Histoire du développement du tour CNC : du tournage de base à la révolution technologique dans la fabrication de pièces complexes
Temps de publication:2025-02-24 Trier par:Le blog Nombre de vues:696
Fossile vivant de la civilisation industrielle, l'évolution du tour à commande numérique illustre l'éternelle quête de la fabrication de précision. Depuis les artisans égyptiens de 1300 av. J.-C. qui utilisaient un lit rotatif en bois actionné par une corde, jusqu'au XXIe siècle équipé de machines-outils intelligentes à cinq axes dotées d'algorithmes d'IA, la technologie a toujours été en train de redéfinir la "précision" des limites de la période de la révolution industrielle : le tour à vapeur sera comprimé à 0,1 mm d'erreur d'usinage, tandis que le système CNC moderne, grâce au contrôle en boucle fermée à l'échelle, a atteint 0,0000 mm. Pendant la révolution industrielle, les tours à vapeur ont réduit les erreurs d'usinage à 0,1 mm, tandis que les systèmes CNC modernes ont atteint un contrôle microscopique de 0,001 mm grâce au contrôle d'échelle en boucle fermée. Particulièrement dans le domaine de la haute performancealuminiumDans le domaine de la fabrication de composants, la capacité synergique multi-axes du tour CNC a complètement modifié le processus traditionnel : si l'on prend l'exemple de la coque du moteur d'un véhicule à énergie nouvelle, l'usinage composite de sa pièce dentaire de dissipation thermique et de son embout de roulement peut être réalisé en une seule fois dans le système CNC intégré à la tourelle motorisée de l'axe Y, ce qui peut améliorer l'efficacité de 400% par rapport à l'usinage séquentiel traditionnel, et contrôler l'erreur de coaxialité à 5μm près, et ce saut technologique reconfigure non seulement le processus de production, mais promeut également les limites techniques de la conception légère. Ce saut technologique permet non seulement de reconfigurer le processus de production, mais aussi de repousser les limites techniques de la conception légère.
Le développement des machines-outils à commande numérique
Une machine-outil à commande numérique est une machine-outil qui utilise des informations sous forme de code numérique (instructions de programme) pour commander l'outil afin d'effectuer un usinage automatique selon un programme de travail, une vitesse de déplacement et une trajectoire donnés, appelée machine-outil à commande numérique.
intervalle de temps | événement de développement | Caractéristiques techniques |
1952 | Parsons et le Massachusetts Institute of Technology (MIT) ont collaboré pour produire la première fraiseuse verticale CNC à trois coordonnées au monde utilisant le principe du multiplicateur d'impulsions. | Premières explorations de la technologie CNC avec commande par tube électronique |
1954 | Bendix USA a produit la première machine-outil industrielle à commande numérique au monde. | Le début de l'application industrielle des machines-outils à commande numérique marque la maturité initiale de la technologie CNC. |
