Diseño y fabricación de moldes de fundición a presión de aluminio
Fecha:2024-08-05 Categorías:Blog Vistas:2676
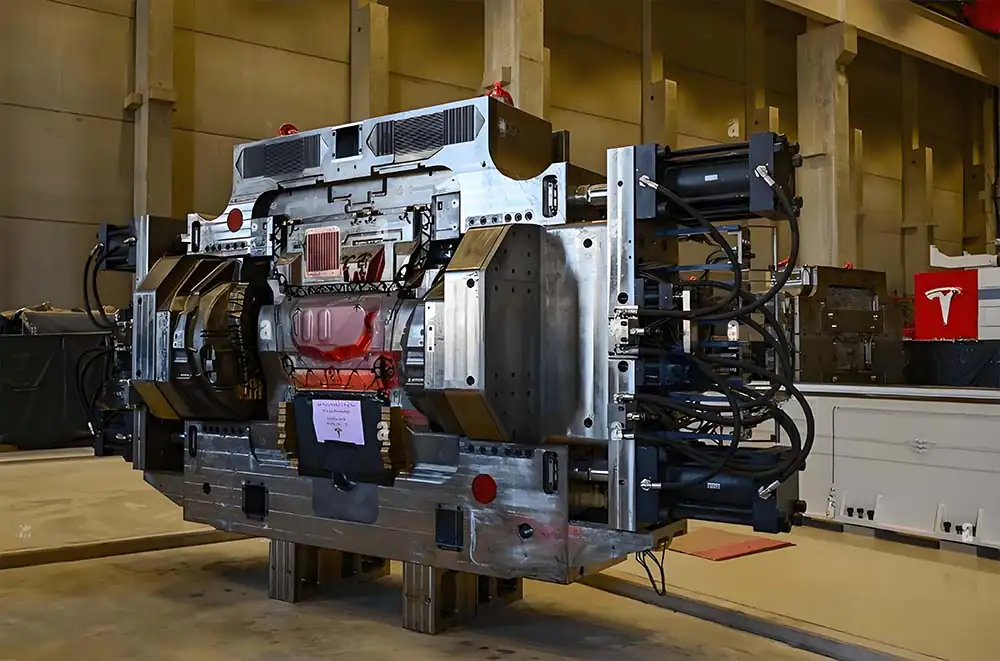
A. Introducción a la tecnología de moldeo por fundición a presión
La fundición a presión se refiere a la fundición a presión, es el uso de la presión de la máquina de fundición a presión de aleación de líquido fundido a una cierta velocidad llena de acuerdo a ciertas partes de la estructura y los requisitos del proceso de diseño y después de la fabricación de precisión de la cavidad del molde, y la aleación de líquido fundido para mantener bajo una cierta presión, bajo la acción de la cavidad del molde, la solidificación de refrigeración y la conformación de una especie de alta eficiencia y alta eficiencia de la tecnología de fundición de precisión.
B. Características y ámbito de aplicación de la tecnología de moldeo por fundición a presión
1, las características de la tecnología de moldeo a presión
Alta presión, alta velocidad es el líquido de fundición a presión o proceso de moldeo de llenado de metal semi-líquido de las dos características principales, sino también la tecnología de moldeo de fundición a presión y otro método de fundición es la diferencia más fundamental.
2、Ámbito de aplicación de la tecnología de moldeo por fundición a presión
La tecnología de fundición a presión es uno de los métodos más avanzados de conformado de metales, y es una forma eficaz de conseguir menos virutas y ninguna viruta. En la actualidad, la aleación utilizada para la fundición a presión ya no se limita únicamente a las aleaciones de zinc, aluminio, magnesio y cobre, sino que se está ampliando gradualmente a la fundición de hierro y acero y otras aleaciones de hierro para producir piezas fundidas a presión.
C. Tendencia de desarrollo de la tecnología de moldeo por fundición a presión
Gracias al uso de la tecnología de moldeo por fundición a presión, las empresas obtienen beneficios económicos evidentes. Futuro del moldeo por fundición a presión
La tecnología avanza en la dirección de:
(1) La tecnología de moldeado por fundición a presión evoluciona hacia la inteligencia.
(2) Investigación y desarrollo de nuevos materiales para la fundición a presión a fin de satisfacer las necesidades del progreso tecnológico industrial.
(3) Investigación y desarrollo de nuevos tipos de equipos de fundición a presión para mejorar el nivel de automatización.
(4) Desarrollo de nuevas tecnologías de detección.
(5) Desarrollo de nuevas tecnologías de fundición a presión y mejora y perfeccionamiento del proceso de fundición a presión.
(6), mejorar la vida del molde de fundición a presión, reducir los costes de producción para resolver el problema de la fundición a presión de metales ferrosos ampliado gradualmente a la utilización de hierro fundido y acero fundido y otras aleaciones de hierro para producir piezas fundidas a presión.
