Classification des procédés de fabrication des métaux
Temps de publication:2024-08-03 Trier par:Le blog Nombre de vues:1366
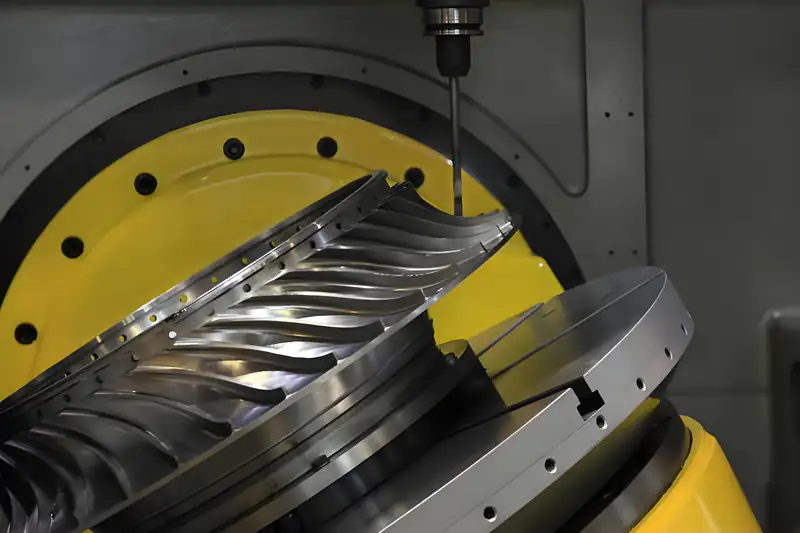
Le travail à chaud comprend le moulage, le forgeage et le soudage. Le travail à froid, également connu sous le nom de processus de coupe des métaux, comprend le processus de coupe des outils (qui comprend le processus de tournage, le processus de forage et d'alésage, le rabotage, l'insertion, le brochage, le processus de fraisage, le processus de coupe abrasive ; le traitement des dents d'engrenage). Les éléments suivants sont brièvement présentés.
(i) Coulée
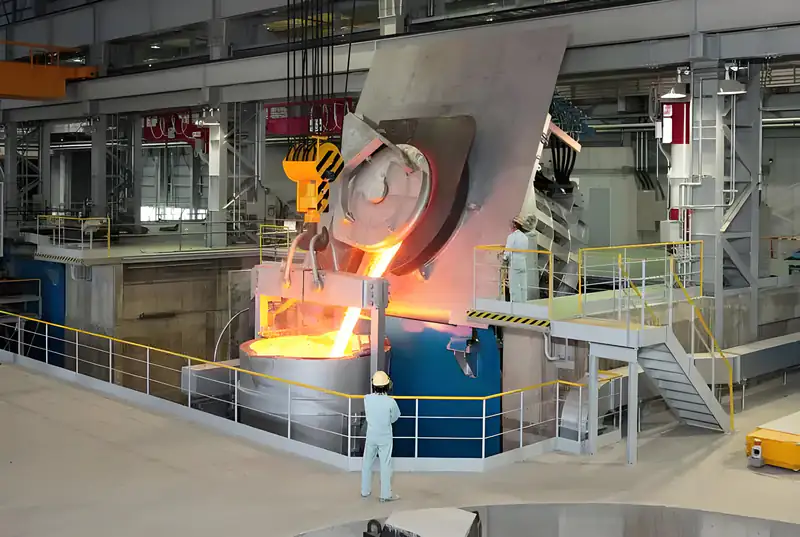
Le processus de coulée consiste à verser du métal liquide dans un moule de coulée et à le laisser refroidir pour obtenir un moulage d'une certaine forme et d'un certain caractère. Il s'agit de la méthode de mise en forme du métal à l'état liquide. Le moulage permet de produire des billettes de formes complexes, notamment avec des cavités internes complexes, de taille et de poids illimités. La production d'une seule pièce peut également être une production de masse, l'utilisation de la plupart des matériaux provenant d'un large éventail de sources, des prix bas, mais aussi des pièces de rebut et des déchets disponibles, de sorte que le coût est faible. Les pièces moulées et les pièces proches de la forme et de la taille de la tolérance de traitement sont faibles. L'inconvénient des pièces moulées est qu'il existe de nombreux processus et que le contrôle des processus est difficile. En raison des contraintes internes dues au refroidissement du métal, les défauts sont fréquents, de sorte que la qualité n'est pas stable ; en raison de son organisation interne grossièrement inégale, ses propriétés mécaniques ne sont pas aussi élevées que celles des pièces forgées. Il existe également des problèmes de forte intensité de main-d'œuvre et de mauvaises conditions de travail.