1959 | Les systèmes CNC ont évolué vers la deuxième génération avec des commandes transistorisées. | Fiabilité et stabilité accrues des transistors par rapport aux tubes |
1965 | Les systèmes CNC ont évolué vers la troisième génération, utilisant des circuits intégrés de commande à petite échelle. | L'utilisation de circuits intégrés améliore les performances et la fiabilité des systèmes CNC. |
1970 | La quatrième génération de CNC est apparue et les mini-ordinateurs ont commencé à être utilisés pour les CNC. | L'application de la technologie informatique permet au système CNC d'atteindre un niveau d'intelligence et d'automatisation plus élevé. |
1974 | La cinquième génération de CNC est apparue et les microprocesseurs ont commencé à être utilisés dans les CNC. | Les applications des microprocesseurs rendent les CNC plus flexibles et plus efficaces |
Fin des années 1970-début des années 1980 | Les États-Unis, l'Allemagne, le Japon et d'autres pays ont réalisé des progrès significatifs dans le domaine des machines-outils à commande numérique, lançant une série de machines-outils à commande numérique très performantes. | La technologie des machines-outils à commande numérique évolue progressivement et le champ d'application s'élargit. |
1980s | La production japonaise de machines-outils à commande numérique dépasse celle des États-Unis, ce qui fait du Japon le premier producteur mondial de machines-outils à commande numérique. | L'innovation technologique et le contrôle de la qualité dans le domaine des machines-outils à commande numérique ont fait du Japon un leader sur le marché mondial. |
Des années 1990 à aujourd'hui | La technologie des machines-outils à commande numérique continue de se développer, les pays ont introduit des machines-outils à commande numérique de haute performance et de haute précision. | Les machines-outils à commande numérique s'améliorent constamment en termes de contrôle, de précision, d'automatisation et de flexibilité. Elles sont largement utilisées dans l'aérospatiale, l'automobile, l'électronique et d'autres secteurs de fabrication haut de gamme. |
2020s | L'industrie chinoise des machines-outils à commande numérique se développe rapidement, avec des avancées technologiques remarquables, brisant le monopole technologique étranger. | La Chine a réalisé des progrès significatifs dans le domaine des machines-outils CNC haut de gamme, et la compétitivité du marché des machines-outils CNC produites dans le pays a continué à s'améliorer |
Tour manuel ancien
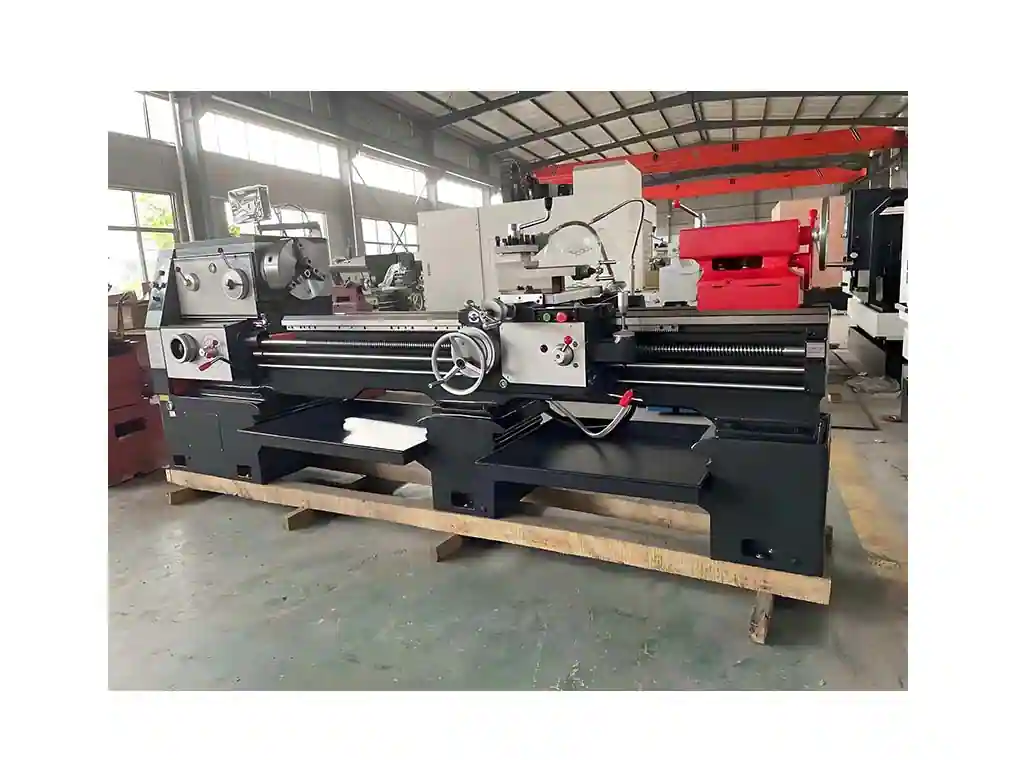
L'essence de l'usinage sur tour réside dans la délicate synergie dynamique entre une pièce en rotation et un outil linéaire. Les artisans utilisaient des cordes fabriquées à partir de tendons d'animaux pour entourer le bois et réaliser une coupe rotative en tirant d'avant en arrière, inaugurant ainsi la première méthode d'usinage de pièces rondes.
