Moules de coulée sous pression
Temps de publication:2025-02-25 Trier par:Le blog Nombre de vues:1003
coulée à basse pression Il s'agit d'une méthode de coulée dans laquelle le métal en fusion est injecté dans la cavité du moule sous l'effet de la pression du gaz. Par rapport à la coulée à haute pression, la coulée à basse pression peut améliorer la qualité de la surface des pièces coulées, réduire la porosité et convient à la coulée de formes plus complexes. Dans le processus de coulée à basse pression, la composition et la conception du moule sont cruciales, ce qui affecte directement la qualité de la coulée, l'efficacité de la production et la durée de vie du moule. Le présent document aborde les points suivants Moule de coulée à basse pression Les principaux composants de la fonte et leur influence sur la qualité de la fonte.
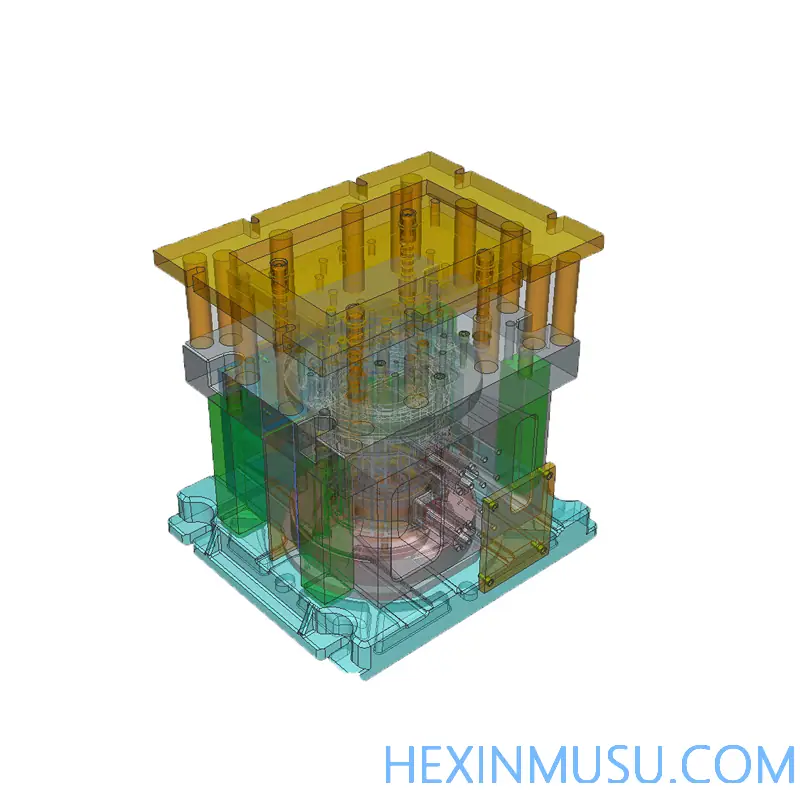
Les principaux composants d'un moule de coulée à basse pression
Moules de coulée à basse pression par les six composants de base de la synergie : la cavité du moule comme le noyau de la formation, en utilisant H13 usinage de précision en acier de moule de travail à chaud, pour assurer ± 0,15 mm de tolérance dimensionnelle et Ra ≤ 0,8μm finition de surface ; port d'injection à travers la conception tangente conique 60 ° pour atteindre le remplissage de flux laminaire, le taux d'écoulement est contrôlé dans le 0,8-1,2m/s pour éviter le volume de gaz ; système d'échappement intégration de la surface de séparation de la micro-gap (. 0,05-0,08 mm), de la rainure de vide et des bouchons en céramique poreuse pour réduire le taux de défaut de porosité de plus de 80% ; le système de refroidissement intègre le profilage avec la forme de la voie d'eau, 8-12 mm de la disposition de la surface, combiné avec la soupape de contrôle du flux pour rendre le gradient de température du moule <15 ℃ ; le cadre du moule adopte la structure de boîte en fonte ductile QT600, l'élasticité de la déformation de <0,02 mm/1000kN ; le système d'étanchéité est par un anneau en caoutchouc fluoré à haute température et un joint dur en métal. Le système d'étanchéité est combiné à un anneau en caoutchouc fluoré à haute température et à un joint métallique dur. Le taux de fuite est <0,5Pa-m³/s, ce qui garantit le fonctionnement stable de 150 000 moules.
