Formation de fissures dans les moyeux de roue en aluminium coulé à basse pression : causes et mesures d'amélioration
Temps de publication:2025-01-27 Trier par:Le blog Nombre de vues:1254
coulée à basse pression Elle permet d'atteindre un degré élevé de mécanisation et d'automatisation, d'augmenter la productivité (10 ~ 15 types/h), de réduire de nombreux facteurs humains défavorables dans le processus de production, d'améliorer le taux de produits finis, de réduire considérablement l'intensité du travail des ouvriers. Cependant, la qualité des pièces moulées à basse pression dépend du plan de traitement, des paramètres de traitement, de la structure du moule, de l'opération manuelle et d'autres facteurs ; toute conception déraisonnable ou opération incorrecte du lien peut entraîner des défauts dans les pièces moulées à basse pression. La génération de fissures dans les roues en aluminium est un facteur important qui affecte le coût de production et la productivité des entreprises. Il est donc particulièrement important de discuter des causes des fissures dans les roues en aluminium coulées à basse pression. Ensuite, je discuterai avec vous de l'usine de moulage à basse pression en Chine. aluminium Formation de fissures sur les roues automobiles et mesures pour les éliminer.
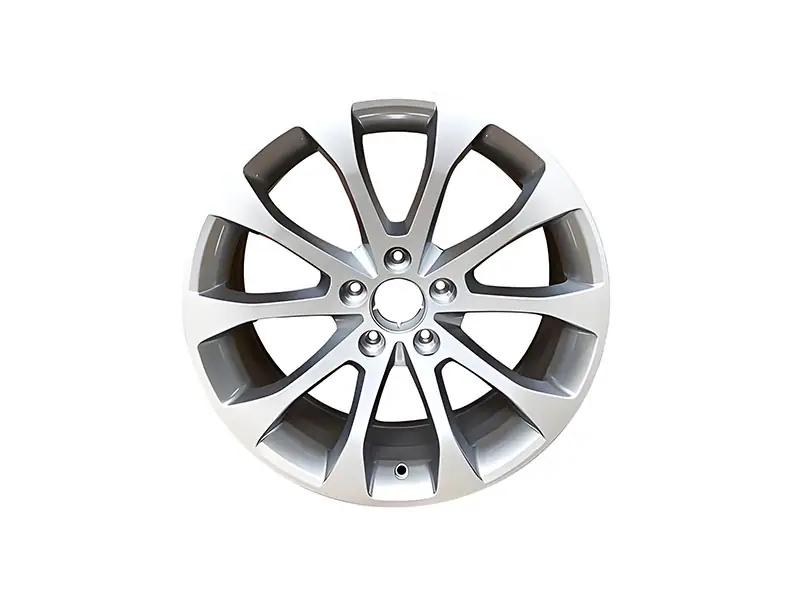
Qu'est-ce qu'une roue de coulée à basse pression ?
Les roues moulées à basse pression sont fabriquées à l'aide de la technologie de moulage à basse pression, qui permet d'obtenir une densité et une résistance élevées, ainsi qu'un bon contrôle de la qualité. Le processus consiste à injecter un alliage liquide dans un moule à basse pression, où l'alliage se refroidit et se solidifie. Le moulage à basse pression produit des roues à haute densité, à structure homogène, à bonne résistance et ténacité, et convient à la production de masse.
Le processus de production est divisé en plusieurs étapes : tout d'abord, l'alliage liquide est injecté dans le moule ; ensuite, l'alliage est refroidi et solidifié ; enfin, la roue est soumise à un traitement thermique et à des processus de finition et de peinture. Ce processus permet de réduire les bulles d'air et les impuretés, d'améliorer la résistance et la précision et de renforcer la sécurité de la roue.
aveccoulée gravitationnelleLa coulée à basse pression est plus efficace et produit des produits de meilleure qualité que la coulée à basse pression. La coulée par gravité s'appuie sur la gravité pour faire couler le métal, ce qui peut entraîner une distribution inégale, compromettant ainsi la qualité et la sécurité. Le moulage à basse pression contrôle l'écoulement de l'alliage d'aluminium en appliquant une pression, ce qui garantit la précision et la solidité de la roue.
Par conséquent, les roues moulées à basse pression prennent de plus en plus d'importance dans la construction automobile, car elles offrent une efficacité, une qualité et une sécurité élevées.