Le premier changement qualitatif dans la technologie des tours a eu lieu pendant la révolution industrielle, lorsque la demande explosive de l'industrie métallurgique a donné lieu au premier changement qualitatif dans la technologie des tours. L'introduction de la vapeur, le remplacement de la force humaine par un système de transmission par courroie et la conception résistante aux vibrations du banc en fonte ont permis au tour de produire pour la première fois des pièces standard en grande quantité. Le système de transmission à engrenages né à cette époque a permis d'atteindre une précision d'usinage de l'ordre du millimètre, posant ainsi la première pierre de l'ingénierie mécanique moderne.
Aujourd'hui, la pénétration de la technologie CNC a complètement reconfiguré l'ADN du tour. L'opérateur passe du statut de travailleur manuel à celui d'architecte de programmes, et la machine-outil se transforme en un terminal intelligent capable d'exécuter de manière autonome une logique complexe. Cette transformation permet non seulement de raccourcir le cycle de traitement des surfaces complexes de 60%, mais aussi de stabiliser la précision dimensionnelle au niveau du micron, marquant ainsi l'entrée officielle de l'industrie manufacturière dans l'ère de la précision numérique.
Conception et fonction de base des tours manuels
La conception modulaire du tour manuel, pierre angulaire de l'usinage, reste la source d'inspiration des machines-outils modernes. La synergie de chaque composant, du banc en fonte à l'entraînement de précision, illustre la sagesse originelle de l'ingénierie mécanique et fournit la logique sous-jacente à l'évolution de la technologie CNC.
canapé
Le banc en fonte du tour manuel adopte une structure en caisson, et le renforcement interne en forme de grille améliore considérablement la rigidité à la torsion, et ses performances d'amortissement des vibrations peuvent absorber des vibrations de coupe de plus de 80%. La combinaison d'un rail de guidage en V et d'un rail de guidage plan avec une rectification de précision sur la surface du banc garantit que la précision linéaire du mouvement de la plaque d'entraînement est contrôlée à 0,02 mm/m. Cette base de rigidité permet au tour de maintenir sa stabilité lors de l'usinage d'alliages de haute dureté, tandis que le matériau en fonte traité contre le vieillissement supprime efficacement la déformation due à l'augmentation de la température et garantit la précision géométrique de l'usinage à long terme.
boîte à broches
La boîte à broches sert de centre de puissance avec un système de transmission à six vitesses intégré, qui permet un large réglage de la vitesse de 45 à 2000 tr/min grâce à un jeu d'engrenages coulissants. La conception modulaire du mandrin à trois mors à centrage automatique et de la pince de serrage élastique permet de changer rapidement de solution de serrage pour les pièces de Φ5-300 mm, ce qui, avec l'interface de la broche à cône morse, garantit que le battement radial des pièces ne dépasse pas 0,03 mm. La conception de la liaison de la poignée à vitesse variable et de l'embrayage permet à l'opérateur de changer en douceur les vitesses de rotation pendant le processus de coupe, qui est adapté aux besoins de multiples scénarios, allant du tournage de finition des alliages d'aluminium à l'ébauche de l'acier inoxydable.
buggy
Le système de plaque d'entraînement composite intègre une fonction d'alimentation longitudinale/transversale, un guide de vis longitudinal de 6 mm/révolution, avec un cadran permettant d'obtenir une précision de réglage de 0,02 mm. Le porte-outil de la tourelle à quatre stations permet de changer rapidement d'outil et de réaliser des opérations multi-processus telles que le tournage, le rainurage et le filetage en l'espace de 15 secondes. Grâce au rapport d'engrenage de la boîte à roue suspendue, 60 pas standard de 0,5 à 10 mm peuvent être générés pour répondre à la demande d'usinage de précision des arbres d'entraînement, des vis et d'autres pièces, et sa précision de positionnement répétable atteint ±0,01 mm.