Les méthodes de production du moulage sont divisées en deux catégories : le moulage en sable et le moulage spécial, le moulage en sable étant la principale méthode.
1,moulage en sable La plupart des moules en sable sont encore fabriqués à la main. Le moulage en sable est principalement utilisé pour la production de fonte, d'acier moulé, de cuivre moulé, d'aluminium moulé et d'autres matériaux. La conception structurelle des pièces coulées doit tenir compte du processus de coulée et des exigences de performance de la métallurgie, afin d'éviter la production de trous de retrait, de relâchement de retrait, de sous-dosage, de ségrégation à froid, de déformation, de fissures et d'autres défauts ; il convient de prêter attention aux points suivants : ① les pièces coulées doivent avoir une épaisseur de paroi et une inclinaison structurelle raisonnables, l'épaisseur de la paroi de la pièce devant être aussi uniforme que possible. ② raccordement des parois de la pièce moulée : le raccordement des parois de la pièce moulée doit être structuré avec des coins arrondis. Éviter les raccordements en croix et à angle aigu, les raccordements à paroi épaisse et à paroi mince pour assurer une transition graduelle. ③ Les pièces moulées doivent éviter les plans horizontaux excessifs. ④ Afin d'éviter le gauchissement et la déformation de la pièce moulée, pour les grandes pièces moulées plates et les longues boîtes dont l'épaisseur de paroi est inégale, il convient de leur donner une forme symétrique ou d'augmenter la plaque nervurée afin d'améliorer leur rigidité. ⑤ Éviter que le retrait de la pièce moulée ne soit entravé, comme dans le cas des pièces moulées courantes en forme de roue, dont les rayons sont en nombre pair et de forme linéaire. Cependant, pour les alliages ayant un retrait important, des fissures sont parfois produites en raison d'une contrainte excessive. Afin d'éviter les fissures, les rayons peuvent être courbés, afin d'absorber la déformation des rayons ou de la jante de la roue et de réduire les contraintes internes. (6) selon le principe de la solidification séquentielle, la structure de la coulée La coquille en acier moulé illustrée dans la figure, sera modifiée du côté droit de l'apparence de la coquille au fond de 76 mm pour maintenir une épaisseur de paroi uniforme, et augmenter progressivement l'épaisseur de la paroi jusqu'à la bride avec la bride, pour s'assurer que la coquille conformément à la solidification séquentielle, ne produit plus de défauts de rétrécissement.
2,Moulage de spécialités
- ① Le moulage par fusion, qui utilise la cire comme matériau de fabrication des moules, également connu sous le nom de "fabrication à la cire perdue", permet de couler une grande variété de métaux ferreux et non ferreux.
- ②moulage de métaux Le modèle peut être utilisé 40 000 fois, le moulage a une bonne précision (jusqu'à IT12~IT14), la surface est lisse et propre, il peut être utilisé avec moins ou pas de traitement, et il peut être mécanisé.
- (iii)coulée sous pression Machine de coulée sous pression : Chambre de pression de la machine de coulée sous pression versant du métal liquide ou semi-liquide, remplissage de type Pu, et dans la formation et la cristallisation à haute pression. La pression de coulée sous pression couramment utilisée est de 5 ~ 150MPa, le débit de métal est de 5 ~ 100m / s. Haute efficacité et facile à automatiser, la qualité du produit est bonne, pour obtenir un traitement avec moins de copeaux et sans copeaux, à faible coût. ④coulée à basse pression .
- ⑤ Coulée centrifuge : le métal liquide est ajouté à un moule de coulée en rotation.
(ii) Forgeage
Incluant le forgeage et l'emboutissage, la déformation plastique du métal sous l'action de forces extérieures, généralement à haute température. Le forgeage se divise en deux catégories : le forgeage libre et le forgeage sous pression. L'objet du processus d'emboutissage est la tôle, généralement à température ambiante, donc également connu sous le nom d'emboutissage de la tôle ou d'emboutissage à froid.