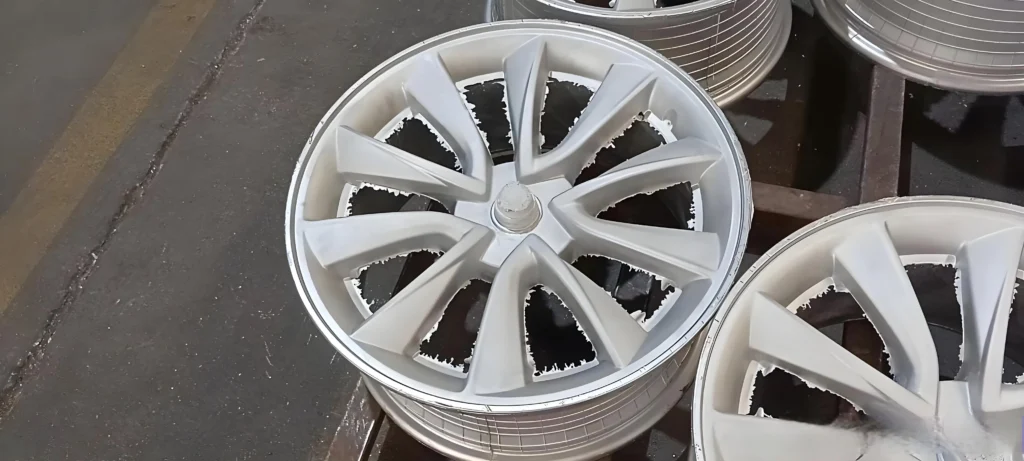
Avantage technologique des roues de coulée à basse pression et remodelage de la valeur industrielle
La révolution de la fabrication de précision stimulée par l'automatisation mécanique
La technologie de coulée à basse pression, grâce à un degré élevé de mécanisation et d'automatisation, a atteint une capacité de production stable de 10 à 15 pièces par heure, ce qui représente une augmentation d'environ 301 tonnes par rapport à l'efficacité de la coulée par gravité traditionnelle. Son principe de base consiste à utiliser un gaz à basse pression (0,02-0,08 MPa) pour presser les alliages d'aluminium liquides dans les cavités du moule en douceur, ce qui évite les problèmes de gaz enroulés et de scories oxydées, causés par le métal liquide qui s'écoule librement dans le cas de la coulée par gravité. Prenons l'exemple d'un projet de production de masse de roues de véhicules à énergie nouvelle : grâce à l'introduction d'une ligne de coulée à basse pression entièrement automatique, le rendement du produit est passé de 82% à 96%, tandis que les coûts de main-d'œuvre ont été réduits de 45%. La combinaison d'un système de contrôle de la température du moule en boucle fermée et de capteurs de pression intelligents a permis d'affiner le grain de la coulée au niveau du micron, et la résistance à la fatigue par flexion dynamique du moyeu de roue a dépassé un million de cycles, ce qui répond pleinement aux exigences de légèreté et de sécurité des véhicules de haut de gamme. Ce moyeu répond parfaitement à la double exigence de légèreté et de sécurité des modèles haut de gamme.
Diagnostic interdisciplinaire des causes de fissures dans les moyeux de coulée à basse pression
Corrélation profonde entre la morphologie des fissures et les mécanismes de rupture
Dans le processus de production des roues en alliage d'aluminium, la formation de fissures est souvent le résultat du couplage de plusieurs facteurs, tels que les propriétés des matériaux, la conception structurelle et les paramètres du processus. D'après l'analyse de la mécanique des fractures, les fissures des roues peuvent être divisées en trois types principaux :
- Fissuration thermique (défauts de solidification)Elle se produit principalement au niveau du joint rayon-jante et se manifeste sous la forme d'une fissure réticulée répartie le long des limites de grain. Le métal liquide résiduel entre le squelette dendritique à la fin de la solidification ne peut pas résister à la contrainte de contraction, et les cas typiques montrent que la probabilité de fissuration thermique augmente de 60% lorsque le taux de refroidissement local dépasse 4°C/s.
- Fissuration à froid (contrainte mécanique)La fracture se trouve généralement à la racine de la bride du moyeu et présente les caractéristiques typiques d'une fracture fragile. L'analyse de la rupture d'un moyeu de véhicule utilitaire a montré que le métal solidifié restant dans le tube de levage pendant le démoulage a soumis le moulage à une contrainte de traction de plus de 200 MPa, ce qui a directement déclenché une fissure pénétrante.
