Traitement de surface de l'aluminium
Temps de publication:2024-10-21 Trier par:Le blog Nombre de vues:885
Les procédés de traitement de surface de l'aluminium peuvent être divisés en

- Traitement de surface mécanique : Traitement des surfaces d'aluminium par des moyens mécaniques afin d'améliorer leur aspect, leur résistance à l'usure, leur adhérence, etc.
- Traitement chimique de la surface : L'objectif principal est de modifier la composition, la structure et les propriétés de la surface de l'aluminium par des réactions chimiques afin d'améliorer sa résistance à la corrosion et à l'abrasion, ainsi que ses propriétés décoratives et fonctionnelles.
Quels sont les procédés de traitement de surface de l'aluminium ?
I. POLISSAGE
Le polissage est une méthode courante de traitement de l'aluminium destinée à réduire la rugosité de la surface d'une pièce par une action mécanique, chimique ou électrochimique afin d'obtenir une surface brillante et plane. Ce processus utilise des outils de polissage et des particules abrasives ou d'autres moyens de polissage pour modifier la surface de la pièce. Le but principal du polissage n'est pas d'améliorer la précision dimensionnelle ou géométrique de la pièce, mais plutôt d'obtenir une surface lisse ou un éclat semblable à celui d'un miroir. Dans certains cas, le polissage est également utilisé pour éliminer le lustre, c'est-à-dire le matage. Un outil couramment utilisé dans le processus de polissage est le disque de polissage, qui est généralement constitué de plusieurs couches de toile, de feutre ou de cuir laminées ensemble et serrées de part et d'autre d'une plaque métallique circulaire. La jante du disque est recouverte d'un produit de polissage, qui consiste en un mélange homogène d'abrasifs micronisés et de graisse. Lors du polissage, le disque de polissage est pressé contre la pièce en rotation rapide (vitesse circonférentielle généralement supérieure à 20 mètres par seconde), de sorte que le matériau abrasif produit un effet de culbutage et de micro-coupure sur la surface de la pièce, ce qui permet d'obtenir une finition brillante. Après le traitement de polissage, la rugosité de la surface