La technologie du moulage sous pression : un processus de fabrication clé pour transformer les visions en réalité
Temps de publication:2024-12-24 Trier par:Le blog Nombre de vues:625
Dans la fabrication moderne, le processus de moulage sous pression est considéré comme un moyen important de fabriquer des pièces métalliques de précision. Il est capable de produire des pièces métalliques de forme complexe en injectant du métal en fusion dans des moules de précision sous haute pression, et est largement utilisé dans l'automobile, l'électronique et d'autres domaines, soutenant le développement technologique de plusieurs industries de pointe. Cet article propose une analyse approfondie des processus de base, de la sélection des matériaux et des applications du processus de moulage sous pression, ainsi que de la manière dont ce processus permet d'atteindre l'innovation et l'excellence dans le domaine de la fabrication.
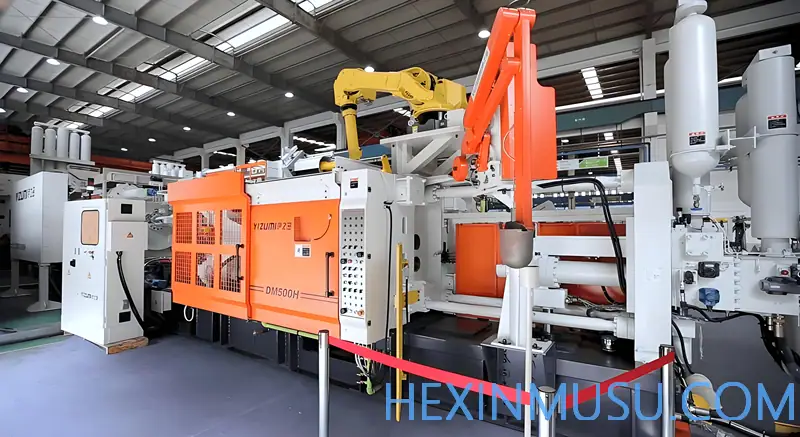
Qu'est-ce que le moulage sous pression ?
Le moulage sous pression est une méthode efficace et précise de moulage des métaux qui utilise des moules réutilisables pour produire des pièces métalliques de forme complexe. Contrairement aux procédés de moulage traditionnels, le moulage sous pression injecte du métal en fusion dans le moule sous haute pression. Il est particulièrement adapté à la production en grande série, offrant une grande précision, une répétabilité et une excellente finition de surface.
Le procédé de moulage sous pression a d'abord été utilisé dans l'industrie de l'imprimerie, mais son potentiel d'utilisation s'est rapidement étendu à un certain nombre de domaines, notamment l'automobile, l'aérospatiale et l'électronique. Aujourd'hui, le moulage sous pression utilise principalement des métaux légers tels que l'aluminium, le zinc et le magnésium pour répondre aux besoins de fabrication d'une large gamme de produits, des petits composants complexes aux pièces automobiles importantes. L'avantage principal du moulage sous pression est sa capacité à créer des pièces avec des tolérances extrêmement serrées et un besoin réduit d'usinage ultérieur, ce qui en fait une technologie indispensable dans la fabrication moderne.
Processus de moulage sous pression
Le processus de production du moulage sous pression peut être divisé en plusieurs étapes clés :
- Préparation du moule
Les moules sont la base du processus de moulage sous pression, et les types de moules les plus courants sont les moules à cavité unique, les moules à cavités multiples et les moules combinés. La conception du moule doit tenir compte de la complexité de la pièce et de l'échelle de production, et le moule doit être nettoyé et préchauffé avant utilisation pour éviter les fissures et les défauts thermiques. - processus d'injection
Au cours du processus d'injection, le métal en fusion est fondu et injecté dans le moule dans différents systèmes. Dans le cas du système à chambre chaude, la fusion a lieu à l'intérieur de la machine de coulée, tandis que le système à chambre froide déverse le métal en fusion dans la chambre froide où il est injecté dans le moule sous l'effet de la pression. - Refroidissement et solidification
Le métal en fusion est refroidi et solidifié dans un moule pour former la pièce finale. Le processus de refroidissement nécessite une pression contrôlée afin d'éviter que la pièce ne présente des défauts dus à la contraction. - éjecter (d'un avion)
Une fois le métal entièrement solidifié, le moule est ouvert et l'éjecteur de la machine pousse la pièce à l'extérieur. - Découpage et post-traitement
Pour garantir la qualité de la pièce, il faut éliminer l'excès de matière et les bavures. Si nécessaire, la précision de la pièce peut être encore améliorée par des méthodes de post-traitement telles que la rectification.