- Fissuration par corrosion sous contrainte (interaction avec l'environnement)Dans les environnements côtiers à forte humidité, les contraintes résiduelles dans le moyeu agissent en synergie avec les ions de chlorure pour provoquer des fissures qui s'étendent lentement le long des joints de grains. Ces fissures présentent une morphologie de bifurcation dendritique distinctive en observation microscopique.
Analyse systématique des facteurs clés de la fracturation
1. l'amplification mécanique des défauts de conception des structures
- Concentration des contraintes dans les angles vifsSi le rayon du congé intérieur dans la zone de transition du rayon de la roue est inférieur à 3 mm, le facteur de concentration des contraintes (Kt) peut atteindre 3,5-4,2, ce qui est bien supérieur à la limite d'élasticité de l'alliage d'aluminium A356-T6 (220 MPa). Les données de simulation d'une roue sportive montrent qu'après avoir optimisé l'angle R de 2 mm à 5 mm, la contrainte équivalente maximale est réduite de 315 MPa à 185 MPa.
- Effet de mutation de l'épaisseur de la paroiLorsque la différence d'épaisseur entre des zones voisines dépasse 3:1, le gradient de contrainte thermique généré pendant le processus de refroidissement peut dépasser la limite de résistance à la traction du matériau. Le cas de rupture d'un moyeu de roue léger montre que l'épaisseur du joint jante-rayon a été réduite de 8 mm à 3 mm, ce qui a entraîné un pic de contrainte locale de 280 MPa.
2. le risque systémique d'inadéquation des paramètres du processus
- Une fenêtre de temps étroite pour maintenir la pressionLe temps de maintien de moins de 15 secondes entraîne l'interruption de la contraction et la formation d'un relâchement de la contraction, tandis que plus de 40 secondes créent une résistance mécanique à la solidification du métal dans le tube ascendant. Un projet de test DOE a confirmé que lorsque le temps de maintien est contrôlé entre 25 et 30 secondes, le taux de fissuration est réduit de 7,2% à 0,8%.
- Contrôle incorrect du taux de remplissageLorsque la vitesse de remplissage dépasse 120 mm/s, la probabilité de rouleaux de gaz turbulents dans le métal liquide augmente de 40%, et les défauts microscopiques formés par la rétention de gaz deviennent le point de départ de l'initiation des fissures. Le processus d'augmentation progressive (0,03MPa initial, 0,06MPa final) peut équilibrer efficacement la vitesse de remplissage et le risque de rouleaux de gaz.
3. les défis de l'équilibre dynamique dans la gestion thermique des moules
- gradient de température d'emballementLorsque la différence de température du moule dépasse 50℃, le taux de différence de retrait de solidification de chaque région de la coulée dépasse 0,8%, ce qui induit une fissuration thermique. Une usine par l'implantation de point de surveillance de la température du moule a trouvé que la fluctuation de la température dans la zone de rayon jusqu'à ± 30 ℃, après l'installation du système de contrôle de la température de partition différence de température est stable dans ± 5 ℃.
- Mauvaise sélection de l'agent de refroidissementLe refroidissement traditionnel à l'eau peut facilement provoquer une chute soudaine de la température de surface du moule. L'utilisation de la technologie de refroidissement mixte par aérosol permet de contrôler avec précision la vitesse de refroidissement de 3 à 8 ℃ / s, afin d'éviter les contraintes de trempe dues à un refroidissement rapide.
Solutions d'ingénierie pour la prévention des fissures
1. système optimisé pour la dynamique des systèmes de levage
- Reconstruction de la géométrie du coureurLe diamètre du tuyau de levage a été augmenté de Φ60mm à Φ85mm, et avec la conception de la glissière inclinée à 30°, le débit du liquide métallique a été stabilisé à 0,8-1,0m/s. La pratique d'un projet a montré que ce mouvement a réduit la probabilité de gel du tuyau de levage de 70%.
- Amélioration de l'isolationAdoption d'un manchon de préservation de la chaleur nano-microporeux (conductivité thermique ≤ 0,1W/m-K), qui prolonge la limite de temps de la préservation de la chaleur de 40% par rapport au matériau traditionnel en fibre céramique pour assurer la fluidité du canal de rétraction.
2. voie d'optimisation bionique pour la conception structurelle
- Technologie de cartographie des flux de stressLa roue légère a perdu 12% de poids grâce à cette technique, tandis que la rigidité à la flexion a été augmentée de 18%. Cette technique a permis à une roue légère de perdre 12% de poids, tandis que la rigidité à la flexion a augmenté de 18%.
