Procédé de moulage en sable
Temps de publication:2024-10-08 Trier par:Le blog Nombre de vues:1848
Qu'est-ce que le moulage en sable ?
moulage en sable Le moulage en sable, également connu sous le nom de "moulage en sable", est une méthode de moulage ancestrale qui trouve de nombreuses applications dans le monde entier. Il s'agit d'une méthode de production de pièces moulées utilisant du sable lié à l'argile (ou des moules en sable fabriqués à partir d'autres matériaux tels que le gypse et la résine de silicone) comme matériau de moulage. Le principe consiste à tirer parti de la souplesse et de la facilité de moulage du moule en sable, à y verser le métal en fusion et, lorsque le métal s'est solidifié, à casser le moule en sable afin d'obtenir la pièce moulée souhaitée. Appliqué à une variété de métaux, le moulage en sable de l'aluminium, le moulage en sable du fer, le moulage en sable du cuivre, cède maintenant la place au moulage en sable de la Chine.aluminiumfonderieNingbo HexinLe processus de moulage au sable est expliqué en détail.
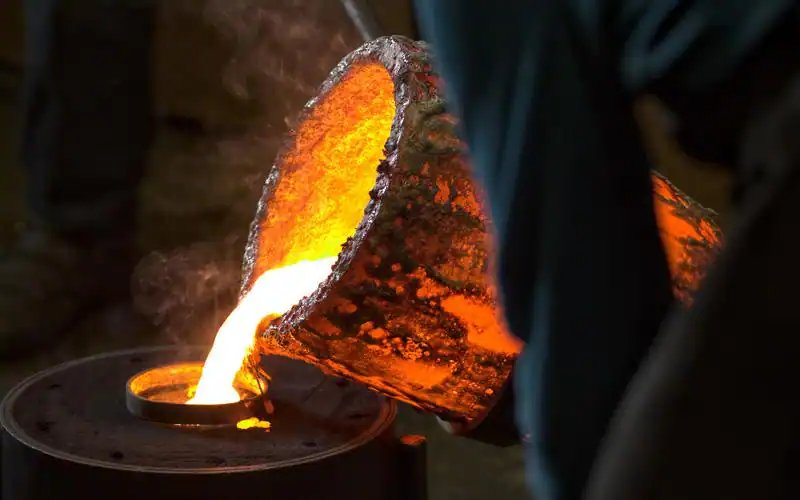
Processus conventionnel de production de moulage en sable
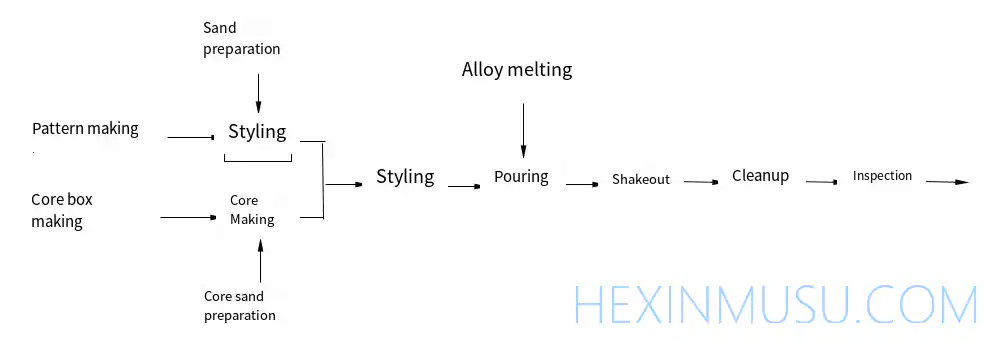
Procédé de moulage en sable
(1) Préparation du sable de moulage et du sable de noyautage
Les matériaux de moulage pour le moulage en sable sont principalement le sable utilisé pour la fabrication des moules en sable et le sable de noyautage utilisé pour la fabrication des noyaux en sable. Le sable est généralement constitué de sable brut (sable de montagne ou de rivière), d'argile et d'eau mélangés dans une certaine proportion, dont environ 9 % d'argile, environ 6 % d'eau, le reste étant du sable brut. Parfois, une petite quantité d'additifs tels que de la poudre de charbon, de l'huile végétale, des copeaux de bois, etc. sont également ajoutés pour améliorer les performances du sable et du sable de noyautage. La structure du sable compacté est illustrée dans la figure.
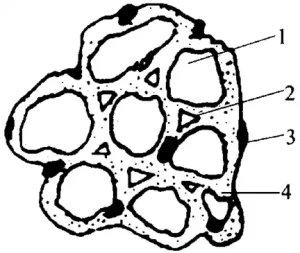
Schéma de la structure du sable 1 - grains de sable 2 - vides
3 - Attachement 4 - Membrane d'argile
Le sable de carottage est généralement préparé à la main en raison de sa faible demande.
L'environnement dans lequel se trouve le noyau est difficile, de sorte que les exigences de performance du sable du noyau sont supérieures à celles du sable haut, tandis que le liant du sable du noyau (argile, huile, etc.) est plus important que la proportion du liant dans le sable, de sorte que sa perméabilité n'est pas aussi bonne que celle du sable, le noyau doit être conçu pour créer un canal respirant (trous) ; afin d'améliorer le rendement du noyau, il convient d'ajouter des additifs, tels que des copeaux de bois.
Certaines petites pièces exigeantes sont souvent fabriquées avec des noyaux en sable huilé (huile de tung + sable, cuits jusqu'à l'obtention d'une couleur brun jaunâtre).
(2) Propriétés du sable de type
La qualité du sable a une incidence directe sur la qualité des pièces coulées. Un sable de mauvaise qualité entraînera la production de porosités, de trachomes, de sable collant, de sable et d'autres défauts. Un bon sable doit présenter les propriétés suivantes :
- ① Perméabilité au gaz La capacité du sable du moule à laisser passer le gaz est appelée perméabilité au gaz. Le métal à haute température coulant dans le moule, le type est rempli d'un grand nombre de gaz. Ces gaz doivent être évacués du moule en douceur, sinon le moule produira de la porosité, de la sous-épaisseur et d'autres défauts. La perméabilité à l'air de la coulée dépend de la taille des particules de sable, de la teneur en argile, de la teneur en humidité, de la compacité du sable et d'autres facteurs. Plus la taille des particules de sable est fine, plus la teneur en argile et en humidité est élevée, plus la compacité du sable est élevée, plus la perméabilité à l'air est mauvaise.
