Moulage par gravité d'alliages d'aluminium : défauts courants et mesures préventives
Temps de publication:2025-01-21 Trier par:Le blog Nombre de vues:381
coulée gravitationnelle Dans le processus de coulée, la première solidification du liquide métallique est due à l'expansion thermique et à la contraction du volume, ce qui nécessite de s'appuyer sur la partie supérieure du liquide métallique pour compléter la gravité, afin de compléter l'effet de rétrécissement. La solidification de la coulée par gravité pour l'ordre de solidification, est la partie entière dans la solidification de la solidification conformément à un certain ordre de solidification successive, la position de solidification relativement en arrière peut être le retrait complémentaire de la position de solidification relativement en avant, de sorte que les défauts finaux de la coulée sont concentrés dans les dernières parties de refroidissement (colonnes montantes, position des vannes), pour obtenir des pièces moulées de production qualifiées. Coulée par gravité aluminium Séquence de solidification des pièces moulées de roues :
Jante - Rayon - Moyeu central (biseauté) - Cône de déviation - Carotte (contremarche)
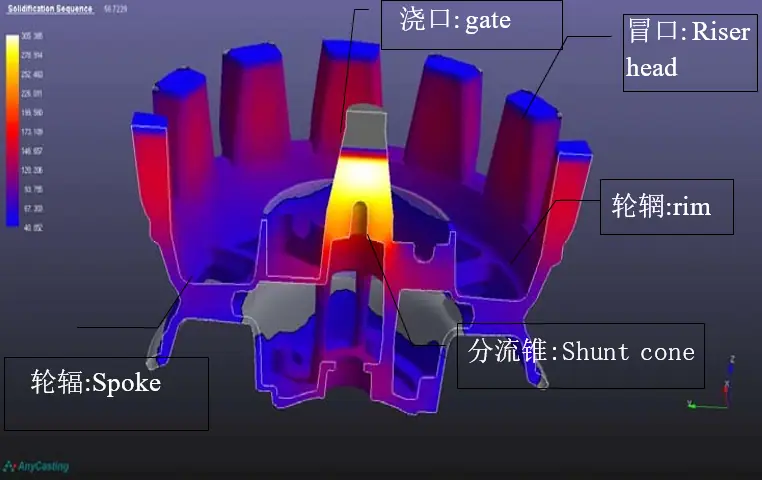
Les paramètres de conception du processus de coulée comprennent les tolérances d'usinage, les tolérances de processus (élévateurs, etc. pour compenser la position de retrait), le retrait du métal (coefficient de retrait) et la traction de la pente du moule, le système de refroidissement (pour garantir que la coulée de la solidification séquentielle), etc.
Lorsque la séquence de solidification des pièces coulées ou les paramètres de conception du processus ne répondent pas aux exigences du produit, des défauts de coulée apparaissent. Les défauts de coulée les plus courants des pièces coulées en alliage d'aluminium et les mesures préventives sont les suivants :
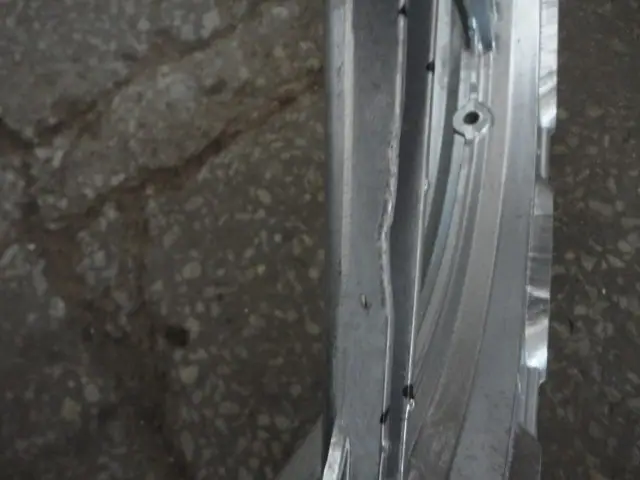
1. sous-couvert .