1. exercice libre
La billette est placée sur l'équipement (marteau de forgeage libre ou presse hydraulique) entre le haut et le bas contre le fer, parce que la billette dans la pression s'écoule librement, c'est ce qu'on appelle le forgeage libre. En fonction de l'utilisation de l'équipement et de la nature de la force de forgeage, le forgeage libre est divisé en deux catégories : le forgeage libre sur le marteau et le forgeage libre sur la presse hydraulique, les grandes pièces devant être forgées dans la presse hydraulique. Les produits de forgeage libre présentent une faible précision dimensionnelle, une consommation de matériaux, une faible productivité, de mauvaises conditions de travail, une intensité de travail élevée, et ne peuvent être produits qu'en une seule pièce, la production en petits lots est raisonnable.
2、Die forgeage
Lors du matriçage, l'ébauche est placée dans la chambre de matriçage, de sorte que la pièce se forme sous l'effet de la pression. En fonction de l'utilisation de différents équipements, le matriçage est divisé en matriçage au marteau, presse à manivelle sur le matriçage, machine de matriçage plat, presse à vis sur le matriçage et autres équipements spéciaux sur le matriçage. La productivité du matriçage est élevée, la surface de la pièce est propre, la précision dimensionnelle est élevée, l'efficacité des matériaux est élevée, la distribution du flux de matriçage est plus raisonnable, la durée de vie est améliorée, des pièces complexes souples peuvent être forgées, l'opération est simple, la mécanisation est facile à réaliser, le coût est faible, l'opération est couramment utilisée pour les petites et moyennes pièces forgées de la production de masse.
3、Emboutissage de la feuille
La tôle est traitée à l'aide d'une matrice montée sur un banc de presse pour la déformer ou la séparer afin d'obtenir une pièce ou une ébauche. Les ébauches de tôle sont généralement des plaques minces d'une épaisseur de 1 à 2 mm ou moins, généralement sans chauffage. Les matières premières utilisées pour l'emboutissage des tôles doivent avoir une bonne plasticité et une faible résistance à la déformation, comme l'acier à faible teneur en carbone, l'acier allié, le cuivre et l'aluminium. Les pièces embouties sont légères, ont une bonne rigidité, une structure légère, une qualité stable et une bonne interchangeabilité. L'opération est simple, facile à mécaniser et à automatiser, et peu coûteuse. En raison du coût élevé de la fabrication des moules d'emboutissage, la production de masse n'est que raisonnable.
4) Autres méthodes de traitement sous pression
La formation par extrusion, de sorte que le département de déformation du métal difficile à mettre Υ Hydra, peut fabriquer une variété de matériaux, une variété de formes de pièces métalliques, et une haute précision, de bonnes propriétés mécaniques, peut être automatisée mécaniquement. Formage par laminage : tel que le laminage, le laminage à chaud d'engrenages, le laminage d'anneaux. Forgeage de précision, forgeage en chaîne, forgeage à marteau à grande vitesse, etc.
(iii) Coupe
Le processus de coupe est divisé en deux catégories : le serrage et l'usinage. Le serrage est généralement effectué à la main, principalement pour le traçage, l'ébarbage, le sciage, le limage, le grattage, le perçage et l'alésage, le taraudage et le flambage, etc. L'usinage dépend de l'utilisation d'outils de coupe et se divise en deux catégories : l'une consiste à utiliser des outils pour le traitement, tels que le tournage, le perçage, l'alésage, le rabotage, le fraisage, etc. ; l'autre consiste à utiliser des abrasifs pour le traitement, tels que la rectification, la rectification articulée, la rectification, l'ultrafinition, etc. L'usinage doit disposer d'outils, tels que des outils de tournage, des outils de rabotage, des outils d'insertion, des outils tranchants, des outils d'alésage, etc.
1、Tournage
Les machines-outils de tournage comprennent les machines-outils générales, les tours verticaux, les tours à tourelle, les tours à profiler, les tours automatiques et divers tours à usage spécifique. Le tournage peut traiter la surface de la face frontale, du cercle extérieur, du cercle intérieur, du cône, du filetage, de la surface de formage rotative, de la rainure rotative et du moletage, etc., l'utilisation d'une large gamme de précision de surface d'usinage et la facilité de garantir que la surface des pièces traitées par la précision de position de la surface, l'efficacité de production élevée, les coûts de production faibles.