- ② Résistance La capacité du sable à résister aux dommages extérieurs est appelée résistance. Le sable doit avoir une résistance suffisante pour ne pas s'effondrer lors du moulage, de la manipulation et de la fermeture de la boîte, et pour ne pas endommager la surface de la pièce moulée lors de la coulée. La résistance du sable ne doit pas être trop élevée, sinon la coulée sera défectueuse en raison de la diminution de la perméabilité à l'air et des concessions.
- La réfractarité est la capacité du sable à résister aux températures élevées et à la chaleur. Si la réfractarité est faible, la coulée produira facilement un sable collant. Plus le sable contient de SiO2, plus les particules de sable sont grosses, meilleure est la réfractarité.
- Il s'agit de la capacité du sable à se déformer sous l'action d'une force extérieure et à conserver la forme existante après l'élimination de la force extérieure. Bonne plasticité, opération de moulage facile, forme précise et contour clair du moule en sable.
- ⑤ Concession La capacité du sable du moule à être comprimé lorsque la coulée est condensée. Si la concessionnalité n'est pas bonne, la pièce est sujette à des tensions internes ou à des fissures. Plus le sable est serré, plus la concessionnalité est mauvaise. L'ajout de copeaux de bois au sable de moulage peut améliorer la concessionnalité.
Dans l'atelier, les fournisseurs de produits de moulage en sable utilisent couramment la méthode du pincement de la main pour évaluer grossièrement certaines des propriétés du sable, par exemple en saisissant une poignée de sable, le pincement donne une impression de souplesse et de facilité de déformation ; en lâchant le sable après que la masse ne s'est pas détachée, qu'elle ne colle pas à la main et que les empreintes de main sont claires ; en le cassant, la section de la pièce est plate et régulière et il n'y a pas de phénomène de fissuration, et en même temps on ressent un certain degré de résistance, on pense que le sable répond aux exigences de performance appropriées, le sable. Comme le montre la figure.
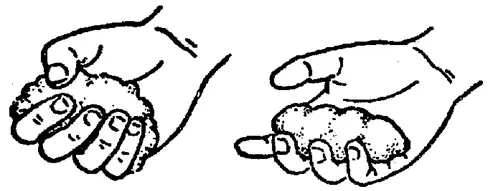
Lorsque l'humidité du sable est correcte, elle est visible lorsque la main est relâchée.
Il peut être malaxé à la main pour former une boule de sable Lignes de main claires
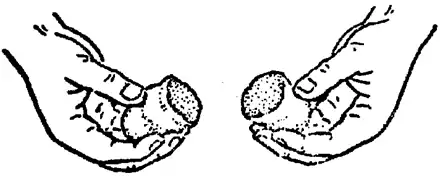
Fracture avec une fente brisée avec une forme fragmentée
En même temps, il y a suffisamment de force
(3) Composition des moules
Les moules pour les produits moulés en sable sont fabriqués à partir de matériaux de moulage en fonction de la forme de la pièce, et les moules peuvent être en sable ou en métal. Un moule en sable est fabriqué à partir d'un matériau de moulage à base de sable (sable à noyau). Il est utilisé pour couler le métal liquide afin d'obtenir des pièces moulées de la forme, de la taille et de la qualité requises.
Un moule se compose généralement d'un moule supérieur, d'un moule inférieur, d'un noyau, d'une cavité et d'un système de coulée, comme le montre la figure ci-contre.
Les surfaces de jointure entre les composants du moule sont appelées plans de joint. La partie de la cavité entourée par le matériau de moulage dans le moule, c'est-à-dire la cavité formant le corps de la pièce moulée, est appelée cavité. Le métal liquide s'écoule dans la cavité et la remplit grâce au système de coulée, et le gaz produit est évacué du moule en sable par la sortie d'air, etc.
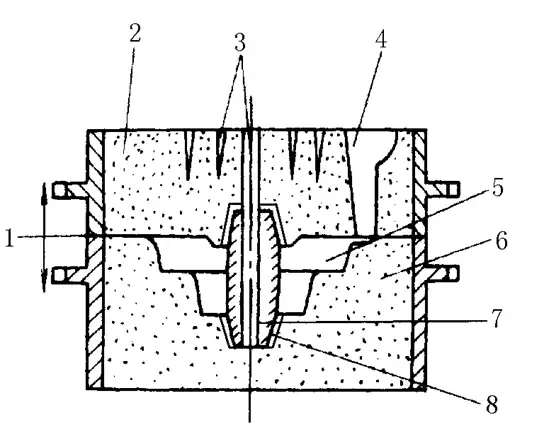
1-Surface de séparation 2-Moule supérieur 3-Sortie d'air 4-Système de coulée 5-Cavité 6-Moule inférieur
Support de tête 7-core 8-core
(4)Systèmes de vannes
- Système de coulée Le système de coulée est une série de canaux dans le moule permettant au métal liquide de s'écouler dans la cavité. Sa fonction est de :
① Injecter le liquide métallique rapidement et sans à-coups ;
②Bloquer les scories, le sable, etc. pour éviter qu'ils ne pénètrent dans la cavité ;
(iii) Réguler la température de chaque partie de la coulée pour compléter la contraction du volume du métal liquide pendant le refroidissement et la solidification.
Le réglage correct du système de coulée est d'une grande importance pour garantir la qualité des pièces coulées et réduire la consommation de métal. Si le système de coulée n'est pas raisonnable, les pièces coulées sont sujettes à des défauts tels que le soufflage de sable, les trous de sable, les trous de scories, l'échec de la coulée, la porosité et les trous de retrait. Le système de coulée typique se compose de quatre parties : la porte extérieure, la carotte droite, la carotte transversale et la carotte intérieure, comme le montre la figure ci-dessous.
Pour les petites pièces de forme simple, la carotte transversale peut être supprimée.