Caractéristiques : Dans le processus de formage de la fonte, certaines parties du remplissage sont incomplètes.
Causes de la formation :
a. La fluidité du liquide d'aluminium n'est pas forte, la teneur en gaz du liquide est élevée, la peau d'oxyde est plus importante ;
b. Mauvais système de moulage, la section de la porte intérieure est trop petite ;
c. Mauvaises conditions d'échappement du moule, mauvais échappement, trop de peinture, température du moule trop élevée, ce qui entraîne une pression d'air élevée dans la cavité et ne peut pas être évacué en douceur.
Mesures préventives : 1. Améliorer la fluidité du liquide d'aluminium, en particulier l'affinage et la scorification, augmenter de manière appropriée la température du moule ou la température de coulée (augmenter la vitesse de coulée, ajuster l'épaisseur de la paroi, ouvrir le canal de la barre auxiliaire) ; 2. Augmenter la section de la porte intérieure ; 3. Améliorer les conditions d'échappement, en fonction du phénomène défectueux combiné à la situation réelle du moule, augmenter la rainure de débordement et la ligne d'échappement, les cavités concaves profondes pour ajouter les bouchons d'échappement, repasser la peinture, de manière à ce que la peinture soit fine et uniforme, et attendre que le moule sèche et fermer la production. Attendre le séchage de la peinture avant de procéder à la fabrication du moule.
2. craquements
Caractéristiques : l'ébauche est endommagée ou cassée, s'ouvre en longues lignes minces, statu quo irrégulier, pénétration et non-pénétration de deux types, sous l'action de la force extérieure, la tendance est au développement, aux fissures froides, aux fissures chaudes, mais la différence est que les fissures froides au niveau du métal ne sont pas oxydées, et que les fissures chaudes au niveau du métal sont oxydées.
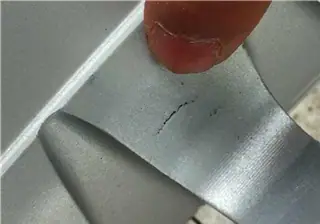
Causes de la formation :
a. La structure de la coulée n'est pas raisonnable, la contraction est entravée, l'angle rond de la coulée est faible ;
b. L'unité d'éjection est déviée et chargée de manière inégale ;
c. La température du moule est trop élevée ou trop basse, ce qui entraîne des tensions et des fissures graves lors de l'ouverture du moule ;
d. Les éléments nocifs de l'alliage dépassent la norme et le taux d'élongation diminue ;
e. Mauvaise ventilation ;
Mesures préventives : 1, améliorer la structure de la coulée, réduire la différence d'épaisseur de la paroi du moule, augmenter la partie fissurée du coin arrondi ou du rayon de l'arc ; 2, corriger le système d'éjection du moule et les goupilles de serrage supérieures et inférieures du moule, les douilles, pour s'assurer que l'éjection se fait en douceur ; 3, ajuster la température du moule à la température normale pour éliminer le phénomène de moule inversé et irrégulier, augmenter la pente de ramassage du moule ; 4, contrôler la composition de l'aluminium liquide, en particulier la composition des éléments dangereux ; 5, rogner le système d'échappement du moule pour s'assurer que cette partie de l'échappement du moule se fait en douceur. 5. réparer le système d'échappement du moule pour s'assurer que cette partie de l'échappement du moule est lisse.