Diseño de moldes de fundición a presión
A. Visión general del diseño de moldes de fundición a presión
- La fundición a presión, el molde de fundición a presión, la máquina de fundición a presión, la aleación de fundición a presión a través de los parámetros del proceso de fundición a presión de la coordinación entrelazada, la finalización común del proceso de fundición a presión del molde de fundición a presión. Molde de fundición a presión en el proceso de producción de fundición a presión es el siguiente:
- ①.Determinar el sistema de vertido, especialmente la posición de la compuerta interior y la dirección de infusión y la posición del sistema de rebose, que en conjunto determinan las condiciones de llenado del metal fundido y la condición de moldeo;
- ②, molde de fundición a presión es la reproducción de la fundición a presión, determina la forma y la precisión de la fundición a presión;
- ③, la calidad de la superficie de conformación del molde afecta directamente a la calidad superficial de la pieza moldeada a presión y al tamaño de la resistencia al desmoldeo.
- ④, después del moldeo por fundición a presión, asegúrese de que las piezas fundidas a presión se desenganchen suavemente del molde de fundición a presión, y después de empujar hacia fuera el cuerpo del molde, no debe haber ningún cambio de
- La aparición de formas, roturas, etc;
- ⑤ La resistencia y rigidez del molde para soportar el impacto de la fuerza de inyección y la velocidad de la compuerta interior en el molde;
- (vi) Controlar y regular el intercambio de calor y el equilibrio térmico del molde durante el proceso de fundición a presión;
- (vii) Maximizar la eficacia de moldeo de la máquina de fundición a presión.
B. Principios básicos del diseño de moldes de fundición a presión
(1), comprender plenamente el uso de fundición a presión y otras partes estructurales de la relación de montaje, y de acuerdo con las características estructurales de fundición a presión, el uso de rendimiento, en el diseño del molde para distinguir entre la principal y secundaria, destacando los puntos clave de la estructura del molde, así como en combinación con el procesamiento del proceso de molde, la elección razonable de la superficie de separación del molde, el número de cavidades y la disposición de la forma de la fundición a presión de la forma de la puesta en marcha de la forma de la parte de la forma de liberación del molde.
(2) Comprender la capacidad real de procesamiento del molde del sitio, como el equipo existente y puede colaborar con el equipo de la unidad, así como el nivel técnico del operador, combinado con el diseño práctico de la forma de la estructura del molde en línea con la capacidad de procesamiento del sitio.
(3), el molde debe adaptarse a la producción de fundición a presión de los diversos requisitos del proceso, elegir de acuerdo con los requisitos del proceso de fundición a presión del sistema de vertido y el sistema de desbordamiento, especialmente la ubicación de la compuerta interior, la velocidad de la compuerta interior y la dirección del flujo de líquido, debe hacer que el metal líquido fluya suavemente y sin problemas, y la descarga ordenada del gas de la cavidad, con el fin de lograr un buen efecto de llenado y evitar la generación de defectos en la fundición a presión.
(4) Bajo la premisa de garantizar una calidad estable de las piezas fundidas a presión y una producción segura, los moldes de fundición a presión deben tener:
①, estructura simple, avanzada y razonable, funcionamiento preciso y fiable, reducir el procedimiento de operación.
②, fácil de manejar, seguro y rápido, fácil de desmontar las piezas de desgaste, fácil mantenimiento, bajo coste de fabricación.
(iii) Mayor eficiencia de fundición a presión, llenado rápido del molde, apertura rápida del molde, mecanismo de desmoldeo flexible y fiable, y alto grado de automatización.
(5), las piezas estructurales del molde deben cumplir los requisitos del proceso de mecanizado y del proceso de tratamiento térmico. La selección adecuada de materiales, especialmente las piezas de moldeo y otras partes en contacto directo con el metal líquido, se debe seleccionar de acero de alta calidad resistente al calor, y el tratamiento de endurecimiento, de modo que tenga suficiente resistencia a la deformación térmica, resistencia a la fatiga y dureza y otras propiedades mecánicas integrales, así como propiedades resistentes a la corrosión.
(6), debe tener muy en cuenta los cambios de temperatura del molde en las partes deslizantes relativas de la precisión de coincidencia provocada por el impacto.
(7) El diseño del molde debe basarse en la viabilidad de una consideración global de la economía.
La estructura general del molde es sencilla y práctica, y el coste global es bajo.
②, se debe seleccionar económico, práctico tamaño ajuste precisión.
(iii) Prestar atención a reducir el consumo de material residual del sistema de fundición.
Además de los requisitos básicos del diseño normal, debe prestarse especial atención:
1. Adoptar una estructura simple razonable y avanzada para que la pieza de trabajo sea precisa y fiable, y que la rigidez de la estructura sea buena, es decir, que el molde tenga suficiente grosor para garantizar que tenga suficiente rigidez para evitar que el molde se deforme y se agriete. También hay que tener en cuenta que el molde sea fácil de desmontar y cambiar, lo que favorece la
Prolongar la vida útil del molde;
2. Las piezas del molde deben cumplir los requisitos del proceso de mecanizado y del proceso de tratamiento térmico. Trate de evitar o reducir las esquinas afiladas y paredes delgadas para facilitar el tratamiento térmico posterior y evitar la concentración de tensiones. Si la estructura no puede evitar las esquinas afiladas, debe estar en el desbaste para reservar suficiente ángulo R, el tratamiento térmico después del mecanizado en su lugar para evitar el riesgo de agrietamiento de tratamiento térmico.