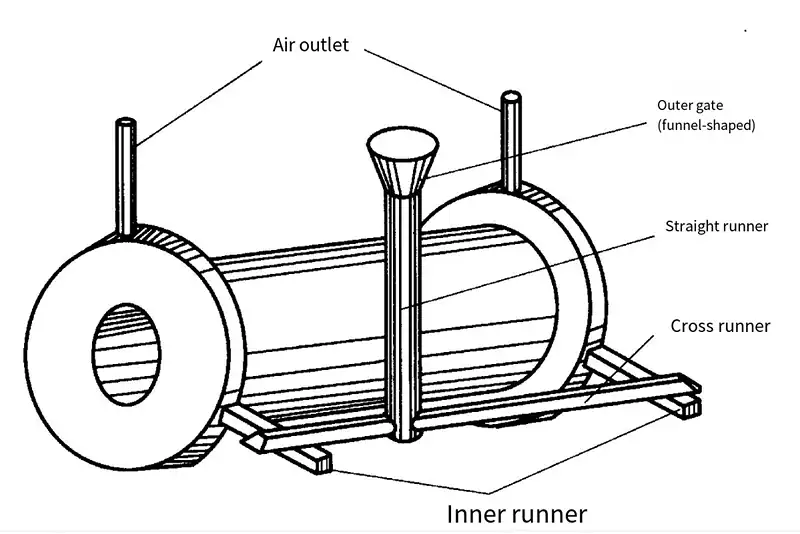
Systèmes de coulée typiques
- ① Porte extérieure Sa fonction est de contenir le métal liquide injecté et de faciliter l'impact du métal liquide sur le moule en sable. Les petites pièces moulées ont généralement la forme d'un entonnoir (appelé gobelet de coulée), tandis que les plus grandes pièces moulées ont la forme d'un bassin (appelé pot de coulée).
- ② Canal droit Il s'agit d'un canal vertical reliant la porte extérieure au canal horizontal. La modification de la hauteur du canal droit peut modifier la pression statique du métal liquide et le débit du métal liquide, ce qui modifie la capacité de remplissage du métal liquide. Si la hauteur ou le diamètre de la coulée droite est trop important, la coulée sera insuffisamment coulée. Afin de faciliter le retrait de la tige, le canal droit est généralement de forme conique, avec un grand sommet et un petit fond.
- ③ Canal transversal Il s'agit d'un canal horizontal permettant d'introduire le métal liquide du canal droit dans le canal intérieur, généralement ouvert sur la surface de séparation du moule en sable, et dont la forme de la section transversale est généralement trapézoïdale haute et située sur le dessus du canal intérieur. La fonction principale du canal transversal est de distribuer le métal liquide dans le canal intérieur et de bloquer le laitier.
- Elle est directement reliée à la cavité et peut réguler la direction et la vitesse du flux de métal liquide dans la cavité ainsi que la vitesse de refroidissement de chaque partie de la pièce moulée. La forme de la section transversale de la carotte intérieure est généralement plate, trapézoïdale et en forme de croissant, et peut également être triangulaire.
- Elévateurs Les défauts courants tels que le retrait et le relâchement sont dus à la contraction du volume de la pièce coulée lorsqu'elle refroidit et se solidifie. Afin d'éviter le retrait et le relâchement, la partie supérieure ou épaisse de la colonne montante est souvent coulée. Les colonnes montantes sont les cavités et le métal injecté dans les cavités de la coulée. Le métal liquide dans la colonne montante peut constamment compenser le retrait du moulage, de sorte que le moulage peut éviter les trous de retrait et le relâchement dû au retrait. Les colonnes montantes sont redondantes et doivent être retirées lors du nettoyage. Les colonnes montantes complètent le rôle de retrait, mais jouent également le rôle d'échappement et de collecte du laitier.
(5) Fabrication de moules et de boîtes à noyaux
Le moule est l'équipement nécessaire à la production d'une pièce moulée. Pour les pièces coulées avec une cavité interne, le moulage de la cavité interne formée par le noyau de sable, et donc également pour préparer la boîte à noyau pour le noyau de sable. Les matériaux couramment utilisés pour la fabrication des moules et des boîtes à noyaux sont le bois, le métal et le plastique. La production d'une seule pièce ou d'un petit lot est largement utilisée pour les moules et les boîtes à noyaux en bois, tandis que la production en masse de moules et de boîtes à noyaux en métal ou en plastique est très répandue. La durée de vie des moules et des boîtes à noyaux en métal est de 100 000 à 300 000 fois, celle des moules en plastique peut atteindre plusieurs dizaines de milliers de fois, tandis que celle des moules en bois n'est que d'environ 1 000 fois. Afin de garantir la qualité des pièces coulées, il est nécessaire, lors de la conception et de la fabrication des moules et des boîtes à noyau, de concevoir un schéma de processus de moulage, puis de fabriquer des moules et des boîtes à noyau en fonction de la forme et de la taille du schéma de processus. Voir le diagramme ci-dessous.
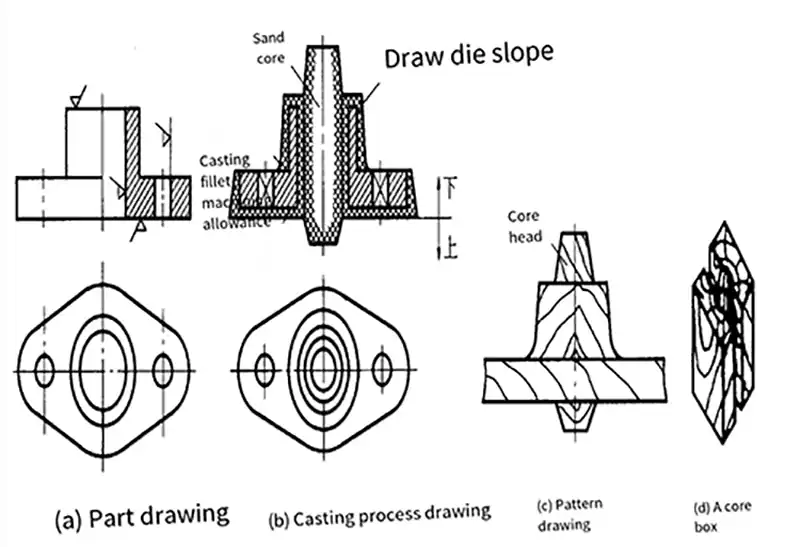
Lors de la conception d'un diagramme de processus, il convient de prendre en compte certains des éléments suivants :
- ① Choix du plan de joint Le plan de joint est l'interface entre le sable supérieur et le sable inférieur, et le choix du plan de joint doit permettre de démouler le moule, de rendre le modelage pratique et de garantir la qualité des pièces coulées.