Contrôles et systèmes synergiques
Le système de commande à trois volants constitue un paradigme unique d'interaction homme-machine : la main gauche règle l'avance longitudinale (0,05-0,3 mm/r), la main droite contrôle la profondeur de coupe transversale (précision de ±0,01 mm), et la pédale relie l'embrayage pour démarrer et arrêter la broche. Le train d'engrenages planétaires du porte-outil décompose le mouvement de la broche en rapports d'avance précis, tandis que le mécanisme de demi-écrou synchronise automatiquement la vitesse d'avance pendant le filetage, une logique mécanique qui transforme les processus d'usinage complexes en opérations manuelles intuitives.
Porte-outils et lubrification
Le porte-outil quadrilatéral réglable permet un ajustement fin de la hauteur de l'outil ±2 mm et assure la rigidité du processus de coupe grâce à un mécanisme de verrouillage par coin. Le système de lubrification par barbotage assure une alimentation continue en huile pour les engrenages et 8 points de graissage manuel pour les pièces à frottement critique. Le programme de lubrification composée permet à la machine de maintenir un coefficient de frottement stable même après 8 heures de fonctionnement continu. Le mécanisme de réglage de l'angle du porte-outil permet de régler l'angle d'inclinaison de -5° à 45°, ce qui répond aux exigences d'usinage des cônes, des sphères et d'autres contours façonnés.
Les limites de l'utilisation d'un tour manuel expliquées en détail
automatisation limitée
Lors de l'usinage des engrenages de transmission automobile, l'opérateur doit synchroniser la vitesse d'avance, la profondeur de coupe et la vitesse de la broche, ce qui prend jusqu'à 50 minutes pour une seule pièce d'usinage, alors que l'équipement à commande numérique ne prend que 12 minutes. Cette forte dépendance à l'égard de l'intervention manuelle a entraîné une perte d'efficacité de 35% dans la production de masse, et le taux de rebut des opérateurs novices était cinq fois plus élevé que celui de la main-d'œuvre qualifiée.
La complexité de la précision
Lors de l'usinage de boîtiers de buses d'injecteurs diesel, les différences d'expérience des opérateurs peuvent entraîner des fluctuations des tailles critiques d'alésage de 0,05 à 0,12 mm. La déformation thermique du banc décale la contre-pointe de 0,03 mm après 4 heures d'usinage continu et l'usure des outils accumule une erreur de 0,1 mm pour 20 pièces, des variables qui rendent difficile la garantie de la cohérence des pièces par lots.
Des réglages qui prennent du temps
Un lot de 1 000 pièces de boîtiers de roulements montre que le changement de tour traditionnel nécessite d'ajuster la position de la contre-pointe (25 minutes), de recharger les fixations (15 minutes), de calibrer la coupe d'essai (30 minutes), le temps de préparation représentant un total de 28%. En revanche, l'équipement CNC peut être appelé par le programme pour compléter la gamme complète de paramètres en 8 minutes, ce qui met en évidence le goulot d'étranglement de l'efficacité du mode manuel de la production en grande quantité.