de la pièce peut généralement atteindre Ra0,63~0,01 micron. En fonction des différentes étapes du polissage, telles que le polissage grossier (processus de polissage de base), le polissage moyen (processus de finition) et le polissage fin (processus de vernissage), il est crucial de choisir les bons disques de polissage et les bons composés de polissage. Cela permet non seulement d'obtenir des résultats de polissage optimaux, mais aussi d'améliorer considérablement l'efficacité du polissage. En raison de la brillance et de la beauté de la surface, en Chine, le polissage est une activité très importante.Moulage sous pressionL'entreprise l'applique souvent aux pièces décoratives automobiles, aux pièces automobiles modifiées en aluminium, etc.
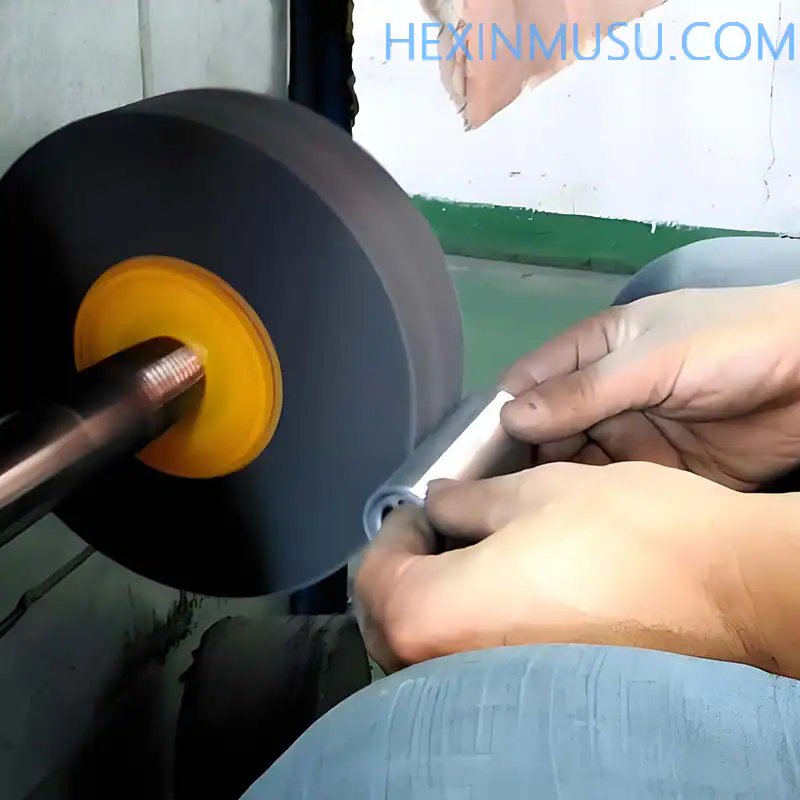
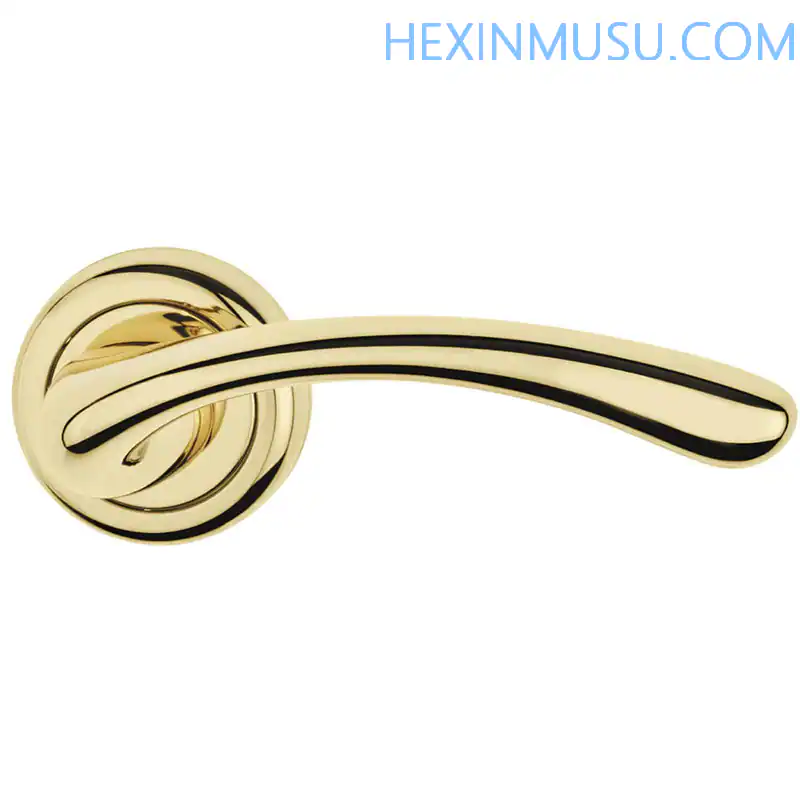
II.sablage
Le principe de base du processus de sablage consiste à utiliser de l'air comprimé comme source d'énergie pour entraîner le matériau de pulvérisation (y compris le minerai de cuivre, le sable de quartz, l'émeri, le sable de fer, le sable de Hainan, etc.) afin de former un faisceau de jet à grande vitesse sur la surface à nettoyer en pulvérisant une forte concentration de petites particules abrasives, afin d'éliminer la rouille, la peau oxydée ou d'autres contaminants de surface (et d'obtenir une surface rugueuse convenable). La surface est soumise à la friction des particules abrasives qui sont projetées à grande vitesse. La surface du substrat est nettoyée et rendue rugueuse par l'impact et l'action de coupe du flux d'abrasif à grande vitesse. Le processus modifie non seulement la forme de la surface extérieure de la pièce, mais aussi, grâce au rôle des abrasifs sur la surface, donne à la pièce un certain degré de propreté et une rugosité différente (en changeant la taille du matériau d'impact pour contrôler la rugosité de la surface de l'aluminium), souvent utilisé par le fournisseur chinois de produits de moulage sous pression en tant que produits de moulage sous pression en aluminium sur la surface du processus de traitement, ou d'autres traitements de surface du prétraitement au cours du processus.