- Pour faciliter le démoulage, toutes les surfaces perpendiculaires au plan de joint sont inclinées de 0,5º~4º.
- ③ Surépaisseur d'usinage La surface de la pièce moulée à traiter doit présenter une surépaisseur d'usinage appropriée.
- ④ Retrait La pièce moulée doit se rétracter en refroidissant, et la taille du moule doit tenir compte de l'influence du retrait de la pièce moulée. Généralement utilisé pour les pièces en fonte afin d'augmenter de 1 % ; les pièces en acier moulé afin d'augmenter de 1,5 % à 2 % ; les pièces en alliage d'aluminium afin d'augmenter de 1 % à 1,5 %.
- ⑤ Couler des coins arrondis Tous les points d'inflexion de chaque surface du moulage doivent être transformés en coins arrondis transitoires pour faciliter le modelage et assurer la qualité du moulage.
- (6) Tête de noyau Pour les moules en sable avec noyau, une tête de noyau correspondante doit être fabriquée sur le moule.
Méthodes de modélisation
Le choix de la méthode de moulage doit non seulement dépendre du type de production, mais aussi des conditions d'équipement de l'usine, de la taille et de la complexité de la pièce moulée, ainsi que des exigences de qualité. Les méthodes de moulage peuvent être divisées en deux catégories : le moulage manuel et le moulage mécanique.
Le moulage à la main est principalement utilisé pour la production de petites séries de pièces uniques, tandis que le moulage à la machine est principalement utilisé pour la production de grandes séries.
(1). Modélisation de la main
- (A) Les caractéristiques du moulage intégral sont les suivantes : le moule est une structure intégrale, la plus grande section transversale est plate à une extrémité du moule, les surfaces de séparation sont généralement plates et l'opération est simple. Le moule intégral convient aux pièces moulées de forme simple, telles que les disques et les couvercles.
- (B) Les caractéristiques du moulage en deux parties sont les suivantes : les moules sont séparés et la surface séparée des moules (appelée surface de séparation) doit être la plus grande section transversale des moules, afin de faciliter le levage des moules. Le processus de moulage en deux parties est fondamentalement similaire à celui du moulage en un seul bloc, à la différence que deux opérations sont ajoutées lors de la fabrication du moule supérieur, à savoir la mise en place du moule supérieur et le prélèvement du demi-moule supérieur. Le moulage en deux parties convient aux pièces moulées de forme complexe, telles que les manchons, les tubes et les corps de vanne.
- (C) bloc vivant Le moule de moulage sur la partie amovible ou mobile est appelé bloc vivant. Lorsqu'il y a un obstacle sur le côté du moule pour étendre la pièce (comme une petite languette), la pièce est souvent transformée en bloc vivant. Lors du démoulage, le corps principal du moule est d'abord retiré, puis le bloc vivant laissé dans le moule est retiré séparément ; cette méthode est appelée moulage en bloc vivant. Lors du moulage du bloc vivant relié à des clous, il convient de noter que le sable autour du bloc vivant doit d'abord être bourré fermement, puis les clous doivent être retirés.
- (D) moulage au sable : lorsque le moulage est conforme aux caractéristiques structurelles du besoin de moulage, mais qu'en raison des conditions (moule trop fin, difficulté de fabrication des moules, etc.), le moulage se fait en un seul bloc ; pour faciliter le moulage, la surface inférieure de la pièce doit être creusée en une surface courbe ou présenter des changements de forme de l'échelle (surface de séparation inégale) ; cette méthode s'appelle le moulage au sable.
- (F) Moulage à trois bacs Le processus consistant à utiliser trois bacs à sable pour fabriquer la pièce moulée est appelé moulage à trois bacs. Toutes les méthodes de moulage susmentionnées utilisent deux bacs à sable, qui sont faciles à utiliser et largement répandus. Toutefois, certaines pièces moulées, telles que les deux extrémités de la section transversale sont plus grandes que la section transversale centrale, nécessitent l'utilisation de trois bacs à sable, à partir de deux directions respectives du moule.
- (G) moulage par raclage d'une taille supérieure à 500 mm Les pièces moulées à corps rotatif, telles que les poulies, les volants d'inertie, les grands engrenages et d'autres productions uniques, peuvent être moulées par raclage afin d'économiser du bois et de réduire le temps et le coût de traitement des moules. Le racloir est une planche de bois adaptée à la forme de la section de moulage. Lors du moulage, le racleur tourne autour d'un axe central fixe et racle la cavité requise dans le moule en sable.
- (H) Le moulage par fausse boîte est l'utilisation d'une plaque de base préfabriquée ou d'une fausse boîte pour remplacer le sable excavé dans le moulage par creusage de sable.
- (I) Moulage en fosse La méthode consistant à mouler directement sur le plancher de sable ou dans la fosse de sable de la fonderie est appelée moulage en fosse. Lorsque de grandes pièces sont produites en une seule pièce, le moulage en fosse est souvent utilisé pour économiser le bac à sable, réduire la hauteur de coulée et faciliter les opérations de coulée. La structure du moulage en fosse, le moulage doit être pris en compte lors de la coulée pour que le gaz contenu dans la fosse puisse sortir en douceur du sol, souvent du coke, du laitier et d'autres matériaux respirables, et pour que le gaz puisse sortir du tuyau en fer.
(2). Modélisation de la machine
La productivité du moulage manuel est faible, la qualité de surface des pièces moulées est médiocre, l'exigence de travailleurs ayant un niveau technique élevé, l'intensité de la main-d'œuvre, de sorte que dans la production de masse, on utilise généralement le moulage à la machine. Le moulage machine est l'opération principale du processus de moulage ----. Le resserrement du sable et le moulage permettent de réaliser la mécanisation. En fonction des différentes méthodes de serrage du sable et de démarrage du moule, on distingue le moulage par compactage par micro-vibration pneumatique, le moulage par pression de tir, le moulage par haute pression et le moulage par projection de sable.