2、Travaux de forage et d'alésage
① Traitement des machines de forage : les équipements couramment utilisés sont les machines de forage de bureau, les machines de forage verticales et les machines de forage pour culbuteurs, etc. ② Traitement des aléseuses : l'équipement principal est une aléseuse horizontale. La machine à aléser peut effectuer des opérations de perçage, d'alésage, d'alésage, de rainurage, de cercle de tournage, de face de tournage et de plan de fraisage, dont l'alésage est l'opération principale. La machine à aléser étant dotée d'un dispositif de positionnement précis, elle convient au système de positionnement et de traitement des trous des sièges de boîtes, des supports et d'autres formes de grandes pièces complexes ; c'est l'équipement clé pour l'usinage, les autres équipements ne pouvant être remplacés. La gamme de traitement de la machine à aléser est large, elle permet d'obtenir une grande précision de traitement et une faible rugosité, mais son inconvénient est sa faible productivité.
3. rabotage, interpolation et brochage
①Le rabotage est utilisé pour traiter les surfaces planes, et les raboteuses sont divisées en deux types : les raboteuses à tête de taureau et les raboteuses à tête de dragon. La raboteuse peut traiter le plan horizontal, le plan vertical, le plan incliné, mais aussi la rainure (rainure à angle droit, rainure en forme de V et de T, rainure en queue d'aronde) et la surface de formage linéaire. Le mouvement principal de la raboteuse est un mouvement linéaire alternatif, il y a des pistes vides, et chaque mouvement alternatif est accompagné de deux impacts, ce qui limite la vitesse de rabotage et réduit la productivité.
L'insertion peut être considérée comme une "raboteuse verticale", qui est principalement utilisée pour l'usinage des rainures de clavettes dans les trous, les trous carrés, les trous polygonaux, les trous cannelés et les surfaces externes de certaines pièces. L'équipement utilisé pour la coupe par insertion est une machine d'insertion.
③L'équipement pour le brochage est une brocheuse. Le mouvement rectiligne de la broche est le mouvement principal. Il n'y a pas de mouvement d'avance du brochage, l'avance est obtenue par l'élévation de chaque dent de la fraise. Le brochage peut donc être considéré comme un arrangement séquentiel haut et bas, plus d'un couteau de rabotage pour la maladie du rabotage Le brochage est généralement utilisé pour la finition, et un voyage pour atteindre les exigences de précision, peut être traité plan de brochage, arc semi-circulaire et une certaine combinaison de surfaces. Le brochage est un outil façonné, le brochage une fois pour compléter la coupe grossière, la coupe de précision, plus précise et le travail de réparation, c'est une méthode de finition, à haute efficacité. Mais la fabrication de la broche est complexe, son coût élevé, elle ne peut pas traiter les trous en escalier, les trous borgnes et les trous surdimensionnés, elle convient uniquement au traitement d'une spécification du trou ou de la rainure de clavette.
4, traitement simultané du broyage
Le fraisage est réalisé par la rotation et le <mouvement de la fraise, qui est l'une des principales méthodes d'usinage plan. L'équipement comprend une fraiseuse horizontale, une fraiseuse verticale, une fraiseuse à portique, une fraiseuse à outil et toutes sortes de fraiseuses spéciales. La fraiseuse peut usiner des plans (horizontaux, verticaux, obliques), des rainures (rainure à angle droit, rainure de clavette, rainure d'angle, rainure en queue d'aronde, rainure en forme de T, rainure en arc) et des surfaces de formage. Elle peut également effectuer le traitement des trous (y compris le perçage, l'alésage, l'alésage, l'alésage) et les travaux d'indexation.
5. Traitement de la coupe abrasive
Les abrasifs sont utilisés pour couper avec un grand nombre d'abrasifs répartis sur la surface de la meule. Les méthodes de rectification comprennent : la rectification cylindrique externe, la rectification cylindrique interne, la rectification plane, la rectification de filets, ainsi que les méthodes de rectification de haute précision et de haute efficacité : la rectification de précision, la rectification d'ultraprécision, la rectification de miroirs, la rectification à grande vitesse, la rectification de meules larges, la rectification de coupe profonde à avance lente, et les meules Jin J avec des meules en nitrure de bore cubique. Les rectifieuses universelles comprennent les rectifieuses cylindriques générales, les rectifieuses cylindriques universelles, les rectifieuses internes, les rectifieuses planes et les rectifieuses sans centre.