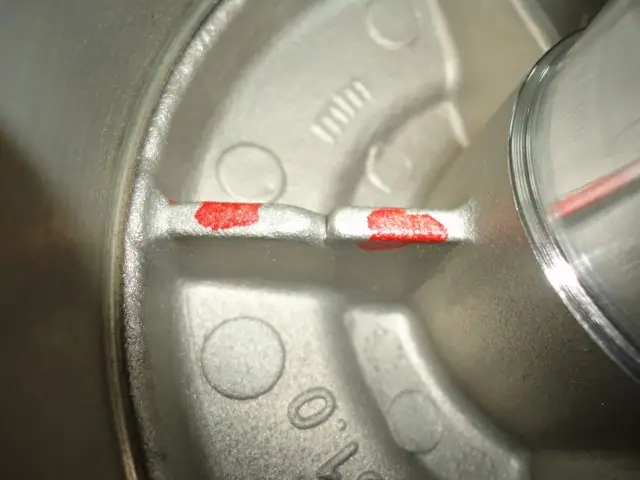
3. barrière de froid
Caractéristiques : Traces à l'extrémité ou au revers de l'écoulement du fluide, avec des bords arrondis à leurs intersections, ayant tendance à se poursuivre sous l'effet de forces extérieures.
Causes de la formation :
a. Mauvaise fluidité du liquide d'aluminium ;
b. La fusion du remplissage des sous-brins liquides est médiocre ou le processus est trop long pour la connexion ;
c. La température du liquide (moule) est trop basse ou la ventilation est insuffisante ;
Mesures préventives : 1. Augmenter de manière appropriée la température de l'aluminium liquide et la température du moule, vérifier et ajuster la composition de l'alliage d'aluminium liquide ; 2. Disposer raisonnablement le canal de débordement, augmenter le canal d'écoulement, raccourcir le processus, de sorte que l'aluminium liquide soit suffisamment rempli ; 3. Augmenter la vitesse de coulée ou augmenter la température du moule, améliorer le système d'échappement du moule.
4. (de boissons) pétillant
Caractéristiques : Sous la peau de la coulée, des bulles se forment par l'expansion des gaz rassemblés.
Causes de la formation :
a. La température du moule est trop élevée et la température de l'aluminium liquide est trop élevée ;
b. La vitesse de remplissage est trop rapide, et le liquide métallique est impliqué dans le gaz pendant le processus de remplissage.
c. La peinture est gazée, trop pulvérisée, pas évaporée avant la coulée, le gaz est enveloppé dans la surface de coulée ;
d. Mauvaise ventilation ;
e. Temps de rétention insuffisant et ouverture prématurée du moule.
Mesures préventives : 1, modifier le processus de refroidissement du moule, refroidir la température du moule jusqu'à la température de travail normale ; modifier le processus de fusion pour s'assurer que la température de l'aluminium liquide est normale ; 2, ralentir la vitesse de remplissage, pour éviter le paquet de gaz tourbillonnaire (peut être contrôlé par la densité de l'écran, l'épaisseur de l'écran, etc.) ; 3, sélectionner une petite quantité de gaz pour le revêtement, pulvériser une couche mince et uniforme de peinture, sécher complètement et évaporer après la fermeture du moule ; 4, modifier le temps de sortie du moule pour s'assurer que la solidification de l'ensemble.
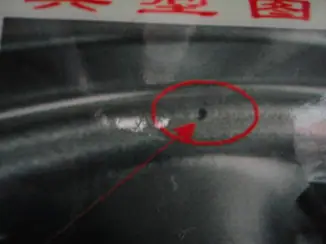
5. Trous d'air (trous de gaz et de scories)
Caractéristiques : trous de forme régulière avec des surfaces lisses, formés par les gaz présents à l'intérieur de la coulée.
Causes de la formation :
a. Le liquide d'aluminium pénètre dans la cavité, un impact positif se produit, entraînant un tourbillon ; b. La vitesse de chargement est trop rapide, entraînant un écoulement stagnant ;
c. Mauvais échappement ; d. Position de la cavité du moule trop profonde ; e. Trop de peinture, pas complètement séchée et évaporée avant le remplissage ;
f. Mauvais affinage de l'aluminium liquide, scorification incomplète ;
h. Il y a des débris dans la cavité et le filtre ne répond pas aux exigences ou est mal placé ; i. La surépaisseur d'usinage est trop importante.