- (A) compactage pneumatique par micro-vibration le moulage est utilisé vibration (fréquence 150 ~ 500 fois / min, amplitude 25-80mm) - compactage - micro-vibration (fréquence 700 ~ 1000 fois / min, amplitude 5 ~ l0mm) sable compacté. l0mm) pour compacter le sable de moulage. Ce type de machine de moulage est moins bruyant, le sable est compacté de façon homogène et la productivité est élevée.
- (B) Le moulage par injection se caractérise par l'utilisation d'air comprimé pour projeter du sable dans la cavité en vue d'un compactage initial, puis le piston de compactage comprime à nouveau le sable, et après le lancement du sable, la surface de contact entre les deux types de sable avant et après est la surface de séparation. La taille de la pièce moulée par injection est précise, la rugosité de la surface est faible et la productivité est élevée. Il peut produire 240 à 300 moules par heure et est couramment utilisé pour la production en masse de pièces moulées de petite et moyenne taille.
- (C) Le moulage à haute pression utilise un système hydraulique pour générer une pression très élevée afin de compacter le moule en sable. Il se caractérise par des dimensions de moulage précises, une faible rugosité de surface et une productivité élevée. Le moulage à haute pression convient aux pièces de petite et moyenne taille aux formes plus complexes, aux variétés multiples et aux lots moyens ou plus.
- (D) Le moulage par projection de sable consiste à utiliser une lame rotative à grande vitesse pour projeter le sable transporté par la bande transporteuse à grande vitesse afin de compacter le moule de sable. Le moulage par projection de sable est très adaptable, ne nécessite pas de bac à sable spécial ni de gabarit, et convient à la production de pièces uniques et de petits lots de pièces moulées de grande taille.
carottage
Afin d'obtenir la cavité intérieure ou la forme locale de la pièce moulée, le sable de noyautage ou d'autres matériaux sont placés dans la cavité à l'intérieur des éléments de la pièce moulée, appelés noyaux. La grande majorité des noyaux sont constitués de sable de noyautage. La qualité du noyau dépend principalement de la préparation d'un sable de noyautage qualifié et de l'utilisation d'un processus de noyautage correct.
Lors de la coulée du noyau de sable par l'impact d'un métal liquide à haute température et entouré, outre les exigences du noyau de sable avec la coulée de la forme correspondante de la cavité interne, il faut également avoir une meilleure perméabilité, réfractarité, concessions, résistance et d'autres propriétés. Nous devons donc choisir du sable de quartz avec peu d'impuretés et de l'huile végétale, du verre soluble et d'autres liants pour formuler le sable du noyau, et dans le noyau de sable dans l'os du noyau de métal et faire les trous de ventilation afin d'améliorer la résistance et la perméabilité.
Les noyaux de grande et moyenne taille aux formes simples peuvent être fabriqués avec du sable argileux. En revanche, pour les noyaux aux formes complexes et aux exigences de performance élevées, des liants spéciaux doivent être utilisés pour les formuler, tels que le sable à l'huile, le sable à la graisse et le sable à la résine.
En outre, le sable de noyautage doit également présenter certaines propriétés particulières, telles qu'une faible hygroscopicité (afin d'éviter que le noyau ne retourne à l'humidité après la fermeture de la boîte), moins de dégagement gazeux (après la coulée du métal, le matériau du noyau doit produire le moins de gaz possible lorsqu'il est chauffé) et un bon ponçage (afin de faciliter l'enlèvement du noyau lors du nettoyage).
Les noyaux sont généralement fabriqués à partir de boîtes à noyaux, et leur fabrication en boîte à noyaux ouverte est une méthode manuelle courante de fabrication de noyaux plus complexes avec des sections transversales rondes.
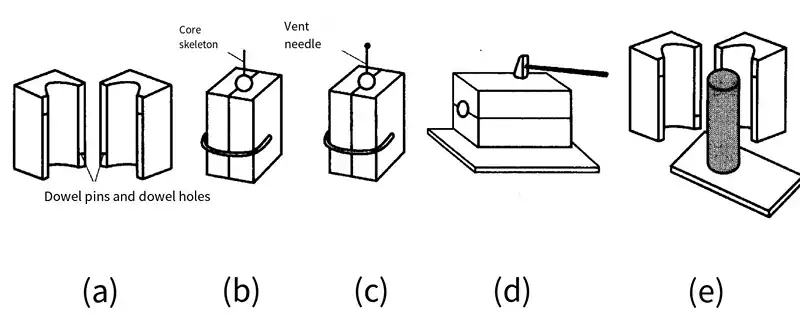
Folio core box core making
(a) Préparer la boîte à noyaux (b) Serrer la boîte à noyaux, ajouter le sable et l'os à noyaux à tour de rôle, pilonner le sable (c) Gratter et attacher les trous d'aération (d) Desserrer les pinces, tapoter la boîte à noyaux (e) Ouvrir la boîte à noyaux, retirer le noyau de sable, et appliquer la peinture.
Opérations de base de la modélisation
Il existe de nombreuses méthodes de moulage, mais la plupart d'entre elles comprennent le pilonnage au sable, le démarrage du moule, la réparation du moule et la fermeture de la boîte.
(1) regarder
La forme originale de la pièce moulée en bois, en métal ou en d'autres matériaux est appelée collectivement le moule, qui est utilisé pour former la cavité de la pièce moulée. Les moules en bois sont appelés moules en bois, les moules en métal ou en plastique sont appelés moules en métal ou moules en plastique. Actuellement, la plupart des usines utilisent des moules en bois. La forme du moule est similaire à la forme de la pièce moulée, à la différence que la pièce moulée, comme les trous, dans le moule n'est pas seulement solide sans trous, mais aussi dans la position correspondante pour faire la tête du noyau.