3. Grandemolde de fundición a presión(El área proyectada de la superficie de separación es superior a 1 metro cuadrado), debe utilizarse un sistema de guiado de montante guía cuadrado para evitar que se reduzca la precisión de guiado debido a la gran diferencia de dilatación térmica entre los moldes móvil y fijo;
4. Para el diseño de moldes de fundición a presión grandes y complejos, el sistema de vertido, el sistema de escape y el sistema de refrigeración, lo mejor es realizar un análisis de flujo y un análisis de balance térmico. Esta disposición del sistema de canal (bebedero recto, bebedero transversal, compuerta interior) y la ubicación del sistema de precalentamiento a temperatura constante, el tamaño del ángulo, la cantidad, etc. harán un diseño razonable; Como todos sabemos, el sistema de vertido es el metal líquido de la cámara de presión a la cavidad, está estrechamente relacionado con el metal líquido en las partes de la cavidad, la dirección, el estado de flujo, y puede ajustar la velocidad de llenado, el tiempo de llenado, la temperatura de la cavidad y otras condiciones de llenado. En la producción de fundición a presión, el sistema de vertido en la calidad de fundición a presión, la eficiencia de la operación de fundición a presión, la vida del molde (alta temperatura, alta presión, metal líquido de alta velocidad en la pared de la cavidad del molde, corrosión, etc.), el borde de corte de fundición a presión y la limpieza y así sucesivamente también tiene un impacto significativo, se puede ver el sistema de vertido.
El diseño y su importancia;
5. Consideraciones sobre el diseño de la puerta interior:
El líquido metálico de alta temperatura que entra en la cavidad desde la compuerta interior no debe entrar positivamente en la pared y el núcleo del modelo fijo dinámico, para evitar que la cavidad sufra erosión temprana, adherencia del molde y agrietamiento, etc.; cuando se adopta la compuerta interior de múltiples filamentos, se debe tener en cuenta para evitar los defectos de vórtice, envoltura de gas y escorificación oxidativa, etc., que son causados por el impacto del metal líquido en la cavidad desde unas pocas vías de convergencia; la selección del grosor de la compuerta interior se formula generalmente de acuerdo con los datos empíricos, y se recomienda elegir uno más grande bajo la condición de llenado del molde tanto como sea posible para evitar la erosión temprana, la adherencia del molde, la picadura y el agrietamiento causados por la excesiva velocidad de inyección a presión. Bajo la condición de tipo de llenado, trate de elegir uno más grande para evitar el impacto de la compresión demasiado grande y la velocidad de inyección, que causará la erosión, la adherencia del molde, picaduras y grietas en la etapa inicial del molde;
6. Diseño de tanques de rebose y ventilación:
La función del canal de rebose es acumular el líquido metálico frío y el líquido metálico envuelto con gas que entran primero en la cavidad, así como regular la temperatura de cada parte del molde para mejorar el equilibrio térmico del molde, lo que favorece la prolongación de la vida útil del molde. Generalmente situado al final del proceso de metal líquido, establecer un tanque de desbordamiento adecuado puede mejorar las condiciones de llenado, mejorar la calidad de las piezas fundidas. La ranura de escape se utiliza para descargar el aire y el gas de volatilización de la pintura de la cavidad, cuya ubicación está relacionada con la ubicación de la compuerta interior y la estructura del producto. Con el fin de hacer que la inyección de gas de la cavidad en la medida de lo posible por la fundición a presión de descarga de metal líquido, se establecerá en la última parte de la ranura de escape de llenado de metal líquido. El tanque de escape se combina generalmente con el tanque de desbordamiento, dispuesto en el extremo posterior del tanque de desbordamiento, con el fin de fortalecer el desbordamiento y el efecto de escape.
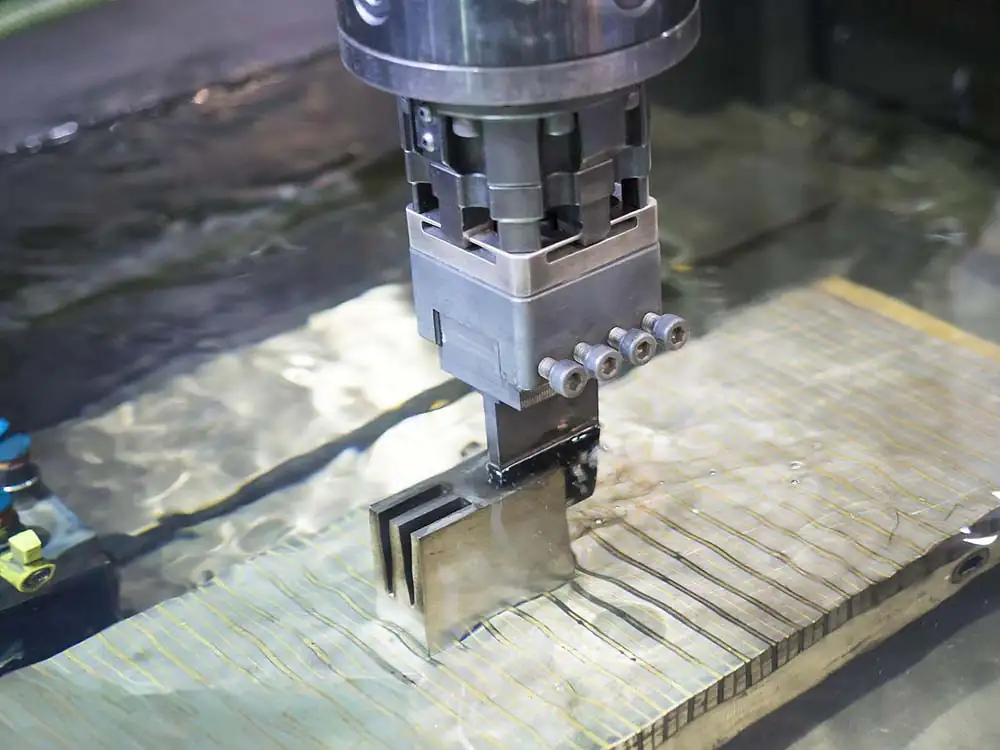
Efecto del mecanizado en el fallo del molde