Types de moulage sous pression
En fonction du processus de fusion et d'injection, le processus de moulage sous pression peut être divisé en deux types principaux : le moulage sous pression à chambre chaude et le moulage sous pression à chambre froide :
- moulage sous pression en cellule chaude (métallurgie)
Convient pour les métaux à bas point de fusion tels que le zinc et certains autres métaux.aluminium. Le procédé utilise un piston pneumatique pour injecter le métal dans le moule par l'intermédiaire d'un réservoir de métal en fusion relié à une machine de moulage sous pression. Il est efficace, rapide et adapté à la production en grande quantité de petites pièces, couramment utilisées dans la production d'électronique grand public. - moulage sous pression en chambre froide (métallurgie)
Utilisé pour les métaux à point de fusion élevé tels que les alliages d'aluminium et de cuivre. Dans le cas du moulage sous pression en chambre froide, le métal en fusion est d'abord versé dans une chambre froide, puis injecté dans le moule par l'intermédiaire d'un piston. Ce procédé convient aux pièces nécessitant une grande solidité et une grande résistance à la chaleur et est largement utilisé dans les applications automobiles et aérospatiales.
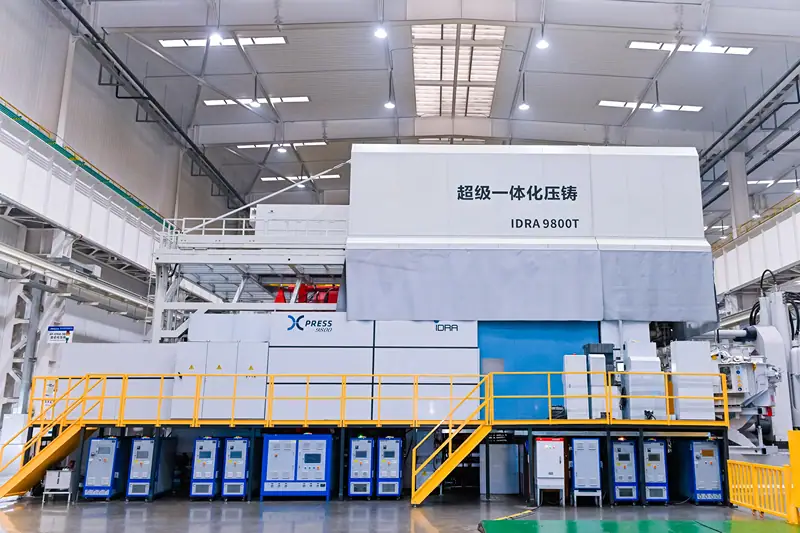
Variantes et innovations en matière de moulage sous pression
Au fur et à mesure que la technologie évolue, le processus de moulage sous pression a connu de nombreuses variantes et innovations pour répondre aux différents besoins de l'industrie. C'est le cas, par exemple :
- moulage sous pression par gravitéLes moules de précision : Le métal en fusion est injecté dans le moule par gravité, ce qui permet de produire de grandes quantités de pièces moulées de précision.
- moulage sous pressionRemplissage de métal par basse ou haute pression, adapté à la production de pièces de haute précision, telles que les pièces automobiles et aérospatiales.
- moulage sous videLes produits de l'industrie de l'emballage : Améliorer la qualité de la surface et la précision des dimensions en créant un environnement sous vide qui réduit la rétention d'air et qui convient aux produits haut de gamme.