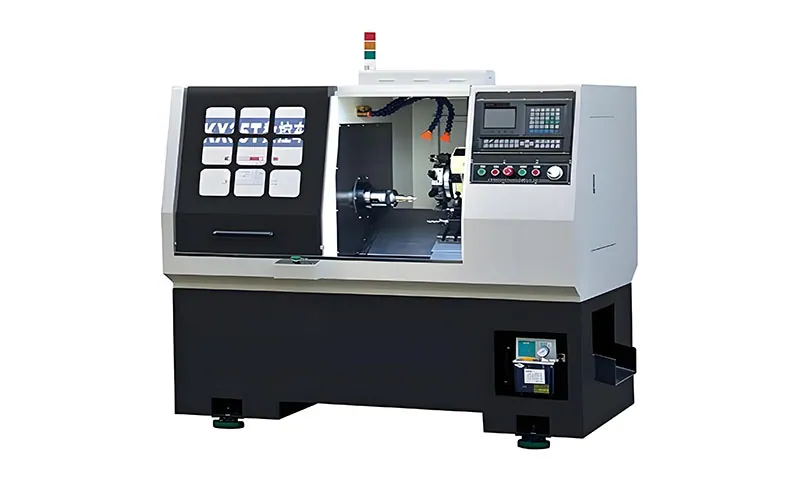
Tour CNC moderne
En tant qu'équipement central du système de fabrication intelligent, le tour CNC moderne redéfinit les limites de la fabrication de précision grâce à l'intégration profonde de la technologie numérique et de l'ingénierie mécanique. Son évolution technologique se reflète non seulement dans la mise à niveau du matériel, mais aussi dans la percée du système de contrôle intelligent.
système de contrôle
Les tours CNC modernes sont équipés d'un système de contrôle numérique qui agit comme le système nerveux central de l'équipement, coordonnant le fonctionnement de la broche, des axes d'alimentation et des dispositifs auxiliaires en temps réel par le biais d'un bus de données à grande vitesse. Le module intégré de compensation des erreurs peut corriger automatiquement l'écart de transmission mécanique et la déformation thermique provoqués par une petite déviation. Grâce au mécanisme de rétroaction en boucle fermée de la balance, la précision de positionnement sera stabilisée dans la catégorie du micron. Cette logique de contrôle numérique modifie complètement le mode de fonctionnement de l'usinage traditionnel, qui repose sur l'expérience manuelle, et permet à la précision du contour des surfaces complexes d'atteindre le niveau de 1/10 du diamètre d'une mèche de cheveux.
Interface de programmation conviviale
L'interface homme-machine intelligente révolutionne la création de programmes d'usinage, avec un module de simulation 3D qui visualise les trajectoires d'outils et les processus d'enlèvement de matière. L'opérateur peut rapidement générer du code G grâce à la fonction de programmation par glisser-déposer, et le système optimise automatiquement la combinaison des paramètres de coupe et reconnaît même les caractéristiques du dessin pour recommander des stratégies d'usinage. La fusion de l'écran tactile et de la commande vocale améliore l'efficacité du débogage de l'équipement de 60% et réduit considérablement la nécessité de faire appel à des experts en programmation.
Algorithmes de contrôle adaptatif
Le cœur intelligent de la machine ajuste dynamiquement la vitesse d'avance et la charge de la broche grâce à un réseau multi-capteurs qui recueille des données en temps réel sur les forces de coupe, les spectres de vibration et les changements de température. Lors de l'usinage de composants aérospatiaux en titane, l'algorithme identifie les points durs dans le matériau et réduit automatiquement la profondeur de coupe pour éviter l'écaillage de l'outil. Cette capacité d'auto-optimisation permet à la machine de maintenir une efficacité maximale tout au long de l'usinage continu, prolongeant la durée de vie de l'outil de plus de 30%, tout en garantissant une rugosité de surface stable de Ra0,8μm ou moins.
Des capacités de traitement plus avancées
La technologie de liaison à 5 axes s'affranchit de la limitation de la dimension du mouvement des machines-outils traditionnelles et permet l'usinage complet de pièces complexes telles que les pales de turbine grâce à la synergie de la tête pendulaire de l'axe B et de la table rotative de l'axe C. La conception de la tourelle motorisée avec broche de fraisage intégrée permet l'usinage simultané de trous transversaux et d'extrémités pendant le tournage, ce qui élimine les erreurs de serrage secondaires. La capacité multitâche permet de concentrer sur une seule machine des processus qui nécessiteraient autrement trois machines, ce qui réduit la durée du cycle de production de 40%.