Como todos sabemos, los moldes de fundición a presión tienen un ciclo de fabricación largo y un mecanizado complejo, que implica torneado, rectificado, fresado, taladrado y cepillado.mecanizadoy mecanizado por descarga eléctrica (corte por hilo, EDM) y otros procesos. Su calidad de procesamiento, especialmente la calidad de procesamiento de la superficie en el proceso de fabricación del molde y el uso posterior del proceso, afectará significativamente a la resistencia a la fractura del molde, resistencia a la fatiga, resistencia a la fatiga térmica y resistencia al desgaste, resistencia a la corrosión y así sucesivamente. Un ligero error en el procesamiento puede provocar el fallo prematuro del molde. Por ejemplo, el agrietamiento y el agrietamiento térmico sonaluminioUn fenómeno de fallo común en los moldes de fundición a presión, que está causado por la fatiga térmica, la tensión, la baja resistencia y la rugosidad de la superficie del molde.
1、 La influencia del proceso de corte
Módulo en el proceso de corte de mecanizado, debido a la destrucción del equilibrio original del sustrato de la pieza de trabajo, se producirá el estrés, estas tensiones internas reducir la resistencia total de la superficie del módulo, lo que resulta en la falta de resistencia a la fatiga térmica, lo que conduce a la fisuración o agrietamiento en las esquinas y la transición de arco de radio pequeño. Por lo tanto, las esquinas afiladas deben evitarse en la medida de lo posible. Las esquinas afiladas y los cortes de mecanizado pueden causar significativamente la concentración de tensiones, a menos que existan requisitos especiales, de lo contrario, se deben evitar las esquinas afiladas y las esquinas del arco de radio de curvatura totalmente ampliado, el propósito es evitar o reducir la concentración de tensiones. Por ejemplo: aumentar el radio de arco R de 1 mm a 5 mm, la tensión interna máxima se reduce en aproximadamente 40%, lo que mejora en gran medida la tenacidad del molde. Cuando el radio del arco del módulo de 2mm a 20mm, la tenacidad al impacto puede incrementarse en 4 veces. Del mismo modo, el tamaño de la rugosidad de la superficie del molde en la vida del molde también tiene un mayor impacto. Por ejemplo, la existencia de marcas evidentes de cuchillas, grietas, cortes, etc., estos defectos de procesamiento provocarán la concentración de tensiones, convirtiéndose en la causa raíz de las grietas. Por lo tanto, para garantizar que la rugosidad de la superficie de los requisitos del molde, superficie de la cavidad debe ser molido y pulido para eliminar las marcas de corte y otros defectos. Proceso de perforación de orificios de agua de refrigeración, si la perforación de dos vías, desalineación, causará agrietamiento temprano en el lugar, conducir a la fuga de agua. Después de la forja y el recocido del embrión de molde, o embrión de molde, núcleo, después del procesamiento en el horno de aire de calentamiento y enfriamiento, por lo general hay un cierto espesor de la capa de descarburación, el procesamiento de corte debe ser descarburación capa todos eliminados. De lo contrario, la capa de descarburación residual en el uso del molde, reducirá la resistencia a la fatiga térmica de la superficie del molde, resultando en el agrietamiento de la pieza.
2. Efecto del proceso de molienda:
Tras el tratamiento térmico de los moldes de fundición a presión, pueden producirse los siguientes problemas en el rectificado (incluido el rectificado de sujeción y de muela):
A. Se produce agrietamiento o fisuración, que se debe a que la muela abrasiva es demasiado dura, la cantidad de alimentación es grande, la velocidad de rectificado es rápida, la tensión de rectificado es demasiado grande, la refrigeración es insuficiente o el refrigerante no se ha seleccionado correctamente. Debido a la dureza de la muela abrasiva, el calor de fricción generado por la tensión de tracción es mayor que la tenacidad a la fractura del material, se producirá el agrietamiento;
B. Quemaduras por rectificado y reblandecimiento de la superficie. Superficie ablandada en contacto con el metal fundido de fundición a presión, debido a su resistencia relativamente baja, y la resistencia a la fatiga térmica también es insuficiente, fácilmente conducir a la formación de grietas, erosión y picaduras.