- moulage par extrusionIl peut améliorer les propriétés mécaniques et la précision des pièces et est couramment utilisé dans les pièces automobiles.
- Moulage sous pression semi-solideProduction de pièces à géométrie complexe avec une précision et une résistance accrues grâce à des températures de coulée spécifiques.
Comparaison des avantages et des inconvénients du moulage sous pression
Les avantages du moulage sous pression des métaux, un processus de fabrication largement utilisé dans la production industrielle, l'ont rendu important dans la production de masse. Cependant, il présente également certaines limites qui peuvent affecter son utilisation dans certains scénarios d'application. Les principaux avantages et inconvénients du moulage sous pression et leurs causes sont analysés ci-dessous :
Avantages de la coulée sous pression
- Excellente précision dimensionnelle
Le moulage sous pression est capable de produire des pièces d'une grande précision dimensionnelle et est particulièrement adapté aux applications exigeant des tolérances serrées. La précision dépend de la conception du moule et du processus de fabrication, et une plus grande précision dimensionnelle peut être obtenue en particulier lorsque les moules sont fabriqués à l'aide de machines CNC de haute précision, telles que les machines CNC à 5 axes. En outre, l'utilisation de variantes de processus telles que le moulage sous pression (LPDC) et le moulage par gravité permet de remplir les moules avec précision, augmentant ainsi la précision de la pièce. - Géométrie complexe
Le moulage sous pression est capable de produire des pièces à géométrie complexe, y compris des pièces moulées, des parois minces et d'autres conceptions. Cette caractéristique a permis au moulage sous pression de produire des pièces avec des structures complexes et un large éventail de fonctions dans des domaines tels que l'aérospatiale, l'automobile et l'électronique grand public. Les concepteurs peuvent ainsi intégrer davantage de fonctionnalités dans une seule pièce, ce qui réduit la nécessité d'un assemblage ultérieur. - Production en grande quantité pour une livraison rapide
Le moulage sous pression est un procédé de production à grand volume qui permet de fabriquer de grandes quantités de pièces. Dans le cas du moulage à haute pression, la production est plus rapide en raison des pressions élevées utilisées, ce qui réduit le coût de production par unité de pièce. L'utilisation de moules combinés permet notamment de fabriquer plusieurs pièces simultanément, ce qui augmente la productivité et la rentabilité par pièce. - Finition de surface lisse
En raison de la pression élevée injectée dans le métal pendant le processus de moulage sous pression, les pièces métalliques moulées ont généralement une finition de surface lisse, en particulier dans la zone de l'enveloppe de la pièce.coulée à basse pressionetcoulée gravitationnelleet d'autres processus. Ce traitement de surface de haute qualité permet non seulement d'améliorer l'aspect de la pièce, mais aussi de réduire les efforts nécessaires pour les traitements de surface ultérieurs. - Longue durée de vie des moules
moule de coulée sous pressionIls sont généralement fabriqués dans un acier de haute qualité offrant une excellente résistance aux températures et aux pressions élevées. Ces aciers robustes permettent aux moules de résister à une utilisation prolongée et d'avoir une longue durée de vie, ce qui réduit la fréquence de remplacement des moules et les coûts de maintenance pour une production à long terme.