III. Le dessin
Le processus d'emboutissage des profilés en aluminium est un moyen unique de traitement de surface, qui peut refléter la texture du matériau métallique, grâce au meulage de la surface de la pièce, en créant soigneusement un motif de lignes délicat et uniforme, afin de donner au profilé en aluminium une beauté décorative. En fonction des différents motifs après l'étirage, le processus d'étirage des profilés en aluminium peut être divisé en plusieurs types, y compris l'étirage droit, l'étirage désordonné, l'ondulation et le filage, chacun d'entre eux présentant des effets visuels uniques. Ce brossage de la surface met non seulement en évidence la texture unique du matériau métallique, mais améliore également la résistance à l'abrasion et à la corrosion du produit, car l'effet brossé aura un effet convexe et concave très subtil. Par conséquent, le tréfilage est également utilisé comme processus de réparation, parce que la surface du métal présente des rayures locales, la surface entière avec la machine de tréfilage pour faire des rayures cohérentes (réduire l'épaisseur de la paroi) ------- couvre les rayures.
IV. Anodisation
Un processus d'oxydation électrolytique dans lequel l'aluminium et l'acier inoxydable sont utilisés pour la production d'électricité.aluminiumLa surface est généralement transformée en un film d'oxyde qui possède des propriétés protectrices, décoratives et d'autres propriétés fonctionnelles.L'anodisation de l'aluminium, selon cette définition, ne comprend qu'une partie du processus, la génération du film d'oxyde anodique. Une pièce en métal ou en alliage est utilisée comme anode pour former un film d'oxyde sur sa surface par électrolyse. Le film d'oxyde métallique modifie l'état et les propriétés de la surface, comme la coloration de la surface, l'amélioration de la résistance à la corrosion, l'amélioration de la résistance à l'usure et de la dureté, et la protection de la surface du métal. Par exemple, l'oxydation anodique de l'aluminium, l'aluminium et ses alliages seront placés dans l'électrolyte correspondant (tel que l'acide sulfurique, l'acide chromique, l'acide oxalique, etc.) en tant qu'anode, dans des conditions spécifiques et selon le rôle du courant appliqué, l'électrolyse. L'oxydation de l'anode d'aluminium ou de son alliage entraîne la formation d'une fine couche d'oxyde d'aluminium sur la surface, d'une épaisseur de 5 à 30 microns, et d'un film d'oxyde anodique dur pouvant atteindre 25 à 150 microns. Après l'oxydation anodique de l'aluminium ou de ses alliages, la dureté et la résistance à l'usure sont améliorées, jusqu'à 250 ~ 500 kg / mm2, bonne résistance à la chaleur, point de fusion du film d'oxyde anodique dur jusqu'à 2320K, excellente isolation, tension de claquage jusqu'à 2000V, résistance à la corrosion améliorée, dans le brouillard salin ω = 0,03NaCl après des milliers d'heures de non-corrosion. Couche mince de film d'oxyde avec un grand nombre de micropores, peut adsorber une variété de lubrifiants, convient à la fabrication de cylindres de moteur ou d'autres pièces résistantes à l'usure ; la capacité d'adsorption des micropores du film peut être colorée en une variété de belles couleurs. Les métaux non ferreux ou leurs alliages (tels que l'aluminium, le magnésium et ses alliages, etc.) peuvent être traités par oxydation anodique. Cette méthode est largement utilisée dans les pièces de machines, les pièces d'avions et d'automobiles, les instruments de précision et les équipements radio, les nécessités quotidiennes, la décoration architecturale et d'autres aspects. En règle générale, l'anode est constituée d'aluminium ou d'un alliage d'aluminium et la cathode est constituée d'une plaque de plomb. L'aluminium et la plaque de plomb sont placés dans une solution aqueuse contenant de l'acide sulfurique, de l'acide oxalique, de l'acide chromique, etc. pour effectuer une électrolyse, de sorte que la surface de l'aluminium et de la plaque de plomb puisse former une sorte de film oxydé. Parmi ces acides, l'anodisation à l'acide sulfurique est la plus répandue.
processus
Couleur unique, couleur dégradée : polissage/sablage/dessin→ dégraissage→anodisation→neutralisation→dessin→double couleur : ①polissage/sablage/dessin→ dégraissage→masquage→anodisation1→anodisation2 →sealing→dessin ②polissage/sablage/dessin→dégraissage→anodisation1 →gravure au radium→anodisation2 →sealing→anodisation.