C, tensión de rectificado. Moldeo de la superficie del molde hay tensión de molienda, la reducción de la fuerza de la superficie del molde y la resistencia a la fatiga térmica, dará lugar a grietas o fisuras en el molde tipo bit esquina y la transición de arco pequeño R, puede ser inferior a la temperatura de revenido de 20 ~ 30 ℃ temperatura para un tratamiento de revenido, para lograr el propósito de eliminar el estrés.
3. Efectos del tratamiento de los vertidos
A. Produce una capa endurecida de color blanco brillante
El mecanizado por electroerosión (EDM y WEDM) de las cavidades de los moldes se suele realizar después de enfriar el molde para garantizar su precisión. Durante el proceso de mecanizado, debido a las altas temperaturas (hasta miles de grados Celsius, o incluso decenas de miles de grados Celsius) generadas instantáneamente por una sola descarga, el metal de la superficie del molde se funde, vaporiza y evapora rápidamente. La aplicación de refrigerante de enfriamiento rápido da como resultado, desde la superficie en orden: capa de re-solidificación (espesor de hasta 0,2 mm cuando se golpea en bruto, golpe fino de hasta 0,01 mm más o menos), capa endurecida re-enfriada (su espesor es generalmente dentro de 0,05 mm, el lado más superficial de la organización de enfriamiento sobrecalentado, frágil y de alta sensibilidad a las grietas), capa ablandada de revenido a alta temperatura y la organización normal de la matriz. Dentro de esta capa endurecida, especialmente en la capa de re-solidificación produce muchas grietas finas, grietas e incluso se extienden a la capa endurecida re-templado (a menudo referido como la capa blanca brillante o capa metamórfica). Su presencia puede provocar accidentes como el agrietamiento o cuarteamiento prematuro del molde. (Por ejemplo, esto suele ocurrir con los insertos de moldes como las carcasas de embrague y los cuerpos de las cajas de cambios de los automóviles). Por lo tanto, es necesario eliminar completamente esta capa de deformación mediante esmerilado manual, esmerilado químico o esmerilado electrolítico.
B, EDM rugosidad de la superficie y resistencia a la fatiga de la relación entre el mecanizado de descarga eléctrica de los parámetros de calibre eléctrico, materiales de electrodos, en comparación con el mecanizado, su resistencia a la fatiga es mucho menor. Rough golpe, en el ancho de pulso de 1050μ s cuando su resistencia a la fatiga es de aproximadamente 60% para el mecanizado.
C. Medidas de protección
Independientemente de la profundidad de la capa blanca del proceso de descarga, para las malas condiciones de trabajo de los moldes de fundición a presión, esta capa blanca debe ser eliminada (lijado); ajustar los parámetros del proceso de descarga, preferiblemente el proceso de descarga de dos etapas gruesa y fina en la medida de lo posible para utilizar una alta frecuencia, los parámetros del proceso de corriente pequeña, para controlar la capa blanca de 0,01 mm más o menos; el proceso de descarga, además de lijar para eliminar la capa blanca, sino que también debe llevarse a cabo inmediatamente durante un período suficientemente largo de tiempo para el secundario. La temperatura de revenido suele ser superior a la temperatura de revenido final. La temperatura de revenido suele ser inferior a la temperatura de revenido final de 20 ~ 30 ℃ o 30 ~ 50 ℃, con el fin de eliminar por completo la tensión de tracción en la superficie, mejorar la estabilidad de revenido de la capa retemplada, reducir la fragilidad.
En general, los defectos de corte, rectificado y mecanizado de descarga eléctrica en la superficie del molde reducirá la calidad de la superficie del molde causando concentración de tensiones. Para el molde de fundición a presión en condiciones de trabajo de alta temperatura y alta presión, llevar el papel de la alternancia de la tensión térmica y la alternancia de la tensión mecánica, la superficie del molde es fácil de producir grietas y agrietamiento y la corrosión, hacer que el fallo prematuro del molde. (Por supuesto, también se ven afectados por la calidad del acero, el diseño, el tratamiento térmico, el uso, el mantenimiento y muchos otros factores). Todos ellos merecen gran atención por parte de los ingenieros de diseño de moldes, artesanos técnicos, operarios de producción e inspectores de calidad. Presentar requisitos razonables de calidad de la superficie del molde, tratar de evitar las esquinas afiladas de las piezas y la conexión de transición de arco de radio pequeño y las marcas obvias de cuchillo, controlar el mecanizado por descarga eléctrica de los parámetros de calibre eléctrico, para eliminar la capa blanca y así sucesivamente. Para desarrollar la norma de aceptación de rugosidad de corte, mecanizado de descarga eléctrica y rectificado de sujeción, y aplicar estrictamente el sistema de inspección para cada proceso. Esto evitará eficazmente el fallo prematuro del molde causado por un procesamiento inadecuado y mejorará la vida útil del molde.