Inconvénients du moulage sous pression
- Pour les métaux non ferreux uniquement
Le procédé de moulage sous pression s'applique principalement aux métaux non ferreux tels que l'aluminium, le zinc et le magnésium. Ces métaux ont des points de fusion modérés et sont facilement injectés dans des moules sous haute pression. En revanche, le moulage sous pression n'est pas adapté aux métaux ferreux dont le point de fusion est plus élevé, tels que l'acier et le fer. Le moulage de métaux tels que l'acier et le fer nécessite un équipement spécial et des processus plus complexes, ce qui limite quelque peu l'application du moulage sous pression. - Coût élevé des moules
Les moules de coulée sous pression sont plus coûteux à fabriquer, en particulier lorsqu'on utilise la technologie de l'injection sous pression.usinage à commande numériqueLa fabrication de moules est un processus complexe et coûteux. L'utilisation de moules en acier de haute qualité augmente encore les coûts, en particulier pour la fabrication de pièces complexes. Si le procédé de moulage sous pression convient à la production de gros volumes, le coût de l'outillage peut être un facteur limitant pour les petits lots ou les pièces complexes. - Sensibilité aux défauts
Au cours du processus de production, les pièces moulées sous pression peuvent présenter des porosités, des retraits, des porosités et d'autres défauts, en particulier dans le cas de la coulée sous haute pression, ces défauts sont plus fréquents. Par exemple, la rétention d'air pendant le processus de moulage peut entraîner la création de pores à la surface de la pièce, et ces pores peuvent former des bulles d'air pendant le traitement thermique, ce qui affecte la qualité de la pièce. Des étapes supplémentaires de finition de la surface peuvent être nécessaires pour traiter ces défauts, ce qui augmente les coûts de production. - Ne convient pas à la production à petite échelle
Bien que le moulage sous pression convienne à la production à grande échelle, son investissement initial est élevé, en particulier les coûts fixes liés à la fabrication du moule et à la mise en place de l'équipement. Par conséquent, le procédé de moulage sous pression n'est généralement pas adapté à la production à petite échelle ou à la production de pièces uniques. Pour la production à petite échelle, d'autres procédés (tels que le moulage par injection ou l'usinage CNC) peuvent être plus adaptés et permettre de réduire les coûts et les délais de production.
Matériaux métalliques de Hershey dans la coulée sous pression
Les matériaux métalliques utilisés dans le processus de moulage sous pression sont généralement des alliages non ferreux tels que l'aluminium, le magnésium et le zinc. Ces alliages présentent des caractéristiques de performance différentes et conviennent à des applications différentes. Le tableau suivant présente une comparaison détaillée des alliages de moulage sous pression les plus courants, avec une liste de leurs principales compositions, points de fusion, propriétés et applications typiques.
alliages | Sous-types communs | base | Point de fusion (°C) | Principales caractéristiques | application typique |
---|---|---|---|---|---|
aluminium | a380, a360, a390, a413, adc12 | Aluminium (Al), Cuivre (Cu), Silicium (Si), Magnésium (Mg) | 577 - 660 | Léger, résistant à la corrosion, haute résistance, bonne maniabilité et bon rapport qualité-prix. | Automobile (composants de moteur, roues, châssis), aérospatiale (composants structurels, boîtiers), électronique (boîtiers, carrosseries) |
alliage de magnésium | az91d, am60b, as41b | Magnésium (Mg), Aluminium (Al), Zinc (Zn) | 632 - 650 | Extrêmement léger, bonne coulabilité pour les applications sensibles au poids, excellente coulabilité. | Aérospatiale (structure de la carrosserie, composants intérieurs), automobile (composants légers), électronique (appareils portables, boîtiers de téléphones mobiles) |
alliage de zinc | Alliage de zinc #2, #3, #5, #7, ZA8, ZA27 | Zinc (Zn), Aluminium (Al), Cuivre (Cu), Magnésium (Mg) | 381 - 419 | Excellente coulabilité, point de fusion bas, convient aux conceptions complexes et est rentable. | Électronique (connecteurs, boîtiers), quincaillerie (serrures, boutons), jouets et pièces automobiles (pièces décoratives, engrenages) |