Caractéristiques techniques
1、Iméliorer la résistance,2、Avoir n'importe quelle couleur sauf le blanc.3、Avoir des trous d'étanchéité sans nickel pour répondre aux exigences de l'absence de nickel en Europe, en Amérique et dans d'autres pays.
V. Le processus d'électrophorèse est divisé en électrophorèse anodique et électrophorèse cathodique.Si les particules de peinture sont chargées négativement et que la pièce est l'anode, les particules de peinture se déposent en un film sur la pièce sous l'action de la force du champ électrique, c'est l'électrophorèse anodique ; au contraire, si les particules de peinture sont chargées positivement et que la pièce est la cathode, les particules de peinture se déposent en un film sur la pièce, c'est l'électrophorèse cathodique.Le processus général de l'électrophorèse anodique est le suivant :Prétraitement de la pièce (déshuilage → lavage à l'eau chaude → dérouillage → lavage à l'eau froide → phosphatation → lavage à l'eau chaude → passivation) → électrophorèse anodique → post-traitement de la pièce (lavage à l'eau claire → séchage).
- 1. dégraissage.La solution est généralement une solution chimique alcaline chaude de dégraissage à 60°C (chauffée à la vapeur) pendant environ 20 minutes.
- 2、Laver à l'eau chaude. Température 60°C (chauffage à la vapeur), durée 2min.
- 3. l'élimination de la rouille.Utiliser H2SO4 ou HCl , par exemple, avec une solution de détartrage à l'acide chlorhydrique, acidité totale HCl ≥ 43 points ; acidité libre > 41 points ; ajouter du détergent 1,5% ; laver à température ambiante pendant 10~20min.
- 4. laver à l'eau froide.Laver à l'eau froide dans le flux pendant 1 minute.
- 5. la phosphatation.Phosphate avec une température moyenne (60 ℃ phosphate 10min), la solution de phosphate peut être des produits finis disponibles dans le commerce. Le processus ci-dessus peut également être remplacé par le sablage → lavage.
- 6. la passivation.Utiliser le médicament correspondant à la solution de phosphatation (fourni par le fabricant qui vend la solution de phosphatation) pendant 1 à 2 minutes à température ambiante.
- 7. électrophorèse anodique.Composition de l'électrolyte : peinture noire pour électrophorèse H08-1, fraction massique solide 9%~12%, fraction massique d'eau distillée 88%~91%. Tension : (70±10)V ; temps : 2~2,5min ; température de la laque : 15~35℃ ; valeur PH de la laque : 8~8,5. Veillez à déconnecter la pièce de l'entrée et de la sortie de la cuve. Le courant diminuera progressivement avec l'épaississement du film de peinture pendant le processus d'électrophorèse.
- 8. laver à l'eau.Laver à l'eau froide.
- 9. séchage.Il peut être cuit au four à (165±5)°C pendant 40-60 minutes.
VI. PVD
PVD est l'abréviation de Physical Vapor Deposition (dépôt physique en phase vapeur), qui fait référence à l'utilisation de la technologie de décharge d'arc à basse tension et à courant élevé dans des conditions de vide, à l'utilisation de la décharge de gaz pour faire évaporer le matériau cible et à l'ionisation des matériaux et des gaz évaporés, et à l'utilisation de l'effet d'accélération du champ électrique pour faire en sorte que les matériaux évaporés et leurs produits de réaction se déposent sur la pièce à usiner.La technologie de dépôt physique en phase vapeur est un processus simple, qui améliore l'environnement, ne pollue pas, nécessite moins de consommables, produit un film uniforme et dense et assure une forte liaison avec le substrat. Cette technologie est largement utilisée dans l'aérospatiale, l'électronique, l'optique, les machines, la construction, l'industrie légère, la métallurgie, les matériaux et d'autres domaines. Elle permet de préparer des couches de film résistantes à l'usure et à la corrosion, décoratives, conductrices d'électricité, isolantes, photoconductrices, piézoélectriques, magnétiques, lubrifiantes, supraconductrices, etc.