Technologie d'automatisation intégrée
Le système modulaire de changement automatique d'outils est équipé d'un magasin d'outils à 40 stations, qui peut effectuer le changement d'outils en 0,8 seconde et vérifier automatiquement les paramètres de l'outil grâce à des puces RFID. Le système de refroidissement intelligent ajuste l'angle de pulvérisation du liquide de coupe et le débit en fonction des caractéristiques du matériau traité, et la technologie de micro-lubrification est adoptée pour réduire la consommation de liquide de refroidissement de 85% pendant l'usinage des alliages d'aluminium.La sonde d'inspection intégrée de la pièce mesure automatiquement les dimensions clés pendant l'espace d'usinage, et les données en temps réel sont renvoyées au système de contrôle pour effectuer des corrections compensatoires, formant ainsi une gestion complète de la qualité en boucle fermée.
Comparaison entre le cœur d'un tour manuel et celui d'un tour à commande numérique
dimension de comparaison | tour à main | Tour CNC |
---|---|---|
Précision de l'usinage | ±0,05~0,1mm (en fonction des compétences de l'opérateur) | ±0,005~0,01mm (échelle de contrôle en boucle fermée) |
efficacité de la production | Consommation de temps élevée par pièce (par exemple, 30 minutes pour l'usinage d'arbres étagés) | Production rapide de lots (usinage de la même pièce en 5 minutes) |
complexité opérationnelle | Technicien qualifié requis (3 ans d'expérience ou plus) | Programmé pour fonctionner automatiquement (1 semaine de formation au fonctionnement de base pour commencer à travailler) |
Coût initial | 30 000~100 000 ¥ (équipement d'entrée de gamme) | 200 000~2 millions ¥ (modèle à 5 axes) |
Capacité de production flexible | Convient pour les pièces uniques/petits lots (l'ajustement du changement prend 1~2 heures). | Prise en charge de pièces complexes ou de grand volume (le processus de changement ne prend que 5 minutes) |
application typique | Entretien des moules, enseignement pratique, production artisanale | Pièces pour l'aérospatiale, pièces pour l'automobile, dispositifs médicaux |
taux de consommation d'énergie | Consommation moyenne d'énergie 3~5kW-h (sans perte en veille) | Consommation électrique moyenne 10~30kW-h (y compris le système de refroidissement/changement d'outils) |
coût de maintenance | Frais d'entretien annuels ¥0,5~10 000 (les pièces mécaniques sont faciles à remplacer) | Frais de maintenance annuels ¥30,000~100,000 (la maintenance nécessite des ingénieurs professionnels) |
Analyse approfondie des avantages et des inconvénients
Avantages des tours manuels
- Production flexible à faible coût
- Adapté aux entreprises en phase de démarrage : 1/10e du coût d'achat de l'équipement CNC
- Réponse rapide aux changements : aucune programmation n'est nécessaire pour ajuster les parcours d'outils (par exemple, pour l'usinage de pièces en bronze de forme).
- Valeur patrimoniale technique
- Développement de l'intuition mécanique : l'opérateur peut visualiser les forces de coupe et les propriétés des matériaux.
- Statistiques d'une école technique à Ningbo : la formation pratique au tour manuel permet aux étudiants d'améliorer la précision de la sélection des outils 40%
Avantages du tour CNC
- Capacité d'usinage de pièces complexes
- Liaison 5 axes : usinage des pales de turbines (précision de surface ±0,005 mm)
- Fraisage-tournage : perçage/taraudage simultanés (par exemple, économie de 3 processus dans l'usinage de rotules de direction automobiles).
