalmente obtuvimos los productos calificados de granallado para la aleación ADC12.
2. Carencias y perspectivas de la investigación
Deficiencias del proceso de investigación: debido al pequeño número de experimentos, y difícil de detectar la fuerza local del producto, por lo que no realmente encontrar la fuerza y la dureza del producto adaptado a la granallado sin desollar el punto crítico (datos), no logró el logro de menor costo de ADC12 aleación de la fuerza del producto y la dureza y el impacto de granallado y la fuerza de raspado de la balanza.
Perspectivas para la dirección de la investigación futura: con el desarrollo de la tecnología de IA de grandes datos, creo que la misma industria ADC12 aleación shot peening problema resuelto más a fondo, gastar menos costos y cosechar más beneficios.
Faqs
- P: ¿Cuáles son las ventajas de rendimiento de fundición de ADC12?
R: Excelente fluidez, fácil de moldear piezas de precisión complejas y fuerte resistencia a la corrosión, adecuada para la producción en serie. - P: ¿Cómo puedo evitar los peelings abrasivos?
R: Se requiere un control exhaustivo de la composición del material, el diseño del escape del molde, los parámetros del proceso de fundición a presión (por ejemplo, temperatura, presión) y los parámetros de granallado. - P: ¿Cómo se establecen los parámetros del proceso de granallado?
A: El material de la granalla (como la granalla de acero inoxidable), la velocidad (50 ~ 70 m / s), el tiempo (5 ~ 15 minutos) deben ajustarse en función de las características de la pieza de trabajo. - P: ¿Cuáles son los defectos más comunes tras el granallado ADC12?
R: Descamación, arrugas, deformación, etc., causadas principalmente por una composición excesiva del material, un mal diseño del molde o unos parámetros de granallado inadecuados. - P: ¿Qué hay que hacer para optimizar los moldes?
R: Mejorar el diseño del bebedero mediante el análisis del flujo del molde, aumentar el canal de escape y el canal de desbordamiento para evitar los agujeros de aire y la segregación en frío. - P: ¿Cómo se ajusta el proceso de fundición a presión?
R: Aumentar la temperatura del horno de mantenimiento (660°C ± 10°C) para optimizar la presión de colada y la velocidad de llenado para garantizar un producto denso. - P: ¿Cómo se seleccionan las granallas de granallado?
R: Utilizar pellets de acero inoxidable con un diámetro de 0,2~0,6 mm, cribar para eliminar las partículas de gran tamaño y mezclar proporcionalmente los pellets nuevos y los viejos. - P: ¿Cuáles son las mejores prácticas para establecer los parámetros de voladura?
R: Los parámetros iniciales se ajustan a baja velocidad, corto tiempo y bajo caudal de granalla, y se ajustan gradualmente hasta que no se produce despellejamiento y se consigue calidad superficial.