(2) Préparation avant le moulage
- ① Préparer les outils de moulage, choisir une plaque de base plate et un bac à sable de taille appropriée. Si le bac à sable est trop grand, non seulement il consommera trop de sable, mais il gaspillera également le temps de pilonnage du sable. Si le bac à sable est trop petit, le sable autour du moule en bois ne sera pas pilonné fermement et le métal liquide s'écoulera facilement de la surface de séparation, c'est-à-dire entre les interfaces, lors de la coulée. En général, la distance entre le moule en bois, la paroi intérieure et le sommet du bac à sable doit être comprise entre 30 et 100 mm, ce qui correspond à la quantité de sable à manger. La valeur spécifique de la capacité de consommation de sable dépend de la taille du moule en bois.
- ② Essuyer le moule en bois afin d'éviter que le sable de moulage ne colle au moule en bois et n'endommage la cavité lors du levage du moule.
- ③ Lorsque vous placez le moule en bois, faites attention au sens de la pente sur le moule en bois et ne le placez pas au mauvais endroit..
(3)livre de sable
- ① Le sable de battage doit être ajouté au sable par étapes. Pour un petit bac à sable, il faut ajouter à chaque fois une épaisseur de sable d'environ 50 à 70 mm. Trop de sable n'est pas étanche, et trop peu de sable coûte des heures de travail. Lors du premier ajout de sable, le sable autour du moule en bois doit être pressé fermement à la main pour éviter que le moule en bois ne bouge dans le bac à sable. Ensuite, utilisez l'extrémité pointue du marteau à sable pour marteler fermement par étapes, et enfin utilisez l'extrémité plate du marteau à sable pour marteler fermement la couche supérieure de sable.
- ② Le pilonnage du sable doit être effectué selon un certain itinéraire. Ne pas est un peu, ouest un peu chaotique pilonnage, afin d'éviter les différentes parties de l'étanchéité.
- ③ Le pilonnage du sable doit être approprié. Si la force est trop importante, le sable est trop serré et le gaz ne peut pas s'écouler dans la cavité. Si la force est insuffisante, le sable est trop lâche et la boîte s'effondre facilement. L'étanchéité de chaque partie du même sable est différente, près de la paroi intérieure du bac à sable, le sable doit être bien tassé pour éviter l'effondrement du bac. Près de la partie de la cavité, le sable doit être légèrement plus serré pour résister à la pression du métal liquide. À l'écart de la cavité, la couche de sable doit être suffisamment lâche pour faciliter la perméabilité à l'air.
- ④ Lors du pilonnage du sable, il faut éviter que le marteau ne frappe le moule en bois. En général, la distance entre le marteau et le moule en bois est de 20 à 40 mm, sinon il est facile d'endommager le moule en bois.
(4) saupoudrer du sable
Avant de construire le modèle en sable, il convient de saupoudrer une couche de sable sec à grain fin et non argileux (c'est-à-dire de sable) sur la surface de séparation afin d'éviter que les bacs à sable supérieur et inférieur ne se collent l'un à l'autre et ne parviennent pas à s'ouvrir. Pour répandre le sable, la main doit être légèrement surélevée par rapport au bac à sable, tout en se retournant, tout en se balançant, de manière à ce que le sable, à travers les fissures du doigt, soit lentement et uniformément répandu vers le bas, et recouvert d'une fine couche sur la surface de séparation. Enfin, le moule en bois doit être soufflé pour enlever le sable de séparation, afin de ne pas faire adhérer le sable de séparation à la surface du modèle en sable et, lors de la coulée du métal liquide, au moulage, de sorte qu'il produise des défauts.
(5)percer un trou
En plus de s'assurer que le sable a une bonne perméabilité à l'air, il faut également s'assurer que le sable a été martelé et gratté à plat, avec une aiguille d'aération pour percer les trous d'aération, de sorte que le gaz puisse facilement s'échapper lors du versement. Les trous de ventilation doivent être verticaux et uniformément répartis.
(6)portail ouvert
La porte extérieure doit être creusée en un cône de 60°, avec un diamètre de 60 à 80 mm à la grande extrémité, et la surface de la porte doit être polie, et la connexion avec la tige droite doit être faite en une transition arrondie, de manière à guider le métal liquide pour qu'il s'écoule en douceur dans le moule en sable. Si la porte extérieure est creusée trop superficiellement et prend la forme d'un disque, le métal liquide éclaboussera et blessera les personnes lors de la coulée.
(7)Faire la ligne de clôture
Si les bacs à sable supérieur et inférieur ne sont pas équipés de goupilles de positionnement, une ligne de fermeture doit être tracée sur la paroi du bac à sable avant que les modèles de sable supérieur et inférieur ne soient ouverts. La méthode la plus simple consiste à appliquer de la poussière de craie sur la paroi du bac, puis à utiliser une aiguille pour tracer une ligne fine. Il est nécessaire d'aller dans le four pour cuire le bac à sable, l'argile à sable est utilisée pour coller dans la paroi du bac à sable, avec un couteau de plâtrier à plat, puis de sculpter la ligne, connue sous le nom de numéro de boue de jeu. La ligne doit être située au point le plus éloigné des deux bords à angle droit de la paroi du bac à sable afin de garantir que les directions x et y peuvent être positionnées et de limiter la rotation du type de sable. Le nombre de lignes à deux endroits ne doit pas être égal, afin de ne pas faire d'erreur lors de la fermeture du bac. Une fois la ligne terminée, vous pouvez ouvrir la boîte pour commencer le moule.
(8)prendre un moule
- ① Avant de prendre le moule, trempez le pinceau dans un peu d'eau et badigeonnez le sable autour du moule en bois afin d'éviter d'endommager la cavité de sable lors de la prise du moule. La brosse à eau doit être une brosse, ne pas laisser la brosse à eau à un certain endroit, afin d'éviter une quantité excessive d'eau locale et de produire une grande quantité de vapeur d'eau pendant la coulée, de sorte que la coulée produise des défauts de porosité.
- ② La position de la tige de démarrage du moule doit coïncider autant que possible avec le centre de gravité du moule en bois. Avant de commencer le moule, utilisez un petit marteau pour taper doucement sur la partie inférieure de la goupille de démarrage du moule afin de desserrer le moule en bois et de faciliter le démarrage du moule.
- ③ Lorsque vous soulevez le moule, soulevez lentement le moule en bois verticalement, lorsque le moule en bois est sur le point d'être complètement soulevé, retirez-le rapidement. Veillez à ne pas dévier et à ne pas vous balancer lorsque vous soulevez le moule.