alliage de cuivre | Laiton (par exemple C85700), bronze (par exemple C93200) | Cuivre (Cu), Zinc (Zn) (Laiton) ; Cuivre (Cu), Etain (Sn) (Bronze) | 900 - 1083 | Haute résistance, excellente conductivité et résistance à la corrosion, durable. | Tuyaux (tuyaux d'eau résistant à la corrosion, tuyaux de gaz), connecteurs électriques (bornes, contacts électriques), composants marins (composants résistant à la corrosion), roulements |
alliage d'étain | - | Etain (Sn) (90%), cuivre (Cu) (2.5%), plomb (Pb) (7.5%), antimoine (Sb) | 170 - 230 | Point de fusion bas, bonne fluidité, résistance à la corrosion, coulée facile. | Articles décoratifs (bijoux, artisanat), figurines, souvenirs |
alliage de plomb | - | Plomb (Pb), étain (Sn) | 183 - 327 | Faible point de fusion, doux, bonne résistance à la corrosion, adapté au blindage contre les radiations. | Blindage contre les radiations (équipements médicaux, installations nucléaires), batteries (progressivement remplacées) |
alliage à base d'étain | - | Etain (Sn), Cuivre (Cu), Antimoine (Sb) | 232 | Point de fusion bas, bonnes propriétés de coulée, bonne résistance à la corrosion. | Composants électroniques (matériaux de soudure, pièces électroniques), bijouterie, applications spéciales (petites pièces, bijouterie fine) |
Comparaison du moulage sous pression avec d'autres procédés de fabrication
Le moulage sous pression est souvent confondu avec d'autres procédés de fabrication (par exemple, le moulage par injection, le forgeage, l'estampage, etc. Malgré leurs similitudes, chaque procédé présente des avantages et des domaines d'application qui lui sont propres. Vous trouverez ci-dessous une comparaison entre le moulage sous pression et des procédés courants tels que le moulage par injection et le forgeage, afin de mieux comprendre les différences et les scénarios d'application :
Différence entre le moulage sous pression et le moulage par injection
Le moulage sous pression et le moulage par injection sont deux procédés de moulage populaires, qui utilisent tous deux le principe de l'injection et conviennent à la fabrication de pièces présentant des détails complexes et une excellente finition de surface. Toutefois, les matériaux et les processus applicables diffèrent. Voici les principales différences entre ces deux procédés :
divergence | moulage sous pression | moulage par injection |
---|---|---|
flux de travail | Injection de métal en fusion sous pression dans des moules en acier préconçus | Injection de plastique fondu sous pression dans des moules en acier ou en aluminium conçus à l'avance. |
fabrication | Alliages de métaux non ferreux (par exemple aluminium, zinc, magnésium) | Thermoplastiques ou thermodurcissables |
Matériaux du moule | acier (chimie) | Acier ou aluminium |
temps de recharge | Temps de recharge plus long | Temps de recharge plus court |
vitesse de production | relativement lent | dans un délai relativement court |
coût de transformation | Coût des moules plus élevé (utilisation de moules en acier) | Coûts d'outillage réduits (utilisation d'outillage en aluminium) |
coût des composants | Plus élevé (en raison d'un temps de production plus long) | Plus faible (temps de production plus rapide) |
Différence entre le moulage sous pression et le forgeage
La principale différence entre le forgeage et le moulage sous pression réside dans la manière dont ils sont mis en forme. Le forgeage consiste à former le métal à l'état solide en appliquant des forces de compression, tandis que le moulage sous pression consiste à injecter du métal en fusion dans un moule conçu à l'avance. Les deux procédés diffèrent également en termes de matériaux applicables, de vitesse de production et de performance des pièces :
divergence | forge (métal) | moulage sous pression |
---|---|---|
flux de travail | Mise en forme d'un métal chauffé par application d'une force de compression | Injection sous pression de métal en fusion dans un moule |
fabrication | Pour les métaux ferreux et non ferreux tels que l'acier et l'aluminium | Pour les métaux non ferreux tels que l'aluminium, le zinc et le magnésium |
Matériaux de formage | Pas besoin de moules, mais utilisation de moules pour optimiser la forme | Des moules doivent être utilisés |
vitesse de production | plus lent | dans un délai relativement court |
contrôle de la tolérance | Tolérance moyenne | Contrôle de la tolérance de haute précision |
Propriétés finales de la pièce | Amélioration des propriétés mécaniques | Les propriétés mécaniques dépendent du matériau de coulée |
Différence entre le moulage sous pression et l'emboutissage