Mesures préventives : 1, l'utilisation d'un système propice à l'évacuation des gaz dans la cavité de la forme d'infusion, pour éviter que le liquide d'aluminium ne se referme d'abord sur la surface de séparation du système de débordement ; 2, réduire la vitesse de remplissage de l'aluminium liquide (augmenter la densité de l'écran et d'autres moyens) ; 3, dans la partie finale de remplissage de la cavité, ouvrir la rainure de débordement et le canal d'échappement, et éviter la fermeture de l'aluminium liquide ; 4, l'installation de la cavité profonde des bouchons d'échappement et l'utilisation de la structure en mosaïque pour augmenter l'échappement ; 5, l'utilisation de pistolets à vent pour nettoyer la cavité, et pour re En outre, les alliages contenant de l'aluminium ne doivent pas, dans la mesure du possible, être fondus dans le four d'alimentation ; 7. répondre aux besoins d'ajustement raisonnable de la tolérance d'usinage du produit.
6. Rétrécissement
Caractéristiques : trous de forme irrégulière avec des surfaces rugueuses causées par une compensation interne insuffisante lors de la condensation des pièces de fonte.
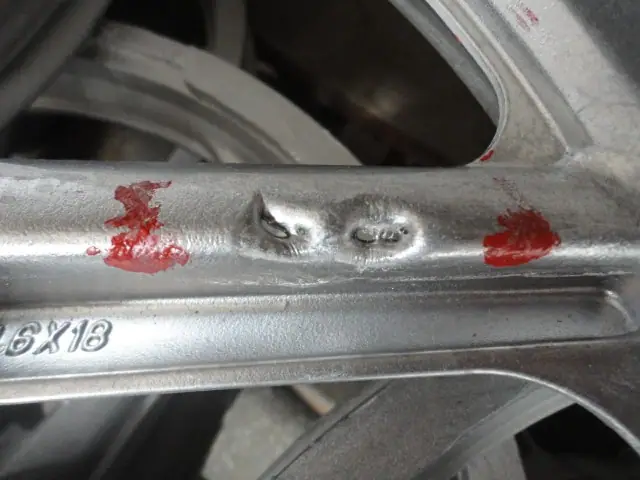
Causes de la formation :
a. La température du liquide d'aluminium est trop élevée ;
b. Epaisseur inégale des parois de la structure de coulée, entraînant des joints chauds ;
c. Une porte intérieure plus petite ;
d. Température locale élevée du moule.
Mesures préventives : 1, en cas de respect des exigences de coulée, réduire la température du liquide d'aluminium ; 2, améliorer la structure de la coulée, éliminer l'accumulation de pièces métalliques, ralentir la transition ; si vous ne pouvez pas modifier la structure de la coulée, l'impact local du retrait des pièces "joints froids", peut être derrière le périmètre des fentes de perçage et de fraisage, puis rempli de matériaux adiabatiques pour augmenter la résistance thermique, peut être ajusté. Champ de température raisonnable ; 3, le nœud chaud local doit être soumis à un refroidissement forcé (on peut utiliser localement du cuivre incrusté et d'autres moyens), afin d'ajuster un gradient de température de retrait raisonnable ; 4, augmenter les colonnes montantes sombres, afin de faciliter le transfert de la pression ; 5, ajuster l'épaisseur du revêtement du moule, afin de contrôler la température locale du moule.
7. design décoratif
Caractéristiques : la surface de la fonte présente des stries lisses, visibles à l'œil nu, mais non perceptibles à la main, la couleur est différente du grain normal du métal de base, légèrement frotté avec du papier de verre qui ne l'est pas.