Considérations clés pour la conception d'un moule de coulée à basse pression
La conception des moules nécessite un équilibre complet entre les propriétés des matériaux, la mécanique structurelle et les coûts de maintenance. La priorité est donnée à l'acier H13 (dureté HRC48-52) ou SKD61 (traitement TD de surface) pour faire face au lavage de l'aluminium et aux contraintes thermiques ; MAGMAsoft est utilisé pour effectuer une simulation couplée multi-champs de la charge-solidification afin de s'assurer que la différence de température entre les fronts métalliques est 1,5 ; la conception modulaire est utilisée pour permettre un remplacement rapide des inserts, et combinée avec les jauges de contrainte pour surveiller l'expansion des fissures de fatigue dans le moule en temps réel. La disposition du circuit d'eau de refroidissement doit être optimisée par ANSYS thermodynamique, de sorte que la différence de température entre les points chauds locaux puisse être contrôlée à ±3℃ ; en même temps, le système de barre de levage hydraulique préréglé (densité de 1/100cm²) et l'interface de positionnement zéro peuvent réduire le temps d'arrêt de la maintenance à 12 minutes.
Avantages et applications des moules de coulée à basse pression
Les moules de coulée à basse pression dans les secteurs de l'automobile et de l'aérospatiale présentent des avantages uniques : grâce à la technologie de mise en forme quasi-nette par surépaisseur d'usinage de 0,3 mm, un bras de commande de véhicule à énergie nouvelle économise 62%.usinageCoûts ; coulée assistée sous vide de sorte que le taux de qualification des pièces à paroi mince de 1,2 mm est de 981 TTP3T, par rapport à la réduction de poids de 351 TTP3T obtenue par le procédé traditionnel ; technologie de contrôle de la température par gradient pour améliorer la résistance à la corrosion des pièces à paroi mince de 1,2 mm.aluminiumLa taille des grains atteint le grade 7 (ASTM E112), la durée de vie des roues moulées en fatigue est multipliée par trois. Dans le domaine de l'aviation, les moules de charnières en alliage de titane Ti6Al4V atteignent une résistance à la traction > 950MPa, les cristaux colonnaires des moules de pales à solidification directionnelle représentent plus de 80%. Par rapport au moulage sous haute pression, la réduction du coût des matériaux d'une seule pièce est de 29% (85 $ contre 120 $), la durée de vie du moule est améliorée de 87,5% (150 000 fois par rapport à 80 000 fois par an).
Principales caractéristiques des moules de coulée à basse pression
Cette technologie allie rentabilité et précision de fabrication : raccourcissement du cycle de développement du moule de 40% (le jumeau numérique ne nécessite que 2 essais), rugosité de surface jusqu'à Ra0,8μm (meilleure que celle de 1,6μm du moulage à haute pression) ; adaptation à une gamme d'épaisseurs de paroi de 0,8 à 150 mm, particulièrement adaptée aux cavités internes complexes, telles que les blocs moteurs ; production entièrement automatisée grâce à l'intégration de l'automate programmable, avec un temps de production de ≤90 secondes par pièce, ce qui permet d'économiser 45% en coûts de main-d'œuvre ; utilisation des matériaux jusqu'à 95% (30% de plus que le moulage au sable) ; réduction supplémentaire de l'empreinte carbone grâce à l'application de l'aluminium recyclé. Économie de 45% ; taux d'utilisation des matériaux jusqu'à 95% (30% de plus que le moulage au sable), avec application d'aluminium recyclé pour réduire davantage l'empreinte carbone.
Foire aux questions (FAQ)
Comment choisir entre l'acier pour moules H13 et l'acier pour moules SKD61 ?