L'emboutissage est un procédé de formage de feuilles de métal à l'aide d'une presse et convient à la production en série de pièces à parois minces. Par rapport au moulage sous pression, l'emboutissage présente des matériaux et des processus de moulage différents, notamment en termes de complexité des pièces concernées et de productivité :
divergence | moulage sous pression | coup de poing |
---|---|---|
flux de travail | Injection de métal en fusion dans un moule pour le façonnage | Former des pièces à partir de feuilles de métal en les emboutissant à l'aide d'une matrice. |
fabrication | Principalement des alliages de métaux non ferreux (par exemple aluminium, zinc) | Convient à tous les types de tôles (acier, aluminium, etc.) |
Matériaux du moule | acier (chimie) | acier (chimie) |
Forme de la pièce | Pour les pièces de forme complexe | Pour les pièces à parois minces et les formes simples |
vitesse de production | plus lent | dans un délai relativement court |
précis | très précis | Précision moindre |
La différence entre le moulage sous pression et l'impression 3D
L'impression 3D est un procédé de fabrication additive qui permet de créer des pièces en empilant des matériaux couche par couche. L'impression 3D offre une plus grande flexibilité et des capacités de prototypage plus rapides que le moulage sous pression, mais diffère en termes de vitesse de production et de performance des pièces :
divergence | moulage sous pression | Impression 3D |
---|---|---|
flux de travail | Injection de métal en fusion dans un moule pour le façonnage | Impression couche par couche de matériaux à partir de modèles numériques |
fabrication | Alliages de métaux non ferreux (par exemple, aluminium, zinc) | Thermoplastiques, poudres métalliques, etc. |
Matériaux du moule | acier (chimie) | Aucun moule n'est nécessaire |
vitesse de production | plus lent | dans un délai relativement court |
précis | très précis | Précision modérée |
appareil | Production en série de pièces complexes | Prototypage rapide, production en petite quantité |
Matériaux courants de moulage sous pression et sélection
L'aluminium, le zinc, le magnésium et d'autres alliages sont des matériaux couramment utilisés pour le moulage sous pression. Ils possèdent chacun des propriétés uniques, adaptées à différents scénarios d'application. Voici les caractéristiques de plusieurs alliages courants :
- aluminiumLes produits de cette catégorie sont : légers, résistants à la corrosion, faciles à traiter et largement utilisés dans les secteurs de l'automobile, de l'aérospatiale et de l'électronique.
- alliage de magnésiumLes produits de cette catégorie sont : très légers pour les applications à poids critique telles que l'aérospatiale et l'électronique grand public ; très légers pour les applications à poids critique telles que l'aéronautique.
- alliage de zincLes produits de cette catégorie sont les suivants : point de fusion bas, excellente aptitude au moulage, couramment utilisés dans les produits électroniques, le matériel informatique et les pièces de jouet.
- alliage de cuivreLes produits de cette catégorie sont les suivants : haute résistance et bonne conductivité électrique pour les connecteurs électriques et les composants marins.
Optimisation de la conception et de la fabrication
La conception du moulage sous pression ne dépend pas seulement de la sélection des matériaux, mais doit également prendre en compte des facteurs tels que la géométrie de la pièce, l'angle d'extraction, le rayon du congé de raccordement, etc. afin d'améliorer les performances, la fabricabilité et la rentabilité de la pièce. Par exemple, un angle d'extraction approprié peut empêcher efficacement les pièces de coller au moule et réduire le risque d'endommagement ; un rayon de congé raisonnable peut aider à répartir uniformément les contraintes et à éviter les concentrations de contraintes.
rendre un verdict
Le moulage sous pression est devenu une technologie indispensable à la fabrication moderne, grâce à sa haute précision et à ses capacités de production en grande quantité. Qu'il s'agisse de pièces automobiles, de boîtiers électroniques ou de composants aérospatiaux, la technologie du moulage sous pression constitue une base solide pour l'innovation et l'excellence de la conception. Les matériaux et les processus continuant à progresser, le moulage sous pression continuera à l'avenir d'apporter des solutions plus efficaces et de meilleure qualité à un grand nombre d'industries.