6、Légèreté de finition
La finition comprend la rectification, le rodage, la superfinition et le polissage. Meulage : entre la pièce à usiner et l'outil de recherche enduit d'abrasif, la pièce à usiner peut être entraînée en rotation par le tour, l'outil de recherche tenu à la main effectuant un mouvement axial de va-et-vient, souvent testé, jusqu'à ce qu'il soit qualifié. Le liquide de meulage est composé de paraffine, d'huile végétale ou de paraffine et d'huile. Le matériau le plus couramment utilisé pour les outils de recherche est la fonte. La quantité de meulage est généralement de 0,005 ~ 0,02 mm. Honage : tête de honage par un certain nombre de bandes de pierre à huile au lieu de l'outil de recherche, utilisé comme un trou dans le processus de finition. Ultrafinition : les bandes de pierre à huile avec des grains abrasifs très fins sont utilisées comme tête de meulage pour être légèrement pressées sur la surface de travail pour le traitement. Polissage : une roue douce enduite de pâte à polir tourne à grande vitesse pour effectuer une faible coupe sur la pièce afin de réduire la rugosité de la surface de travail et d'en améliorer la brillance.
7、Traitement de la forme de la dent d'engrenage
Les engrenages sont largement utilisés dans de nombreux types d'équipements mécaniques et d'instruments, et constituent un élément important de la transmission du mouvement et de la puissance. Les engrenages les plus courants sont les suivants : engrenages cylindriques à denture droite, engrenages cylindriques à denture hélicoïdale, engrenages cylindriques à denture hélicoïdale, engrenages coniques à denture droite et engrenages à vis sans fin. Pour que le mécanisme de transmission par engrenage fonctionne de manière précise, régulière et fiable, il faut choisir la courbe de profil de la dent appropriée, c'est-à-dire la courbe de la dent, l'utilisation actuelle de la courbe de la dent étant principalement la développante, la cycloïde et l'arc, etc. Si une ligne droite mobile dans le plan suit le rayon du cercle rb pour un roulement pur sans glissement, alors la trajectoire de tout point sur la ligne droite mobile a est appelée le rayon du cercle rb de la développante, le rayon du cercle rb est appelé le cercle de base, la ligne droite mobile est appelée l'occurrence de la ligne. La dent d'engrenage involue est formée par le même cercle de base de deux compositions en développante opposées. Involue ; tout point a1 normal doit être tangent au cercle de base, la forme de la développante et la taille du rayon du cercle de base, plus le rayon est petit, plus la courbure de la développante est petite, et vice versa, lorsque le rayon est infini, la développante devient une ligne droite, la ligne droite de la crémaillère peut être considérée comme le rayon de l'infini du cercle de base de la formation de la développante.
(1) Noms, paramètres de base et principales dimensions de chaque partie des engrenages cylindriques à denture droite
①Noms des départements Cercle du sommet de la dent--Le cercle passant par le sommet des dents de la roue de sélection est appelé cercle du sommet de la dent, et son diamètre est indiqué par da. Cercle de racine - Le cercle passant par la racine des dents de la roue de sélection est appelé cercle de racine et son diamètre est indiqué par df. Cercle d'indexation - Dans les engrenages standard, le cercle où l'épaisseur théorique de la dent est égale à la direction de la dent est appelé cercle d'indexation ; son diamètre est indiqué par d et son rayon par r. Le cercle d'indexation est situé entre le cercle du sommet de la dent et le cercle du pied de la dent, et constitue la base de calcul de la taille de l'engrenage. Cercle d'indexation de l'épaisseur de la dent - le cercle d'indexation sur la longueur de l'arc occupé par une dent de l'engrenage est appelé le degré de la dent du cercle d'indexation, avec s. Cercle d'indexation inter-dents - le cercle d'indexation sur la longueur d'arc occupée par une rainure de roue est appelé cercle d'indexation inter-dents, exprimé par e. Périapsis - la longueur d'arc entre les points correspondants de deux dents adjacentes sur le cercle d'indexation est appelée périapsis (périapsis du cercle d'indexation) et est exprimée par P. P = s + e. Hauteur du sommet de la dent - la distance radiale entre le sommet de la dent, le sommet du cercle et le cercle d'indexation est appelée hauteur du sommet de la dent et est exprimée par ha. Hauteur de la dent de travail - lorsque deux engrenages s'engrènent, la distance radiale entre le sommet des deux engrenages est appelée hauteur de la dent de travail, exprimée en hw. Jeu radial - lorsque deux engrenages s'engrènent, une dent m au sommet du cercle et l'autre dent au pied du cercle entre la distance radiale appelée jeu radial, exprimée en C.