(9) manucure
Après avoir retiré le moule, si la cavité est endommagée, toutes sortes d'outils de réparation doivent être utilisés correctement en fonction de la forme de la cavité et du degré d'endommagement. Si la cavité est très endommagée, le moule en bois peut être replacé dans la cavité pour la réparer, puis retiré à nouveau.
(10)clôturer un dossier
La fermeture de la boîte est le dernier processus de moulage, qui joue un rôle important dans la qualité du moule en sable. Avant de fermer la boîte, il convient de vérifier soigneusement que le moule de sable n'est pas endommagé, que le sable ne s'est pas détaché et que la porte n'est pas rognée. Si vous souhaitez poser le noyau, vous devez vérifier qu'il est sec, qu'il n'est pas endommagé et que les trous d'aération ne sont pas obstrués. La position du noyau dans le moule en sable doit être précise et stable, afin de ne pas affecter la précision de la coulée et d'éviter d'être emporté par le métal liquide lors de la coulée. Lors de la fermeture de la boîte, il convient de prêter attention à la boîte de sable supérieure afin de maintenir le niveau bas et de l'aligner sur la ligne de fermeture afin d'éviter de se tromper de boîte. Après avoir fermé la boîte, il est préférable de couvrir la carotte avec du papier ou un morceau de bois pour éviter que du sable ou des débris ne tombent dans la carotte.
Sélection de la position de coulée et du plan de joint
moulagesLa position de coulée de la pièce est la position de la pièce dans le moule pendant la coulée.
Le plan de joint est la surface où les deux moitiés de la pièce moulée entrent en contact l'une avec l'autre.
Leur principe de sélection vise principalement à garantir la qualité des pièces moulées et à simplifier le processus de moulage. En règle générale, la position de coulée doit être choisie d'abord après le plan de joint, mais en production, la sélection de la position de coulée et la détermination du plan de joint étant parfois contradictoires, il est nécessaire d'analyser en détail les avantages et les inconvénients des différentes options et de choisir la meilleure option.
(1) .Principe de sélection de la position de coulée
- (A) la surface d'usinage importante de la coulée doit être orientée vers le bas - les trous d'air, les trous de sable, les scories, les trous de retrait sont susceptibles d'apparaître dans la surface supérieure, tandis que la partie inférieure du métal liquide est relativement pure, l'organisation du métal est relativement dense. Parfois, lorsque la surface d'usinage importante est orientée vers le bas pour une raison quelconque, elle doit être réalisée dans la position de la surface d'exemple, dans la mesure du possible.
- (B) Le grand plan de la pièce coulée doit être orienté vers le bas En raison de l'effet du rayonnement thermique pendant la coulée, le sable sur la surface supérieure de la cavité de coulée est susceptible de se voûter et de se fissurer, ce qui entraîne des défauts de sable et d'inclusions sur la surface supérieure de la pièce coulée, de sorte que le grand plan doit être orienté vers le bas.
- (C) les pièces à parois minces doivent être placées dans la partie inférieure de la pièce à parois minces, ce qui permet d'augmenter la pression de remplissage et d'améliorer la capacité de remplissage du métal.
- (D) veiller à ce que la coulée réalise une solidification directionnelle En cas de retrait de l'alliage, l'épaisseur de la paroi de la coulée n'est pas uniforme, l'épaisseur de la plus grande partie de la coulée doit être placée dans la coulée la plus haute ou près de la surface de séparation, afin de faciliter la mise en place des colonnes montantes, pour réaliser une solidification directionnelle.
- (F) Il doit être facile de fixer le noyau, de l'installer et de le ventiler, et de fermer le moule.
(2).Principe de sélection des plans de joint
- (A) Le plan de joint doit être choisi au niveau de la plus grande section transversale du moule pour faciliter la prise du moule, en accordant une attention particulière au moulage en sable de creusage.
- (B) Le nombre de surfaces de séparation doit être réduit au minimum et la modélisation en trois boîtes doit être évitée pour la production de masse.
- (C) Toutes les pièces moulées ou la plupart d'entre elles sont réalisées dans le même moule en sable afin de réduire les erreurs de positionnement, les arêtes vives et les bavures et d'améliorer la précision des pièces moulées.
- (D) Le nombre de noyaux et de blocs vivants doit être réduit autant que possible afin de simplifier le processus de moulage et de fabrication des noyaux et d'améliorer la productivité.
Sélection des paramètres du processus
(1) Allocation d'usinage
Les pièces moulées doivent être découpées en surface et il convient de prévoir à l'avance une certaine marge d'usinage, dont la taille dépend du type d'alliage de fonderie, des méthodes de modélisation, de la taille de la pièce moulée et de la surface de traitement de la pièce moulée, ainsi que de l'emplacement de nombreux facteurs. Rugosité de la surface de l'acier moulé, déformation, surépaisseur de traitement ; la surface de l'alliage non ferreux est lisse, la surépaisseur de traitement est faible ; la modélisation de la machine est de haute précision, la surépaisseur de traitement peut être choisie plus petite ; la production d'une seule pièce ou d'un petit lot comporte plus de facteurs affectant la surépaisseur de traitement qu'il convient d'augmenter ; plus la coulée est grande et complexe, plus la surépaisseur de traitement est importante ; la coulée de la surface supérieure est plus importante que la surface inférieure et les côtés de la surépaisseur de traitement.
La surépaisseur d'usinage pour les petites pièces en fonte est de 4,5 ~ 5,5 mm ; la surépaisseur d'usinage pour les petites pièces en métal non ferreux est de 3 mm ; la surépaisseur d'usinage pour les pièces en fonte grise peut se référer à la norme JB2854-80.
