5 défauts courants et leurs solutions, tels que les trous de retrait de la coulée, la rugosité de la surface et l'absence de finition
Temps de publication:2024-08-03 Trier par:Le blog Nombre de vues:1507
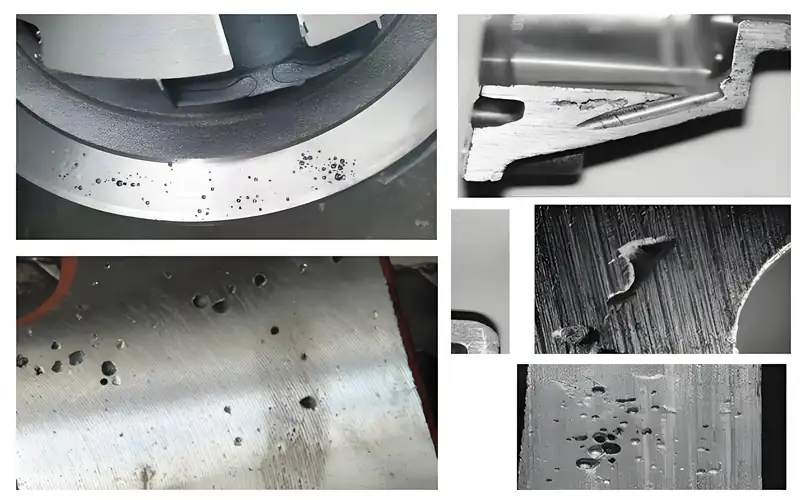
Porosité (y compris bulles d'air, trous d'étranglement, poches d'air)
Causes de la formation :
1) La température de préchauffage du moule est trop basse et le métal liquide se refroidit trop rapidement dans le système de coulée.
2、Mauvaise conception de l'échappement des moules, mauvaise évacuation des gaz.
3. une mauvaise peinture, un mauvais échappement, voire des gaz volatils ou en décomposition.
4. la surface de la cavité du moule présente des trous et des piqûres. Après l'injection du métal liquide, le gaz se dilate rapidement et comprime le métal liquide, formant un trou d'étranglement.
5. la surface de la cavité du moule est rouillée et n'est pas nettoyée.
6. un mauvais stockage des matières premières (noyau de sable) et l'absence de préchauffage avant utilisation.
7. un mauvais désoxydant, un dosage insuffisant ou une mauvaise utilisation.
Voici quelques méthodes pour éviter la création de trous d'air (bulles, trous d'étranglement, poches d'air).
1、Contrôler la température de coulée dans la plage appropriée pour éviter une expansion excessive du gaz.
2, le préchauffage du moule est suffisant, l'utilisation d'une bonne perméabilité, la taille appropriée des particules du revêtement (comme le graphite), pour favoriser l'évacuation des gaz.
3、Adopter la méthode de versement par inclinaison pour réduire le risque de rétention de gaz.
4, les matières premières doivent être correctement stockées dans un endroit sec et ventilé, et doivent être préchauffées avant utilisation.
5, la sélection d'un désoxydant à haut rendement (tel que le magnésium), l'élimination efficace des gaz dans la matière fondue.
Rétrécissement et rétrécissement
Causes de la formation :
1, la température de travail du moule n'atteint pas les conditions requises pour une solidification directionnelle, ce qui entraîne une mauvaise évacuation des gaz.
2. un mauvais choix de revêtement, un contrôle imprécis de l'épaisseur du revêtement dans les différentes parties, ce qui affecte la voie d'évacuation des gaz.
3. la disposition des pièces dans le moule n'est pas bien conçue, ce qui peut entraver l'écoulement naturel et l'évacuation des gaz.
4, la conception de la sortie d'air de coulée ne tient pas pleinement compte de son retrait complémentaire, de sorte qu'une partie de la région dans le processus de solidification forme une cavité.
5, le contrôle de la température de coulée n'est pas approprié, une température trop basse entraînera une augmentation de la solubilité du gaz, une température trop élevée aggravera l'expansion et la rétention du gaz.