- Garantie de cohérence de la production
- Fluctuation dimensionnelle <0,01 mm pour un traitement par lots de 2000 pièces.
- Données provenant d'une usine de fabrication de dispositifs médicaux :usinage à commande numériqueTaux de réussite du fil de clouage 99,7%, manuel seulement 82%
Suggestions de sélection
Scénarios d'exigences | Équipement recommandé | raison d'être |
---|---|---|
Enseignement/prototypage (budget limité) | tour à main | Essais et erreurs peu coûteux pour développer les compétences de base |
Petit lot avec de nombreuses variétés (<100 pièces) | Tour CNC économique | Réduction du coût unitaire grâce à la réutilisation des processus |
Grandes quantités de pièces de précision (>1000 pièces) | Tour CNC haut de gamme | Production automatisée + système de traçabilité de la qualité, réduction globale des coûts de 40% |
Pièces ultra-complexes (par exemple, pièces aérospatiales) | Centre de tournage et de fraisage à 5 axes | Usinage multi-face en un seul serrage pour éviter les erreurs de référence. |
Des scénarios d'application diversifiés pour les tours CNC
En tant qu'équipement de base de l'industrie manufacturière moderne, le tour CNC a pénétré dans divers domaines clés de la production industrielle grâce à sa haute précision et à sa grande flexibilité. Des pièces de précision de l'ordre du micron au traitement de composants complexes et de grande taille, ses avantages technologiques redessinent le paysage mondial de la fabrication.
Fabrication de pièces géométriques complexes
Dans le domaine aérospatial, le tour CNC à cinq axes peut réaliser en une seule fois l'aube de turbine (telle que la figure 1) de la mortaise et de la rainure de la racine de la feuille et le traitement du trou de refroidissement du film d'air, le processus traditionnel de 12 processus étant réduit à 3, la précision du contour de l'aube étant de ± 0,005 mm. Un modèle d'usinage de disque pressurisé à haute pression de moteur aéronautique montre que l'utilisation de la technologie composite de fraisage et de tournage, le cycle de production est comprimé de 72 à 18 heures, et le faux-rond est contrôlé dans une fourchette de 5μm à 5μm. L'erreur est contrôlée à moins de 5μm.
Fabrication de moules de précision
Ningbo, ville sous-provinciale du Zhejiangmoule de coulée sous pressionDans le pôle industriel, les tours CNC se chargent de l'usinage de précision des principaux noyaux de moules. Lors du traitement des moules de coques de moteurs de véhicules à énergie nouvelle, le tournage de trous profonds à angles multiples (avec un rapport profondeur/diamètre de 15:1) par le système à canaux chauds augmente la durée de vie des moules jusqu'à 500 000 cycles de matriçage. Le module d'usinage de précision des filets peut générer un micro-pas de 0,2 mm pour répondre aux exigences de moulage des microconnecteurs.
Production de masse de pièces automobiles
- système moteurTournage étagé des tourillons de vilebrequin avec une erreur de circularité ≤ 0,003mm
- système de transmissionTournage dur d'ébauches d'engrenages pour boîtes de vitesses (HRC60) comme alternative aux procédés de rectification conventionnels
- Composants électrifiésEquilibrage dynamique à grande vitesse des rotors de moteurs avec une amplitude <0,01 mm à 8000 tr/min.
4. la fabrication de dispositifs médicaux
Le tournage d'alliages de titane pour les articulations artificielles utilise la technologie de micro-lubrification avec une rugosité de surface Ra0,2μm pour répondre aux exigences d'implantation. L'usinage de micro-filets de vis orthopédiques (M0,6×0,125) atteint une précision de positionnement de 0,01° grâce à l'indexation de l'axe C, ce qui garantit la fiabilité de l'engagement des filets.