Causes de la formation :
a. Chargement trop rapide ;
b. Une quantité de peinture trop importante et irrégulière ;
Mesures préventives : 1. réduction de la vitesse de remplissage ; 2. dosage fin et uniforme de la peinture, selon le principe du milieu mince et du bord épais ;
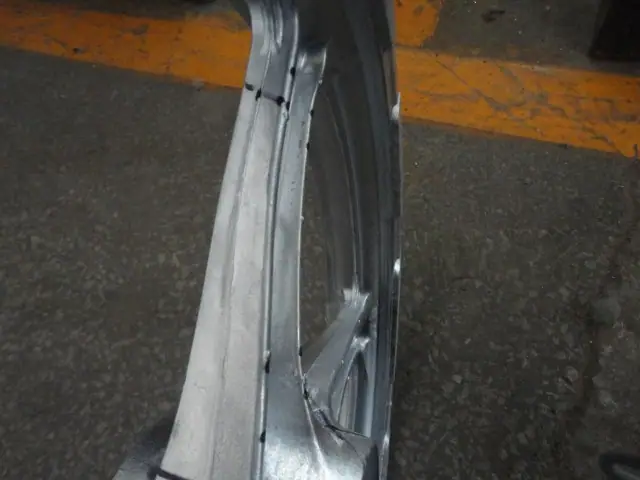
8. déformation
Caractéristiques : la géométrie de la coulée ne correspond pas aux exigences de conception de la déformation globale.
Causes de la formation :
a. Mauvaise conception de la coulée, entraînant un rétrécissement inégal ;
b. Ouverture du moule trop précoce, le moulage n'est pas assez rigide ;
c, l'inclinaison du moule est trop faible, le démoulage est difficile ;
d. Prélèvement et mise en place des pièces de fonte, fonctionnement incorrect ;
e. La coulée se refroidit trop rapidement, ce qui entraîne des déformations.
Mesures préventives : 1, améliorer la structure de la coulée, afin que l'épaisseur de la paroi soit uniforme ; 2, déterminer le meilleur moment pour ouvrir le moule, augmenter la rigidité de la coulée ; 3, augmenter la pente du moule de prélèvement de la coulée ; 4, prélever et placer la coulée, elle doit être légère à prendre et légère à placer ; 5, après l'ouverture du moule, la coulée doit être placée à l'air libre pour refroidir lentement.
9. rétrécissement
Caractéristiques : le retrait des pièces moulées en alliage d'aluminium se produit généralement près de la carotte intérieure, de la partie épaisse de la racine de la colonne montante, de la paroi de la jante, des parties de transfert épaisses et minces des rayons et des pièces à parois minces présentant de grands plans. La fracture est grise lorsque la billette n'est pas traitée, et la fracture est grise et jaune clair ou gris-noir après le traitement thermique, et lorsque la projection radiographique est effectuée, elle est trouble sur le film radiographique, et les plus graves ont la forme d'une maille de soie.usinageLes pièces présentent de petits trous d'épingle dispersés après l'usinage. Le rétrécissement des pièces moulées peut être détecté par rayons X, par fracture et par d'autres méthodes d'inspection.
Causes de la formation :
a. Mauvais retrait de la colonne montante ; b. Trop de gaz dans la charge ; c. Température trop élevée près de la carotte intérieure ; d. Trop d'humidité dans le moule de sable et le noyau de sable n'est pas séché ;
e. mauvaise pulvérisation des revêtements de moule ; f. temps de remplissage inadéquat des pièces moulées dans le processus de coulée ; h. température trop élevée de l'aluminium liquide et vitesse de coulée trop rapide.
Mesures préventives :
1、Supplémenter le liquide d'aluminium de la partie ascendante, améliorer la conception de la porte ; 2、 La scorification du liquide d'aluminium, le traitement de dégazage doit être suffisant et complet ; 3、Système de refroidissement des pièces frettées ou bloc de l'anneau de refroidissement (tel que le bloc de cuivre incrusté dans le moule, etc.) et autres formes d'abaissement de la température du moule près de la carotte intérieure ; 4、Contrôler l'humidité du sable, pour assurer la cuisson et le séchage du noyau de sable ; 5、Sélectionner les bons revêtements, formuler le mélange de peinture approprié de manière irrationnelle, et changer la pulvérisation du revêtement. Choisir le bon revêtement, formuler le mélange de peinture approprié de manière irrationnelle, changer la méthode de pulvérisation du revêtement (plus la porte est proche, plus le revêtement est fin), et fournir une formation professionnelle au personnel concerné ; 6, changer la coulée dans la coulée du temps de remplissage, et ajuster les paramètres du processus ; 7, surveiller en temps réel la température de l'aluminium liquide, et contrôler la vitesse de coulée (augmenter l'écran ou changer la forme de l'écran et d'autres moyens).