② les paramètres de base de l'engrenage cylindrique à denture droite △ module = lorsque le nombre de dents de l'engrenage est Z, le diamètre du cercle d'indice et la circonférence P ont la relation suivante : ou A ce moment, de sorte que , alors d = mZ où : m - connu sous le nom de module, l'unité de mm. La conception des engrenages sera m comme un paramètre de base, de sorte que le calcul, le traitement et les essais des engrenages sont grandement facilités. la taille de la M reflète La taille de M reflète l'épaisseur de la denture, la taille et la capacité de charge de l'engrenage. La valeur i m a été normalisée, par exemple 0,1, 0,5, 1, 1,5, 2, 3 ......... conception selon les calculs de résistance de l'engrenage dérivés de la valeur du module, et ensuite sélectionnée selon les normes nationales. △ Angle de pression : L'angle entre la force normale F et sa vitesse en tout point K de la ligne de denture de la développante est appelé angle de pression k au point K. La développante déterminée, le rayon du cercle de base rb est une valeur fixe, l'angle de pression en plusieurs points de la développante est différent, et plus on s'éloigne du cercle de base, plus l'angle de pression est grand. L'angle de pression du point A sur le cercle d'indexation est généralement appelé "angle de pression". Cette valeur a été normalisée et est souvent fixée à =20°. Les conditions d'engrènement correctes pour les engrenages en développante sont que le module et l'angle de pression des deux engrenages doivent être égaux, et que le module m et l'angle de pression de l'outil doivent également être identiques à ceux de l'engrenage à usiner dans le processus de denture. Une fois le nombre de dents Z et le module m déterminés, la géométrie des engrenages peut être déterminée en plusieurs parties, dont les formules ont été omises.
(2) Usinage des engrenages cylindriques Il existe deux types de méthodes d'usinage : le formage et la rectification. La méthode de formage fait référence au traitement sur la fraiseuse. Pour les engrenages cylindriques à denture droite, lorsque m < 8, on utilise généralement une fraise à module en forme de disque dans la fraiseuse horizontale. Lorsque m≥8, elle est réalisée sur une fraiseuse verticale. La méthode de rectification consiste à utiliser la fraise à engrenages et le mouvement d'engrènement de l'engrenage à tailler, pour découper la forme de la dent sur une machine-outil spéciale. Les méthodes les plus couramment utilisées sont l'insertion d'engrenages sur des machines à façonner les engrenages et le taillage sur des machines à tailler les engrenages.
(3) Finition des engrenages cylindriques Le fraisage, l'insertion d'engrenages et le taillage font partie du traitement de la forme de la dent, et il faut ensuite procéder à la finition, afin d'améliorer encore la précision. Les méthodes de finition du profil de la dent comprennent l'arasage, le façonnage et la rectification de la dent.
8、Découpe au laser
découpe au laser Il s'agit de l'utilisation d'un laser à haute densité d'énergie, dont le diamètre est aussi petit que possible, qui se concentre sur un endroit pour produire une température élevée, qui permet de fondre, de vaporiser, d'ablater ou d'atteindre le point d'ignition, et qui, en même temps, avec l'aide d'un flux d'air à grande vitesse coaxial avec le faisceau, souffle le matériau fondu, de manière à obtenir la découpe de la pièce à usiner. La découpe laser est l'une des méthodes de découpe thermique.
(iv) Technologie d'impression 3D des métaux
huile de cuisson Impression 3D Il s'agit d'un procédé de fabrication métallique de pointe, qui permet de construire avec précision des structures tridimensionnelles complexes sous contrôle informatique en accumulant couche par couche des poudres ou des fils métalliques, ce qui permet de dépasser les limites du traitement soustractif et isotopique traditionnel et d'élargir considérablement la liberté de conception et les limites de l'application des matériaux.
Les principales technologies d'impression 3D de métaux sont les suivantes :
- Fusion et frittage sélectifs par laser (SLM/SLS)
- Fusion sélective par faisceau d'électrons (EBSM)
- Mise en forme de l'enveloppe au laser (LENS)
La technologie d'impression 3D de métaux peut être façonnée directement sans moule, ce qui permet de réaliser des conceptions personnalisées et de produire des structures complexes, avec une grande efficacité, une faible consommation, un faible coût et d'autres avantages.