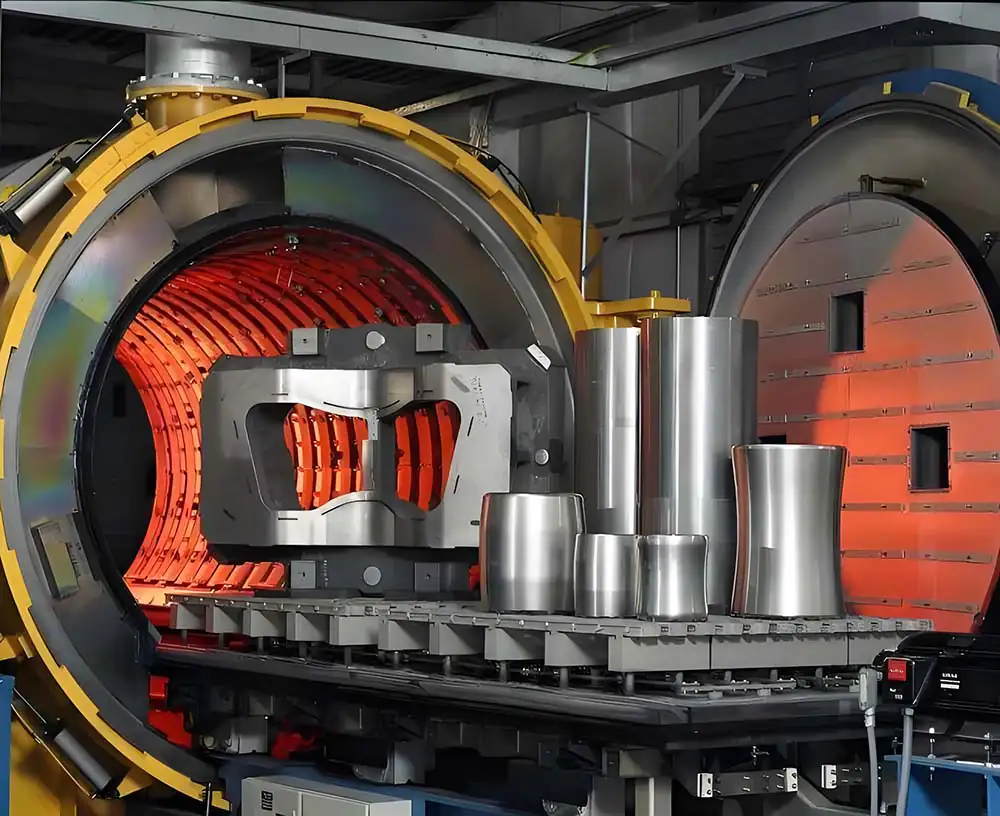
Precauciones para el tratamiento térmico de los moldes de fundición a presión:
La influencia del tratamiento térmico en la vida útil de los moldes de fundición a presión es grande, de acuerdo con la información pertinente, debido a un tratamiento térmico inadecuado, causado por el fallo prematuro de los moldes de fundición a presión representó todo el accidente de los moldes de fundición a presión de 44% más o menos. Acero de enfriamiento de la tensión producida, de hecho, es el proceso de enfriamiento de la tensión térmica y el cambio de fase cuando la superposición de estrés organizacional de los resultados, el acero de enfriamiento en estado de alta tensión baja tenacidad, con alta dureza y resistencia, más frágil, de hecho, no se puede utilizar. Y el estrés de enfriamiento es la causa de la deformación de grietas, y conducir a la resistencia a la fatiga de impacto reducción de la tenacidad. Por esta razón, el acero debe ser templado después del enfriamiento rápido para eliminar el estrés. Estabilizar la organización y mejorar la tenacidad.
1、 Tratamiento de recocido de alivio de tensión antes del enfriamiento del molde
Como resultado del mecanizado del molde para producir una gran tensión interna, con el fin de evitar que el tratamiento térmico con la generación de iteración tensión interna, causando la deformación y agrietamiento del molde, se requiere que el molde en el mecanizado, enfriamiento antes de un tratamiento de recocido desestresante. Temperatura de recocido 600 ~ 650 ℃, el tiempo de aislamiento de acuerdo con el espesor de cada 25 mm, el aislamiento de 1 hora de cálculo, el aislamiento con el horno de enfriamiento a 300 ℃ (también en frío a 500 ℃) fuera de la refrigeración por aire.