10. Mauvaise modélisation :
Caractéristiques : Une partie de la pièce moulée est mal alignée avec l'autre partie au niveau du plan de joint, et un décalage relatif se produit.
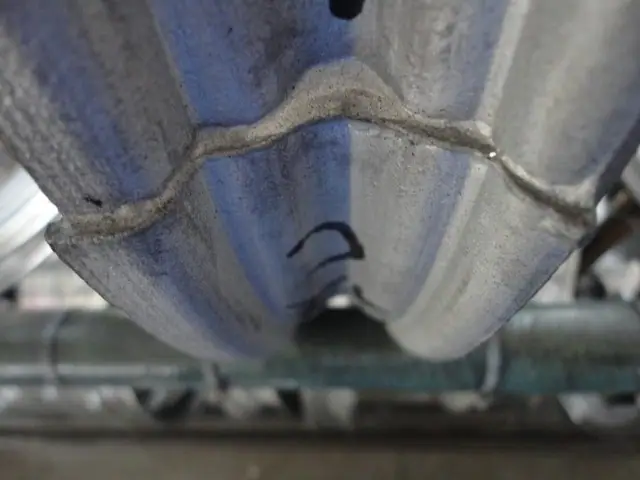
Causes de la formation :
a. Déplacement des inserts du moule (par exemple, les quatre curseurs ne sont pas moulés en place) ;
b. Usure des pièces de guidage du moule (usure des goupilles de serrage du moule et des manchons) ;
c. Faible précision de la fabrication et de l'assemblage des moules.
Mesures préventives : 1, ajuster le bloc, à resserrer ; 2, remplacer les pièces de guidage ; 3, corriger le moule pour éliminer les erreurs.
Choisir le bon prestataire de services de moulage sous pression par gravité
La coulée par gravité est un procédé de coulée des métaux simple et efficace, mais qui nécessite néanmoins des connaissances et de l'expérience. Une précision et une qualité supérieures peuvent être obtenues en se spécialisant dans les techniques de coulée par gravité. Il est donc plus sage de choisir un prestataire de services professionnel tel que Ningbo Hersin pour externaliser vos besoins en matière de moulage.
Chez Ningbo Hexin, notre équipe d'ingénieurs possède de nombreuses années d'expérience dans le domaine de la coulée par gravité et est en mesure de vous conseiller sur le processus de coulée le plus adapté à votre projet. En tant qu'entreprise certifiée ISO 9001:2015, nous sommes équipés d'un matériel de coulée de pointe pour garantir la production de pièces de haute qualité. En téléchargeant vos fichiers de conception via notre plateforme en ligne, vous recevrez un devis précis et une analyse technique dans les 12 heures, ce qui vous aidera à réaliser votre projet plus efficacement.
Questions fréquemment posées et réponses
Causes des défauts de porosité ?
Une mauvaise ventilation, un mauvais affinage du liquide d'aluminium ou des vitesses de coulée excessives sont à l'origine de ce phénomène.
Les pièces moulées en alliage d'aluminium semblent être à l'origine du motif ?
Les motifs sont généralement dus à des vitesses de remplissage trop rapides ou à une pulvérisation inégale de la peinture.
Raisons des fissures dans les pièces moulées en alliage d'aluminium ?
Les fissures sont généralement causées par une conception irrationnelle de la structure de coulée, une température de moule inappropriée ou un excès d'éléments nocifs dans le liquide d'aluminium.
Comment éviter la sous-coulée dans la coulée par gravité de l'aluminium ?
Amélioration de la fluidité de la solution d'aluminium (augmentation de la température de l'eau d'aluminium, ajout d'éléments spécifiques), augmentation de la section de la porte intérieure et amélioration des conditions d'aération du moule (augmentation des bouchons d'aération).