VII. Placage électrolytique
(Electroplating) est le procédé qui consiste à déposer une fine couche d'autres métaux ou alliages sur la surface de certains métaux en utilisant le principe de l'électrolyse.Il s'agit de l'utilisation de l'électrolyse pour fabriquer du métal ou d'autres matériaux sur la surface des pièces attachées à une couche de film métallique afin de prévenir l'oxydation du métal (telle que la corrosion), d'améliorer la résistance à l'usure, la conductivité électrique, la réflectivité, la résistance à la corrosion (sulfate de cuivre, etc.) et de renforcer le rôle de l'esthétique et ainsi de suite. Une grande partie de la couche extérieure de la pièce est également galvanisée.
VIII. La gravure
Habituellement appelée gravure photochimique, la gravure photochimique désigne l'exposition de la plaque, après développement, pour être gravée dans la zone de retrait du film protecteur, en contact avec la gravure de la solution chimique, pour réaliser le rôle de la dissolution de la corrosion, la formation de concavité-convexité ou le creusement de la formation de l'effet. Procédé : méthode d'exposition :Ingénierie selon les graphiques pour ouvrir la préparation taille - préparation du matériel - nettoyage du matériel - séchage → film ou revêtement → séchage → exposition → développement → séchage - gravure → hors du film → OKMéthode de sérigraphie :Ouverture→Plaque de nettoyage (acier inoxydable et autres matériaux métalliques)→Sérigraphie→Etching→De-filmage→OK
IX. Pulvérisation
La pulvérisation est une méthode d'application de la peinture sur la surface de l'objet à recouvrir au moyen d'un pistolet ou d'un atomiseur à disque, qui se disperse en fines gouttelettes uniformes sous l'effet de la pression ou de la force centrifuge.On peut distinguer la pulvérisation pneumatique, la pulvérisation sans air, la pulvérisation électrostatique et les formes de pulvérisation de base susmentionnées de divers dérivés, tels que la pulvérisation atomisée à haut débit et à basse pression, la pulvérisation thermique, la pulvérisation automatique, la pulvérisation multigroupe, etc. L'opération de pulvérisation a un rendement de production élevé, convient au travail manuel et à l'automatisation de la production industrielle, a un large éventail d'applications, principalement dans les domaines de la quincaillerie, du plastique, de l'ameublement, de l'armée, des navires et autres, et est désormais l'application la plus courante d'une méthode de revêtement ; l'opération de pulvérisation requiert des exigences environnementales d'un million à cent niveaux d'atelier sans poussière, l'équipement de pulvérisation est constitué de pistolets de pulvérisation, de cabines de peinture, d'une salle de peinture, d'un four de durcissement / four de séchage, d'un équipement de fonctionnement du convoyeur de pièces à pulvériser, d'un équipement d'élimination du brouillard et d'un équipement de traitement des eaux usées, des gaz d'échappement, etc. Équipement de traitement des eaux usées, des gaz d'échappement, etc. La pulvérisation atomisée à haut débit et à basse pression est caractérisée par une faible pression d'air de pulvérisation et une faible vitesse du jet d'air. La faible vitesse d'écoulement de la peinture atomisée améliore le rebondissement de la peinture sur la surface de l'objet à peindre. Le taux d'absorption de la peinture passe de 30%~40% pour une pulvérisation à air normale à 65%~85%. Dans la finition légère du cuir, la finition est pulvérisée sur la surface du cuir à l'aide d'un pistolet de pulvérisation ou d'un pulvérisateur de bouillie.
X. Gravure au laser
Également connu sous le nom de gravure laser ou de marquage laser, il s'agit d'un processus de traitement de surface utilisant des principes optiques.L'utilisation d'un faisceau laser focalisé de haute intensité émis par un laser au point focal. Le matériau est oxydé et traité. Le marquage a pour effet de révéler la matière profonde par l'évaporation de la matière superficielle, ou de produire des traces par les modifications chimiques et physiques de la matière superficielle provoquées par l'énergie lumineuse, ou de "graver" des traces par la combustion d'une partie de la matière par l'énergie lumineuse, ou de révéler la gravure souhaitée d'une figure ou d'un texte par la combustion d'une partie de la matière par l'énergie lumineuse.