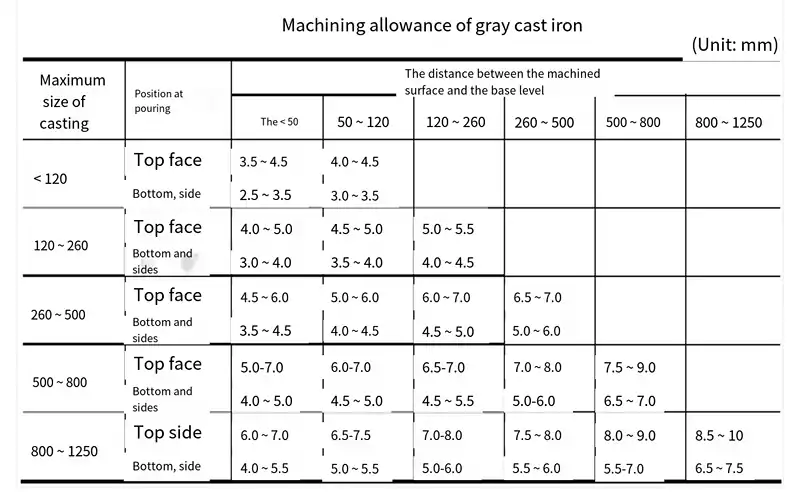
En outre, les pièces en acier moulé d'un diamètre inférieur à 35 mm et les pièces en fonte d'un diamètre inférieur à 25 mm ne sont généralement pas moulées, ce qui rend l'usinage plus économique et plus pratique. Pour le modelage à la machine de petites pièces, le trou peut être plus petit s'il n'est pas moulé. Pour les formes spéciales qui ne nécessitent pas de traitement, les difficultés d'usinage dans le trou, la fente, il doit être moulé.
(2) Pente du moulage
Afin de faciliter le démoulage de l'épreuve, la pente ajoutée à la paroi verticale perpendiculaire au plan de joint est la pente de départ du moule. Plus le moule est haut, plus la valeur de la pente est faible, et la pente de la paroi intérieure est plus importante que celle de la paroi extérieure. La pente de la paroi intérieure est plus grande que celle de la paroi extérieure. La pente du moulage à la main est plus grande que celle du moulage à la machine. Lorsque le moule est court (≤100mm), elle est d'environ 3º, et lorsque le moule est haut (101~160mm), elle est de 0,5°~1°.
(3) Couler des coins arrondis
Afin d'éviter les tensions et les fissures dans les raccords de paroi et les coins de la pièce moulée, d'éviter d'endommager les angles vifs de la pièce moulée et de produire des trous de sable, les raccords de paroi et les coins de la pièce moulée doivent être conçus en quatre coins lors de la conception de la pièce moulée.
(4) Responsables principaux
Afin d'assurer le positionnement, la fixation et la ventilation du noyau dans le moule de coulée, le moule et le noyau sont conçus avec une tête de noyau.
La tête du noyau est la partie tendue du noyau, qui tombe dans le siège du noyau du modèle de coulée et sert à localiser et à soutenir le noyau.
La forme de la tête du noyau dépend du type de noyau, la tête du noyau doit avoir une hauteur (h) ou une longueur (l) suffisante et une pente appropriée, afin de rendre le noyau pratique, précis et fermement fixé dans le moule de coulée, de manière à éviter le flottement, la déflexion et le mouvement du noyau pendant la coulée.
(5) Indemnité de rétrécissement
Étant donné que la fonte subit une contraction de refroidissement après la coulée, la production de moules doit être ajoutée à cette partie de la taille de retrait. En général, la marge de retrait de la fonte grise est de 0,8 % - 1,0 %, celle de l'acier moulé de 1,8 % - 2,2 %, et celle de l'alliage d'aluminium moulé de 1,0 % - 1,5 %. L'importance de la marge de retrait dépend non seulement du type d'alliage, mais aussi du processus de moulage, des pièces moulées dans la contraction de la situation de blocage, etc.
Type d'alliage | Retrait de la coulée | ||
contraction libre | rétrécissement | ||
gris métaux coulés ou trouvés fer (métal) | Petites et moyennes pièces moulées | 1.0 | 0.9 |
Moulages moyens et grands | 0.9 | 0.8 | |
Très grandes pièces moulées | 0.8 | 0.7 | |
fonte ductile | 1.0 | 0.8 | |
Acier au carbone et faiblement allié | 1.6~2.0 | 1.3~1.7 | |
étain bronze | 1.4 | 1.2 | |
Wuxi Bronze | 2.0~2.2 | 1.6~1.8 | |
laiton siliconé | 1.7~1.8 | 1.6~1.7 | |
Alliages aluminium-silicium | 1.0~1.2 | 0.8~1.0 |
Avantages et inconvénients du moulage en sable
Avantages du moulage en sable
- Faibles coûts de fabricationLe moulage en sable utilise des matières premières (sable, argile, etc.) à faible coût et le processus de fabrication est relativement simple, de sorte que les coûts de fabrication sont relativement bas.
- Grande souplesse de fabricationLe moulage en sable permet de produire des pièces de forme et de taille très variées, allant de quelques grammes à plusieurs tonnes, avec une grande facilité et une grande applicabilité.
- Cycle de fabrication courtLe procédé de moulage en sable est relativement simple et nécessite moins de temps de séchage et de durcissement, ce qui se traduit par un cycle de fabrication relativement court.
- Large éventail de sources de matières premières: Le moulage en sable dispose d'un large éventail de sources de matières premières, le sable, l'argile, etc. peuvent être utilisés comme matériau de moulage et sont peu coûteux.
Inconvénients du moulage en sable
- Qualité moyenne de la surface des pièces couléesLa qualité de la surface des pièces moulées en sable peut présenter certains défauts, tels que des trous de sable, des trous de sable, du sable collant, etc.
- Le noyau de sable est susceptible de s'effondrerLes noyaux de sable : Dans la coulée en sable, des noyaux de sable peuvent être nécessaires pour fabriquer des pièces moulées de forme complexe. Les noyaux de sable sont susceptibles de se déformer et de s'effondrer, ce qui entraîne un taux de rejet élevé.
- Baisse de la productivitéLa productivité du moulage en sable est relativement faible, car chaque moule en sable doit être fabriqué à la main et les moules ne peuvent être utilisés qu'une seule fois.
- Consommation d'énergie et émissions polluantes élevéesLe moulage en sable : Le moulage en sable consomme beaucoup d'énergie au cours du processus de production et peut produire certaines émissions polluantes, telles que des poussières et des gaz d'échappement. Cela peut avoir un impact sur l'environnement et la santé des travailleurs.