2, el desarrollo de un proceso de tratamiento térmico razonable
A. El proceso de temple adopta un precalentamiento de varias etapas y un control estricto de la tasa de aumento de la temperatura El acero tipo 1.2343/44 pertenece al acero de alta aleación de carbono medio, y su conductividad térmica es más pobre que la del acero de baja aleación. Por lo tanto, el calentamiento de temple debe adoptar un precalentamiento de varias etapas (de 2 a 3 etapas) para 300°C, 650°C y 850°C. El propósito es hacer que las temperaturas del corazón de la pieza y de la superficie tiendan a equilibrarse, para reducir las tensiones térmicas derivadas de la diferencia de temperatura. Al mismo tiempo su velocidad de calentamiento debe ser implementado principio de calentamiento lento (100 a 200 ℃ / h), con el fin de reducir el estrés térmico generado durante el proceso de calentamiento. En la etapa de calentamiento a alta temperatura se puede utilizar una velocidad de calentamiento más rápida (10 ~ 15 ℃ / h) para acortar el tiempo de calentamiento a alta temperatura para evitar el engrosamiento del grano;
B. Prevención del sobrecalentamiento de las piezas de trabajo
Si la temperatura de la etapa de calentamiento supera la temperatura normal de enfriamiento (incluido el fallo del instrumento o la colocación de la pieza cerca del elemento calefactor, etc. causados por), con el aumento de la temperatura de enfriamiento, la extensión del tiempo de mantenimiento, los granos se engrosan en general, aumenta la organización de la fragilidad, el aumento de la austenita residual, la transformación de carburos globulares en carburos poligonales, y aparece un tejido en forma de malla, el molde es propenso a agrietarse en el proceso de uso;
C. Selección del medio calefactor y del medio refrigerante para el enfriamiento
El mundo de hoy para moldes de precisión grandes y complejos y más uso de vacío o atmósfera protectora de tratamiento térmico para evitar la oxidación de la superficie del molde descarburización, especialmente de vacío de alta presión enfriado por aire proceso de enfriamiento rápido es ampliamente utilizado. Sin embargo, debe tenerse en cuenta que la tasa de enfriamiento de aire no puede ser demasiado baja, que requiere el tamaño de la presión de nitrógeno es suficiente, por lo general requiere que la pieza de trabajo de la temperatura de temple (1020 ~ 1050 ℃) en frío a 538 ℃ en el proceso de su tasa de enfriamiento de la superficie de mayor o igual a 28 ℃ / min, también hay un requisito para la tasa de enfriamiento de la pieza de trabajo de mayor o igual al corazón de 28 ℃ / min. Si el rango de temperatura, la velocidad de enfriamiento es demasiado lento, el enfriamiento de su microestructura tendrá carburos u otros productos de transformación precipitados a lo largo de los límites de grano, reduciendo así la tenacidad del acero, el aumento de la fragilidad, grietas prematuras en el uso del proceso. Además de las condiciones, para grandes moldes de fundición a presión particularmente complejos se puede utilizar el temple isotérmico graduado, puede reducir eficazmente la deformación del molde y evitar el agrietamiento.
D. Proceso de templado
Templar a tiempo después del enfriamiento rápido. La pieza de trabajo de enfriamiento rápido después de enfriar a 90 ~ 70 ℃ debe ser templado inmediatamente, porque la pieza de trabajo después de enfriamiento rápido se encuentra en alta tensión, bajo estado de plasticidad, fácil de causar grietas; Templado a ser suficiente. Molde de fundición a presión complejo grande después de enfriamiento rápido, por lo general tres veces templado, cada tiempo de templado de acuerdo con el espesor efectivo de la pieza de trabajo cada 25 mm de aislamiento cálculo de 1 hora, pero no menos de 4 horas. El propósito es reducir la tensión de transformación organizativa y estabilizar el tamaño.
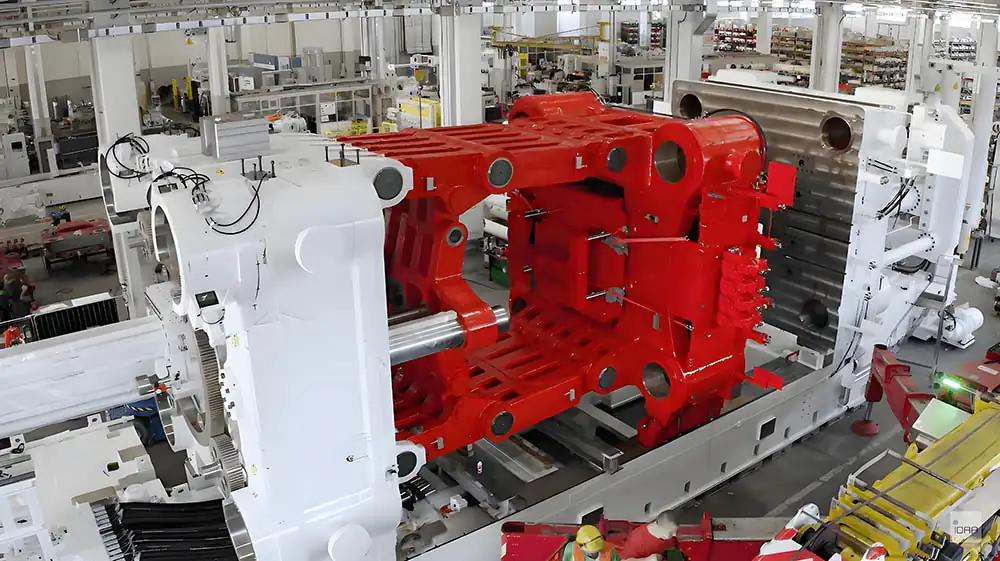
Producción y mantenimiento de moldes de fundición a presión
1、 Buen precalentamiento del molde
Montaje del molde después de la prueba o la producción normal, debe precalentar el molde y la temperatura del molde debe ser uniforme. La temperatura de precalentamiento del molde de fundición a presión de aleación de aluminio-magnesio se recomienda en 250 ~ 320 ℃, el mejor uso de precalentamiento de la máquina de temperatura del molde; precalentamiento del molde a 300 ℃, su resistencia al impacto mejorar muy rápidamente, pero cuando la temperatura del molde es inferior a 200 ℃, la resistencia al impacto del material se reduce mucho aumento de la fragilidad; después de un buen precalentamiento del molde, su conductividad térmica es mayor que el molde no es bueno precalentamiento del molde está cerca de 20%; temperatura de vertido del molde y el molde. temperatura de la superficie (temperatura de precalentamiento) cuanto mayor sea la diferencia, mayor será el estrés térmico, más probable será que se produzca fatiga térmica y grietas. Información editorial de la Asociación Japonesa de Fundición a Presión, la temperatura del molde de 250 ℃ a 350 ℃, es decir, la temperatura de vertido y la diferencia de temperatura de la superficie del molde reducir 100 ℃, entonces la vida del molde se puede aumentar casi 10 veces.