5. traitement des équipements énergétiques
L'usinage de l'alliage haute température Inconel 718 pour la roue de la pompe principale d'une centrale nucléaire prolonge la durée de vie de l'outil de 40% en ajustant dynamiquement les paramètres de coupe grâce à des algorithmes de contrôle adaptatifs.Le tournage intermittent des bagues de roulement d'une éolienne adopte une technologie de suppression des vibrations pour augmenter l'efficacité de l'usinage de 3 fois.
Comparaison des données relatives aux applications industrielles
Domaines d'application | Pièces typiques | Exigences de précision | Ampleur des gains d'efficacité |
---|---|---|---|
aérospatiale | aube de turbine | ±0,005 mm | 300% |
la construction automobile | tourillon de vilebrequin | Rondeur 0,003 mm | 150% |
matériel médical | articulation artificielle | Ra0.2μm | 200% |
Équipements énergétiques | Roue nucléaire | Contour 0,01mm | 250% |
Questions fréquemment posées et réponses
Comment les tours CNC sont-ils passés de l'usinage de base à la fabrication complexe ?
Les tours à commande numérique ont connu trois révolutions technologiques majeures :
- Phase mécatronique (1950-1970): :
- Usinage automatisé de pièces d'arbres simples par programmation avec ruban de perçage (précision ±0,1mm)
- Cas typique : GM utilise le premier tour à commande numérique pour usiner les engrenages de transmission, ce qui a permis d'augmenter l'efficacité de 200%.
- Phase de contrôle numérique (1980-2000): :
- Technologie à microprocesseur introduite, supportant l'interpolation d'arc et la liaison multi-axes (précision ±0,02mm)
- Cas révolutionnaire : usinage 5 axes de disques de turbine de moteur de Boeing 747, réduisant le délai de production de 30 à 7 jours
- Phase de fabrication intelligente (2010 à ce jour): :
- Intégration d'algorithmes d'IA et de technologies IoT telles que l'usine Mazak iSMART pour un contrôle au niveau de 0,0001 mm.
- Une entreprise de moules de coulée sous pression de Ningbo a réduit le nombre d'essais de moules de 15 à 3 grâce à la technologie du jumeau numérique.
Comment concilier efficacité et protection de l'environnement avec le tour à commande numérique ?
- Technologie d'amélioration de l'efficacité: :
- Le système de changement d'outil automatique (temps de changement d'outil ≤ 0,8 sec) augmente l'efficacité du traitement par lots de 60%.
- La technologie de coupe à grande vitesse (vitesse de broche de 30 000 tr/min) réduit le temps de cycle d'usinage des alliages d'aluminium de 40%.
- Innovation durable: :
- Système de lubrification en microquantité (MQL) pour réduire l'utilisation du liquide de coupe 90%, économies annuelles de 150 000 ¥/unité.
- Le module de récupération d'énergie convertit l'énergie de freinage en énergie électrique réutilisable, réduisant ainsi la consommation d'énergie de 25%
- Une usine de pièces automobiles à énergie nouvelle a optimisé l'agencement des matériaux grâce à la CNC, le taux d'utilisation des matériaux est passé de 68% à 92%.
Les tours CNC modernes peuvent-ils traiter des pièces simples et complexes ?
- Usinage de pièces simples: :
- Production stable de 60 pièces par minute grâce à des macros pour la production de boulons par lots
- L'erreur d'usinage de l'axe étagé est contrôlée à ±0,005 mm, ce qui est 5 fois plus précis que les tours traditionnels.
- Percée des pièces complexes: :
- Usinage par fraisage-tournage 5 axes de magasins de moteurs aéronautiques avec 200 caractéristiques en un seul serrage.
- Traitement des articulations artificielles de la hanche dans le domaine médical avec une précision sphérique de Ra0,1μm (équivalent à l'effet miroir).
- Une entreprise de Ningbo transforme des coques en alliage d'aluminium à parois minces de 0,2 mm à l'aide d'un tour CNC, avec une déformation de <0,03 mm.