L'acier H13 (dureté HRC48-52) est adapté aux conditions de cyclage à haute température (par exemple, les moules de bloc moteur) et sa résistance à la fatigue thermique est 30% supérieure à celle du SKD61 ; tandis que le SKD61 avec un traitement d'infiltration du vanadium par TD a une dureté de surface de HV1800, qui est plus adaptée aux systèmes de goupilles d'éjection avec des exigences de résistance à l'usure élevées, et il peut prolonger la durée de vie à plus de 200 000 cycles de moulage.
2) Comment résoudre le problème de l'adhérence de l'aluminium au moule ?
L'utilisation de la technologie d'ébarbage au laser (rugosité de surface Sa 2,5μm) combinée à un revêtement en carbone amorphe (coefficient de frottement 0,1), ainsi que la pulvérisation quantitative d'agents de démoulage (3-5g/m²), permet de réduire le taux de collage de l'aluminium à moins de 0,1%. Après l'application d'un moule de carter de boîte de vitesses, le temps de nettoyage est passé de 30 minutes/moule à 5 minutes.
3. comment optimiser le système de refroidissement du moule ?
L'utilisation de l'impression 3D avec la forme du circuit d'eau de refroidissement, la distance de la surface du moule est réduite à 5 mm, avec un contrôle dynamique du flux (régulation de l'algorithme PID), peut faire passer la différence de température locale du moule de ± 15 ℃ à ± 3 ℃, le temps de solidification de la coulée est réduit de 25%, le rendement est augmenté de 12%.
4) Quelle est la différence de coût entre les moules de coulée à basse pression et à haute pression ?
L'investissement initial dans le moule pour la coulée à basse pression est inférieur de 40% (environ 500 000 RMB contre 850 000 RMB), mais le coût du matériau par pièce est réduit de 29% (85 RMB contre 120 RMB). Avec une capacité de production annuelle de 100 000 pièces, le coût total du processus à basse pression peut être réduit de 2,1 millions de yuans.
5) Comment prolonger la durée de vie des moules ?
Le traitement de nitruration (couche blanche brillante d'une épaisseur de 0,08-0,12 mm) combiné à un recuit sous contrainte (300°C x 4 heures) tous les 50 000 cycles de moulage peut augmenter la durée de vie des moules en acier H13 de 100 000 à 180 000 cycles de moulage, avec une réduction des coûts de maintenance globaux de 35%.
6) Comment garantir la qualité des pièces moulées à parois minces (<1,5 mm) ?
L'adoption de la technologie assistée par le vide (vide dans la cavité ≤ 50mbar) superposée à l'extrusion et à la rétraction (pression 80-100MPa) permet de produire de manière stable des pièces en alliage d'aluminium d'une épaisseur de paroi de 1,2 mm, avec un taux de porosité de <0,5% et une augmentation de la résistance de 20%.
7. quelles sont les tendances technologiques futures ?
Des moules intelligents (équipés de capteurs à fibre optique pour la surveillance des contraintes en temps réel) et des revêtements auto-cicatrisants (microcapsules libérant des agents de restauration) seront produits en masse en 2026, ce qui devrait réduire les coûts d'entretien des moules de 40% supplémentaires. La technologie de coulée semi-solide abaissera la limite d'épaisseur des parois à 0,5 mm, ce qui stimulera la réduction du poids des véhicules à énergie nouvelle de plus de 15%.
rendre un verdict
La composition du moule de coulée à basse pression détermine directement la qualité et la productivité des pièces coulées. Grâce à une conception raisonnable des différents composants du moule, notamment la cavité du moule, l'orifice d'injection, le système d'échappement, le système de refroidissement, etc., la qualité de la surface du moulage peut être considérablement améliorée, les défauts peuvent être réduits et la durée de vie du moule peut être prolongée. Avec le développement de la technologie, les matériaux et la conception des moules de coulée à basse pression continuent d'innover et joueront un rôle important dans de plus en plus de domaines à l'avenir.