2、 Formular el proceso de fundición correcto
La temperatura de vertido debe ser razonable, no demasiado alta. De lo contrario, la temperatura de vertido es demasiado alta, aunque la fluidez es mejor, pero el tiempo de condensación de la fundición es largo, fácil de producir agujeros de contracción, agujeros de aire, fácil de reducir la dureza de la superficie del molde, hay un molde pegajoso, producir grietas. Ajustar la fuerza de apriete de la máquina de fundición a presión, para que la fuerza del molde sea uniforme. Seleccionar (o ajustar) correctamente la velocidad de llenado y la presión de llenado. Una velocidad de llenado (velocidad de expulsión) demasiado alta aumentará la superficie de la cavidad debido a la erosión y la posibilidad de daño del molde pegajoso, una velocidad de llenado demasiado baja, aunque propicia la descarga de gas, pero hará que las propiedades mecánicas de la fundición disminuyan y la calidad de la superficie sea mala. Del mismo modo, el aumento de la presión de llenado también aumentará la velocidad de llenado de la boquilla. En resumen, ajustar un valor moderado.
3、 Cierre el agua de refrigeración durante la producción
Cuando se interrumpe la operación de colada de la fundición a presión, recuerde cerrar el agua de refrigeración, para no hacer que la temperatura del molde baje demasiado, de modo que al reanudar la operación de colada, afecte a la calidad de las piezas fundidas y a la vida útil del molde.
4、 Selección del agente desmoldeante adecuado y del método de pulverización correcto
Fundición a presión para ser rociado en la superficie de la cavidad de contacto con la solución de metal, su papel principal es evitar la adhesión de líquido de metal en la superficie de la cavidad y asegurar que la separación de fundición y la pared, prolongar la vida útil del molde. El agente de desmoldeo tiene agua, aceite, en los últimos años también se ha desarrollado polvo y agente de desmoldeo granular. Requisitos: el agente de desmoldeo no puede tener un efecto adverso en la calidad de la superficie de la colada, no se produce olor a humo, y no debe dejar residuos. La concentración del agente de desmoldeo debe ser adecuada, agitando a menudo, nunca dejar que se precipite, de lo contrario la cavidad del molde será extremadamente fría causada por el agrietamiento por fatiga térmica. La cantidad de pulverización debe ser menor, la pulverización debe ser uniforme, la formación de la película debe ser fina. Una pulverización demasiado gruesa provocará piezas fundidas sueltas, escoria, ampollas, porosidad y otros defectos. Si el efecto de pulverización del agente desmoldeante a base de agua no es bueno, debe elegir agente desmoldeante a base de aceite o agente desmoldeante a base de polvo. Sin embargo, debe utilizarse al vacío. El desmoldeo es rápido, de alta productividad, buena calidad, y el molde produce menos estrés térmico, lo que favorece la prolongación de la vida útil del molde.
5. Asegurarse de que la calidad de la aleación de aluminio fundido garantiza la composición de la aleación de aluminio;
La fusión de aleaciones de aluminio y el tanque de retención deben estar separados. La fusión central debe controlar estrictamente el contenido de gases tales como óxidos, evitar absolutamente la chatarra y el material de vuelta al horno añadido directamente al horno de mantenimiento, de lo contrario contaminará la solución de metal, no sólo reducirá seriamente la calidad de las piezas fundidas, sino que también será fácil causar adherencia y corrosión del molde. El contenido de Fe de la solución de aleación de aluminio debe controlarse entre 0,7 ~ 1,3%, si es inferior a 0,7% es fácil que se produzca el fenómeno de adherencia al molde, si es superior a 1,3% se formará un punto duro del compuesto metálico, lo que provocará la erosión.
6、 Establecer un buen sistema de mantenimiento del molde, para que éste se encuentre en buenas condiciones de funcionamiento:
A, la limpieza oportuna y la limpieza del molde, eliminar los residuos de la cavidad y el borde de vuelo; B, la sustitución o reparación de las piezas dañadas; C, el tratamiento regular de alivio de tensión del molde: el primer tratamiento de alivio de tensión para la puesta en marcha inicial del molde para utilizar alrededor de 2000 ~ 5000 moldes; el segundo tratamiento de alivio de tensión para el uso de 10.000 ~ 20.000 moldes; el resto del intervalo entre cada tratamiento de alivio de tensión, lo mismo que lo anterior, el máximo no puede exceder de 15.000 moldes. D. Después de utilizar el molde durante un período de tiempo, la dureza de la superficie del molde se reducirá y aparecerá el fenómeno de moldes pegajosos, la superficie del molde debe ser rectificada lisa, y se debe realizar un tratamiento de nitruración con un espesor de capa de nitruración de 0,08-0,12mm, o tratamiento compuesto de nitruración + oxidación, lo que mejorará eficazmente la vida útil del molde.