Moulage sous pression : problèmes courants et stratégies d'adaptation
Pourquoi les pièces moulées sous pression sont-elles sujettes à la porosité ?
Les poches sont généralement dues au fait que le métal ne s'évacue pas complètement pendant le processus d'injection, ou à une conception défectueuse du moule (par exemple, un mauvais système d'évacuation). Les stratégies consistent à optimiser la conception de l'évent du moule, à ajuster la vitesse et la pression d'injection et à utiliser un système d'évent plus efficace.
Pourquoi les défauts sont-ils susceptibles d'apparaître à la surface des pièces moulées sous pression ?
Les défauts de surface tels que les bulles, les plis et les rayures sont principalement dus à des surfaces de moule inégales ou à un flux de métal inégal. Pour éviter ces problèmes, il convient de vérifier régulièrement l'état de surface du moule et de s'assurer que la température d'injection et le débit sont stables.
Quel est le problème des trous de retrait dans les pièces moulées sous pression ?
Le trou de rétraction est dû au fait que le métal de refroidissement de la coulée n'a pas réussi à reconstituer le matériau de remplissage ; il apparaît souvent dans les formes larges ou complexes de la coulée sous pression. Le retrait peut être évité efficacement en optimisant la conception du moule, en améliorant l'efficacité du système de coulée et en ajustant la vitesse de refroidissement.
Les pièces moulées sous pression sont-elles susceptibles de se fissurer ?
Les fissures se produisent généralement lorsque le métal s'écoule de manière irrégulière ou se refroidit trop rapidement, et peuvent être causées par une pression d'injection excessive ou une mauvaise conception du moule. Il est possible de réduire les fissures en contrôlant la vitesse d'injection, la température et la pression, et en utilisant des matériaux très résistants.
Qu'en est-il de l'instabilité dimensionnelle des pièces moulées sous pression ?
L'instabilité dimensionnelle peut être due à l'usure du moule, à une pression d'injection instable ou à un mauvais contrôle de la température. Une révision et une maintenance régulières du moule pour maintenir des conditions d'injection stables, ainsi qu'un réglage précis du système de contrôle de la température, peuvent résoudre efficacement le problème de l'instabilité dimensionnelle.
Comment l'usure des moules affecte-t-elle la qualité du moulage sous pression ?
L'usure des moules peut entraîner une perte de précision du produit et même affecter l'apparence et les performances des pièces moulées. Pour lutter contre l'usure des moules, il convient d'inspecter et de remplacer régulièrement les moules, d'utiliser des matériaux résistants à l'usure et d'optimiser la conception et le processus des moules.
Pourquoi les pièces moulées sous pression sont-elles sujettes à la déformation ?
La déformation est généralement due à un refroidissement inégal ou à une mauvaise conception du moule, en particulier lorsque la pièce moulée est de grande taille ou complexe. Le risque de déformation peut être réduit en ajustant le système de refroidissement et en optimisant la conception du moule.
Comment réduire la ségrégation par le froid ?
La ségrégation à froid est un défaut de délamination dû au fait que le métal ne fusionne pas complètement lorsqu'il est injecté dans le moule. Pour éviter la ségrégation à froid, la vitesse et la température d'injection doivent être optimisées pour garantir un écoulement régulier du métal, et le système de coulée et les canaux doivent être conçus de manière appropriée.
Le post-traitement des pièces moulées sous pression est-il nécessaire ?
Les exigences de post-traitement des pièces moulées sous pression dépendent des exigences de conception et des critères de qualité de la surface de la pièce. Certaines pièces nécessitent un usinage supplémentaire, tel que le meulage, le perçage ou l'ébavurage, afin de respecter des tolérances et des finitions de surface strictes.