- règle de transition du gradientLa conception d'une zone de transition conique 1:4 dans la zone de mutation de l'épaisseur de la paroi et l'ajout de rainures de détente d'une profondeur de 1,5 mm à la racine du rayon ont permis de réduire le pic de contrainte local de 295MPa à 175MPa.
3. innovation en matière de système intelligent de contrôle de la température du moule
- Régulation couplée de la température multizoneLe système de contrôle de la température : a mis au point un module de contrôle de la température indépendant à six zones, la zone de la jante étant réglée à 320°C (pour favoriser le rétrécissement par maquillage) et la zone des rayons étant maintenue à 280°C (pour inhiber la fissuration thermique). Dans la production de masse d'une roue de marque haut de gamme, ce système permet d'atteindre une uniformité de température du moule de ±3℃.
- Stratégie de refroidissement dynamiqueLe refroidissement par air est utilisé pour maintenir la température du moule pendant la phase de remplissage, et le refroidissement par brouillard est utilisé pour accélérer la solidification pendant la phase de maintien, ce qui raccourcit l'ensemble du cycle de production de 8 secondes.
Pratiques d'innovation de processus de Ningbo Hexin
Dans le cadre de la coopération avec une marque de luxe allemande, l'équipe de He Xin a atteint la référence industrielle grâce à trois percées technologiques clés :
- Technologie de formation de composites par moulage et filage à basse pressionLa résistance à l'impact radial du moyeu de la roue est augmentée de 35% grâce à un processus de filage superposé dans la zone de la jante, de sorte que le grain est orienté le long de la circonférence.
- Système de chauffage par gradient (technologie brevetée)Le moule est recouvert d'un revêtement en nitrure de titane de 0,2 mm d'épaisseur, qui, associé au dispositif de chauffage par induction, permet un contrôle précis de la température avec une différence de température de ≤5℃ dans la zone du rayon.
- Plate-forme de simulation numérique de processusL'intégration de MAGMAsoft et du système ANSYS permet de réduire le nombre d'essais de moulage de 12 à 3, ce qui raccourcit le cycle de développement de 60%.
Choisir la bonne installation de roues de coulée à basse pression
Les fournisseurs de qualité doivent posséder quatre compétences de base :
- Base de données des matériauxAccumulation de dizaines de milliers d'ensembles de paramètres de processus et de relations de cartographie des propriétés des alliages, mise en correspondance rapide des meilleures solutions en matière de matériaux.
- Contrôle de la qualité de l'ensemble du processusMise en place de 12 points de contrôle de la qualité, depuis l'analyse de la pureté du lingot (teneur en Fe ≤ 0,15%) jusqu'à la détection des défauts par rayons X (norme ASTM E505).
- production flexibleSystème de changement rapide de moule compatible avec les roues de 16 à 24 pouces, temps de changement <45 minutes
- fabrication écologiqueTaux de récupération des copeaux d'aluminium ≥95%, consommation d'énergie par unité de produit inférieure de 28% à la moyenne de l'industrie.
Questions fréquemment posées et réponses
1) Pourquoi les roues coulées à basse pression sont-elles mieux adaptées aux véhicules à énergie nouvelle ?
Sa haute densification peut supporter le couple instantané du moteur (≥3000N-m), tandis que la caractéristique de légèreté (40% de réduction de poids par rapport aux roues en acier) améliore directement l'autonomie de 5%-8%.
2. comment déterminer la cause des fissures par analyse métallographique ?
- Fissuration thermique : présence d'un film d'oxyde continu aux joints de grains, fissures en forme de réseau zigzag.
- Fracture froide : la fracture est droite, des étapes de solubilisation claires sont visibles.
- Corrosion sous contrainte : présence d'un enrichissement en Cl élémentaire aux extrémités des fissures (détection EDS)
3) Comment la durée de vie du moule affecte-t-elle le taux de fissuration ?
Lorsque le moule est utilisé pendant plus de 5 000 cycles, des microfissures superficielles peuvent entraîner une augmentation de la résistance au démoulage du 25%, nécessitant une réparation régulière du revêtement au laser (rétablissement de la dureté de la surface à HRC 45 ou plus).
4) Quelles sont les orientations futures du développement technologique ?
L'intelligence artificielle a été introduite dans l'optimisation du processus, avec des algorithmes d'apprentissage automatique régulant le profil de pression en temps réel, dans le but de contrôler le taux de fissuration à moins de 0,11 TP3T, tandis que la productivité a été augmentée de 201 TP3T supplémentaires.