Méthodes de prévention :
1) Augmenter la température de l'outil de meulage ;
2) Ajuster l'épaisseur du revêtement, pulvériser uniformément, enlever le revêtement, ne pas former un phénomène d'accumulation locale du revêtement ;
3. le chauffage local du moule ou l'utilisation de matériaux isolants pour l'isolation locale ;
4. les joints chauds sont incrustés de blocs de cuivre pour le refroidissement local ;
5、Concevoir le radiateur sur le moule, ou accélérer le taux de refroidissement de la zone locale par le biais de l'eau, etc ;
6. Bloc de refroidissement amovible, placé en rotation dans la cavité, afin d'éviter que le bloc de refroidissement lui-même ne soit pas suffisamment refroidi au cours du processus de production continu ;
7) Le dispositif de mise sous pression est conçu sur la colonne montante du moule ;
8) La conception du système d'écoulement doit être précise et la température d'écoulement appropriée doit être sélectionnée.
Les problèmes d'œil de laitier, impliquant le piégeage du laitier fondu ou du laitier d'oxyde métallique, sont des défauts courants dans le processus de coulée.
Raison : l'œil de laitier est principalement causé par le processus de fusion de l'alliage et le processus de coulée (y compris une conception incorrecte du système de coulée), le moule lui-même ne causera pas de trous de laitier, et les moules métalliques sont l'un des moyens efficaces d'éviter les trous de laitier.
Méthodes de prévention et de traitement :
1. le système de coulée est correctement réglé ou un tamis en fibre de coulée est utilisé.
2) Versement de l'inclinaison.
3. un contrôle strict de la qualité et de la sélection des matières fondues.
Fissures (fissures chaudes, fissures froides)
Causes de la formation :
Le moulage en moule métallique est sujet aux fissures car le moule métallique lui-même n'a pas de concessions, la vitesse de refroidissement est rapide, ce qui peut facilement conduire à une augmentation de la contrainte interne du moulage, l'ouverture est trop précoce ou trop tardive, l'angle de coulée est trop petit ou trop grand, le revêtement est trop mince, ce qui peut facilement conduire à la fissuration du moulage, et la cavité du moule elle-même est également sujette à provoquer des fissures.
Méthodes de prévention et de contrôle : 1. Il convient de prêter attention à l'exécution de la structure de la coulée, de sorte que l'épaisseur de la paroi de la coulée des parties inégales de la transition uniforme, et l'utilisation de la taille appropriée du congé. 2. Ajuster l'épaisseur du revêtement, de sorte que toutes les parties de la coulée autant que possible pour atteindre le taux de refroidissement requis, pour éviter une contrainte interne excessive. 3. Faire attention à la température de travail du moule en métal, ajuster l'inclinaison du moule, et à temps pour retirer le noyau fissuré et sortir la coulée de refroidissement lent.
Ségrégation froide (mauvaise fusion)
Causes de la formation :
1. la conception de l'échappement du moule métallique n'est pas raisonnable ; 2. la température de travail est trop basse ; 3. la qualité du revêtement est médiocre (matériau synthétique) ; 4. la position d'ouverture de la carotte n'est pas appropriée ; 5. la vitesse de coulée est trop lente, etc.
Méthodes de prévention et de contrôle : 1, conception correcte du système de coulée et d'échappement ; 2, grandes pièces moulées à parois minces, le revêtement ne doit pas être trop fin, un épaississement approprié du revêtement favorise le moulage ; 3, augmentation appropriée de la température de travail du moule ; 4, utilisation d'une méthode de coulée inclinée ; 5, utilisation de la vibration mécanique pour la coulée du moule métallique.
Sixièmement, le trou de sable (sand hole)
Raison de la formation : les particules de sable à la surface du noyau de sable sont enveloppées par le liquide de cuivre, ce qui forme des trous à la surface de la pièce moulée.1, mauvaise résistance de la surface du noyau de sable, brûlé ou pas complètement durci.2, la taille du noyau de sable est incompatible avec le moule extérieur, et le noyau de sable est écrasé lorsque le moule est fermé.3, le moule est plongé dans l'eau de graphite contaminée par le sable.4, le sable qui est frotté du noyau à la poche de coulée et au canal de coulée est rincé dans la cavité avec l'eau de cuivre.
Méthodes de prévention et de contrôle : 1. production du noyau de sable en stricte conformité avec le processus de production, vérification de la qualité ; 2. la taille du noyau de sable et du moule extérieur est cohérente ; 3. nettoyage de l'encre en temps opportun ; 4., v. éviter le frottement entre le paquet de coulée et le noyau de sable ; sous le noyau de sable lorsque le sable souffle, nettoyer le sable dans la cavité du moule.